Π‘ΠΈΠ»ΠΎΡ Π² Π±ΠΎΡΠΊΠ°Ρ
ΠΠ° ΠΡΠ±Π°Π½ΠΈ ΠΏΠΎΡΠ²ΠΈΠ»ΠΎΡΡ ΠΌΠ½ΠΎΠ³ΠΎ ΠΆΠ΅Π»Π°ΡΡΠΈΡ Π·Π°Π½ΠΈΠΌΠ°ΡΡΡΡ ΠΆΠΈΠ²ΠΎΡΠ½ΠΎΠ²ΠΎΠ΄ΡΡΠ²ΠΎΠΌ, ΠΎΡΠΎΠ±Π΅Π½Π½ΠΎ ΠΏΠΎΡΠ»Π΅ ΠΏΡΠΈΠ½ΡΡΠΈΡ Π·Π°ΠΊΠΎΠ½Π° βΠ ΠΏΠΎΠΌΠΎΡΠΈ Π»ΠΈΡΠ½ΡΠΌ ΠΏΠΎΠ΄ΡΠΎΠ±Π½ΡΠΌ Ρ ΠΎΠ·ΡΠΉΡΡΠ²Π°ΠΌβ.
Π Π±ΠΎΠ»ΡΡΠΈΠ½ΡΡΠ²Π΅ ΡΠ΅ΡΠΌΠ΅ΡΡΠΊΠΈΡ ΠΈ Π΄ΠΎΠΌΠ°ΡΠ½ΠΈΡ Ρ ΠΎΠ·ΡΠΉΡΡΠ² Π² Π·ΠΈΠΌΠ½Π΅Π΅ Π²ΡΠ΅ΠΌΡ ΠΊΠΎΡΠΌΠ»Π΅Π½ΠΈΠ΅ ΠΊΡΡΠΏΠ½ΠΎΠ³ΠΎ ΡΠΎΠ³Π°ΡΠΎΠ³ΠΎ ΡΠΊΠΎΡΠ° ΠΎΡΡΡΠ΅ΡΡΠ²Π»ΡΠ΅ΡΡΡ Π² ΠΎΡΠ½ΠΎΠ²Π½ΠΎΠΌ ΡΠ΅Π½ΠΎΠΌ, Ρ Π΄ΠΎΠ±Π°Π²Π»Π΅Π½ΠΈΠ΅ΠΌ Π½Π΅Π·Π½Π°ΡΠΈΡΠ΅Π»ΡΠ½ΠΎΠ³ΠΎ ΠΊΠΎΠ»ΠΈΡΠ΅ΡΡΠ²Π° ΡΠ²ΡΠΊΠ»Ρ ΠΈΠ»ΠΈ ΡΡΠΊΠ²Ρ, ΠΈ ΠΎΡΠ΅Π½Ρ ΡΠ΅Π΄ΠΊΠΎ ΠΈΡΠΏΠΎΠ»ΡΠ·ΡΠ΅ΡΡΡ ΠΊΠΎΠΌΠ±ΠΈΠΊΠΎΡΠΌ.
Π ΡΠ²ΠΈΠ½ΠΎΠ²ΠΎΠ΄ΡΡΠ²Π΅ Π² ΡΡΠΎ Π²ΡΠ΅ΠΌΡ Π² ΠΎΡΠ½ΠΎΠ²Π½ΠΎΠΌ ΠΈΡΠΏΠΎΠ»ΡΠ·ΡΡΡ ΠΊΠΎΠ½ΡΠ΅Π½ΡΡΠ°ΡΡ. Π’Π°ΠΊΠΎΠ΅ ΠΎΠ΄Π½ΠΎΡΡΠΎΡΠΎΠ½Π½Π΅Π΅ ΠΊΠΎΡΠΌΠ»Π΅Π½ΠΈΠ΅ Π½Π΅ ΡΠΎΠ»ΡΠΊΠΎ Π½Π΅ Π²ΡΠ³ΠΎΠ΄Π½ΠΎ ΡΠΊΠΎΠ½ΠΎΠΌΠΈΡΠ΅ΡΠΊΠΈ, Π½ΠΎ ΠΈ Π½Π΅ ΠΏΠΎΠ·Π²ΠΎΠ»ΡΠ΅Ρ Π΄ΠΎΡΡΠΈΡΡ ΠΆΠ΅Π»Π°Π΅ΠΌΠΎΠΉ Π²ΡΡΠΎΠΊΠΎΠΉ ΠΏΡΠΎΠ΄ΡΠΊΡΠΈΠ²Π½ΠΎΡΡΠΈ. Π ΠΏΡΠΎΡΠ΅ΡΡΠ΅ Π·Π°Π³ΠΎΡΠΎΠ²ΠΊΠΈ ΡΠ΅Π½Π° Π±ΠΎΠ»ΡΡΠΎΠ΅ ΠΊΠΎΠ»ΠΈΡΠ΅ΡΡΠ²ΠΎ ΠΏΠΈΡΠ°ΡΠ΅Π»ΡΠ½ΡΡ Π²Π΅ΡΠ΅ΡΡΠ² ΠΏΡΠΎΡΡΠΎ-Π½Π°ΠΏΡΠΎΡΡΠΎ ΡΠ»Π΅ΡΡΡΠΈΠ²Π°Π΅ΡΡΡ ΠΈ, Π² ΠΏΠ΅ΡΠ²ΡΡ ΠΎΡΠ΅ΡΠ΅Π΄Ρ, β Π²ΠΈΡΠ°ΠΌΠΈΠ½Ρ.
ΠΠ·Π±Π΅ΠΆΠ°ΡΡ ΡΡΠΈΡ ΠΏΠΎΡΠ΅ΡΡ ΠΌΠΎΠΆΠ½ΠΎ, Π·Π°Π³ΠΎΡΠ°Π²Π»ΠΈΠ²Π°Ρ Π½Π΅ ΡΠ΅Π½ΠΎ, ΠΎΡΠΎΠ±Π΅Π½Π½ΠΎ Π² Π΄ΠΎΠΆΠ΄Π»ΠΈΠ²ΡΠΉ ΠΏΠ΅ΡΠΈΠΎΠ΄, Π° ΡΠΈΠ»ΠΎΡ. Π‘ΠΈΠ»ΠΎΡΠΎΠ²Π°Π½ΠΈΠ΅ — ΡΡΠΎ ΠΏΡΠΎΡΠ΅ΡΡ ΠΏΡΠΈΠ³ΠΎΡΠΎΠ²Π»Π΅Π½ΠΈΡ ΡΠΎΡΠ½ΡΡ ΠΊΠΎΡΠΌΠΎΠ² Π² Π°Π½Π°ΡΡΠΎΠ±Π½ΡΡ ΡΡΠ»ΠΎΠ²ΠΈΡΡ (Π² Π±Π΅ΡΠΊΠΈΡΠ»ΠΎΡΠΎΠ΄Π½ΠΎΠΉ ΡΡΠ΅Π΄Π΅). ΠΠΎΠ½ΡΠ΅ΡΠ²Π°Π½ΡΠΎΠΌ ΡΠ»ΡΠΆΠΈΡ ΠΌΠΎΠ»ΠΎΡΠ½Π°Ρ ΠΊΠΈΡΠ»ΠΎΡΠ° — ΠΏΡΠΎΠ΄ΡΠΊΡ ΠΆΠΈΠ·Π½Π΅Π΄Π΅ΡΡΠ΅Π»ΡΠ½ΠΎΡΡΠΈ ΠΌΠΎΠ»ΠΎΡΠ½ΠΎΠΊΠΈΡΠ»ΡΡ Π±Π°ΠΊΡΠ΅ΡΠΈΠΉ. ΠΡΠΈ ΠΏΡΠ°Π²ΠΈΠ»ΡΠ½ΠΎΠΌ ΡΠΈΠ»ΠΎΡΠΎΠ²Π°Π½ΠΈΠΈ, ΠΊΠ°ΠΊ ΠΏΡΠ°Π²ΠΈΠ»ΠΎ, ΠΏΠΎΡΠ΅ΡΠΈ ΠΏΠΈΡΠ°ΡΠ΅Π»ΡΠ½ΡΡ Π²Π΅ΡΠ΅ΡΡΠ² Π½Π΅ ΠΏΡΠ΅Π²ΡΡΠ°ΡΡ 10%, Π½Π΅ ΠΈΠ·ΠΌΠ΅Π½ΡΠ΅ΡΡΡ ΠΏΠΈΡΠ°ΡΠ΅Π»ΡΠ½Π°Ρ ΡΠ΅Π½Π½ΠΎΡΡΡ ΠΊΠΎΡΠΌΠ°, ΡΠΎΡ ΡΠ°Π½ΡΡΡΡΡ ΠΌΠΈΠ½Π΅ΡΠ°Π»ΡΠ½ΡΠ΅ Π²Π΅ΡΠ΅ΡΡΠ²Π°, ΠΊΠ°ΡΠΎΡΠΈΠ½, Π° ΡΠ°Ρ Π°ΡΠ° ΠΏΡΠ΅Π²ΡΠ°ΡΠ°ΡΡΡΡ Π² ΠΌΠΎΠ»ΠΎΡΠ½ΡΡ ΠΊΠΈΡΠ»ΠΎΡΡ. ΠΠ½Π° ΠΎΠ±Π»Π°Π΄Π°Π΅Ρ Π΄ΠΈΠ΅ΡΠΈΡΠ΅ΡΠΊΠΈΠΌΠΈ ΡΠ²ΠΎΠΉΡΡΠ²Π°ΠΌΠΈ. ΠΠΎΠ±ΡΠΎΠΊΠ°ΡΠ΅ΡΡΠ²Π΅Π½Π½ΡΠΉ ΡΠΈΠ»ΠΎΡ Π²ΠΎΠ·Π±ΡΠΆΠ΄Π°Π΅Ρ Π°ΠΏΠΏΠ΅ΡΠΈΡ ΠΈ ΡΠΏΠΎΡΠΎΠ±ΡΡΠ²ΡΠ΅Ρ Π»ΡΡΡΠ΅ΠΌΡ ΠΏΠ΅ΡΠ΅Π²Π°ΡΠΈΠ²Π°Π½ΠΈΡ Π΄ΡΡΠ³ΠΈΡ ΠΊΠΎΡΠΌΠΎΠ².
ΠΡΠΈΠ³ΠΎΡΠΎΠ²ΠΈΡΡ ΡΠΈΠ»ΠΎΡ ΠΌΠΎΠΆΠ½ΠΎ Π² Π»ΡΠ±ΠΎΠΉ ΡΠΌΠΊΠΎΡΡΠΈ ΠΎΡ 100 Π΄ΠΎ 500 ΠΈ Π±ΠΎΠ»Π΅Π΅ Π»ΠΈΡΡΠΎΠ². ΠΡΠΎΠ±Π΅Π½Π½ΠΎ ΠΏΠΎΠ΄ΠΎΠΉΠ΄ΡΡ Π΄Π»Ρ ΡΡΠΎΠ³ΠΎ ΠΆΠ΅Π»Π΅Π·ΠΎΠ±Π΅ΡΠΎΠ½Π½ΡΠ΅ ΠΊΠΎΠ»ΡΡΠ° ΠΈΠ»ΠΈ ΠΊΠΎΡΠΎΠ±Π°, ΠΊΠΎΡΠΎΡΡΠ΅ ΠΌΠΎΠΆΠ½ΠΎ ΠΈΠ·Π³ΠΎΡΠΎΠ²ΠΈΡΡ ΡΠ°ΠΌΠΎΠΌΡ, ΠΈΡΠΏΠΎΠ»ΡΠ·ΡΡ ΠΏΡΠΎΡΡΠ΅ΠΉΡΡΡ ΠΎΠΏΠ°Π»ΡΠ±ΠΊΡ.
ΠΠ· ΡΠ΅Π³ΠΎ ΠΈ ΠΊΠ°ΠΊ ΠΌΠΎΠΆΠ½ΠΎ Π³ΠΎΡΠΎΠ²ΠΈΡΡ ΡΠΈΠ»ΠΎΡ?
ΠΠ»Ρ ΡΠ²ΠΈΠ½Π΅ΠΉ ΠΆΠ΅Π»Π°ΡΠ΅Π»ΡΠ½ΠΎ Π³ΠΎΡΠΎΠ²ΠΈΡΡ ΠΊΠΎΠΌΠ±ΠΈΡΠΈΠ»ΠΎΡ: ΡΡΠ°Π²Π°, ΡΠ΅Π·Π°Π½ΡΠΉ ΠΊΠ°ΡΡΠΎΡΠ΅Π»Ρ, ΡΠ²ΡΠΊΠ»Π°, ΠΌΠΎΡΠΊΠΎΠ²Ρ Ρ Π±ΠΎΡΠ²ΠΎΠΉ, ΠΊΠ°Π±Π°ΡΠΊΠΈ, Π°ΡΠ±ΡΠ·Ρ, Π΄ΡΠ½ΠΈ, ΠΎΠ³ΡΡΡΡ, ΠΎΡΡ ΠΎΠ΄Ρ ΡΠ±Π»ΠΎΠΊ, Π³ΡΡΡ. ΠΡΡ ΡΡΠ° ΡΠΌΠ΅ΡΡ ΠΈΠ·ΠΌΠ΅Π»ΡΡΠ°Π΅ΡΡΡ, Π·Π°ΠΊΠ»Π°Π΄ΡΠ²Π°Π΅ΡΡΡ Π² Π±ΠΎΡΠΊΠΈ ΠΈ ΡΡΠ°ΡΠ΅Π»ΡΠ½ΠΎ ΡΡΠ°ΠΌΠ±ΡΠ΅ΡΡΡ. Π‘Π²Π΅ΡΡ Ρ ΠΊΠΎΡΠΎΠ±Π° ΡΡΠ°ΡΠ΅Π»ΡΠ½ΠΎ Π·Π°ΠΊΡΡΠ²Π°ΡΡΡΡ, ΡΡΠΎΠ±Ρ ΠΈΠ·Π±Π΅ΠΆΠ°ΡΡ ΠΏΠΎΠΏΠ°Π΄Π°Π½ΠΈΡ Π²ΠΎΠ·Π΄ΡΡ Π°, ΠΏΠΎΡΠΊΠΎΠ»ΡΠΊΡ, Π½Π°ΠΏΠΎΠΌΠ½Ρ, ΠΏΡΠΎΡΠ΅ΡΡ ΠΏΡΠΈΠ³ΠΎΡΠΎΠ²Π»Π΅Π½ΠΈΡ ΡΠΈΠ»ΠΎΡΠ° ΠΈΠ΄ΡΡ Π±Π΅Π· Π΄ΠΎΡΡΡΠΏΠ° Π²ΠΎΠ·Π΄ΡΡ Π°.
ΠΡΠΏΠΎΠ»ΡΠ·ΠΎΠ²Π°Π½ΠΈΠ΅ ΡΠ°ΠΊΠΎΠ³ΠΎ ΠΊΠΎΠΌΠ±ΠΈΡΠΈΠ»ΠΎΡΠ° ΠΏΠΎΠ·Π²ΠΎΠ»ΡΠ΅Ρ ΡΠ½ΠΈΠ·ΠΈΡΡ ΡΠ°ΡΡ ΠΎΠ΄ ΠΊΠΎΠΌΠ±ΠΈΠΊΠΎΡΠΌΠ° Π² ΡΡΠ΅Π΄Π½Π΅ΠΌ Π½Π° 30%. Π‘ΠΊΠ°ΡΠΌΠ»ΠΈΠ²Π°ΡΡ Π΅Π³ΠΎ ΠΌΠΎΠΆΠ½ΠΎ Π² ΡΠ»Π΅Π΄ΡΡΡΠΈΡ ΠΊΠΎΠ»ΠΈΡΠ΅ΡΡΠ²Π°Ρ : Ρ ΡΡΠΊΠ°ΠΌ — 2-4 ΠΊΠ³, ΡΡΠΏΠΎΡΠΎΡΠ½ΡΠΌ ΠΌΠ°ΡΠΊΠ°ΠΌ — 6-7 ΠΊΠ³, ΠΏΠΎΡΠΎΡΡΡΠ°ΠΌ Π² 2-4 ΠΌΠ΅ΡΡΡΠ° — 2-4 ΠΊΠ³, Π½Π° ΠΎΡΠΊΠΎΡΠΌΠ΅ — 4-5 ΠΊΠ³, Π²ΡΠ±ΡΠ°ΠΊΠΎΠ²Π°Π½Π½ΡΠΌ ΡΠ²ΠΈΠ½ΠΎΠΌΠ°ΡΠΊΠ°ΠΌ Π½Π° ΠΎΡΠΊΠΎΡΠΌΠ΅ — 8-12 ΠΊΠ³.
ΠΡΠΏΠΎΠ»ΡΠ·ΠΎΠ²Π°ΡΡ ΠΊΠΎΠΌΠ±ΠΈΡΠΈΠ»ΠΎΡ ΠΌΠΎΠΆΠ½ΠΎ Π½Π΅ ΡΠΎΠ»ΡΠΊΠΎ Π² ΡΠ²ΠΈΠ½ΠΎΠ²ΠΎΠ΄ΡΡΠ²Π΅, Π½ΠΎ ΠΈ Π² ΠΏΡΠΈΡΠ΅Π²ΠΎΠ΄ΡΡΠ²Π΅. ΠΡΠ½ΠΎΠ²Π½ΡΠΌ ΡΡΠ΅Π±ΠΎΠ²Π°Π½ΠΈΠ΅ΠΌ ΠΏΡΠΈ Π·Π°Π³ΠΎΡΠΎΠ²ΠΊΠ΅ ΠΊΠΎΠΌΠ±ΠΈΡΠΈΠ»ΠΎΡΠ° Π΄Π»Ρ ΠΏΡΠΈΡΡ β Π±ΠΎΠ»Π΅Π΅ ΡΡΠ°ΡΠ΅Π»ΡΠ½ΠΎΠ΅ ΠΈΠ·ΠΌΠ΅Π»ΡΡΠ΅Π½ΠΈΠ΅ β Π΄ΠΎ 0,5 ΡΠΌ.
Π‘ΠΎΡΡΠ°Π²: ΠΌΠΎΡΠΊΠΎΠ²Ρ, ΡΡΠ°Π²Π° Π±ΠΎΠ±ΠΎΠ²ΡΡ (Π³ΠΎΡΠΎΡ , ΡΠΎΡ, Π»ΡΡΠ΅ΡΠ½Π°), ΡΠ²ΡΠΊΠ»Π° Ρ Π±ΠΎΡΠ²ΠΎΠΉ, ΠΊΠ°ΡΡΠΎΡΠ΅Π»Ρ Π·Π°ΠΏΠ°ΡΠ΅Π½Π½ΡΠΉ, Π½ΠΎ ΠΌΠΎΠΆΠ½ΠΎ ΠΈΡΠΏΠΎΠ»ΡΠ·ΠΎΠ²Π°ΡΡ Π²ΡΡ, ΡΡΠΎ Π΅ΡΡΡ ΠΏΠΎΠ΄ ΡΡΠΊΠΎΠΉ. ΠΠ°Π²Π°ΡΡ Π² ΡΠ»Π΅Π΄ΡΡΡΠΈΡ ΠΊΠΎΠ»ΠΈΡΠ΅ΡΡΠ²Π°Ρ : Π³ΡΡΠΈ, ΡΡΠΊΠΈ — 250-300 Π³, ΠΊΡΡΡ -20-25, ΠΈΠ½Π΄Π΅ΠΉΠΊΠΈ — 35-50 Π³. Π‘ΠΊΠ°ΡΠΌΠ»ΠΈΠ²Π°Π½ΠΈΠ΅ ΡΠΈΠ»ΠΎΡΠ° ΠΏΠΎΠ·Π²ΠΎΠ»ΡΠ΅Ρ ΡΠΊΠΎΠ½ΠΎΠΌΠΈΡΡ Π΄ΠΎ 35% ΠΊΠΎΠ½ΡΠ΅Π½ΡΡΠ°ΡΠΎΠ², ΠΏΡΠΈ ΠΎΠ΄Π½ΠΎΠ²ΡΠ΅ΠΌΠ΅Π½Π½ΠΎΠΌ ΠΏΠΎΠ²ΡΡΠ΅Π½ΠΈΠΈ ΡΠΉΡΠ΅Π½ΠΎΡΠΊΠΎΡΡΠΈ Π½Π° 20-15 %, ΠΏΡΠΈΠ²Π΅Ρ β ΠΎΡ 5 Π΄ΠΎ 17%.
ΠΠ»Ρ ΠΊΡΠΎΠ»ΠΈΠΊΠΎΠ² Π½Π°ΠΈΠ±ΠΎΠ»Π΅Π΅ ΡΡΡΠ΅ΠΊΡΠΈΠ²Π½ΠΎ Π³ΠΎΡΠΎΠ²ΠΈΡΡ ΡΠΈΠ»ΠΎΡ ΠΈΠ· ΠΎΡΡΠ°ΡΠΊΠΎΠ² ΠΊΠ°ΠΏΡΡΡΡ Ρ Π΄ΠΎΠ±Π°Π²Π»Π΅Π½ΠΈΠ΅ΠΌ ΠΌΠΎΡΠΊΠΎΠ²ΠΈ ΠΈ ΡΠ°Ρ Π°ΡΠ½ΠΎΠΉ ΡΠ²ΡΠΊΠ»Ρ Ρ Π±ΠΎΡΠ²ΠΎΠΉ.
ΠΠ»Ρ ΠΊΡΡΠΏΠ½ΠΎΠ³ΠΎ ΡΠΎΠ³Π°ΡΠΎΠ³ΠΎ ΡΠΊΠΎΡΠ° ΡΠΈΠ»ΠΎΡ ΡΠ²Π»ΡΠ΅ΡΡΡ ΠΎΠ±ΡΠ·Π°ΡΠ΅Π»ΡΠ½ΡΠΌ Π² ΠΊΠΎΡΠΌΠ»Π΅Π½ΠΈΠΈ. ΠΠΎ ΡΡΠ°Π²Π½Π΅Π½ΠΈΡ Ρ ΠΊΠΎΠΌΠ±ΠΈΡΠΈΠ»ΠΎΡΠΎΠΌ, Π΅Π³ΠΎ ΠΏΡΠΈΠ³ΠΎΡΠΎΠ²ΠΈΡΡ Π΅ΡΡ ΠΏΡΠΎΡΠ΅. ΠΠ»Ρ ΡΡΠΈΡ ΡΠ΅Π»Π΅ΠΉ ΠΌΠΎΠΆΠ½ΠΎ ΠΈΡΠΏΠΎΠ»ΡΠ·ΠΎΠ²Π°ΡΡ Π»ΡΠ±ΡΡ ΡΡΠ°Π²Ρ, Π² ΡΠΎΠΌ ΡΠΈΡΠ»Π΅ ΠΈ ΡΠΎΡΠ½ΡΠΊΠΈ. ΠΠ΅ΠΎΠ±Ρ ΠΎΠ΄ΠΈΠΌΠΎ ΡΠΎΠ»ΡΠΊΠΎ ΡΡΠ°ΡΠ΅Π»ΡΠ½ΠΎ ΠΈΠ·ΠΌΠ΅Π»ΡΡΠΈΡΡ ΠΈ ΡΡΡΠ°ΠΌΠ±ΠΎΠ²Π°ΡΡ ΡΠΌΠ΅ΡΡ. Π‘ΠΈΠ»ΠΎΡ Π½Π°ΠΈΠ±ΠΎΠ»Π΅Π΅ Π²ΡΡΠΎΠΊΠΎΠ³ΠΎ ΠΊΠ°ΡΠ΅ΡΡΠ²Π° ΠΏΠΎΠ»ΡΡΠ°Π΅ΡΡΡ ΠΏΡΠΈ ΠΈΡΠΏΠΎΠ»ΡΠ·ΠΎΠ²Π°Π½ΠΈΠΈ ΡΠΏΠ΅ΡΠΈΠ°Π»ΡΠ½ΡΡ Π·Π°ΠΊΠ²Π°ΡΠΎΠΊ.
ΠΡ, Π° ΡΠ΅ΠΏΠ΅ΡΡ ΠΎ ΡΠΎΠΌ, ΡΡΠΎ Π΄Π΅Π»Π°ΡΡ ΡΠ΅ΠΌ, ΠΊΡΠΎ Π½Π΅ ΠΈΠΌΠ΅Π΅Ρ Π²ΠΎΠ·ΠΌΠΎΠΆΠ½ΠΎΡΡΠΈ ΠΈΠ·Π³ΠΎΡΠΎΠ²ΠΈΡΡ ΠΊΠΎΠ»ΡΡΠ° ΠΈΠ»ΠΈ ΠΊΠΎΡΠΎΠ±Π°. ΠΠ΅ Π±Π΅Π΄Π°! ΠΠΎΠ·ΡΠΌΠΈΡΠ΅ Π»ΡΠ±ΡΡ ΠΎΡΡΠ»ΡΠΆΠΈΠ²ΡΡΡ ΡΠ²ΠΎΠΉ ΡΡΠΎΠΊ Π±ΠΎΡΠΊΡ. ΠΡΡΠ°Π²ΡΡΠ΅ Π²Π½ΡΡΡΡ ΡΡΠΊΠ°Π² ΠΈΠ· ΠΏΠΎΠ»ΠΈΡΡΠΈΠ»Π΅Π½ΠΎΠ²ΠΎΠΉ ΠΏΠ»ΡΠ½ΠΊΠΈ, ΡΡΠ°ΡΠ΅Π»ΡΠ½ΠΎ Π΅Π³ΠΎ Π½Π°ΠΏΠΎΠ»Π½ΠΈΡΠ΅ ΠΈ Π·Π°Π²ΡΠΆΠΈΡΠ΅. Π Π·Π°Π²ΠΈΡΠΈΠΌΠΎΡΡΠΈ ΠΎΡ Π²ΠΈΠ΄Π° ΡΡΠ°Π²Ρ, Π²Π°Ρ ΡΠΈΠ»ΠΎΡ Π±ΡΠ΄Π΅Ρ Π³ΠΎΡΠΎΠ² ΡΠ΅ΡΠ΅Π· 1 ΠΈΠ»ΠΈ 3 ΠΌΠ΅ΡΡΡΠ°.
www.kaicc.ru
Π‘ΠΈΠ»ΠΎΡ ΡΠ΅ΠΌΠ΅Π½ΡΠ° Π±Π΅Π· ΠΎΠΏΡΠΈΠΉ β Π²ΡΠ΅Π³ΠΎ Π»ΠΈΡΡ ΠΏΡΡΡΠ°Ρ Π±ΠΎΡΠΊΠ° ΠΈΠ»ΠΈ Π½Π΅ΡΠΊΠΎΠ»ΡΠΊΠΎ ΡΠΎΠ²Π΅ΡΠΎΠ² ΠΏΠΎΠΊΡΠΏΠ°ΡΠ΅Π»Ρ Π±Π΅ΡΠΎΠ½Π½ΠΎΠ³ΠΎ Π·Π°Π²ΠΎΠ΄Π°
Π‘ΠΈΠ»ΠΎΡ ΠΏΡΠ΅Π΄Π½Π°Π·Π½Π°ΡΠ΅Π½ Π΄Π»Ρ Π²ΡΠ΅ΠΌΠ΅Π½Π½ΠΎΠ³ΠΎ Ρ ΡΠ°Π½Π΅Π½ΠΈΡ ΡΠ΅ΠΌΠ΅Π½ΡΠ° Π½Π΅ΠΏΠΎΡΡΠ΅Π΄ΡΡΠ²Π΅Π½Π½ΠΎ Π½Π° ΠΏΡΠΎΠΈΠ·Π²ΠΎΠ΄ΡΡΠ²Π΅Π½Π½ΠΎΠΉ ΠΏΠ»ΠΎΡΠ°Π΄ΠΊΠ΅ ΠΠ‘Π£. ΠΠΎΡΠΊΠΎΠ»ΡΠΊΡ Π² ΠΏΡΠΎΠΈΠ·Π²ΠΎΠ΄ΡΡΠ²Π΅Β Π±Π΅ΡΠΎΠ½Π° ΡΠ°Π·Π»ΠΈΡΠ½ΡΡ ΠΌΠ°ΡΠΎΠΊ Π½Π΅ΠΎΠ±Ρ ΠΎΠ΄ΠΈΠΌΠΎ ΠΏΡΠΈΠΌΠ΅Π½ΡΡΡ Π²ΡΠΆΡΡΠΈΠΉ ΠΊΠΎΠΌΠΏΠΎΠ½Π΅Π½Ρ ΡΠΎΠΎΡΠ²Π΅ΡΡΡΠ²ΡΡΡΠΈΡ ΠΏΠ°ΡΠ°ΠΌΠ΅ΡΡΠΎΠ², ΡΠΎ ΠΏΠΎΠ΄ ΠΊΠ°ΠΆΠ΄ΡΡ ΠΈΡΠΏΠΎΠ»ΡΠ·ΡΠ΅ΠΌΡΡ ΠΌΠ°ΡΠΊΡ ΡΠ΅ΠΌΠ΅Π½ΡΠ° ΠΏΡΠΈΡ ΠΎΠ΄ΠΈΡΡΡ ΠΎΠ±ΡΡΡΡΠ°ΠΈΠ²Π°ΡΡ ΠΎΡΠ΄Π΅Π»ΡΠ½ΡΠΉ ΡΠΈΠ»ΠΎΡ (ΡΠΌΠ΅ΡΠΈΠ²Π°Π½ΠΈΠ΅ ΡΠ΅ΠΌΠ΅Π½ΡΠΎΠ² ΡΠ°Π·Π½ΡΡ ΠΌΠ°ΡΠΎΠΊ Π² ΠΎΠ±ΡΠ΅ΠΌ ΡΠΈΠ»ΠΎΡΠ΅ Π½Π΅ Π΄ΠΎΠΏΡΡΠΊΠ°Π΅ΡΡΡ). Π‘ΠΈΠ»ΠΎΡΡ Π²ΠΊΠ»ΡΡΠ°ΡΡΡΡ Π² ΡΠ΅Ρ Π½ΠΎΠ»ΠΎΠ³ΠΈΡΠ΅ΡΠΊΡΡ ΡΠ΅ΠΏΠΎΡΠΊΡ ΠΏΡΠΎΠΈΠ·Π²ΠΎΠ΄ΡΡΠ²Π΅Π½Π½ΠΎΠ³ΠΎ ΡΠΈΠΊΠ»Π° Π±Π΅ΡΠΎΠ½Π½ΠΎΠ³ΠΎ Π·Π°Π²ΠΎΠ΄Π°, ΠΎΡ Π½ΠΈΡ Π½Π°ΠΏΡΡΠΌΡΡ Π·Π°Π²ΠΈΡΠΈΡ ΠΏΡΠΎΠΈΠ·Π²ΠΎΠ΄ΠΈΡΠ΅Π»ΡΠ½ΠΎΡΡΡ Π±Π΅ΡΠΎΠ½ΠΎΡΠΌΠ΅ΡΠΈΡΠ΅Π»Ρ.
ΠΡΠ½Π°ΡΠ΅Π½ΠΈΠ΅ ΡΠΈΠ»ΠΎΡΠ° ΡΠ΅ΠΌΠ΅Π½ΡΠ°
ΠΠΎΠ½ΡΡΡΡΠΊΡΠΈΠ²Π½ΠΎ ΡΠΈΠ»ΠΎΡΠ½ΡΠ΅ Π±Π°ΡΠ½ΠΈ ΠΏΡΠ΅Π΄ΡΡΠ°Π²Π»ΡΡΡ ΡΠΎΠ±ΠΎΠΉ ΡΠΈΠ»ΠΈΠ½Π΄ΡΠΈΡΠ΅ΡΠΊΠΈΠ΅ Π΅ΠΌΠΊΠΎΡΡΠΈ Π΄ΠΈΠ°ΠΌΠ΅ΡΡΠΎΠΌ Π΄ΠΎ 4 ΠΌΠ΅ΡΡΠΎΠ² ΠΈ Π²ΡΡΠΎΡΠΎΠΉ Π΄ΠΎ 15-17 ΠΌΠ΅ΡΡΠΎΠ², ΠΎΡΠ½Π°ΡΠ΅Π½Π½ΡΠ΅ Π²Π½ΡΡΡΠ΅Π½Π½ΠΈΠΌΠΈ ΠΈ Π²Π½Π΅ΡΠ½ΠΈΠΌΠΈ ΠΌΠ΅ΡΠ°Π»Π»ΠΎΠΊΠΎΠ½ΡΡΡΡΠΊΡΠΈΡΠΌΠΈ Π΄Π»Ρ ΠΎΠ±ΡΠ»ΡΠΆΠΈΠ²Π°Π½ΠΈΡ ΡΠΈΠ»ΠΎΡΠΎΠ². ΠΡΠΈ ΠΎΠ³ΡΠΎΠΌΠ½ΡΠ΅ Π±ΠΎΡΠΊΠΈ ΡΡΠΎΡΡ Π½Π΅Π΄Π΅ΡΠ΅Π²ΠΎ, Π½ΠΎ Π΅ΡΠ΅ Π΄ΠΎΡΠΎΠΆΠ΅ ΠΎΠ±Ρ ΠΎΠ΄ΡΡΡΡ ΠΎΠΏΡΠΈΠΈ, ΠΏΡΠ΅Π΄Π»Π°Π³Π°Π΅ΠΌΡΠ΅ ΠΊ Π½ΠΈΠΌ ΠΏΡΠΎΠΈΠ·Π²ΠΎΠ΄ΠΈΡΠ΅Π»ΡΠΌΠΈ. ΠΠΎΠΊΡΠΏΠ°ΡΠ΅Π»ΠΈ Π±Π΅ΡΠΎΠ½Π½ΡΡ Π·Π°Π²ΠΎΠ΄ΠΎΠ² ΠΏΠΎΠ½ΠΈΠΌΠ°ΡΡ, ΡΡΠΎ Π±Π΅Π· ΡΠΈΠ»ΠΎΡΠΎΠ² ΠΈΠΌ Π½Π΅ ΠΎΠ±ΠΎΠΉΡΠΈΡΡ, Π½ΠΎ Π½Π΅ Π²ΡΠ΅Π³Π΄Π° ΡΠΎΠ³Π»Π°ΡΠ½Ρ Ρ ΡΠ΅ΠΌ Π²Π°ΠΆΠ½ΡΠΌ ΠΏΡΠ΅Π΄Π½Π°Π·Π½Π°ΡΠ΅Π½ΠΈΠ΅ΠΌ, ΠΊΠΎΡΠΎΡΠΎΠ΅ ΠΏΡΠ΅Π΄ΠΏΠΈΡΡΠ²Π°Π΅ΡΡΡ ΠΎΡΠ½Π°ΡΠ΅Π½ΠΈΡ ΡΠΈΠ»ΠΎΡΠΎΠ². ΠΠΎΠ΄ΠΌΠ΅Π½Π° Π²ΠΎΠ·Π΄ΡΡΠ½ΡΡ ΡΠΈΠ»ΡΡΡΠΎΠ² ΠΈΠ»ΠΈ Π΄ΠΈΡΠΊΠΎΠ²ΡΡ Π·Π°ΡΠ²ΠΎΡΠΎΠ² Π±ΡΠ΅Π½Π΄ΠΎΠ²ΡΡ ΠΌΠΎΠ΄Π΅Π»Π΅ΠΉ Π½Π° Π΄Π΅ΡΠ΅Π²ΡΡ Π°ΠΏΠΏΠ°ΡΠ°ΡΡΡΡ Π½ΠΈΠ·ΠΊΠΎΠ³ΠΎ ΠΊΠ°ΡΠ΅ΡΡΠ²Π° ΡΠ΅ΡΠ΅Π· Π½Π΅ΠΊΠΎΡΠΎΡΠΎΠ΅ Π²ΡΠ΅ΠΌΡ ΠΎΠ±Π΅ΡΠ½Π΅ΡΡΡ ΠΎΠ³ΡΠΎΠΌΠ½ΡΠΌΠΈ ΡΡΡΠ°ΡΠ°ΠΌΠΈ Π·Π° ΡΡΠ΅ΡΠ± ΡΠΊΠΎΠ»ΠΎΠ³ΠΈΠΈ Π²ΡΠ±ΡΠ°ΡΡΠ²Π°Π΅ΠΌΠΎΠΉ ΠΈΠ· ΡΠΈΠ»ΠΎΡΠ° ΡΠ΅ΠΌΠ΅Π½ΡΠ½ΠΎΠΉ ΠΏΡΠ»ΡΡ ΠΈΠ»ΠΈ ΡΠ½ΠΈΠΆΠ΅Π½ΠΈΠ΅ΠΌ ΠΏΡΠΎΠΈΠ·Π²ΠΎΠ΄ΠΈΡΠ΅Π»ΡΠ½ΠΎΡΡΠΈ Π·Π°Π²ΠΎΠ΄Π° ΠΈΠ·-Π·Π° ΡΡ ΡΠ΄ΡΠ΅Π½Π½ΠΎΠΉ ΠΏΠΎΠ΄Π°ΡΠΈ ΡΠ΅ΠΌΠ΅Π½ΡΠ° ΠΈΠ· ΡΠΈΠ»ΠΎΡΠ°.
Π¦Π΅ΠΌΠ΅Π½Ρ ΡΠ²Π»ΡΠ΅ΡΡΡ Π΄ΠΎΠ²ΠΎΠ»ΡΠ½ΠΎ ΠΊΠ°ΠΏΡΠΈΠ·Π½ΡΠΌ ΠΊ Ρ ΡΠ°Π½Π΅Π½ΠΈΡ ΠΌΠ°ΡΠ΅ΡΠΈΠ°Π»ΠΎΠΌ. Π ΡΡΠΈΡΠ°Π½Π½ΡΠ΅ ΠΌΠ΅ΡΡΡΡ ΠΎΠ½ ΡΠΏΠΎΡΠΎΠ±Π΅Π½ ΡΠ°ΡΡΠ΅ΡΡΡΡ Π²ΡΡΒ ΡΠ²ΠΎΡ Π°ΠΊΡΠΈΠ²Π½ΠΎΡΡΡ ΠΈ ΠΏΡΠ΅Π²ΡΠ°ΡΠΈΡΡΡΡ Π² ΠΌΠΎΠ½ΠΎΠ»ΠΈΡΠ½ΡΡ Π³Π»ΡΠ±Ρ, Π΅ΡΠ»ΠΈ Π½Π΅ ΠΏΡΠΈΠΌΠ΅Π½ΡΡΡ ΡΠΏΠ΅ΡΠΈΠ°Π»ΡΠ½ΡΠ΅ ΡΠΈΡΡΠ΅ΠΌΡ Π°ΡΡΠ°ΡΠΈΠΈ ΠΈ ΡΠ²ΠΎΠ΄ΠΎΠΎΠ±ΡΡΡΠ΅Π½ΠΈΡ. ΠΠΎΡΡΠΎΠΌΡ Π²Π΅Π΄ΡΡΠΈΠ΅ ΠΏΡΠΎΠΈΠ·Π²ΠΎΠ΄ΠΈΡΠ΅Π»ΠΈ Π±Π΅ΡΠΎΠ½Π½ΡΡ Π·Π°Π²ΠΎΠ΄ΠΎΠ² ΡΠΎΠΏΡΠΎΠ²ΠΎΠΆΠ΄Π°ΡΡ ΡΠΈΠ»ΠΎΡΡ Π΄ΠΎΠΏΠΎΠ»Π½ΠΈΡΠ΅Π»ΡΠ½ΡΠΌΠΈ ΠΎΠΏΡΠΈΡΠΌΠΈ, ΠΊΠΎΡΠΎΡΡΠ΅ ΡΠΏΠΎΡΠΎΠ±ΡΡΠ²ΡΡΡ ΠΏΠΎΠ»Π½ΠΎΡΠ΅Π½Π½ΠΎΠΌΡ Π²ΡΠΏΠΎΠ»Π½Π΅Π½ΠΈΡ ΡΠΈΠ»ΠΎΡΠΎΠΌ ΡΠ²ΠΎΠ΅Π³ΠΎ ΡΠ΅Ρ Π½ΠΎΠ»ΠΎΠ³ΠΈΡΠ΅ΡΠΊΠΎΠ³ΠΎ ΠΏΡΠ΅Π΄Π½Π°Π·Π½Π°ΡΠ΅Π½ΠΈΡ β Π²ΡΠ΅ΠΌΠ΅Π½Π½ΠΎΠ³ΠΎ Ρ ΡΠ°Π½Π΅Π½ΠΈΡ ΡΠ΅ΠΌΠ΅Π½ΡΠ° ΠΈ ΠΎΠΏΠ΅ΡΠ°ΡΠΈΠ²Π½ΠΎΠΉ Π΅Π³ΠΎ ΠΏΠΎΠ΄Π°ΡΠΈ Π½Π° Π΄ΠΎΠ·Π°ΡΠΈΡ. ΠΡΠ½ΠΎΠ²Π½ΡΠΌΠΈ ΠΎΠΏΡΠΈΡΠΌΠΈ Π΄Π»Ρ ΡΠΈΠ»ΠΎΡΠ° ΡΠ²Π»ΡΡΡΡΡ:
- ΠΠΈΡΠΊΠΎΠ²ΡΠ΅ Π·Π°ΡΠ²ΠΎΡΡ Π΄Π»Ρ ΠΈΡΡΠ΅ΡΠ΅Π½ΠΈΡ ΡΠ΅ΠΌΠ΅Π½ΡΠ° ΠΈΠ· ΡΠΈΠ»ΠΎΡΠ½ΠΎΠΉ Π΅ΠΌΠΊΠΎΡΡΠΈ;
- ΠΠ²Π°ΡΠΈΠΉΠ½ΡΠ΅ ΠΊΠ»Π°ΠΏΠ°Π½Ρ, Π·Π°ΡΠΈΡΠ°ΡΡΠΈΠ΅ ΠΌΠ΅ΡΠ°Π»Π»ΠΎΠΊΠΎΠ½ΡΡΡΡΠΊΡΠΈΡ ΡΠΈΠ»ΠΎΡΠ° ΠΎΡ ΡΠ΅Π·ΠΊΠΈΡ ΠΏΠ΅ΡΠ΅ΠΏΠ°Π΄ΠΎΠ² Π΄Π°Π²Π»Π΅Π½ΠΈΡ ΠΏΡΠΈ Π·Π°Π³ΡΡΠ·ΠΊΠ°Ρ ΠΈ Π²ΡΠ³ΡΡΠ·ΠΊΠ°Ρ ΡΠ΅ΠΌΠ΅Π½ΡΠ°;
- ΠΠ°ΡΡΠΈΠΊΠΈ ΡΡΠΎΠ²Π½Ρ;
- ΠΠΈΠ±ΡΠ°ΡΠΎΡΡ ΠΈ ΡΠΈΡΡΠ΅ΠΌΡ Π°ΡΡΠ°ΡΠΈΠΈ, ΡΠ°Π·ΡΡΡ Π»ΡΡΡΠΈΠ΅ ΡΠ΅ΠΌΠ΅Π½Ρ;
- ΠΠΎΠ·Π΄ΡΡΠ½ΡΠ΅ ΡΠΈΠ»ΡΡΡΡ;
- ΠΡΠ»ΡΡ ΡΠΏΡΠ°Π²Π»Π΅Π½ΠΈΡ ΡΠΈΠ»ΠΎΡΠΎΠΌ.
ΠΠ°ΠΊΠ»ΡΡΠ΅Π½ΠΈΠ΅
ΠΠ΅ΠΌΠ°Π»ΠΎΠ²Π°ΠΆΠ½ΡΠΌ ΡΠ°ΠΊΡΠΎΡΠΎΠΌ ΠΏΡΠΈ Π²ΡΠ±ΠΎΡΠ΅ ΠΎΠΏΡΠΈΠΉ ΠΏΠΎΠ΄ ΠΏΡΠΈΠΎΠ±ΡΠ΅ΡΠ°Π΅ΠΌΡΠΉ ΡΠΈΠ»ΠΎΡ ΡΠ²Π»ΡΠ΅ΡΡΡ ΠΈΡ Π°Π΄Π°ΠΏΡΠΈΡΠΎΠ²Π°Π½Π½ΠΎΡΡΡ ΠΏΠΎΠ΄ ΠΊΠΎΠ½ΠΊΡΠ΅ΡΠ½ΡΠΉ Π±Π΅ΡΠΎΠ½Π½ΡΠΉ Π·Π°Π²ΠΎΠ΄, ΠΏΡΠ΅Π΄Π»Π°Π³Π°Π΅ΠΌΡΠΉ ΠΏΡΠΎΠΈΠ·Π²ΠΎΠ΄ΠΈΡΠ΅Π»ΡΠΌΠΈ ΠΠ‘Π£. ΠΠΎΠΊΡΠΏΠ°ΡΠ΅Π»Ρ ΠΈΠ·Π±Π°Π²Π»Π΅Π½ ΠΎΡ Π½Π΅ΠΎΠ±Ρ ΠΎΠ΄ΠΈΠΌΠΎΡΡΠΈ ΠΏΠΎΠ΄Π±ΠΈΡΠ°ΡΡ ΠΎΠΏΡΠΈΠΈ Π½ΡΠΆΠ½ΡΡ Ρ Π°ΡΠ°ΠΊΡΠ΅ΡΠΈΡΡΠΈΠΊ, ΠΊΠΎΠ³Π΄Π° Π±ΡΠ΄Π΅Ρ Π²ΡΠ½ΡΠΆΠ΄Π΅Π½ Π²ΡΡΠΈΠ΄ΠΎΡΠΎΠ³Π° Π΄ΠΎΠΎΡΠ½Π°ΡΠ°ΡΡ ΡΡΡΠ°Π½ΠΎΠ²Π»Π΅Π½Π½ΡΠΉ Ρ ΡΠ΅Π±Ρ ΡΠΈΠ»ΠΎΡ. Π’Π΅ΠΌ ΡΠ°ΠΌΡΠΌ ΡΡΠΊΠΎΠ½ΠΎΠΌΠ»Π΅Π½Ρ Π·Π½Π°ΡΠΈΡΠ΅Π»ΡΠ½ΡΠ΅ ΡΡΠΌΠΌΡ, ΠΌΠ½ΠΎΠ³ΠΎΠΊΡΠ°ΡΠ½ΠΎ ΠΏΡΠ΅Π²ΡΡΠ°ΡΡΠΈΠ΅ Π΅Π³ΠΎ ΠΊΠ°ΠΆΡΡΠΈΠΉΡΡ Π²ΡΠΈΠ³ΡΡΡ Π² ΡΠ΅Π½Π΅ ΠΏΡΠΈ ΠΏΠΎΠΊΡΠΏΠΊΠ΅ ΡΠΈΠ»ΠΎΡΠ° Π±Π΅Π· Π·Π°Π²ΠΎΠ΄ΡΠΊΠΎΠ³ΠΎ ΠΎΡΠ½Π°ΡΠ΅Π½ΠΈΡ.
zzbo.ru
ΠΠ°ΠΊΠΈΠ΅ ΠΎΡΠΈΠ±ΠΊΠΈ ΠΏΡΠΈΠ²ΠΎΠ΄ΡΡ ΠΊ ΡΠ°Π·ΡΡΡΠ΅Π½ΠΈΡ ΡΠΈΠ»ΠΎΡΠΎΠ²? β Elevatorist.com
Π Π°Π·ΡΡΡΠ΅Π½Π½ΡΠ΅ ΡΠΈΠ»ΠΎΡΡ β ΡΡΡΠ΅ΠΊΡΠ½ΠΎΠ΅ Π·ΡΠ΅Π»ΠΈΡΠ΅ Π΄Π»Ρ Π·Π΅Π²Π°ΠΊ, ΠΎΠ΄Π½Π°ΠΊΠΎ ΡΠΎΠ²ΡΠ΅ΠΌ Π½Π΅ Π²Π΅ΡΠ΅Π»ΠΎΠ΅ ΡΠ²Π»Π΅Π½ΠΈΠ΅ Π΄Π»Ρ ΡΠ΅Ρ , ΠΊΡΠΎ ΠΏΡΠΈΡΠ°ΡΡΠ΅Π½ ΠΊ ΡΡΠΎΠΌΡ ΡΠΎΠΎΡΡΠΆΠ΅Π½ΠΈΡ. ΠΠ°ΠΆΠ΄ΠΎΠ΅ ΡΠ°ΠΊΠΎΠ΅ Π§Π Π½Π΅ΡΠ΅Ρ Π·Π° ΡΠΎΠ±ΠΎΠΉ ΠΎΠ³ΡΠΎΠΌΠ½ΡΠ΅ ΡΠ±ΡΡΠΊΠΈ, Π° Π² Ρ ΡΠ΄ΡΠ΅ΠΌ ΡΠ»ΡΡΠ°Π΅ β Π΅ΡΠ΅ ΠΈ ΡΠΌΠ΅ΡΡΡ Π»ΡΠ΄Π΅ΠΉ. Π‘ ΠΏΠΎΠΌΠΎΡΡΡ ΠΊΠ²Π°Π»ΠΈΡΠΈΡΠΈΡΠΎΠ²Π°Π½Π½ΡΡ ΡΠΊΡΠΏΠ΅ΡΡΠΎΠ²-ΠΏΡΠ°ΠΊΡΠΈΠΊΠΎΠ² ΠΌΡ ΠΏΠΎΠΏΡΠΎΠ±ΠΎΠ²Π°Π»ΠΈ ΠΎΠ±ΠΎΠ·Π½Π°ΡΠΈΡΡ ΠΎΡΠ½ΠΎΠ²Π½ΡΠ΅ ΠΎΡΠΈΠ±ΠΊΠΈ, ΠΊΠΎΡΠΎΡΡΠ΅ ΠΏΡΠΈΠ²ΠΎΠ΄ΡΡ ΠΊ ΠΏΠΎΠ²ΡΠ΅ΠΆΠ΄Π΅Π½ΠΈΡΠΌ ΡΠΈΠ»ΠΎΡΠΎΠ².
ΠΠ‘Π ΠΠΠ§ΠΠΠΠΠ’Π‘Π― Π‘ ΠΠ ΠΠΠΠ’Π
Β«ΠΠ°ΠΏΡΠΎΠ³ΡΠ°ΠΌΠΌΠΈΡΠΎΠ²Π°ΡΡΒ» ΡΠ°Π·ΡΡΡΠ΅Π½ΠΈΡ Π΅ΠΌΠΊΠΎΡΡΠΈ Π΄Π»Ρ Ρ ΡΠ°Π½Π΅Π½ΠΈΡ Π·Π΅ΡΠ½Π° ΠΌΠΎΠΆΠ½ΠΎ ΡΠΆΠ΅ Π½Π° ΡΡΠΎΠ²Π½Π΅ ΠΏΡΠΎΠ΅ΠΊΡΠ°. ΠΠ»Ρ ΡΡΠΎΠ³ΠΎ Π΄ΠΎΡΡΠ°ΡΠΎΡΠ½ΠΎ ΡΠΏΡΡΡΠΈΡΡ ΡΡΠ΄ ΠΎΡΠ΅Π½Ρ Π²Π°ΠΆΠ½ΡΡ ΡΠ°ΠΊΡΠΎΡΠΎΠ², ΡΠ²ΡΠ·Π°Π½Π½ΡΡ Ρ Π½Π°Π³ΡΡΠ·ΠΊΠ°ΠΌΠΈ Π½Π° ΡΠΈΠ»ΠΎΡ.
ΠΡ ΠΏΠ΅ΡΠ΅ΡΠΈΡΠ»ΡΠ΅Ρ Π½Π°ΡΠ°Π»ΡΠ½ΠΈΠΊ ΠΏΡΠΎΠ΅ΠΊΡΠ½ΠΎΠ³ΠΎ ΡΠΏΡΠ°Π²Π»Π΅Π½ΠΈΡ ΠΠ Β«ΠΠ΅ΡΠ½ΠΎΠ²Π°Ρ CΡΠΎΠ»ΠΈΡΠ°Β» ΠΠ³ΠΎΡΡ ΠΠ΅Π»Π°Π½.
ΠΠΎ Π΅Π³ΠΎ ΡΠ»ΠΎΠ²Π°ΠΌ, Π½Π΅Π»ΡΠ·Ρ Π²ΡΠΏΠΎΠ»Π½ΡΡΡ ΠΏΡΠΎΠ΅ΠΊΡΠ½ΡΠ΅ ΡΠ°ΡΡΠ΅ΡΡ ΠΎΡΠ½ΠΎΠ²Π°Π½ΠΈΠΉ ΡΠΈΠ»ΠΎΡΠ° Π±Π΅Π· ΡΡΠ΅ΡΠ° ΠΊΠΎΠ»ΠΈΡΠ΅ΡΡΠ²Π° ΡΠΈΠΊΠ»ΠΎΠ² Π·Π°Π³ΡΡΠ·ΠΊΠΈ ΠΈ Π²ΡΠ³ΡΡΠ·ΠΊΠΈ, Π° ΡΠ°ΠΊΠΆΠ΅ ΠΎΡΠΎΠ±Π΅Π½Π½ΠΎΡΡΠ΅ΠΉ ΠΈΡΡΠ΅ΡΠ΅Π½ΠΈΡ Π·Π΅ΡΠ½Π° ΠΊΠ°ΠΊ ΡΡΠΏΡΡΠ΅ΠΉ ΡΡΠ΅Π΄Ρ. ΠΡΠ΅Π½Ρ Π²Π°ΠΆΠ½ΠΎ ΠΏΡΠΈΠ½ΠΈΠΌΠ°ΡΡ Π²ΠΎ Π²Π½ΠΈΠΌΠ°Π½ΠΈΠ΅ ΡΡΠΈΠ»ΠΈΡ, Π²ΠΎΠ·Π½ΠΈΠΊΠ°ΡΡΠΈΠ΅ Π²Π½ΡΡΡΠΈ ΡΠΈΠ»ΠΎΡΠ° Π·Π° ΡΡΠ΅Ρ Π΄Π΅ΠΉΡΡΠ²ΠΈΡ Π½Π° Π½Π΅Π³ΠΎ Π·Π΅ΡΠ½Π°. ΠΡΠΆΠ½ΠΎ ΡΠ°ΠΊΠΆΠ΅ Π·Π½Π°ΡΡ ΡΡΠ΅Π±ΠΎΠ²Π°Π½ΠΈΡ ΠΊ Π²Π΅Π»ΠΈΡΠΈΠ½Π΅ ΠΌΠ°ΠΊΡΠΈΠΌΠ°Π»ΡΠ½ΠΎ Π΄ΠΎΠΏΡΡΡΠΈΠΌΡΡ ΡΠ°Π²Π½ΠΎΠΌΠ΅ΡΠ½ΡΡ ΠΈ Π½Π΅ΡΠ°Π²Π½ΠΎΠΌΠ΅ΡΠ½ΡΡ ΠΎΡΠ°Π΄ΠΎΠΊ ΡΠΈΠ»ΠΎΡΠ° (ΠΌΠ°ΠΊΡΠΈΠΌΠ°Π»ΡΠ½ΠΎ Π΄ΠΎΠΏΡΡΡΠΈΠΌΡΠΉ ΠΊΡΠ΅Π½).
ΠΠ³ΠΎΡΡ ΠΠ΅Π»Π°Π½ ΠΏΠΎΠ΄ΡΠ΅ΡΠΊΠΈΠ²Π°Π΅Ρ, ΡΡΠΎ ΠΊ ΠΏΠ»Π°ΡΠ΅Π²Π½ΡΠΌ ΠΏΠΎΡΠ»Π΅Π΄ΡΡΠ²ΠΈΡΠΌ ΠΏΡΠΈΠ²ΠΎΠ΄ΠΈΡ ΠΈΠ³Π½ΠΎΡΠΈΡΠΎΠ²Π°Π½ΠΈΠ΅ ΠΏΡΠΎΠ΅ΠΊΡΠ°Π½ΡΠ°ΠΌΠΈ ΡΠ°ΠΊΠΈΡ ΠΏΠ°ΡΠ°ΠΌΠ΅ΡΡΠΎΠ², ΠΊΠ°ΠΊ Π²Π΅ΡΡΠΎΠ²ΡΠ΅ ΠΈ ΡΠ½Π΅Π³ΠΎΠ²ΡΠ΅ Π½Π°Π³ΡΡΠ·ΠΊΠΈ Π² ΡΠ΅Π³ΠΈΠΎΠ½Π΅, ΠΏΡΠΈΡΠΎΠ΄Π½Π°Ρ ΠΈ ΡΠ΅Ρ Π½ΠΎΠ³Π΅Π½Π½Π°Ρ ΡΠ΅ΠΉΡΠΌΠΈΡΠ½ΠΎΡΡΡ.
ΠΠ½ ΡΠ±Π΅ΠΆΠ΄Π΅Π½, ΡΡΠΎ ΠΎΠ±ΡΠ·Π°ΡΠ΅Π»ΡΠ½ΠΎ Π½ΡΠΆΠ½ΠΎ ΡΡΠΈΡΡΠ²Π°ΡΡ ΠΎΡΠΎΠ±Π΅Π½Π½ΠΎΡΡΠΈ Π³ΡΡΠ½ΡΠ°: Π½Π°Π»ΠΈΡΠΈΠ΅ Π³ΡΡΠ½ΡΠΎΠ²ΡΡ Π²ΠΎΠ΄, ΠΈΡ Π°Π³ΡΠ΅ΡΡΠΈΠ²Π½ΠΎΡΡΡ ΠΊ Π±Π΅ΡΠΎΠ½Ρ ΠΈ ΠΌΠ΅ΡΠ°Π»Π»Ρ; ΠΏΡΠΎΡΠ°Π΄ΠΎΡΠ½ΡΠ΅ ΠΈ ΠΏΡΡΠΈΠ½ΠΈΡΡΡΠ΅ ΡΠ²ΠΎΠΉΡΡΠ²Π° Π³ΡΡΠ½ΡΠΎΠ² ΠΎΡΠ½ΠΎΠ²Π°Π½ΠΈΡ; Π½Π°Π»ΠΈΡΠΈΠ΅ ΠΎΠΏΠΎΠ»Π·Π½Π΅Π²ΡΡ ΡΠ²Π»Π΅Π½ΠΈΠΉ, Π° ΡΠ°ΠΊΠΆΠ΅ Π°Π³ΡΠ΅ΡΡΠΈΠ²Π½ΡΡ ΡΡΠ΅Π΄ Π² Π°ΡΠΌΠΎΡΡΠ΅ΡΠ΅ Π² ΡΠ°ΠΉΠΎΠ½Π΅ ΡΡΡΠΎΠΈΡΠ΅Π»ΡΡΡΠ²Π°.
Β«ΠΡΠΈ ΡΠ°Π·ΠΌΠ΅ΡΠ΅Π½ΠΈΠΈ Π·Π°ΠΊΠ°Π·Π° Π½Π° ΠΈΠ·Π³ΠΎΡΠΎΠ²Π»Π΅Π½ΠΈΠ΅ ΡΠΈΠ»ΠΎΡΠΎΠ² Π½Π΅ΠΎΠ±Ρ ΠΎΠ΄ΠΈΠΌΠΎ ΡΠΊΠ°Π·ΡΠ²Π°ΡΡ ΡΠ°ΠΉΠΎΠ½ ΡΡΡΠΎΠΈΡΠ΅Π»ΡΡΡΠ²Π° ΠΈ Π΅Π³ΠΎ ΠΎΡΠΎΠ±ΡΠ΅ Ρ Π°ΡΠ°ΠΊΡΠ΅ΡΠΈΡΡΠΈΠΊΠΈ, Π° ΡΠ°ΠΊΠΆΠ΅ ΡΡΠ»ΠΎΠ²ΠΈΡ ΠΏΠ»Π°Π½ΠΈΡΡΠ΅ΠΌΠΎΠΉ ΡΠΊΡΠΏΠ»ΡΠ°ΡΠ°ΡΠΈΠΈ ΡΠΈΠ»ΠΎΡΠΎΠ². ΠΡΠΈ ΡΡΠΎΠΌ ΠΎΡ Π·Π°Π²ΠΎΠ΄Π°-ΠΈΠ·Π³ΠΎΡΠΎΠ²ΠΈΡΠ΅Π»Ρ ΠΎΠ±ΡΠ·Π°ΡΠ΅Π»ΡΠ½ΠΎ Π½ΡΠΆΠ½ΠΎ ΠΏΠΎΠ»ΡΡΠΈΡΡ ΠΏΠΎΠ΄ΡΠ²Π΅ΡΠΆΠ΄Π΅Π½ΠΈΠ΅, ΡΡΠΎ Π²ΡΠ΅ ΡΡΠ»ΠΎΠ²ΠΈΡ ΡΡΡΠ΅Π½Ρ Π² ΠΊΠΎΠ½ΡΡΡΡΠΊΡΠΈΠΈ ΡΠΈΠ»ΠΎΡΠ°Β», β ΠΏΠΎΠ΄ΡΠ΅ΡΠΊΠΈΠ²Π°Π΅Ρ Π½Π°ΡΠ°Π»ΡΠ½ΠΈΠΊ ΠΏΡΠΎΠ΅ΠΊΡΠ½ΠΎΠ³ΠΎ ΡΠΏΡΠ°Π²Π»Π΅Π½ΠΈΡ ΠΠ Β«ΠΠ΅ΡΠ½ΠΎΠ²Π°Ρ Π‘ΡΠΎΠ»ΠΈΡΠ°Β».
ΠΠΎΠ½ΡΡΠ½ΠΎ, ΡΡΠΎ Π·Π°ΠΊΠ°Π·ΡΠΈΠΊ ΡΠ°ΠΌΠΎΡΡΠΎΡΡΠ΅Π»ΡΠ½ΠΎ Π½Π΅ ΠΌΠΎΠΆΠ΅Ρ ΠΏΠ΅ΡΠ΅ΠΏΡΠΎΠ²Π΅ΡΠΈΡΡ, ΡΡΠ΅Π» Π»ΠΈ ΠΏΡΠΎΠ΅ΠΊΡΠΈΡΠΎΠ²ΡΠΈΠΊ Π²ΡΠ΅ ΡΡΠΈ ΠΏΠ°ΡΠ°ΠΌΠ΅ΡΡΡ. ΠΠΎΡΡΠΎΠΌΡ, ΠΏΠ΅ΡΠ²ΠΎΠ΅, ΡΡΠΎ Π½Π΅ΠΎΠ±Ρ ΠΎΠ΄ΠΈΠΌΠΎ ΡΠ΄Π΅Π»Π°ΡΡ β Π½Π°ΠΉΡΠΈ Ρ ΠΎΡΠΎΡΡΡ ΠΏΡΠΎΠ΅ΠΊΡΠ½ΡΡ ΠΎΡΠ³Π°Π½ΠΈΠ·Π°ΡΠΈΡ.
Β«ΠΠ²Π°Π»ΠΈΡΠΈΠΊΠ°ΡΠΈΡ Π»ΡΠ±ΡΡ ΡΠΏΠ΅ΡΠΈΠ°Π»ΠΈΡΡΠΎΠ² Π»Π΅Π³ΠΊΠΎ ΠΏΡΠΎΠ²Π΅ΡΠΈΡΡ. ΠΠΎΡΡΠ°ΡΠΎΡΠ½ΠΎ ΡΠ·Π½Π°ΡΡ ΡΡΠ΄ΡΠ±Ρ ΠΈΡ ΠΎΠ±ΡΠ΅ΠΊΡΠΎΠ². ΠΠ²Π° ΠΎΡΠ½ΠΎΠ²Π½ΡΡ Π°ΡΠΏΠ΅ΠΊΡΠ°, ΠΊΠΎΡΠΎΡΡΠ΅ Π½Π΅ΠΎΠ±Ρ ΠΎΠ΄ΠΈΠΌΠΎ ΠΎΠ±ΡΠ·Π°ΡΠ΅Π»ΡΠ½ΠΎ ΠΏΡΠΎΠ²Π΅ΡΠΈΡΡ Π½Π°Π»ΠΈΡΠΈΠ΅ ΠΎΠΏΡΡΠ½ΠΎΠ³ΠΎ ΡΠ΅Ρ Π½ΠΎΠ»ΠΎΠ³Π° (ΠΎΠΏΡΡ ΡΠ°Π±ΠΎΡΡ Π½Π΅ ΠΌΠ΅Π½Π΅Π΅ 5 Π»Π΅Ρ). Π Π½Π°Π»ΠΈΡΠΈΠ΅ ΠΎΠΏΡΡΠ½ΠΎΠ³ΠΎ ΡΡΡΠΎΠΈΡΠ΅Π»Ρ-ΠΊΠΎΠ½ΡΡΡΡΠΊΡΠΎΡΠ° ΠΏΠΎ Π±Π΅ΡΠΎΠ½Ρ ΠΈ ΠΌΠ΅ΡΠ°Π»Π»Ρ ΠΎΠΏΡΡ ΡΠ°Π±ΠΎΡΡ 5-7 Π»Π΅Ρ. ΠΡΠ»ΠΈ ΡΡΠΈ Π»ΡΠ΄ΠΈ Π΅ΡΡΡ ΠΈ Π²Ρ ΡΠ±Π΅Π΄ΠΈΡΠ΅ΡΡ Π² ΠΈΡ ΡΡΠΎΠ²Π½Π΅ ΠΊΠ²Π°Π»ΠΈΡΠΈΠΊΠ°ΡΠΈΠΈ, ΠΌΠΎΠΆΠ½ΠΎ Π·Π°ΠΊΠ»ΡΡΠ°ΡΡ ΠΊΠΎΠ½ΡΡΠ°ΠΊΡΒ», β ΡΠ°ΠΊΠΎΠΉ ΡΠΎΠ²Π΅Ρ Π΄Π°Π΅Ρ ΡΠ΅Ρ Π½ΠΈΡΠ΅ΡΠΊΠΈΠΉ Π΄ΠΈΡΠ΅ΠΊΡΠΎΡ Β«ΠΠ½ΡΠ΅ΡΠΏΡΠΎΠ΅ΠΊΡ GmbHΒ» ΠΠ²Π°Π½ ΠΡΠ½Ρ.
ΠΠ’Π ΠΠ£ΠΠΠ’ Π‘Π’Π ΠΠΠ’Π¬ Π ΠΠΠΠ’ΠΠ ΠΠΠΠ’Π¬?
Π’ΡΠ°ΡΠ΅Π»ΡΠ½ΠΎ ΠΏΠΎΠ΄Π±ΠΈΡΠ°ΡΡ Π½ΡΠΆΠ½ΠΎ Π½Π΅ ΡΠΎΠ»ΡΠΊΠΎ ΠΏΡΠΎΠ΅ΠΊΡΠΈΡΠΎΠ²ΡΠΈΠΊΠΎΠ², Π½ΠΎ ΡΠ°ΠΊΠΆΠ΅ ΡΡΡΠΎΠΈΡΠ΅Π»Π΅ΠΉ ΠΈ ΠΌΠΎΠ½ΡΠ°ΠΆΠ½ΠΈΠΊΠΎΠ². ΠΠ΅ΠΊΠ²Π°Π»ΠΈΡΠΈΡΠΈΡΠΎΠ²Π°Π½Π½ΠΎ Π²ΡΠΏΠΎΠ»Π½Π΅Π½Π½ΠΎΠΉ ΡΠ°Π±ΠΎΡΠΎΠΉ ΠΎΠ½ΠΈ ΠΌΠΎΠ³ΡΡ ΠΈΡΠΏΠΎΡΡΠΈΡΡ ΠΊΠ°ΠΊ Ρ ΠΎΡΠΎΡΠΈΠΉ ΠΏΡΠΎΠ΅ΠΊΡ, ΡΠ°ΠΊ ΠΈ ΠΊΠ°ΡΠ΅ΡΡΠ²Π΅Π½Π½ΠΎΠ΅ ΠΎΠ±ΠΎΡΡΠ΄ΠΎΠ²Π°Π½ΠΈΠ΅.
Β«ΠΠ΄Π΅-ΡΠΎ ΡΡΠΊΠΎΠ½ΠΎΠΌΠΈΠ»ΠΈ, Π³Π΄Π΅-ΡΠΎ Π½Π΅Π΄ΠΎΡΠΌΠΎΡΡΠ΅Π»ΠΈ, ΠΏΡΠΈΠΌΠ΅Π½ΠΈΠ»ΠΈ Π½Π΅ ΡΠ΅ ΠΌΠ°ΡΠ΅ΡΠΈΠ°Π»Ρ, ΠΎΡΠΊΠ»ΠΎΠ½ΠΈΠ»ΠΈΡΡ ΠΎΡ ΠΏΡΠΎΠ΅ΠΊΡΠ° β Π²ΠΎΡ ΠΈ ΠΆΠ΄ΠΈ Π±Π΅Π΄ΡΒ», β Π³ΠΎΠ²ΠΎΡΠΈΡ Π·Π°ΠΌ. Π½Π°ΡΠ°Π»ΡΠ½ΠΈΠΊΠ° ΠΊΠΎΠΌΠΌΠ΅ΡΡΠ΅ΡΠΊΠΎΠ³ΠΎ Π΄Π΅ΠΏΠ°ΡΡΠ°ΠΌΠ΅Π½ΡΠ° ΠΠ Β«ΠΠ΅ΡΠ½ΠΎΠ²Π°Ρ Π‘ΡΠΎΠ»ΠΈΡΠ°Β» ΠΠΈΡΠ°Π»ΠΈΠΉ ΠΠ°ΡΡΠ΅Π½ΠΊΠΎ.
Π ΡΠ΅Ρ Π½ΠΈΡΠ΅ΡΠΊΠΈΠΉ Π΄ΠΈΡΠ΅ΠΊΡΠΎΡ Β«ΠΠ½ΡΠ΅ΡΠΏΡΠΎΠ΅ΠΊΡ GmbHΒ» ΠΠ²Π°Π½ ΠΡΠ½Ρ ΠΏΡΠ΅Π΄ΡΠΏΡΠ΅ΠΆΠ΄Π°Π΅Ρ, ΡΡΠΎ ΡΡΡΠΎΠΈΡΠ΅Π»ΡΠ½Π°Ρ ΠΊΠΎΠΌΠΏΠ°Π½ΠΈΡ, ΠΊΠΎΡΠΎΡΡΡ Π²Ρ Π½Π°Π½ΠΈΠΌΠ°Π΅ΡΠ΅, Π² ΠΏΠ΅ΡΠ²ΡΡ ΠΎΡΠ΅ΡΠ΅Π΄Ρ Π΄ΠΎΠ»ΠΆΠ½Π° ΠΈΠΌΠ΅ΡΡ ΠΎΠΏΡΡ ΡΡΡΠΎΠΈΡΠ΅Π»ΡΡΡΠ²Π° ΡΡΠ½Π΄Π°ΠΌΠ΅Π½ΡΠΎΠ² Π΄Π»Ρ ΡΠΈΠ»ΠΎΡΠ°, Π° ΠΌΠΎΠ½ΡΠ°ΠΆΠ½ΠΈΠΊΠΈ β ΠΎΠΏΡΡ ΡΠ±ΠΎΡΠΊΠΈ Π΅ΠΌΠΊΠΎΡΡΠ΅ΠΉ Π΄Π»Ρ Ρ ΡΠ°Π½Π΅Π½ΠΈΡ Π·Π΅ΡΠ½Π°.
Β«ΠΠ°Π΄ΠΎ ΠΎΡΠ΅Π½Ρ ΡΠΎΠ½ΠΊΠΎ ΠΏΠΎΠ΄Ρ ΠΎΠ΄ΠΈΡΡ ΠΊ ΠΏΠΎΠ΄Π±ΠΎΡΡ ΡΡΡΠΎΠΈΡΠ΅Π»Π΅ΠΉ. Π£ ΡΠ°ΠΌΠΎΠΉ Ρ ΠΎΡΠΎΡΠ΅ΠΉ ΠΊΠΎΠΌΠΏΠ°Π½ΠΈΠΈ Π² ΡΠ°Π·Π³Π°Ρ ΡΠ΅Π·ΠΎΠ½Π° ΡΠ°Π±ΠΎΡΠ°Π΅Ρ Π½Π΅ΡΠΊΠΎΠ»ΡΠΊΠΎ Π±ΡΠΈΠ³Π°Π΄. ΠΡΠΈ ΡΡΠΎΠΌ Π½Π΅ Ρ Π²ΡΠ΅Ρ ΡΠ°Π±ΠΎΡΠ½ΠΈΠΊΠΎΠ² Π΅ΡΡΡ ΠΎΠΏΡΡ ΡΡΡΠΎΠΈΡΠ΅Π»ΡΡΡΠ²Π° ΡΠ»Π΅Π²Π°ΡΠΎΡΠΎΠ². ΠΠΎΡΡΠΎΠΌΡ Π½Π°Π΄ΠΎ ΡΠΌΠΎΡΡΠ΅ΡΡ Π½Π° ΠΊΠ²Π°Π»ΠΈΡΠΈΠΊΠ°ΡΠΈΡ ΠΊΠΎΠ½ΠΊΡΠ΅ΡΠ½ΡΡ Π»ΡΠ΄Π΅ΠΉ, Π° Π½Π΅ Π½Π° ΠΈΠΌΡ ΠΊΠΎΠΌΠΏΠ°Π½ΠΈΠΈ. ΠΡΠΎΠ±Π΅Π½Π½ΠΎΠ΅ Π²Π½ΠΈΠΌΠ°Π½ΠΈΠ΅ Π½ΡΠΆΠ½ΠΎ ΡΠ΄Π΅Π»ΡΡΡ ΠΊΠ²Π°Π»ΠΈΡΠΈΠΊΠ°ΡΠΈΠΈ ΠΏΡΠΎΡΠ°Π±Π°. ΠΡ ΡΡΠΎΠ³ΠΎ ΡΠ΅Π»ΠΎΠ²Π΅ΠΊΠ° Π·Π°Π²ΠΈΡΠΈΡ ΠΎΡΠ΅Π½Ρ ΠΌΠ½ΠΎΠ³ΠΎΠ΅Β», β ΡΠ΅ΠΊΠΎΠΌΠ΅Π½Π΄ΡΠ΅Ρ ΠΠ²Π°Π½ ΠΡΠ½Ρ.
ΠΡΠ΅ ΠΎΠ΄ΠΈΠ½ Π²Π°ΠΆΠ½ΡΠΉ ΡΠΏΠ΅ΡΠΈΠ°Π»ΠΈΡΡ, ΠΎΡ ΠΊΠΎΡΠΎΡΠΎΠ³ΠΎ Π²ΠΎ ΠΌΠ½ΠΎΠ³ΠΎΠΌ Π·Π°Π²ΠΈΡΠΈΡ ΡΡΠ΄ΡΠ±Π° ΡΠΈΠ»ΠΎΡΠΎΠ² β ΡΡΠΎ ΡΠ΅Ρ-ΠΌΠΎΠ½ΡΠ°ΠΆΠ½ΠΈΠΊ. ΠΠ½ ΡΠ»Π΅Π΄ΠΈΡ Π·Π° ΡΠ΅ΠΌ, ΡΡΠΎΠ±Ρ ΠΊΠΎΠ½ΡΡΡΡΠΊΡΠΈΡ Π±ΡΠ»Π° ΡΠΎΠ±ΡΠ°Π½Π° ΡΡΡΠΎΠ³ΠΎ ΠΏΠΎ ΡΡ Π΅ΠΌΠ°ΠΌ Π·Π°Π²ΠΎΠ΄Π°-ΠΈΠ·Π³ΠΎΡΠΎΠ²ΠΈΡΠ΅Π»Ρ.
Β«ΠΠΎΠ³Π΄Π° ΠΎΠ±ΡΠ΅ΠΌ ΡΠΈΠ»ΠΎΡΠ° Π½Π΅Π±ΠΎΠ»ΡΡΠΎΠΉ ΠΈ Π΅ΡΡΡ ΡΠ΅Ρ-ΠΌΠΎΠ½ΡΠ°ΠΆΠ½ΠΈΠΊ, ΡΠΎ ΠΊΠ²Π°Π»ΠΈΡΠΈΠΊΠ°ΡΠΈΡ ΡΠΏΠ΅ΡΠΈΠ°Π»ΠΈΡΡΠΎΠ² ΠΌΠΎΠΆΠ΅Ρ Π±ΡΡΡ ΡΠ΄ΠΎΠ²Π»Π΅ΡΠ²ΠΎΡΠΈΡΠ΅Π»ΡΠ½Π°Ρ. ΠΠΎ, Π΅ΡΠ»ΠΈ ΠΌΡ Π³ΠΎΠ²ΠΎΡΠΈΠΌ ΠΎ Π±ΠΎΠ»ΡΡΠΈΡ ΡΠΈΠ»ΠΎΡΠ°Ρ , ΡΠΊΠ°ΠΆΠ΅ΠΌ, Π²ΠΌΠ΅ΡΡΠΈΠΌΠΎΡΡΡΡ 6, 10, 15 ΡΡΡ. Ρ, ΡΠΎ ΠΎΡΠΎΠ±ΠΎΠ΅ Π²Π½ΠΈΠΌΠ°Π½ΠΈΠ΅ Π½ΡΠΆΠ½ΠΎ ΡΠ΄Π΅Π»ΠΈΡΡ ΠΈ ΠΊΠ²Π°Π»ΠΈΡΠΈΠΊΠ°ΡΠΈΠΈ Π±ΡΠΈΠ³Π°Π΄Ρ, ΠΊΠΎΡΠΎΡΠ°Ρ Π΅Π³ΠΎ ΡΠΎΠ±ΠΈΡΠ°Π΅Ρ, ΠΈ ΡΠΎΠΉ ΠΎΡΠ½Π°ΡΡΠΊΠ΅, ΠΏΡΠΈ ΠΏΠΎΠΌΠΎΡΠΈ ΠΊΠΎΡΠΎΡΠΎΠΉ Π΅Π³ΠΎ ΡΠΎΠ±ΠΈΡΠ°ΡΡ. ΠΡΠ±ΠΎΠΉ ΡΠΈΠ»ΠΎΡ ΠΌΠΎΠΆΠ½ΠΎ ΠΈΡΠΏΠΎΡΡΠΈΡΡ Π½Π° ΡΡΠ°Π΄ΠΈΠΈ ΠΌΠΎΠ½ΡΠ°ΠΆΠ°Β», β ΠΏΠΎΠ΄ΡΠ΅ΡΠΊΠΈΠ²Π°Π΅Ρ ΠΠΈΡΠ°Π»ΠΈΠΉ ΠΠ°ΡΡΠ΅Π½ΠΊΠΎ.
ΠΠΠΠΠ§ΠΠ‘Π’ΠΠΠΠΠ«Π ΠΠΠ’ΠΠ Π ΠΠΠ ΠΠΠ’ΠΠ
ΠΠ°ΠΆΠ½ΡΠΌ Π°ΡΠΏΠ΅ΠΊΡΠΎΠΌ ΠΊΠ°ΡΠ΅ΡΡΠ²Π° ΠΈ Π΄ΠΎΠ»Π³ΠΎΠ²Π΅ΡΠ½ΠΎΡΡΠΈ ΡΠ»Π΅Π²Π°ΡΠΎΡΠ° ΡΠ²Π»ΡΠ΅ΡΡΡ ΡΡΠ½Π΄Π°ΠΌΠ΅Π½Ρ ΠΈ ΡΠΎΠΎΡΠ²Π΅ΡΡΡΠ²Π΅Π½Π½ΠΎ Π±Π΅ΡΠΎΠ½ ΠΈΠ· ΠΊΠΎΡΠΎΡΠΎΠ³ΠΎ ΠΎΠ½ ΡΠ΄Π΅Π»Π°Π½. ΠΠΎ ΠΌΠ½Π΅Π½ΠΈΡ ΡΠ΅Ρ Π½ΠΈΡΠ΅ΡΠΊΠΎΠ³ΠΎ Π΄ΠΈΡΠ΅ΠΊΡΠΎΡΠ° Β«ΠΠ½ΡΠ΅ΡΠΏΡΠΎΠ΅ΠΊΡ GmbHΒ» ΠΠ²Π°Π½Π° ΠΡΠ½Ρ, Π±Π΅ΡΠΎΠ½ Π½ΡΠΆΠ½ΠΎ ΠΏΡΠΎΠ²Π΅ΡΡΡΡ Π΄ΠΎ ΡΠΎΠ³ΠΎ, ΠΊΠ°ΠΊ ΠΎΠ½ ΠΏΠΎΡΠ²ΠΈΠ»ΡΡ Π½Π° ΡΡΡΠΎΠΉΠΊΠ΅.
Β«Π ΠΌΠΎΠΌΠ΅Π½Ρ Π·Π°Π»ΠΈΠ²ΠΊΠΈ Π½Π΅ ΠΏΠΎΠ½ΡΡΠ½ΠΎ, ΡΡΠΎ Π·Π°Π»ΠΈΠ²Π°ΡΡ. Π Π΅Π·ΡΠ»ΡΡΠ°Ρ Π²ΠΈΠ΄Π΅Π½ ΡΠΆΠ΅ ΠΏΠΎΡΠ»Π΅ ΡΠΎΠ³ΠΎ, ΠΊΠ°ΠΊ Π±Π΅ΡΠΎΠ½ Π·Π°Π»ΠΈΡ. ΠΠΎΡΡΠΎΠΌΡ Π½Π°Π΄ΠΎ Π΅Ρ Π°ΡΡ Π½Π° Π·Π°Π²ΠΎΠ΄ ΠΈ ΡΠΌΠΎΡΡΠ΅ΡΡ, ΠΊΠ°ΠΊ ΡΡΠΎΡ ΡΠ°ΡΡΠ²ΠΎΡ Π΄Π΅Π»Π°Π΅ΡΡΡ. Π£Π·Π½Π°Π²Π°ΡΡ ΠΊΠ°ΡΠ΅ΡΡΠ²ΠΎ ΡΠ΅ΠΌΠ΅Π½ΡΠ°, ΠΊΠ°ΡΠ΅ΡΡΠ²Π° ΡΠ΅Π±Π½Ρ, ΠΏΠ΅ΡΠΊΠ°, ΡΠΎΠΎΡΠ½ΠΎΡΠ΅Π½ΠΈΠ΅ Π²ΡΠ΅Ρ ΡΠ»Π΅ΠΌΠ΅Π½ΡΠΎΠ², ΠΈΠ· ΠΊΠΎΡΠΎΡΡΡ ΠΏΡΠΎΠΈΠ·Π²ΠΎΠ΄ΡΡ Π±Π΅ΡΠΎΠ½. Π ΡΠΎΠ»ΡΠΊΠΎ ΡΠ°ΠΊ ΠΌΠΎΠΆΠ½ΠΎ Π±ΡΡΡ ΡΠ²Π΅ΡΠ΅Π½Π½ΡΠΌ, ΡΡΠΎ ΡΠ°ΡΡΠ²ΠΎΡ ΠΏΡΠΈ Π·Π°Π»ΠΈΠ²ΠΊΠ΅ Π±ΡΠ΄Π΅Ρ ΡΠΎΠΎΡΠ²Π΅ΡΡΡΠ²ΠΎΠ²Π°ΡΡ Π½ΡΠΆΠ½ΡΠΌ ΠΏΠ°ΡΠ°ΠΌΠ΅ΡΡΠ°ΠΌΒ», β ΡΠΎΠ²Π΅ΡΡΠ΅Ρ ΠΠ²Π°Π½ ΠΡΠ½Ρ.
ΠΠ½ ΡΠ°ΠΊΠΆΠ΅ ΡΠ΅ΠΊΠΎΠΌΠ΅Π½Π΄ΡΠ΅Ρ ΠΎΠ±ΡΠ°ΡΠ°ΡΡ Π²Π½ΠΈΠΌΠ°Π½ΠΈΠ΅ Π½Π° ΠΊΠ°ΡΠ΅ΡΡΠ²ΠΎ Π³Π΅ΡΠΌΠ΅ΡΠΈΠΊΠ°.
Β«Π― ΡΡΠ°Π»ΠΊΠΈΠ²Π°Π»ΡΡ Ρ ΡΠ΅ΠΌ, ΡΡΠΎ Π½Π΅ΠΊΠΎΡΠΎΡΡΠ΅ ΠΊΠΎΠΌΠΏΠ°Π½ΠΈΠΈ ΠΏΠΎΡΡΠ°Π²Π»ΡΡΡ Π² Π£ΠΊΡΠ°ΠΈΠ½Ρ Π³Π΅ΡΠΌΠ΅ΡΠΈΠΊ, ΠΊΠΎΡΠΎΡΡΠΉ ΡΠ°Π±ΠΎΡΠ°Π΅Ρ ΠΏΡΠΈ ΡΠ΅ΠΌΠΏΠ΅ΡΠ°ΡΡΡΠ°Ρ ΠΎΡ -10, Π΄ΠΎ + 10. Π Ρ Π½Π°Ρ Π±ΡΠ²Π°ΡΡ ΠΏΠΎΠΊΠ°Π·Π°ΡΠ΅Π»ΠΈ -36 +36. ΠΡΠΎΡ ΠΌΠΎΠΌΠ΅Π½Ρ ΠΏΡΠΈ Π·Π°ΠΊΠ»ΡΡΠ΅Π½ΠΈΠΈ ΠΊΠΎΠ½ΡΡΠ°ΠΊΡΠ° Π½Π°Π΄ΠΎ ΠΎΠ±ΡΡΠΆΠ΄Π°ΡΡ Ρ ΠΏΠΎΡΡΠ°Π²ΡΠΈΠΊΠΎΠΌΒ», β Π³ΠΎΠ²ΠΎΡΠΈΡ ΡΠ΅Ρ Π½ΠΈΡΠ΅ΡΠΊΠΈΠΉ Π΄ΠΈΡΠ΅ΠΊΡΠΎΡ Β«ΠΠ½ΡΠ΅ΡΠΏΡΠΎΠ΅ΠΊΡ GmbHΒ».
ΠΠ½ ΠΏΠΎΠ΄ΡΠ΅ΡΠΊΠΈΠ²Π°Π΅Ρ ΠΎΡΠΎΠ±ΡΡ Π²Π°ΠΆΠ½ΠΎΡΡΡ Π³Π΅ΡΠΌΠ΅ΡΠΈΠΊΠ° Π½Π° ΠΊΡΡΡΠ΅ ΡΠΈΠ»ΠΎΡΠ°. ΠΡΠ»ΠΈ ΡΠ°ΠΌ ΠΈΡΠΏΠΎΠ»ΡΠ·ΠΎΠ²Π°ΡΡ Π½Π΅ΠΏΠΎΠ΄Ρ ΠΎΠ΄ΡΡΠΈΠΉ ΠΌΠ°ΡΠ΅ΡΠΈΠ°Π», Ρ Π½ΠΈΠΌ ΡΠΆΠ΅ Π½ΠΈΡΠ΅Π³ΠΎ Π½Π΅Π»ΡΠ·Ρ Π±ΡΠ΄Π΅Ρ ΡΠ΄Π΅Π»Π°ΡΡ. ΠΡΠΈΠ΄Π΅ΡΡΡ ΡΠΎΠ»ΡΠΊΠΎ ΡΠ°Π·Π±ΠΈΡΠ°ΡΡ ΠΈ ΡΠΎΠ±ΠΈΡΠ°ΡΡ ΠΊΠΎΠ½ΡΡΡΡΠΊΡΠΈΡ Π·Π°Π½ΠΎΠ²ΠΎ.
ΠΠΠΠ’ΠΠΠ«Π Π‘ΠΠΠΠΠΠΠΠΠ― Π Π‘Π’ΠΠΠ¬
ΠΠ΄Π½ΠΎΠΉ ΠΈΠ· Π³Π»Π°Π²Π½ΡΡ ΠΎΡΠΈΠ±ΠΎΠΊ, ΠΊΠΎΡΠΎΡΡΡ Π΄ΠΎΠΏΡΡΠΊΠ°ΡΡ ΠΏΡΠΈ ΠΌΠΎΠ½ΡΠ°ΠΆΠ΅, ΡΠ²Π»ΡΠ΅ΡΡΡ Π½Π΅ΠΏΡΠΎΠ΅ΠΊΡΠ½Π°Ρ ΠΏΠΎΡΡΠ°Π½ΠΎΠ²ΠΊΠ° Π±ΠΎΠ»ΡΠΎΠ². Π₯ΡΠ΅ΡΡΠΎΠΌΠ°ΡΠΈΠΉΠ½ΡΠΉ ΠΏΡΠΈΠΌΠ΅Ρ ΠΏΡΠΎΠΈΠ·ΠΎΡΠ΅Π» Π² 2008 Π³ΠΎΠ΄Ρ Π½Π° ΡΠ»Π΅Π²Π°ΡΠΎΡΠ΅ ΠΊΡΡΠΏΠ½ΠΎΠ³ΠΎ ΡΠΊΡΠ°ΠΈΠ½ΡΠΊΠΎΠ³ΠΎ Π°Π³ΡΠΎΡ ΠΎΠ»Π΄ΠΈΠ½Π³Π°.
ΠΡΠΈΡΠΈΠ½Ρ ΠΎΠ±ΡΡΡΠ΅Π½ΠΈΡ ΡΠΈΠ»ΠΎΡΠ° Π΅ΠΌΠΊΠΎΡΡΡΡ Π΅Π΄ΠΈΠ½ΠΎΠ²ΡΠ΅ΠΌΠ΅Π½Π½ΠΎΠ³ΠΎ Ρ ΡΠ°Π½Π΅Π½ΠΈΡ 5,5 ΡΡΡ. Ρ Π·Π΅ΡΠ½Π° ΡΠΎΠ³Π΄Π° ΡΡΡΠ°Π½Π°Π²Π»ΠΈΠ²Π°Π» Π΄ΠΎΠΊΡΠΎΡ ΡΠ΅Ρ Π½ΠΈΡΠ΅ΡΠΊΠΈΡ Π½Π°ΡΠΊ, ΠΏΡΠΎΡΠ΅ΡΡΠΎΡ, Π·Π°Π²Π΅Π΄ΡΡΡΠΈΠΉ ΠΎΡΠ΄Π΅Π»ΠΎΠΌ Π·Π΄Π°Π½ΠΈΠΉ ΠΈ ΡΠΎΠΎΡΡΠΆΠ΅Π½ΠΈΠΉ ΠΠΠ Β«Π£ΠΊΡΠ½ΠΈΠΈΠΏΡΠΎΠ΅ΠΊΡΡΡΠ°Π»ΡΠΊΠΎΠ½ΡΡΡΡΠΊΡΠΈΡ ΠΈΠΌ. Π.Π. Π¨ΠΈΠΌΠ°Π½ΠΎΠ²ΡΠΊΠΎΠ³ΠΎΒ» ΠΠ»Π΅ΠΊΡΠ°Π½Π΄Ρ ΠΠΎΠ»ΠΎΠ΄Π½ΠΎΠ².
ΠΠΎ Π΅Π³ΠΎ ΡΠ»ΠΎΠ²Π°ΠΌ, ΠΎΡΠ½ΠΎΠ²Π½ΡΠ΅ ΠΏΡΠΈΡΠΈΠ½Ρ Π°Π²Π°ΡΠΈΠΈ Π·Π°ΠΊΠ»ΡΡΠ°Π»ΠΈΡΡ ΠΈΠΌΠ΅Π½Π½ΠΎ Π² Π±ΠΎΠ»ΡΠΎΠ²ΡΡ ΡΠΎΠ΅Π΄ΠΈΠ½Π΅Π½ΠΈΡΡ .
Β«ΠΠ°ΡΠ½Ρ Ρ ΠΎΠ±ΡΠ΅ΠΈΠ·Π²Π΅ΡΡΠ½ΡΡ ΠΈΡΡΠΈΠ½. ΠΠΎΠ»ΡΠΎΠ²ΡΠ΅ ΡΠΎΠ΅Π΄ΠΈΠ½Π΅Π½ΠΈΡ ΡΠ°ΡΡΡΠΈΡΡΠ²Π°ΡΡΡΡ Π½Π° ΡΡΠ΅Π· Π±ΠΎΠ»ΡΠΎΠ² ΠΈ ΡΠΌΡΡΠΈΠ΅ ΠΎΡΠ½ΠΎΠ²Π½ΠΎΠ³ΠΎ ΠΌΠ΅ΡΠ°Π»Π»Π°. ΠΡΡΠ±ΠΎ Π³ΠΎΠ²ΠΎΡΡ, Π΅ΡΠ»ΠΈ Π±ΠΎΠ»Ρ ΠΌΠ°Π»ΠΎΠΏΡΠΎΡΠ½ΡΠΉ, Π° ΠΌΠ΅ΡΠ°Π»Π» β ΠΏΡΠΎΡΠ½ΡΠΉ, ΠΏΡΠΎΠΈΡΡ ΠΎΠ΄ΠΈΡ ΡΡΠ΅Π· Π±ΠΎΠ»ΡΠ° ΠΌΠ΅ΡΠ°Π»Π»ΠΎΠΌ. ΠΡΠ»ΠΈ Π½Π°ΠΎΠ±ΠΎΡΠΎΡ, Π±ΠΎΠ»Ρ ΠΏΡΠΎΡΠ½ΡΠΉ, Π° ΠΌΠ΅ΡΠ°Π»Π» ΠΌΠ°Π»ΠΎΠΏΡΠΎΡΠ½ΡΠΉ, ΡΠΎ ΠΏΡΠΎΠΈΡΡ ΠΎΠ΄ΠΈΡ ΡΠ°Π·ΡΡΡΠ΅Π½ΠΈΠ΅ Π² Π²ΠΈΠ΄Π΅ ΡΠΌΡΡΠΈΡ ΠΌΠ΅ΡΠ°Π»Π»Π°. ΠΡΠΎΠΌΠ΅ ΡΠΎΠ³ΠΎ, ΠΏΡΠΈ ΠΏΡΠΎΠ΅ΠΊΡΠΈΡΠΎΠ²Π°Π½ΠΈΠΈ Π±ΠΎΠ»ΡΠΎΠ²ΡΡ ΡΠΎΠ΅Π΄ΠΈΠ½Π΅Π½ΠΈΠΉ ΡΠ°ΡΡΡΠΎΡΠ½ΠΈΠ΅ ΠΌΠ΅ΠΆΠ΄Ρ ΡΠ΅Π½ΡΡΠ°ΠΌΠΈ Π±ΠΎΠ»ΡΠΎΠ² ΠΈ ΠΎΡ ΡΠ΅Π½ΡΡΠΎΠ² Π±ΠΎΠ»ΡΠΎΠ² Π΄ΠΎ ΠΊΡΠ°Ρ Π»ΠΈΡΡΠ° Π΄ΠΎΠ»ΠΆΠ½Ρ Π±ΡΡΡ Π½Π΅ ΠΌΠ΅Π½Π΅Π΅ ΠΎΠ³ΠΎΠ²ΠΎΡΠ΅Π½Π½ΡΡ Π² Π½ΠΎΡΠΌΠ°ΡΠΈΠ²Π½ΠΎΠΉ Π΄ΠΎΠΊΡΠΌΠ΅Π½ΡΠ°ΡΠΈΠΈ Π²Π΅Π»ΠΈΡΠΈΠ½. ΠΡΠ»ΠΈ ΡΡΠΎ ΡΡΠ»ΠΎΠ²ΠΈΠ΅ Π½Π΅ Π²ΡΠΏΠΎΠ»Π½ΡΠ΅ΡΡΡ, ΠΏΠΎΡΡΠ°Π²Π»Π΅Π½Π½ΡΠ΅ ΠΏΠΎ ΡΠ°ΡΡΠ΅ΡΡ (Π² ΠΊΠΎΠ»ΠΈΡΠ΅ΡΡΠ²Π΅Π½Π½ΠΎΠΌ ΠΎΡΠ½ΠΎΡΠ΅Π½ΠΈΠΈ) Π±ΠΎΠ»ΡΡ Π½Π΅ ΡΠ°Π±ΠΎΡΠ°ΡΡ ΠΏΠΎΠ»Π½ΠΎΠΉ ΠΌΠ΅ΡΠΎΠΉ, Π° Π·Π½Π°ΡΠΈΡ, Π²ΡΡ Π½Π°Π³ΡΡΠ·ΠΊΠ° ΠΏΠ΅ΡΠ΅Π΄Π°Π΅ΡΡΡ Π½Π° Π±ΠΎΠ»ΡΡ Π½Π΅ΡΠ°Π²Π½ΠΎΠΌΠ΅ΡΠ½ΠΎ, Ρ Π²ΡΡΠ΅ΠΊΠ°ΡΡΠΈΠΌΠΈ ΠΎΡΡΡΠ΄Π° ΠΏΠΎΡΠ»Π΅Π΄ΡΡΠ²ΠΈΡΠΌΠΈΒ», β ΠΎΠ±ΡΡΡΠ½ΡΠ΅Ρ ΠΠ»Π΅ΠΊΡΠ°Π½Π΄Ρ ΠΠ²Π°Π½ΠΎΠ²ΠΈΡ.
ΠΠΎ Π΅Π³ΠΎ ΠΈΠ½ΡΠΎΡΠΌΠ°ΡΠΈΠΈ, Π² ΡΠ»ΡΡΠ°Π΅ Ρ ΡΠ°Π·ΡΡΡΠΈΠ²ΡΠΈΠΌΡΡ Π² 2008 Π³ΠΎΠ΄Ρ ΡΠΈΠ»ΠΎΡΠΎΠΌ, ΠΌΠΎΠ½ΡΠ°ΠΆΠ½ΠΈΠΊΠΈ, ΡΡΡΠ°Π½Π°Π²Π»ΠΈΠ²Π°Ρ Π²ΠΎΡΠΎΡΠ°, ΠΏΡΠΎΠΈΠ·Π²Π΅Π»ΠΈ Π²ΡΡΠ΅Π· ΠΏΡΠΎΠ΅ΠΌΠ° Π² Π»ΠΈΡΡΠΎΠ²ΠΎΠΉ ΠΎΠ±ΠΎΠ»ΠΎΡΠΊΠ΅ ΠΎΡΠ΅Π½Ρ Π±Π»ΠΈΠ·ΠΊΠΎ ΠΊ ΠΎΡΠ²Π΅ΡΡΡΠΈΡΠΌ ΠΏΠΎΠ΄ Π±ΠΎΠ»ΡΡ β ΡΠ΄Π΅Π»Π°Π»ΠΈ Π΅Π³ΠΎ ΠΏΡΠ°ΠΊΡΠΈΡΠ΅ΡΠΊΠΈ ΠΏΠΎ Π³ΡΠ°Π½ΡΠΌ ΠΎΡΠ²Π΅ΡΡΡΠΈΠΉ, Π½Π΅ Π²ΡΠ΄Π΅ΡΠΆΠ°Π² ΡΠ΅ΠΌ ΡΠ°ΠΌΡΠΌ ΡΡΠ΅Π±ΡΠ΅ΠΌΠΎΠ΅ ΡΠ°ΡΡΡΠΎΡΠ½ΠΈΠ΅ ΠΎΡ ΡΠ΅Π½ΡΡΠ° Π±ΠΎΠ»ΡΠ° Π΄ΠΎ ΠΊΡΠ°Ρ Π»ΠΈΡΡΠ°. Π ΡΠ²ΡΠ·ΠΈ Ρ ΡΡΠΈΠΌ, ΠΈΠ· ΡΡΠ΅Ρ Π±ΠΎΠ»ΡΠΎΠ² Β«ΡΠ°Π±ΠΎΡΠΈΠΌΠΈΒ» ΠΎΠΊΠ°Π·Π°Π»ΠΈΡΡ Π΄Π²Π°.
Β«Π ΡΠ΅Π·ΡΠ»ΡΡΠ°ΡΠ΅, ΠΏΠΎ ΠΌΠ΅ΡΠ΅ Π·Π°Π³ΡΡΠ·ΠΊΠΈ ΡΠΈΠ»ΠΎΡΠ° Π·Π΅ΡΠ½ΠΎΠΌ ΠΏΡΠΎΠΈΡΡ ΠΎΠ΄ΠΈΠ»ΠΎ ΡΠ²Π΅Π»ΠΈΡΠ΅Π½ΠΈΠ΅ Π²Π½ΡΡΡΠ΅Π½Π½ΠΈΡ ΡΠ°ΡΡΡΠ³ΠΈΠ²Π°ΡΡΠΈΡ ΡΡΠΈΠ»ΠΈΠΉ Π² ΡΠ»Π΅ΠΌΠ΅Π½ΡΠ°Ρ ΠΎΠ±ΠΎΠ»ΠΎΡΠΊΠΈ, Π² ΡΠΎΠΌ ΡΠΈΡΠ»Π΅ ΠΈ Π² ΡΠ°ΠΉΠΎΠ½Π΅ Π±ΠΎΠ»ΡΠΎΠ²ΡΡ ΡΠΎΠ΅Π΄ΠΈΠ½Π΅Π½ΠΈΠΉ. ΠΠΎΡΠΊΠΎΠ»ΡΠΊΡ ΠΏΡΠ°ΠΊΡΠΈΡΠ΅ΡΠΊΠΈ ΠΎΠ΄Π½Π° ΡΡΠ΅ΡΡ Π±ΠΎΠ»ΡΠΎΠ² Π±ΡΠ»Π° Π²ΡΠΊΠ»ΡΡΠ΅Π½Π° ΠΈΠ· ΡΠ°Π±ΠΎΡΡ, ΠΎΡΡΠ°Π²ΡΠΈΠ΅ΡΡ Π΄Π²Π΅ ΡΡΠ΅ΡΠΈ Β«Π³Π΅ΡΠΎΠΈΡΠ΅ΡΠΊΠΈ ΡΠΎΠΏΡΠΎΡΠΈΠ²Π»ΡΠ»ΠΈΡΡ, ΠΊΠ°ΠΊ ΠΌΠΎΠ³Π»ΠΈΒ». Π ΠΊΠΎΠ³Π΄Π° ΡΠΈΠ»ΠΎΡ Π·Π°ΠΏΠΎΠ»Π½ΠΈΠ»ΠΈ ΠΏΡΠΈΠΌΠ΅ΡΠ½ΠΎ Π½Π° 70%, ΠΎΠ½ΠΈ ΡΠΌΡΠ»ΠΈ ΠΌΠ΅ΡΠ°Π»Π» ΠΎΠ±ΠΎΠ»ΠΎΡΠΊΠΈ. ΠΡΠΎΠΌΠ΅ ΡΡΠΎΠ³ΠΎ, Π² ΡΠ°ΠΉΠΎΠ½Π΅ ΠΏΡΠΎΠ΅ΠΌΠ° Π½Π΅ΠΎΠ±Ρ ΠΎΠ΄ΠΈΠΌΠΎ Π±ΡΠ»ΠΎ ΠΏΠΎΡΡΠ°Π²ΠΈΡΡ Π±ΠΎΠ»ΡΡ ΠΊΠ»Π°ΡΡΠ° 8.8, Π° ΠΏΠΎΡΡΠ°Π²Π»Π΅Π½Ρ Π±ΡΠ»ΠΈ Π±ΠΎΠ»ΡΡ ΠΌΠ΅Π½Π΅Π΅ ΠΏΡΠΎΡΠ½ΡΠ΅ β ΠΊΠ»Π°ΡΡΠ° 5.8, ΡΡΠΎ ΡΠ°ΠΊΠΆΠ΅ Π½Π΅ ΡΠΏΠΎΡΠΎΠ±ΡΡΠ²ΠΎΠ²Π°Π»ΠΎ ΡΠ²Π΅Π»ΠΈΡΠ΅Π½ΠΈΡ ΠΏΡΠΎΡΠ½ΠΎΡΡΠΈΒ», β ΠΎΠ±ΡΡΡΠ½ΠΈΠ» Π·Π°Π²Π΅Π΄ΡΡΡΠΈΠΉ ΠΎΡΠ΄Π΅Π»ΠΎΠΌ Π·Π΄Π°Π½ΠΈΠΉ ΠΈ ΡΠΎΠΎΡΡΠΆΠ΅Π½ΠΈΠΉ ΠΠΠ Π£ΠΊΡΠ½ΠΈΠΈΠΏΡΠΎΠ΅ΠΊΡΡΡΠ°Π»ΡΠΊΠΎΠ½ΡΡΡΡΠΊΡΠΈΡ ΠΈΠΌ. Π.Π. Π¨ΠΈΠΌΠ°Π½ΠΎΠ²ΡΠΊΠΎΠ³ΠΎ.
ΠΠΎ ΡΠ΅ΠΊΠΎΠΌΠ΅Π½Π΄Π°ΡΠΈΡΠΌ ΡΠΏΠ΅ΡΠΈΠ°Π»ΠΈΡΡΠΎΠ² Π½Π° ΠΎΡΡΠ°Π»ΡΠ½ΡΡ ΡΠΈΠ»ΠΎΡΠ°Ρ ΡΡΠΎΠ³ΠΎ ΡΠ»Π΅Π²Π°ΡΠΎΡΠ° ΠΎΡΠΌΠ΅ΡΠ΅Π½Π½ΡΠ΅ Π²ΡΡΠ΅ ΠΎΡΠΈΠ±ΠΊΠΈ Π±ΡΠ»ΠΈ Π²ΠΎΠ²ΡΠ΅ΠΌΡ ΠΈΡΠΏΡΠ°Π²Π»Π΅Π½Ρ, ΡΡΠΎ ΠΏΠΎΠ·Π²ΠΎΠ»ΠΈΠ»ΠΎ ΠΏΡΠ΅Π΄ΠΎΡΠ²ΡΠ°ΡΠΈΡΡ Π²ΠΎΠ·ΠΌΠΎΠΆΠ½ΠΎΠ΅ ΡΠ°Π·ΡΡΡΠ΅Π½ΠΈΠ΅ Π΅ΠΌΠΊΠΎΡΡΠ΅ΠΉ.
ΠΡΠΎΡΠ½ΠΎΡΡΡ ΡΠΈΠ»ΠΎΡΠΎΠ² Π·Π°Π²ΠΈΡΠΈΡ ΡΠ°ΠΊΠΆΠ΅ ΠΎΡ ΠΏΡΠΎΡΠ½ΠΎΡΡΠ½ΡΡ ΠΈ Π΄Π΅ΡΠΎΡΠΌΠ°ΡΠΈΠ²Π½ΡΡ Ρ Π°ΡΠ°ΠΊΡΠ΅ΡΠΈΡΡΠΈΠΊ ΠΏΡΠΈΠΌΠ΅Π½Π΅Π½Π½ΡΡ ΠΌΠ°ΡΠ΅ΡΠΈΠ°Π»ΠΎΠ². Π₯ΠΎΡΠΎΡΠΈΠ΅ ΠΏΡΠΎΠΈΠ·Π²ΠΎΠ΄ΠΈΡΠ΅Π»ΠΈ ΠΈΡΠΏΠΎΠ»ΡΠ·ΡΡΡ, ΠΊΠ°ΠΊ ΠΏΡΠ°Π²ΠΈΠ»ΠΎ, Π²ΡΡΠΎΠΊΠΎΠΏΡΠΎΡΠ½ΡΡ ΡΡΠ°Π»Ρ Π΄Π»Ρ ΡΠ»Π΅ΠΌΠ΅Π½ΡΠΎΠ² ΠΎΠ±ΠΎΠ»ΠΎΡΠ΅ΠΊ ΠΈ Π²Π΅ΡΡΠΈΠΊΠ°Π»ΡΠ½ΡΡ ΡΠ΅Π±Π΅Ρ. ΠΠ΄Π½Π°ΠΊΠΎ Π½Π° ΡΡΠΎΡ ΡΡΠ΅Ρ Π΅ΡΡΡ ΠΈ Π°Π»ΡΡΠ΅ΡΠ½Π°ΡΠΈΠ²Π½ΠΎΠ΅ ΠΌΠ½Π΅Π½ΠΈΠ΅.
Β«Π― ΠΏΡΠΈΡΠ΅Π» ΠΊ ΠΏΠ°ΡΠ°Π΄ΠΎΠΊΡΠ°Π»ΡΠ½ΠΎΠΌΡ Π½Π° ΠΏΠ΅ΡΠ²ΡΠΉ Π²Π·Π³Π»ΡΠ΄ Π²ΡΠ²ΠΎΠ΄Ρ, ΡΡΠΎ Π΄Π»Ρ ΡΠ»Π΅ΠΌΠ΅Π½ΡΠΎΠ² ΠΎΠ±ΠΎΠ»ΠΎΡΠ΅ΠΊ ΡΠΈΠ»ΠΎΡΠΎΠ² Π»ΡΡΡΠ΅ ΠΏΡΠΈΠΌΠ΅Π½ΡΡΡ ΠΌΠ°Π»ΠΎΠΏΡΠΎΡΠ½ΡΡ ΡΡΠ°Π»Ρ Ρ Π±ΠΎΠ»ΡΡΠΎΠΉ ΠΏΠ»ΠΎΡΠ°Π΄ΠΊΠΎΠΉ ΡΠ΅ΠΊΡΡΠ΅ΡΡΠΈ ΠΏΡΠΈ ΡΠ°ΡΡΡΠΆΠ΅Π½ΠΈΠΈ ΠΈ Π±ΠΎΠ»Π΅Π΅ ΠΏΡΠΎΡΠ½ΡΠ΅ Π±ΠΎΠ»ΡΡ. ΠΠ°, ΡΠ°ΠΊΠΈΠ΅ ΠΊΠΎΠ½ΡΡΡΡΠΊΡΠΈΠΈ Π±ΡΠ΄ΡΡ Π±ΠΎΠ»Π΅Π΅ ΡΡΠΆΠ΅Π»ΡΠΌΠΈ, Π½ΠΎ ΠΊΠΎΠ³Π΄Π° ΡΠ΅ΡΡ ΠΈΠ΄Π΅Ρ ΠΎ Ρ ΡΠ°Π½Π΅Π½ΠΈΠΈ Π½Π΅ΡΠΊΠΎΠ»ΡΠΊΠΈΡ ΡΡΡΡΡ ΡΠΎΠ½Π½ Π·Π΅ΡΠ½Π°, Π»ΠΈΡΠ½ΠΈΠ΅ 5-10 Ρ ΠΌΠ΅ΡΠ°Π»Π»Π° Π½Π° ΠΊΠΎΠ½ΡΡΡΡΠΊΡΠΈΠΈ β ΡΡΠΎ ΡΠ»ΠΎΠ½Ρ Π΄ΡΠΎΠ±ΠΈΠ½Π°Β», β ΡΡΠΈΡΠ°Π΅Ρ ΠΠ»Π΅ΠΊΡΠ°Π½Π΄Ρ ΠΠΎΠ»ΠΎΠ΄Π½ΠΎΠ².
Π‘Π²ΠΎΡ ΠΏΠΎΠ·ΠΈΡΠΈΡ ΠΎΠ½ ΠΎΠ±ΡΡΡΠ½ΡΠ΅Ρ ΡΠ΅ΠΌ, ΡΡΠΎ ΠΏΡΠΈ ΠΌΠ°Π»ΠΎΠΏΡΠΎΡΠ½ΠΎΠΉ ΡΡΠ°Π»ΠΈ ΠΈ ΠΏΡΠΎΡΠ½ΡΡ Π±ΠΎΠ»ΡΠ°Ρ Π² ΠΊΠΎΠ½ΡΡΡΡΠΊΡΠΈΠΈ Π²ΠΎΠ·Π½ΠΈΠΊΠ°Π΅Ρ Β«ΡΠ°Π²Π½ΠΎΠ²Π΅ΡΠ½ΠΎΠ΅Β» ΡΠΎΡΡΠΎΡΠ½ΠΈΠ΅.
Β«ΠΠΎΠ½ΡΡΡΡΠΊΡΠΈΠΈ ΠΈΠ·Π³ΠΎΡΠ°Π²Π»ΠΈΠ²Π°ΡΡΡΡ Ρ ΠΎΠΏΡΠ΅Π΄Π΅Π»Π΅Π½Π½ΡΠΌΠΈ Π΄ΠΎΠΏΡΡΠΊΠ°ΠΌΠΈ. Π ΠΏΡΠΈΠΌΠ΅ΡΡ, Π΄Π»Ρ ΡΠΎΠ³ΠΎ, ΡΡΠΎΠ±Ρ ΠΏΠΎΡΡΠ°Π²ΠΈΡΡ Π±ΠΎΠ»ΡΡ Π΄ΠΈΠ°ΠΌΠ΅ΡΡΠΎΠΌ 10 ΠΌΠΌ, Π½ΡΠΆΠ½Ρ ΠΎΡΠ²Π΅ΡΡΡΠΈΡ Π² ΠΏΠ°Π½Π΅Π»ΡΡ Π΄ΠΈΠ°ΠΌΠ΅ΡΡΠΎΠΌ 11-12 ΠΌΠΌ. Π£ΠΏΠ»ΠΎΡΠ½ΠΈΡΠ΅Π»ΠΈ Π½Π΅ ΠΎΠ±Π΅ΡΠΏΠ΅ΡΠΈΠ²Π°ΡΡ Π·Π°ΡΡΠΆΠΊΡ Π±ΠΎΠ»ΡΠΎΠ², ΠΏΠΎΡΡΠΎΠΌΡ ΠΏΡΠΈ Π·Π°Π³ΡΡΠ·ΠΊΠ΅ ΡΠΈΠ»ΠΎΡΠ° ΠΏΡΠΎΠΈΡΡ ΠΎΠ΄ΠΈΡ ΠΏΠΎΡΡΠ΅ΠΏΠ΅Π½Π½Π°Ρ ΠΎΠ±ΡΡΠΆΠΊΠ° Π²ΡΠ΅Ρ ΡΠΎΠ΅Π΄ΠΈΠ½Π΅Π½ΠΈΠΉ, Π²ΡΠ±ΠΈΡΠ°ΡΡΡΡ Π²ΡΠ΅ Π»ΡΡΡΡ (ΠΏΠΎΠ΄Π°ΡΠ»ΠΈΠ²ΠΎΡΡΠΈ) Π² Π±ΠΎΠ»ΡΠΎΠ²ΡΡ ΡΠΎΠ΅Π΄ΠΈΠ½Π΅Π½ΠΈΡΡ . Π ΠΏΡΠΈ Π½Π°Π»ΠΈΡΠΈΠΈ Π΄ΡΡΠ³ΠΈΡ Π½Π΅ΡΠΎΠ²Π΅ΡΡΠ΅Π½ΡΡΠ² ΠΏΡΠΎΠΈΡΡ ΠΎΠ΄ΠΈΡ Π½Π΅Π±ΠΎΠ»ΡΡΠΎΠ΅ ΡΠΌΡΡΠΈΠ΅ ΠΎΡΠ½ΠΎΠ²Π½ΠΎΠ³ΠΎ ΠΌΠ΅ΡΠ°Π»Π»Π° Π±ΠΎΠ»Π΅Π΅ ΠΏΡΠΎΡΠ½ΡΠΌΠΈ Π±ΠΎΠ»ΡΠ°ΠΌΠΈ, ΡΠΎ Π΅ΡΡΡ, Π²ΡΠ΅ ΡΠ»Π΅ΠΌΠ΅Π½ΡΡ ΡΠ°Π±ΠΎΡΠ°ΡΡ ΡΠΎΠ²ΠΌΠ΅ΡΡΠ½ΠΎΒ», β ΡΠ°ΡΡΠΊΠ°Π·ΡΠ²Π°Π΅Ρ ΠΠ»Π΅ΠΊΡΠ°Π½Π΄Ρ ΠΠ²Π°Π½ΠΎΠ²ΠΈΡ.
Π‘ΠΎΠ²ΡΠ΅ΠΌ Π΄ΡΡΠ³Π°Ρ ΡΠΈΡΡΠ°ΡΠΈΡ Ρ Π²ΡΡΠΎΠΊΠΎΠΏΡΠΎΡΠ½ΡΠΌΠΈ ΡΡΠ°Π»ΡΠΌΠΈ. ΠΠ½ΠΈ ΠΈΠΌΠ΅ΡΡ ΠΌΠ°Π»ΡΡ ΠΏΠ»ΠΎΡΠ°Π΄ΠΊΡ ΡΠ΅ΠΊΡΡΠ΅ΡΡΠΈ, Π²ΡΠ»Π΅Π΄ΡΡΠ²ΠΈΠ΅ ΡΠ΅Π³ΠΎ Π½Π°ΡΠΈΠ½Π°ΡΡ Π»ΠΈΠ±ΠΎ ΡΡΠ΅Π·Π°ΡΡ Π±ΠΎΠ»Ρ (Π΅ΡΠ»ΠΈ ΠΎΠ½ ΠΌΠ°Π»ΠΎΠΏΡΠΎΡΠ½ΡΠΉ), Π»ΠΈΠ±ΠΎ ΡΠ°Π·ΡΡΡΠ°ΡΡΡΡ ΠΏΡΠΈ ΡΠΌΡΡΠΈΠΈ.
Β«Π₯ΠΎΡΠΎΡΠΎ, Π΅ΡΠ»ΠΈ Π±ΡΠ΄Π΅Ρ ΡΠΌΠΈΠ½Π°ΡΡΡΡ ΠΎΡΠ½ΠΎΠ²Π½ΠΎΠΉ ΠΌΠ΅ΡΠ°Π»Π», Π³ΠΎΡΠ°Π·Π΄ΠΎ Ρ ΡΠΆΠ΅, Π΅ΡΠ»ΠΈ Π±ΡΠ΄ΡΡ ΡΡΠ΅Π·Π°ΡΡΡΡ Π±ΠΎΠ»ΡΡ. Π‘ΡΠ΅Π· Π±ΠΎΠ»ΡΠΎΠ² β ΠΏΡΠΈΠ·Π½Π°ΠΊ ΡΠ°Π·ΡΡΡΠ΅Π½ΠΈΡ Π²ΡΠ΅ΠΉ ΠΊΠΎΠ½ΡΡΡΡΠΊΡΠΈΠΈ ΡΠΈΠ»ΠΎΡΠ°, Π° Π½Π΅ ΠΊΠ°ΠΊΠΎΠ³ΠΎ-Π»ΠΈΠ±ΠΎ ΠΎΡΠ΄Π΅Π»ΡΠ½ΠΎΠ³ΠΎ ΡΠΎΠ΅Π΄ΠΈΠ½Π΅Π½ΠΈΡ. ΠΡΠΊΠ»ΡΡΠ΅Π½ΠΈΠ΅ ΠΈΠ· ΡΠ°Π±ΠΎΡΡ Π΄Π°ΠΆΠ΅ ΠΎΠ΄Π½ΠΎΠ³ΠΎ Π±ΠΎΠ»ΡΠ° ΠΏΠΎΡΡΠ΅Π±ΡΠ΅Ρ ΠΏΠ΅ΡΠ΅ΡΠ°ΡΠΏΡΠ΅Π΄Π΅Π»Π΅Π½ΠΈΡ ΡΡΠΈΠ»ΠΈΠΉ Π½Π° ΠΎΡΡΠ°Π²ΡΠΈΠ΅ΡΡ, Π΄Π²ΡΡ Π±ΠΎΠ»ΡΠΎΠ² β Π΅ΡΠ΅ Π±ΠΎΠ»ΡΡΠ΅Π΅ ΠΏΠ΅ΡΠ΅ΡΠ°ΡΠΏΡΠ΅Π΄Π΅Π»Π΅Π½ΠΈΠ΅, ΡΡΠΈ β Π΅ΡΠ΅ Π±ΠΎΠ»ΡΡΠ΅, ΠΈ Ρ.Π΄. Π΄ΠΎ ΠΏΠΎΠ»Π½ΠΎΠ³ΠΎ ΡΠ°Π·ΡΡΡΠ΅Π½ΠΈΡ ΠΊΠΎΠ½ΡΡΡΡΠΊΡΠΈΠΈ ΡΠΈΠ»ΠΎΡΠ°Β», β ΠΏΠΎΠ΄ΡΠ΅ΡΠΊΠΈΠ²Π°Π΅Ρ ΡΠΊΡΠΏΠ΅ΡΡ.
ΠΠΠΠ ΠΠΠΠΠ¬ΠΠ Π ΠΠ‘Π‘Π§ΠΠ’ΠΠΠΠ«Π ΠΠΠ’Π ΠΠΠ«Π Π Π‘ΠΠΠΠΠΠ«Π ΠΠΠΠ Π£ΠΠΠ ΠΠ ΠΠ Π«Π¨Π£
ΠΡΠ΅ ΠΎΠ΄Π½Π° Β«ΠΊΠ»Π°ΡΡΠΈΡΠ΅ΡΠΊΠ°ΡΒ» ΠΎΡΠΈΠ±ΠΊΠ°, ΠΊΠΎΡΠΎΡΠ°Ρ Π²Π΅Π΄Π΅Ρ ΠΊ ΡΠ°Π·ΡΡΡΠ΅Π½ΠΈΡ ΡΠΈΠ»ΠΎΡΠΎΠ², β ΡΡΠΎ Π½Π΅ΠΏΡΠ°Π²ΠΈΠ»ΡΠ½ΠΎ ΠΎΠΏΡΠ΅Π΄Π΅Π»Π΅Π½Π½Π°Ρ Π²Π΅ΡΡΠΎΠ²Π°Ρ ΠΈ ΡΠ½Π΅Π³ΠΎΠ²Π°Ρ Π½Π°Π³ΡΡΠ·ΠΊΠ° Π½Π° ΠΊΡΡΡΡ. Π‘Π΅ΠΉΡΠ°Ρ Π² Π£ΠΊΡΠ°ΠΈΠ½Π΅ ΠΏΠΎ Π΄Π΅ΠΉΡΡΠ²ΡΡΡΠ΅ΠΌΡ Π·Π°ΠΊΠΎΠ½ΠΎΠ΄Π°ΡΠ΅Π»ΡΡΡΠ²Ρ ΠΏΡΠΈΠ½ΡΡ ΠΌΠ°ΠΊΡΠΈΠΌΠ°Π»ΡΠ½ΡΠΉ ΠΏΠΎΠΊΠ°Π·Π°ΡΠ΅Π»Ρ ΡΡΠΎΠΉ Π½Π°Π³ΡΡΠ·ΠΊΠΈ Π΄Π»Ρ ΡΠΎΠΎΡΡΠΆΠ΅Π½ΠΈΠΉ β 180 ΠΊΠ³/ΠΌΒ².
Β«ΠΡΠΈ ΡΠ°ΡΡΠ΅ΡΠ΅ ΡΠΈΠ»ΠΎΡΠΎΠ² Π½Π° ΡΡΠ°ΠΏΠ΅ Π·Π°ΠΊΠ°Π·Π° Π½Π΅ΠΎΠ±Ρ ΠΎΠ΄ΠΈΠΌΠΎ ΡΡΠΈΡΡΠ²Π°ΡΡ ΡΠ½Π΅Π³ΠΎΠ²ΡΡ Π½Π°Π³ΡΡΠ·ΠΊΡ Π½Π° ΠΊΡΡΡΡ ΡΠΈΠ»ΠΎΡΠ°. ΠΠ½Π° Π΄ΠΎΠ»ΠΆΠ½Π° Π±ΡΡΡ Π½Π΅ ΠΌΠ΅Π½ΡΡΠ΅ 140 ΠΊΠ³/ΠΌΒ². Π’Π°ΠΊΠΎΠΉ ΡΠ°ΡΡΠ΅Ρ Π΄ΠΎΠ»ΠΆΠ΅Π½ ΠΎΠ±Π΅Π·ΠΎΠΏΠ°ΡΠΈΡΡ ΡΠΈΠ»ΠΎΡ Π² ΡΠ½Π΅ΠΆΠ½ΡΡ ΠΈ Π²Π΅ΡΡΠ΅Π½ΡΡ Π·ΠΈΠΌΡ. ΠΡΠΈ ΠΎΠ±Π»Π΅Π΄Π΅Π½Π΅Π½ΠΈΠΈ ΠΊΡΠΎΠ²Π»ΠΈ ΠΈ Π±ΠΎΠ»ΡΡΠΎΠΌ ΠΏΠΎΡΡΠ²Π΅ Π²Π΅ΡΡΠ°, ΠΊΡΠΎΠ²Π»Ρ ΠΈΡΠΏΡΡΡΠ²Π°Π΅Ρ Π½Π΅Π²Π΅ΡΠΎΡΡΠ½ΡΠ΅ Π½Π°Π³ΡΡΠ·ΠΊΠΈΒ», β ΠΎΠ±ΡΡΡΠ½ΡΠ΅Ρ Π½Π°ΡΠ°Π»ΡΠ½ΠΈΠΊ ΡΠ΅Ρ Π½ΠΈΡΠ΅ΡΠΊΠΎΠ³ΠΎ ΠΎΡΠ΄Π΅Π»Π° ΠΡΡΠΏΠΏΡ ΠΠΠ ΠΠ’Π ΠΠΠ Π‘Π΅ΡΠ³Π΅ΠΉ Π©Π΅ΡΠ±Π°Π½Ρ.
ΠΠ°ΠΊ ΡΠ°ΡΡΠΊΠ°Π·ΡΠ²Π°ΡΡ ΡΡΠ°ΡΡΠ½ΠΈΠΊΠΈ ΡΡΠ½ΠΊΠ°, Π½Π΅ΡΠ΅Π΄ΠΊΠΈ ΡΠ»ΡΡΠ°ΠΈ, ΠΊΠΎΠ³Π΄Π° ΠΏΡΠΎΠ΄Π°Π²ΡΡ Π½Π΅ΠΊΠΎΡΠΎΡΡΡ ΠΈΠΌΠΏΠΎΡΡΠ½ΡΡ ΡΠΈΠ»ΠΎΡΠΎΠ² Π±Π΅Π·Π·Π°ΡΡΠ΅Π½ΡΠΈΠ²ΠΎ ΠΌΠ°Π½ΠΈΠΏΡΠ»ΠΈΡΡΡΡ Π΄Π°Π½Π½ΡΠΌΠΈ ΠΎ ΡΠ½Π΅Π³ΠΎΠ²ΡΡ ΠΈ Π²Π΅ΡΡΠΎΠ²ΡΡ Π½Π°Π³ΡΡΠ·ΠΊΠ°Ρ . Π§ΡΠΎΠ±Ρ ΡΠ΅Π°Π»ΠΈΠ·ΠΎΠ²Π°ΡΡ ΡΠ²ΠΎΡ ΠΏΡΠΎΠ΄ΡΠΊΡΠΈΡ, ΠΎΠ½ΠΈ ΡΠ½ΠΈΠΆΠ°ΡΡ ΡΠ΅Π½Ρ Π½Π° ΡΠΈΠ»ΠΎΡ ΠΈ ΠΏΡΠΈ ΡΡΠΎΠΌ ΡΠΌΠ°Π»ΡΠΈΠ²Π°ΡΡ, ΡΡΠΎ ΠΏΡΠΎΠ΄Π°ΡΡ ΠΊΡΡΡΡ Ρ Π·Π°Π½ΠΈΠΆΠ΅Π½Π½ΠΎΠΉ Π²Π΅ΡΡΠΎΠ²ΠΎΠΉ ΠΈ ΡΠ½Π΅Π³ΠΎΠ²ΠΎΠΉ Π½Π°Π³ΡΡΠ·ΠΊΠΎΠΉ. ΠΠΈΠ±ΠΎ ΠΆΠ΅ Π½Π° ΠΏΡΠΎΡΡΠ±Ρ Π·Π°ΠΊΠ°Π·ΡΠΈΠΊΠ° ΠΏΡΠ΅Π΄ΠΎΡΡΠ°Π²ΠΈΡΡ ΠΎΠ±ΠΎΡΡΠ΄ΠΎΠ²Π°Π½ΠΈΠ΅ Ρ Π±ΠΎΠ»Π΅Π΅ Π²ΡΡΠΎΠΊΠΈΠΌΠΈ ΠΏΠΎΠΊΠ°Π·Π°ΡΠ΅Π»ΡΠΌΠΈ ΠΏΠΎ Π²Π΅ΡΡΠΎΠ²ΠΎΠΉ ΠΈ ΡΠ½Π΅Π³ΠΎΠ²ΠΎΠΉ Π½Π°Π³ΡΡΠ·ΠΊΠ΅, ΠΌΠ΅Π½ΡΡΡ Π»ΠΈΡΡ ΡΠΈΡΡΡ Π² Π΄ΠΎΠΊΡΠΌΠ΅Π½ΡΠ°ΡΠΈΠΈ, ΠΎΡΡΠ°Π²Π»ΡΡ ΠΏΡΠ΅Π΄Π»ΠΎΠΆΠ΅Π½Π½ΡΠΉ ΡΠ°Π½Π΅Π΅ Π²Π°ΡΠΈΠ°Π½Ρ ΠΊΡΡΡΠΈ. ΠΠΎΠ½ΡΡΠ½ΠΎ, ΡΡΠΎ ΡΡΠΎ Π²Π΅Π΄Π΅Ρ ΠΊ ΡΠ°Π·ΡΡΡΠ΅Π½ΠΈΡ ΡΠΈΠ»ΠΎΡΠΎΠ².
Β«ΠΡΠΈΡΠΈΠ½Ρ Π²ΡΠ΅Ρ ΠΎΡΠ½ΠΎΠ²Π½ΡΡ ΠΏΠ°Π΄Π΅Π½ΠΈΠΉ, ΠΊΠΎΡΠΎΡΡΠ΅ Π±ΡΠ»ΠΈ Π² Π£ΠΊΡΠ°ΠΈΠ½Π΅ ΠΈ Π² Π ΠΎΡΡΠΈΠΈ Π·Π° ΠΏΠΎΡΠ»Π΅Π΄Π½Π΅Π΅ Π²ΡΠ΅ΠΌΡ β ΡΡΠΎ Π·Π°Π½ΠΈΠΆΠ΅Π½Π½Π°Ρ ΡΠ½Π΅Π³ΠΎΠ²Π°Ρ ΠΈ Π²Π΅ΡΡΠΎΠ²Π°Ρ Π½Π°Π³ΡΡΠ·ΠΊΠ°, β Π³ΠΎΠ²ΠΎΡΠΈΡ ΠΠ²Π°Π½ ΠΡΠ½Ρ. β ΠΠ° ΠΏΠΎΡΠ»Π΅Π΄Π½ΠΈΠ΅ Π΄Π²Π° Π΄Π΅ΡΡΡΠΈΠ»Π΅ΡΠΈΡ ΡΠ½Π΅Π³ΠΎΠ²ΡΠ΅ Π½Π°Π³ΡΡΠ·ΠΊΠΈ Π² Π£ΠΊΡΠ°ΠΈΠ½Π΅ ΠΌΠ΅Π½ΡΠ»ΠΈΡΡ 3 ΡΠ°Π·Π° ΠΈ Π²ΡΠ΅ Π² ΡΡΠΎΡΠΎΠ½Ρ ΡΠ²Π΅Π»ΠΈΡΠ΅Π½ΠΈΡ. Π’ΡΠΈ Π³ΠΎΠ΄Π° Π½Π°Π·Π°Π΄ Π² Π£ΠΊΡΠ°ΠΈΠ½Π΅ Π±ΡΠ»ΠΈ ΠΎΡΠ΅Π½Ρ Π±ΠΎΠ»ΡΡΠΈΠ΅ ΡΠ½Π΅Π³ΠΎΠΏΠ°Π΄Ρ. Π£ ΡΠ΅Ρ , ΠΊΡΠΎ ΠΏΠΎΡΠ»Π΅ Π½ΠΈΡ Β«Π²ΡΠΆΠΈΠ»Β» β ΠΊΡΡΡΠΈ Ρ Π½ΠΎΡΠΌΠ°Π»ΡΠ½ΠΎΠΉ ΡΠ½Π΅Π³ΠΎΠ²ΠΎΠΉ ΠΈ Π²Π΅ΡΡΠΎΠ²ΠΎΠΉ Π½Π°Π³ΡΡΠ·ΠΊΠΎΠΉ. ΠΠΎ Π½Π΅ΠΊΠΎΡΠΎΡΡΠ΅ ΡΠΈΠ»ΠΎΡΡ Π² Π£ΠΊΡΠ°ΠΈΠ½Π΅ ΡΠΏΠ°Π»ΠΈΒ».
Β«Π‘Π»ΡΡΠ°ΠΈ, ΠΊΠΎΠ³Π΄Π° ΡΠΈΠ»ΠΎΡ Π½Π΅ Π²ΡΠ΄Π΅ΡΠΆΠΈΠ²Π°Π΅Ρ ΡΠ½Π΅Π³ΠΎΠ²ΠΎΠΉ Π½Π°Π³ΡΡΠ·ΠΊΠΈ, ΠΌΠΎΠΆΠ½ΠΎ ΠΎΡ Π°ΡΠ°ΠΊΡΠ΅ΡΠΈΠ·ΠΎΠ²Π°ΡΡ ΡΡΠ΅ΠΌΡ ΡΠ»ΠΎΠ²Π°ΠΌΠΈ: Β«ΠΆΠ°Π΄Π½ΠΎΡΡΡ ΡΡΠ°Π΅ΡΠ° ΡΠ³ΡΠ±ΠΈΠ»Π°Β». ΠΡΠ»ΠΈ Π²Ρ Ρ ΠΎΡΠΈΡΠ΅, ΡΡΠΎΠ±Ρ ΠΊΠΎΠ½ΡΡΡΡΠΊΡΠΈΡ ΡΠΈΠ»ΠΎΡΠ° ΡΠΊΡΠΏΠ»ΡΠ°ΡΠΈΡΠΎΠ²Π°Π»Π°ΡΡ ΠΏΡΠΎΠ΄ΠΎΠ»ΠΆΠΈΡΠ΅Π»ΡΠ½ΠΎΠ΅ Π²ΡΠ΅ΠΌΡ, Π΄ΠΎΠ±Π°Π²ΡΡΠ΅ Π² ΠΊΠΎΠ½ΡΡΡΡΠΊΡΠΈΠΈ ΠΏΠΎΠΊΡΡΡΠΈΡ ΡΡΡΡ Π±ΠΎΠ»ΡΡΠ΅ ΠΌΠ΅ΡΠ°Π»Π»Π° β ΡΠ²Π΅Π»ΠΈΡΠ΅Π½ΠΈΠ΅ Π²Π΅ΡΠ° ΠΏΠΎΠΊΡΡΡΠΈΡ Π½Π° 20% ΠΏΡΠΈΠ²Π΅Π΄Π΅Ρ ΠΊ ΡΡΡΠΆΠ΅Π»Π΅Π½ΠΈΡ Π²ΡΠ΅ΠΉ ΠΊΠΎΠ½ΡΡΡΡΠΊΡΠΈΠΈ Π½Π° 5-10%. ΠΠΎΡΡΠ°Π²ΡΡΠ΅ Π΄ΠΎΠΏΠΎΠ»Π½ΠΈΡΠ΅Π»ΡΠ½ΡΠ΅ ΡΠ°ΡΠΏΠΎΡΠΊΠΈ ΠΈ ΡΡΠΎΠΉΠΊΠΈ, ΡΠΌΠ΅Π½ΡΡΠ°ΡΡΠΈΠ΅ ΡΠ°ΡΡΠ΅ΡΠ½ΡΠ΅ Π΄Π»ΠΈΠ½Ρ ΡΠΆΠ°ΡΡΡ ΠΈ ΡΠΆΠ°ΡΠΎ-ΠΈΠ·ΠΎΠ³Π½ΡΡΡΡ ΡΠ»Π΅ΠΌΠ΅Π½ΡΠΎΠ². ΠΠΎ Ρ Π½Π°Ρ Π½Π° ΠΊΡΡΡΠ΅ ΠΎΠ±ΡΡΠ½ΠΎ ΡΠΊΠΎΠ½ΠΎΠΌΡΡΒ», β ΡΡΠΈΡΠ°Π΅Ρ ΠΠ»Π΅ΠΊΡΠ°Π½Π΄Ρ ΠΠΎΠ»ΠΎΠ΄Π½ΠΎΠ².
ΠΠΊΡΠΏΠ΅ΡΡ Π°ΠΊΡΠ΅Π½ΡΠΈΡΡΠ΅Ρ Π²Π½ΠΈΠΌΠ°Π½ΠΈΠ΅ Π½Π° ΡΠΎΠΌ, ΡΡΠΎ Π΅ΡΠ»ΠΈ ΡΡΠ΅Π½ΠΊΠ° ΡΠΈΠ»ΠΎΡΠ° ΡΠ°Π±ΠΎΡΠ°Π΅Ρ ΠΏΡΠ°ΠΊΡΠΈΡΠ΅ΡΠΊΠΈ Π½Π° ΡΠ°ΡΡΡΠΆΠ΅Π½ΠΈΠ΅ (ΡΠΆΠ°ΡΠΈΠ΅ Π²ΠΎΡΠΏΡΠΈΠ½ΠΈΠΌΠ°ΡΡ Π²Π΅ΡΡΠΈΠΊΠ°Π»ΡΠ½ΡΠ΅ ΡΠ»Π΅ΠΌΠ΅Π½ΡΡ-ΡΠ΅Π±ΡΠ°), ΡΠΎ ΠΊΠΎΠ½ΡΡΡΡΠΊΡΠΈΠΈ ΠΊΡΡΡΠΈ ΡΠ°Π±ΠΎΡΠ°ΡΡ Π½Π° ΡΠ»ΠΎΠΆΠ½ΡΠ΅ Π²ΠΈΠ΄Ρ Π½Π°Π³ΡΡΠΆΠ΅Π½ΠΈΡ: ΡΠΆΠ°ΡΠΈΠ΅ Ρ ΠΈΠ·Π³ΠΈΠ±ΠΎΠΌ, ΡΠ°ΡΡΡΠΆΠ΅Π½ΠΈΠ΅ Ρ ΠΈΠ·Π³ΠΈΠ±ΠΎΠΌ ΠΈ ΠΈΠ·Π³ΠΈΠ± Ρ ΠΊΡΡΡΠ΅Π½ΠΈΠ΅ΠΌ.
Β«Π£ΡΠΈΡΡΠ²Π°Ρ, ΡΡΠΎ ΡΠΈΠ»ΠΎΡΡ ΡΠ²Π»ΡΡΡΡΡ Π΄ΠΎΠ²ΠΎΠ»ΡΠ½ΠΎ Π²ΡΡΠΎΠΊΠΈΠΌΠΈ ΡΠΎΠΎΡΡΠΆΠ΅Π½ΠΈΡΠΌΠΈ, ΠΏΡΠΈ ΠΈΡ ΠΌΠΎΠ½ΡΠ°ΠΆΠ΅ Π²ΠΎΠ·ΠΌΠΎΠΆΠ½ΠΎ Π½Π°ΠΊΠΎΠΏΠ»Π΅Π½ΠΈΠ΅ ΠΎΡΠΊΠ»ΠΎΠ½Π΅Π½ΠΈΠΉ ΡΠ°Π·ΠΌΠ΅ΡΠΎΠ² ΠΎΡ ΠΏΡΠΎΠ΅ΠΊΡΠ½ΡΡ ΠΏΠΎ Π²ΡΡΠΎΡΠ΅ ΠΈ Π² ΠΏΠ»ΠΎΡΠΊΠΎΡΡΠΈ (Ρ.Π½. ΡΠ»Π»ΠΈΠΏΡΠΎΠΈΠ΄Π½ΠΎΡΡΡ). ΠΠΎΡΠΊΠΎΠ»ΡΠΊΡ ΠΏΡΠΈ ΡΠ°ΡΡΠ΅ΡΠ°Ρ ΠΏΠΎΠ΄ΠΎΠ±Π½ΡΠ΅ ΡΠ°ΠΊΡΠΎΡΡ Π²ΠΎΠ·Π΄Π΅ΠΉΡΡΠ²ΠΈΡ Π½Π° ΠΊΠΎΠ½ΡΡΡΡΠΊΡΠΈΠΈ Π½Π΅ ΡΡΠΈΡΡΠ²Π°ΡΡΡΡ, Π² ΡΠ΅Π°Π»ΡΠ½ΡΡ ΠΊΠΎΠ½ΡΡΡΡΠΊΡΠΈΡΡ ΠΏΠΎΠΊΡΡΡΠΈΡ ΠΌΠΎΠ³ΡΡ Π²ΠΎΠ·Π½ΠΈΠΊΠ½ΡΡΡ ΠΎΡΠ΅Π½Ρ Π±ΠΎΠ»ΡΡΠΈΠ΅ Π½Π΅ΠΏΡΠΎΠ΅ΠΊΡΠ½ΡΠ΅ ΡΡΠΈΠ»ΠΈΡ. Π₯ΠΎΡΡ, Π΅ΡΠ»ΠΈ ΡΠ°ΡΡΠΌΠ°ΡΡΠΈΠ²Π°ΡΡ Π²ΠΎΠΏΡΠΎΡ Π² ΠΏΡΠ°ΠΊΡΠΈΡΠ΅ΡΠΊΠΎΠΉ ΠΏΠ»ΠΎΡΠΊΠΎΡΡΠΈ, ΡΠΎ ΠΏΡΠΎΡΠ΅ΡΡ Π²ΡΠΏΠ°Π΄Π΅Π½ΠΈΡ ΡΠ½Π΅Π³Π° Π½Π΅ ΡΠ²Π»ΡΠ΅ΡΡΡ ΠΌΠ³Π½ΠΎΠ²Π΅Π½Π½ΡΠΌ: ΠΎΠ½ Π»Π΅Π³ΠΊΠΎ ΠΏΡΠΎΠ³Π½ΠΎΠ·ΠΈΡΡΠ΅ΡΡΡ. Π ΠΏΡΠΈ Ρ ΠΎΡΠΎΡΠ΅ΠΌ ΠΎΠ±ΡΠ»ΡΠΆΠΈΠ²Π°Π½ΠΈΠΈ Π·Π΄Π°Π½ΠΈΠΉ Π½Π΅ ΠΏΡΠ΅Π΄ΡΡΠ°Π²Π»ΡΠ΅Ρ ΠΎΠΏΠ°ΡΠ½ΠΎΡΡΠΈ β Π²ΡΠ΅Π³Π΄Π° ΠΌΠΎΠΆΠ½ΠΎ Π½Π°Π±ΡΠ°ΡΡ Π»ΡΠ΄Π΅ΠΉ Π΄Π»Ρ ΠΎΡΠΈΡΡΠΊΠΈ ΠΊΡΡΡΒ», β ΠΎΠ±ΡΡΡΠ½ΡΠ΅Ρ ΠΏΡΠΎΡΠ΅ΡΡΠΎΡ.
Π§ΡΠΎ ΠΆΠ΅ ΠΊΠ°ΡΠ°Π΅ΡΡΡ Π²Π΅ΡΡΠΎΠ²ΡΡ Π½Π°Π³ΡΡΠ·ΠΎΠΊ, ΡΠΎ ΠΏΠΎ Π΅Π³ΠΎ ΡΠ»ΠΎΠ²Π°ΠΌ, ΠΎΠ½ΠΈ ΠΎΠΏΠ°ΡΠ½Ρ Π΄Π»Ρ ΡΠΈΠ»ΠΎΡΠΎΠ² Ρ ΠΎΡΠ΅Π½Ρ Π±ΠΎΠ»ΡΡΠΎΠΉ Π±ΠΎΠΊΠΎΠ²ΠΎΠΉ ΠΏΠΎΠ²Π΅ΡΡ Π½ΠΎΡΡΡΡ, ΠΊΠΎΡΠΎΡΡΠ΅ Π½Π°Ρ ΠΎΠ΄ΡΡΡΡ Π² Π½Π΅Π·Π°Π³ΡΡΠΆΠ΅Π½Π½ΠΎΠΌ ΡΠΎΡΡΠΎΡΠ½ΠΈΠΈ. ΠΠ»Ρ Π·Π°Π³ΡΡΠΆΠ΅Π½Π½ΡΡ ΡΠΈΠ»ΠΎΡΠΎΠ² Π²Π΅ΡΡΠΎΠ²Π°Ρ Π½Π°Π³ΡΡΠ·ΠΊΠ° ΠΎΠΏΠ°ΡΠ½ΠΎΡΡΠΈ Π½Π΅ ΠΏΡΠ΅Π΄ΡΡΠ°Π²Π»ΡΠ΅Ρ.
ΠΡΠ΅ ΡΠΊΡΠΏΠ΅ΡΡΡ Π΅Π΄ΠΈΠ½Ρ Π²ΠΎ ΠΌΠ½Π΅Π½ΠΈΠΈ β ΠΈΠ·Π±Π΅ΠΆΠ°ΡΡ Π½Π΅ΠΏΡΠΈΡΡΠ½ΠΎΡΡΠ΅ΠΉ Ρ ΠΊΡΡΡΠ°ΠΌΠΈ ΠΌΠΎΠΆΠ½ΠΎ Π»ΠΈΡΡ ΠΏΠΎΠΊΡΠΏΠ°Ρ ΡΠΈΠ»ΠΎΡΡ Ρ Π½Π°Π΄Π΅ΠΆΠ½ΡΡ ΠΈ ΠΏΡΠΎΠ²Π΅ΡΠ΅Π½Π½ΡΡ ΠΏΠΎΡΡΠ°Π²ΡΠΈΠΊΠΎΠ², ΡΡΠΈ Π΅ΠΌΠΊΠΎΡΡΠΈ Π΄Π»Ρ Ρ ΡΠ°Π½Π΅Π½ΠΈΡ Π·Π΅ΡΠ½Π° ΠΏΡΠΎΡΠ»ΠΈ ΠΈΡΠΏΡΡΠ°Π½ΠΈΠ΅ Π²ΡΠ΅ΠΌΠ΅Π½Π΅ΠΌ, Π²Π΅ΡΡΠ°ΠΌΠΈ ΠΈ ΡΠ½Π΅Π³ΠΎΠΌ, Π° ΡΠ°ΠΌΠΎΠ΅ Π³Π»Π°Π²Π½ΠΎΠ΅ β ΠΊΠΎΠ½ΡΡΡΡΠΊΡΠΈΠΈ Π΄ΠΎΠ»ΠΆΠ½Ρ Π±ΡΡΡ ΡΠ΅ΡΡΠΈΡΠΈΡΠΈΡΠΎΠ²Π°Π½Ρ Π² Π½Π°ΡΠ΅ΠΉ ΡΡΡΠ°Π½Π΅.
ΠΠΠΠΠΠΠΠΠ«Π ΠΠΠΠ Π«
Π‘ΠΏΠ΅ΡΠΈΠ°Π»ΠΈΡΡΡ ΡΡΠ²Π΅ΡΠΆΠ΄Π°ΡΡ, ΡΡΠΎ ΠΏΡΠΈΠ²Π΅ΡΡΠΈ ΠΊ Π±Π΅Π΄Π΅ ΠΌΠΎΠ³ΡΡ Π½Π΅Π³ΡΠ°ΠΌΠΎΡΠ½ΠΎ ΠΏΠΎΡΡΠ°Π²Π»Π΅Π½Π½ΡΠ΅ ΠΈΠ»ΠΈ ΡΠ΄Π΅Π»Π°Π½Π½ΡΠ΅ Π½Π΅ ΠΈΠ· ΡΠΎΠ³ΠΎ ΠΏΡΠΎΡΠΈΠ»Ρ ΠΎΠΏΠΎΡΡ.
ΠΠ°ΡΠ°Π»ΡΠ½ΠΈΠΊ ΡΠ΅Ρ Π½ΠΈΡΠ΅ΡΠΊΠΎΠ³ΠΎ ΠΎΡΠ΄Π΅Π»Π° ΠΡΡΠΏΠΏΡ ΠΠΠ ΠΠ’Π ΠΠΠ Π‘Π΅ΡΠ³Π΅ΠΉ Π©Π΅ΡΠ±Π°Π½Ρ ΡΠ΅ΠΊΠΎΠΌΠ΅Π½Π΄ΡΠ΅Ρ ΠΎΠ±ΡΠ°ΡΠ°ΡΡ Π²Π½ΠΈΠΌΠ°Π½ΠΈΠ΅ Π½Π° ΠΎΠΏΠΎΡΡ Π½Π°Π΄ΡΠΈΠ»ΠΎΡΠ½ΡΡ Π³Π°Π»Π΅ΡΠ΅ΠΉ.
Β«ΠΡΠ»ΠΈ ΠΏΡΠΎΠ΅ΠΊΡΠΎΠΌ ΠΏΡΠ΅Π΄ΡΡΠΌΠΎΡΡΠ΅Π½Π° ΠΎΠΏΠΎΡΠ° ΡΠ°ΡΡΠΈ Π΄Π°Π½Π½ΠΎΠΉ Π³Π°Π»Π΅ΡΠ΅ΠΈ Π½Π° ΠΊΠΎΠ½ΡΡ ΠΊΡΡΡΠΈ ΡΠΈΠ»ΠΎΡΠ°, ΡΠΎ, ΠΊΠ°ΠΊ ΠΏΡΠ°Π²ΠΈΠ»ΠΎ, Π·ΠΈΠΌΠΎΠΉ ΠΈΠ·-Π·Π° ΠΎΠ±Π»Π΅Π΄Π΅Π½Π΅Π½ΠΈΡ ΠΈΠ»ΠΈ Π±ΠΎΠ»ΡΡΠΎΠ³ΠΎ ΡΠ½Π΅Π³Π° ΡΡΠΎ ΠΌΠΎΠΆΠ΅Ρ ΠΏΡΠΈΠ²Π΅ΡΡΠΈ ΠΊ ΠΏΠΎΠ»Π½ΠΎΠΌΡ ΡΠ°Π·ΡΡΡΠ΅Π½ΠΈΡ ΡΠΈΠ»ΠΎΡΠ°Β», β ΠΏΠΎΠ΄ΡΠ΅ΡΠΊΠΈΠ²Π°Π΅Ρ Π‘Π΅ΡΠ³Π΅ΠΉ Π©Π΅ΡΠ±Π°Π½Ρ.
Π ΠΏΡΠΎΡΠ΅ΡΡΠΎΡ ΠΠ»Π΅ΠΊΡΠ°Π½Π΄Ρ ΠΠΎΠ»ΠΎΠ΄Π½ΠΎΠ² Π² ΡΠ²ΠΎΡ ΠΎΡΠ΅ΡΠ΅Π΄Ρ Π°ΠΊΡΠ΅Π½ΡΠΈΡΡΠ΅Ρ Π²Π½ΠΈΠΌΠ°Π½ΠΈΠ΅ Π΅ΡΠ΅ Π½Π° Π΄Π²ΡΡ ΠΏΠΎΠ·ΠΈΡΠΈΡΡ : ΠΏΡΠΎΠΌΠ΅ΠΆΡΡΠΎΡΠ½ΠΎΠΉ ΠΎΠΏΠΎΡΠ΅ ΡΠΈΠ»ΠΎΡΠ° ΠΈ ΠΌΠ΅ΡΠ°Π»Π»ΠΈΡΠ΅ΡΠΊΠΈΡ ΠΊΠΎΠ»ΠΎΠ½Π½Π°Ρ , Π½Π° ΠΊΠΎΡΠΎΡΡΠ΅ ΡΡΡΠ°Π½Π°Π²Π»ΠΈΠ²Π°ΡΡΡΡ Π΅ΠΌΠΊΠΎΡΡΠΈ Π΄Π»Ρ Π·Π΅ΡΠ½Π° Ρ ΠΊΠΎΠ½ΡΡΠΎΠΎΠ±ΡΠ°Π·Π½ΡΠΌ Π΄Π½ΠΈΡΠ΅ΠΌ.
Β«ΠΠ»ΠΎΡ ΠΎ, ΡΡΠΎ Π»ΡΠ΄ΠΈ, ΠΏΡΡΠ°ΡΡΡ ΡΠΉΡΠΈ ΠΎΡ Π΄ΠΎΠΏΠΎΠ»Π½ΠΈΡΠ΅Π»ΡΠ½ΡΡ Π·Π°ΡΡΠ°Ρ, ΠΌΠ΅Π½ΡΡΡ ΠΊΠΎΠ½ΡΡΡΡΠΊΡΠΈΡ ΠΊΠΎΠΌΠΏΠ»Π΅ΠΊΡΠ°. ΠΠ΅Π΄Ρ Π΄Π»Ρ ΡΠΎΠ³ΠΎ, ΡΡΠΎΠ±Ρ Π·Π°Π³ΡΡΠ·ΠΈΡΡ Π·Π΅ΡΠ½ΠΎ Π² ΡΠΈΠ»ΠΎΡ, Π΅Π³ΠΎ Π½Π°Π΄ΠΎ ΠΏΠΎΠ΄Π°ΡΡ ΠΊ Π·Π°Π³ΡΡΠ·ΠΎΡΠ½ΠΎΠΌΡ ΠΎΡΠ²Π΅ΡΡΡΠΈΡ Π½Π° Π±ΠΎΠ»ΡΡΠΎΠΉ Π²ΡΡΠΎΡΠ΅. ΠΠΎΠ΄Π°ΡΠ° Π·Π΅ΡΠ½Π° Π²ΡΠΏΠΎΠ»Π½ΡΠ΅ΡΡΡ Ρ ΠΏΠΎΠΌΠΎΡΡΡ ΡΡΠ°Π½ΡΠΏΠΎΡΡΠ΅ΡΠΎΠ², ΠΊΠΎΡΠΎΡΡΠ΅ ΡΡΡΠ°Π½Π°Π²Π»ΠΈΠ²Π°ΡΡΡΡ Π½Π° ΡΡΠ°Π»ΡΠ½ΡΡ Π³Π°Π»Π΅ΡΠ΅ΡΡ . ΠΠ°Π»Π΅ΡΠ΅ΠΈ, ΠΊΠ°ΠΊ ΠΏΡΠ°Π²ΠΈΠ»ΠΎ, ΠΎΠΏΠΈΡΠ°ΡΡΡΡ Π½Π° Π²Π΅ΡΡ ΡΡΠΊΡ ΡΠΈΠ»ΠΎΡΠ° ΠΈ Π½Π° ΠΏΡΠΎΠΌΠ΅ΠΆΡΡΠΎΡΠ½ΡΠ΅ ΠΎΠΏΠΎΡΡ ΠΌΠ΅ΠΆΠ΄Ρ ΡΠΈΠ»ΠΎΡΠ°ΠΌΠΈ. ΠΠΎ Π·Π°ΡΠ°ΡΡΡΡ ΠΏΡΠΎΠΌΠ΅ΠΆΡΡΠΎΡΠ½ΡΠ΅ ΠΎΠΏΠΎΡΡ ΠΌΠ΅ΠΆΠ΄Ρ ΡΠΈΠ»ΠΎΡΠ°ΠΌΠΈ Π½Π΅ Ρ ΠΎΡΡΡ ΡΡΠ°Π²ΠΈΡΡ, Π² ΡΠ²ΡΠ·ΠΈ Ρ ΡΠ΅ΠΌ ΠΏΡΠΈΡ ΠΎΠ΄ΠΈΡΡΡ ΠΎΠΏΠΈΡΠ°ΡΡ Π³Π°Π»Π΅ΡΠ΅Ρ Π½Π° Π²Π΅ΡΡΠΈΠΊΠ°Π»ΡΠ½ΡΠ΅ ΡΠ΅Π±ΡΠ° ΠΏΠΎ ΠΊΡΠ°Ρ ΡΠΈΠ»ΠΎΡΠ°. Π ΡΡΠΎΠΌ ΡΠ»ΡΡΠ°Π΅ Π²Π΅ΡΡΠΈΠΊΠ°Π»ΡΠ½ΡΠ΅ ΡΠ΅Π±ΡΠ° Π΄Π΅Π»Π°ΡΡ ΠΈΠ· Π±ΠΎΠ»Π΅Π΅ ΠΌΠΎΡΠ½ΠΎΠ³ΠΎ ΠΏΡΠΎΡΠΈΠ»Ρ, ΡΡΠΎ ΠΈΡΠΊΠ»ΡΡΠ°Π΅Ρ ΡΠ°Π²Π½ΠΎΠΌΠ΅ΡΠ½ΠΎΠ΅ ΡΠ°ΡΡΡΠΆΠ΅Π½ΠΈΠ΅ ΡΠΈΠ»ΠΎΡΠ° Π² ΠΏΡΠΎΡΠ΅ΡΡΠ΅ Π½Π°Π³ΡΡΠΆΠ΅Π½ΠΈΡ. Π‘ΠΈΠ»ΠΎΡ β ΡΡΠΎ Π±ΠΎΡΠΊΠ°, ΠΊΠΎΡΠΎΡΠ°Ρ Π΄ΠΎΠ»ΠΆΠ½Π° ΡΠ²ΠΎΠ±ΠΎΠ΄Π½ΠΎ ΡΠ°ΡΡΡΠ³ΠΈΠ²Π°ΡΡΡΡ ΠΏΡΠΈ Π·Π°Π³ΡΡΠ·ΠΊΠ΅ ΠΈ Π²ΠΎΠ·Π²ΡΠ°ΡΠ°ΡΡΡΡ Π² ΠΈΡΡ ΠΎΠ΄Π½ΠΎΠ΅ ΠΏΠΎΠ»ΠΎΠΆΠ΅Π½ΠΈΠ΅ ΠΏΠΎΡΠ»Π΅ Π²ΡΠ³ΡΡΠ·ΠΊΠΈ Π·Π΅ΡΠ½Π°. ΠΠ°ΡΠΊΠΎΠ»ΡΠΊΠΎ ΡΡΠΎ ΠΎΠΏΠ°ΡΠ½ΠΎ Π΄Π»Ρ ΠΊΠΎΠ½ΡΡΡΡΠΊΡΠΈΠΈ ΡΠΈΠ»ΠΎΡΠ°, ΡΠ»ΠΎΠΆΠ½ΠΎ ΡΠΏΡΠΎΠ³Π½ΠΎΠ·ΠΈΡΠΎΠ²Π°ΡΡ. ΠΡΠΎ ΠΌΠΎΠΆΠ½ΠΎ ΠΎΠ±ΠΎΡΠ½ΠΎΠ²Π°ΡΡ ΡΠ΅Π·ΡΠ»ΡΡΠ°ΡΠ°ΠΌΠΈ ΡΠ°ΡΡΠ΅ΡΠ° ΠΈ ΠΈΠ·ΡΡΠ΅Π½ΠΈΡ ΠΎΠΏΡΡΠ° ΠΈΡΠΏΠΎΠ»ΡΠ·ΠΎΠ²Π°Π½ΠΈΡ ΡΠ°ΠΊΠΈΡ ΠΊΠΎΠ½ΡΡΡΡΠΊΡΠΈΠΉΒ», β ΠΎΡΠΌΠ΅ΡΠ°Π΅Ρ ΠΠ»Π΅ΠΊΡΠ°Π½Π΄Ρ ΠΠΎΠ»ΠΎΠ΄Π½ΠΎΠ².
ΠΠ½ ΡΠ°ΠΊΠΆΠ΅ ΡΠΎΠ²Π΅ΡΡΠ΅Ρ ΠΎΠ±ΡΠ°ΡΠ°ΡΡ Π²Π½ΠΈΠΌΠ°Π½ΠΈΠ΅ Π½Π° ΠΎΠΏΠΎΡΠ½ΡΠ΅ ΠΌΠ΅ΡΠ°Π»Π»ΠΈΡΠ΅ΡΠΊΠΈΠ΅ ΠΊΠΎΠ½ΡΡΡΡΠΊΡΠΈΠΈ ΠΏΠΎΠ΄ ΡΠΈΠ»ΠΎΡΠ°ΠΌΠΈ Ρ ΠΊΠΎΠ½ΡΡΠ½ΡΠΌ Π΄Π½ΠΈΡΠ΅ΠΌ.
Β«ΠΡΠΈΠ΅Π·ΠΆΠ°ΡΡ Π»ΡΠ΄ΠΈ, Π³ΠΎΠ²ΠΎΡΡΡ, ΡΡΠΎ Ρ Π½ΠΈΡ ΡΠΏΠ°Π» ΡΠΈΠ»ΠΎΡ. ΠΠΊΠ°Π·ΡΠ²Π°Π΅ΡΡΡ, Π½Π°ΡΠ°Π»ΠΈ ΠΌΠΎΠ½ΡΠΈΡΠΎΠ²Π°ΡΡ ΡΠΈΠ»ΠΎΡ Π½Π° ΠΎΠΏΠΎΡΠ°Ρ ΠΈ Π·Π°Π±ΡΠ»ΠΈ ΠΏΠΎΡΡΠ°Π²ΠΈΡΡ ΡΠ²ΡΠ·ΠΈ ΠΌΠ΅ΠΆΠ΄Ρ ΠΎΠΏΠΎΡΠ½ΡΠΌΠΈ ΠΊΠΎΠ»ΠΎΠ½Π½Π°ΠΌΠΈ ΠΏΠΎ ΠΊΠΎΠ½ΡΡΡΡ. ΠΡΠ»ΠΈ ΠΊΠΎΠ»ΠΎΠ½Π½Π° ΡΠ°ΡΡΡΠΈΡΠ°Π½Π° ΡΠ°Π±ΠΎΡΠ°ΡΡ Π²ΠΌΠ΅ΡΡΠ΅ ΡΠΎ ΡΠ²ΡΠ·ΡΠΌΠΈ, Π° Π²Ρ Π·Π°Π±ΡΠ»ΠΈ ΠΈΡ ΠΏΠΎΡΡΠ°Π²ΠΈΡΡ, ΡΡΠΎ ΠΏΡΠΎΠΈΠ·ΠΎΠΉΠ΄Π΅Ρ? ΠΡΡΠ΅ΡΡΠ²Π΅Π½Π½ΠΎ, ΠΊΠΎΠ»ΠΎΠ½Π½Ρ ΠΏΠΎΡΠ΅ΡΡΠ»ΠΈ ΡΡΡΠΎΠΉΡΠΈΠ²ΠΎΡΡΡ, Π° ΡΠΈΠ»ΠΎΡ Π·Π°Π²Π°Π»ΠΈΠ»ΡΡ Π½Π°Π±ΠΎΠΊ. Π Π½Π΅Π³ΠΎ ΡΡΠΏΠ΅Π»ΠΈ Π·Π°Π³ΡΡΠ·ΠΈΡΡ ΡΠΎΠ»ΡΠΊΠΎ 100 Ρ Π·Π΅ΡΠ½Π° Π²ΠΌΠ΅ΡΡΠΎ 400 Ρ, Π½Π° ΠΊΠΎΡΠΎΡΡΠ΅ ΠΎΠ½ Π±ΡΠ» ΡΠ°ΡΡΡΠΈΡΠ°Π½. Π ΡΠ΅ΠΌ Π΄ΡΠΌΠ°Π»ΠΈ ΠΏΡΠΎΠ΅ΠΊΡΠΈΡΠΎΠ²ΡΠΈΠΊΠΈ, ΠΈΠ·Π³ΠΎΡΠΎΠ²ΠΈΡΠ΅Π»ΠΈ, ΠΌΠΎΠ½ΡΠ°ΠΆΠ½Π°Ρ ΠΈ ΡΠΊΡΠΏΠ»ΡΠ°ΡΠΈΡΡΡΡΠ°Ρ ΠΎΡΠ³Π°Π½ΠΈΠ·Π°ΡΠΈΠΈ? ΠΡΠΎ ΠΏΡΠΈΠ½ΠΈΠΌΠ°Π» ΡΡΠΎ ΡΠΎΠΎΡΡΠΆΠ΅Π½ΠΈΠ΅ Π² ΡΠΊΡΠΏΠ»ΡΠ°ΡΠ°ΡΠΈΡ? ΠΠ°ΠΊ ΠΌΠΎΠΆΠ½ΠΎ Π±ΡΠ»ΠΎ Π·Π°Π³ΡΡΠΆΠ°ΡΡ ΡΠΈΠ»ΠΎΡ, Π΅ΡΠ»ΠΈ ΠΎΠ½ ΡΠΌΠΎΠ½ΡΠΈΡΠΎΠ²Π°Π½ Ρ Π½Π΅Π΄ΠΎΠ΄Π΅Π»ΠΊΠ°ΠΌΠΈ?Β» β Π½Π΅Π΄ΠΎΡΠΌΠ΅Π²Π°Π΅Ρ ΡΠΊΡΠΏΠ΅ΡΡ.
ΠΠΎ Π΅Π³ΠΎ ΡΠ»ΠΎΠ²Π°ΠΌ, Π½Π΅ΠΎΠ±Ρ ΠΎΠ΄ΠΈΠΌΠΎ ΡΠ»Π΅Π΄ΠΈΡΡ, ΡΡΠΎΠ±Ρ Π² ΠΎΠΏΠΎΡΠ°Ρ , ΡΠ°ΡΠΏΠΎΡΠΊΠ°Ρ ΠΈ Π΄ΡΡΠ³ΠΈΡ ΡΠ»Π΅ΠΌΠ΅Π½ΡΠ°Ρ Π±ΡΠ» ΠΏΡΠΈΠΌΠ΅Π½Π΅Π½ ΠΏΡΠΎΡΠΈΠ»Ρ, ΠΊΠΎΡΠΎΡΡΠΉ ΡΠΎΠΎΡΠ²Π΅ΡΡΡΠ²ΡΠ΅Ρ ΡΡΠ΅Π±ΠΎΠ²Π°Π½ΠΈΡΠΌ Π½ΠΎΡΠΌΠ°ΡΠΈΠ²Π½ΠΎΠΉ Π΄ΠΎΠΊΡΠΌΠ΅Π½ΡΠ°ΡΠΈΠΈ.
Β«ΠΠΌΠ΅ΡΡΠΈΠ΅ΡΡ Π² Π½ΠΎΡΠΌΠ°ΡΠΈΠ²Π½ΠΎΠΉ Π΄ΠΎΠΊΡΠΌΠ΅Π½ΡΠ°ΡΠΈΠΈ ΠΎΠ³ΡΠ°Π½ΠΈΡΠ΅Π½ΠΈΡ ΠΏΠΎ Π³ΠΈΠ±ΠΊΠΎΡΡΠΈ ΡΠ»Π΅ΠΌΠ΅Π½ΡΠΎΠ² Π½Π΅ ΠΏΡΠΈΡΠ»Π°Π½Ρ Π½Π°ΠΌ Ρ ΠΠ°ΡΡΠ° ΠΏΠΎ ΡΠ°ΠΊΡΡ, Π° ΠΏΠΎΠ»ΡΡΠ΅Π½Ρ ΠΏΡΡΠ΅ΠΌ ΠΈΠ·ΡΡΠ΅Π½ΠΈΡ Π½Π΅ ΠΎΠ΄Π½ΠΈΠΌ ΠΏΠΎΠΊΠΎΠ»Π΅Π½ΠΈΠ΅ΠΌ ΠΈΠ½ΠΆΠ΅Π½Π΅ΡΠΎΠ² Π΄Π΅ΠΉΡΡΠ²ΠΈΡΠ΅Π»ΡΠ½ΠΎΠΉ ΡΠ°Π±ΠΎΡΡ ΠΊΠΎΠ½ΡΡΡΡΠΊΡΠΈΠΉ. Π ΠΏΠΎΠ²Π΅ΡΡΡΠ΅, Π·Π° ΡΡΠΎΡ ΠΎΠΏΡΡ Π·Π°ΠΏΠ»Π°ΡΠ΅Π½ΠΎ ΠΎΡΠ΅Π½Ρ Π΄ΠΎΡΠΎΠ³ΠΎ, Π² Ρ.Ρ. ΠΈ ΠΊΡΠΎΠ²ΡΡΒ», β ΡΠ΅Π·ΡΠΌΠΈΡΡΠ΅Ρ ΠΠ»Π΅ΠΊΡΠ°Π½Π΄Ρ ΠΠΎΠ»ΠΎΠ΄Π½ΠΎΠ².
ΠΠ¨ΠΠΠΠ ΠΠ Π ΠΠΠ‘ΠΠΠ£ΠΠ’ΠΠ¦ΠΠ
ΠΠ°ΠΆΠ΅ Π³ΡΠ°ΠΌΠΎΡΠ½ΠΎ ΡΠΏΡΠΎΠ΅ΠΊΡΠΈΡΠΎΠ²Π°Π½Π½ΡΠΉ ΠΈ ΡΠΌΠΎΠ½ΡΠΈΡΠΎΠ²Π°Π½Π½ΡΠΉ ΡΠΈΠ»ΠΎΡ ΠΌΠΎΠΆΠ΅Ρ ΡΠ°Π·ΡΡΡΠΈΡΡΡΡ, Π΅ΡΠ»ΠΈ Π΅Π³ΠΎ Π½Π΅ΠΏΡΠ°Π²ΠΈΠ»ΡΠ½ΠΎ ΡΠΊΡΠΏΠ»ΡΠ°ΡΠΈΡΠΎΠ²Π°ΡΡ.
Β«ΠΠ΅ΡΠ°Π»Π»ΠΈΡΠ΅ΡΠΊΠΈΠ΅ Π΅ΠΌΠΊΠΎΡΡΠΈ Π΄Π»Ρ Ρ ΡΠ°Π½Π΅Π½ΠΈΡ Π·Π΅ΡΠ½Π° ΡΡΠ΅Π±ΡΡΡ ΡΡΡΠΎΠΆΠ°ΠΉΡΠ΅Π³ΠΎ ΠΊΠ²Π°Π»ΠΈΡΠΈΡΠΈΡΠΎΠ²Π°Π½Π½ΠΎΠ³ΠΎ ΠΏΠΎΠ΄Ρ ΠΎΠ΄Π° Π² ΠΏΡΠΎΡΠ΅ΡΡΠ΅ ΠΈΡ ΡΠΊΡΠΏΠ»ΡΠ°ΡΠ°ΡΠΈΠΈ. ΠΠ°Π»Π΅ΠΉΡΠ΅Π΅ ΠΎΡΠΊΠ»ΠΎΠ½Π΅Π½ΠΈΠ΅ ΠΎΡ ΡΠΎΠ±Π»ΡΠ΄Π΅Π½ΠΈΠΉ ΡΡΠ΅Π±ΠΎΠ²Π°Π½ΠΈΠΉ ΡΠ΅Ρ Π½ΠΈΡΠ΅ΡΠΊΠΎΠ³ΠΎ ΡΠ΅Π³Π»Π°ΠΌΠ΅Π½ΡΠ° ΠΏΡΠΈ ΡΠΊΡΠΏΠ»ΡΠ°ΡΠ°ΡΠΈΠΈ ΠΏΠΎΠ΄ΠΎΠ±Π½ΠΎΠ³ΠΎ ΡΠΎΠ΄Π° ΠΎΠ±ΠΎΡΡΠ΄ΠΎΠ²Π°Π½ΠΈΡ, ΠΊΠ°ΠΊ ΠΏΡΠ°Π²ΠΈΠ»ΠΎ, ΠΏΡΠΈΠ²ΠΎΠ΄ΠΈΡ ΠΊ ΡΠΎΠ·Π΄Π°Π½ΠΈΡ Π½Π΅ΡΠΏΡΠ°Π²Π»ΡΠ΅ΠΌΠΎΠΉ ΠΏΡΠ΅Π΄Π°Π²Π°ΡΠΈΠΉΠ½ΠΎΠΉ ΠΎΠ±ΡΡΠ°Π½ΠΎΠ²ΠΊΠΈ, ΡΠΏΠΎΡΠΎΠ±Π½ΠΎΠΉ ΠΏΡΠΈΠ²Π΅ΡΡΠΈ ΠΊ ΠΌΠ°ΡΡΡΠ°Π±Π½ΡΠΌ ΠΊΠ°ΡΠ°ΡΡΡΠΎΡΠΈΡΠ΅ΡΠΊΠΈΠΌ ΡΠ°Π·ΡΡΡΠ΅Π½ΠΈΡΠΌΒ», β Π³ΠΎΠ²ΠΎΡΠΈΡ ΠΊΠΎΠΌΠΌΠ΅ΡΡΠ΅ΡΠΊΠΈΠΉ Π΄ΠΈΡΠ΅ΠΊΡΠΎΡ Π³ΡΡΠΏΠΏΡ Β«Π ΠΠ‘Π’ΠΠ-Π₯ΠΠΠΠΠΠΒ» ΠΠΌΠΈΡΡΠΈΠΉ ΠΡΠΏΠ°Π²ΡΠ΅Π².
ΠΠ½ ΠΏΡΠ΅Π΄ΡΠΏΡΠ΅ΠΆΠ΄Π°Π΅Ρ, ΡΡΠΎ Π±Π΅Π΄Π° Π½Π΅ ΠΏΡΠΈΡ ΠΎΠ΄ΠΈΡ ΠΎΠ΄Π½Π° β ΡΠ°Π·ΡΡΡΠ°ΡΡΠΈΠΉΡΡ ΡΠΈΠ»ΠΎΡ, ΠΊΠ°ΠΊ ΠΏΡΠ°Π²ΠΈΠ»ΠΎ, Π·Π°Π΄Π΅Π²Π°Π΅Ρ ΠΈ Π΄ΡΡΠ³ΠΈΠ΅ ΠΎΠ±ΡΠ΅ΠΊΡΡ.
Β«Π‘ ΡΡΡΡΠΎΠΌ ΠΊΠΎΠΌΠΏΠΎΠ½ΠΎΠ²ΠΊΠΈ ΡΠΎΠ²ΡΠ΅ΠΌΠ΅Π½Π½ΡΡ ΡΠ»Π΅Π²Π°ΡΠΎΡΠ½ΡΡ ΠΊΠΎΠΌΠΏΠ»Π΅ΠΊΡΠΎΠ² ΡΠ°Π·ΡΡΡΠ΅Π½ΠΈΠ΅ ΠΎΠ΄Π½ΠΎΠ³ΠΎ ΠΈΠ· ΡΠΈΠ»ΠΎΡΠΎΠ² Π½Π΅ ΠΎΠ³ΡΠ°Π½ΠΈΡΠΈΠ²Π°Π΅ΡΡΡ ΡΠΎΠ»ΡΠΊΠΎ Π΅Π³ΠΎ ΠΏΠΎΠ²ΡΠ΅ΠΆΠ΄Π΅Π½ΠΈΠ΅ΠΌ ΠΈ, ΠΊΠ°ΠΊ ΠΏΡΠ°Π²ΠΈΠ»ΠΎ, Π²Π΅Π΄ΡΡ ΠΊ ΠΏΠΎΠ²ΡΠ΅ΠΆΠ΄Π΅Π½ΠΈΡ ΠΈΠ»ΠΈ ΡΠ°ΡΡΠΈΡΠ½ΠΎΠΌΡ ΡΠ°Π·ΡΡΡΠ΅Π½ΠΈΡ ΡΡΠ΄ΠΎΠΌ ΡΠ°ΡΠΏΠΎΠ»ΠΎΠΆΠ΅Π½Π½ΡΡ ΠΎΠ±ΡΠ΅ΠΊΡΠΎΠ²: ΡΠΌΠ΅ΠΆΠ½ΡΡ ΡΠΈΠ»ΠΎΡΠΎΠ², Π·Π΅ΡΠ½ΠΎΡΡΡΠΈΠ»ΠΎΠΊ, ΡΠ΅Ρ Π½ΠΎΠ»ΠΎΠ³ΠΈΡΠ΅ΡΠΊΠΎΠ³ΠΎ ΠΈ ΡΡΠ°Π½ΡΠΏΠΎΡΡΠ½ΠΎΠ³ΠΎ ΠΎΠ±ΠΎΡΡΠ΄ΠΎΠ²Π°Π½ΠΈΡ, ΠΊΠΎΠΌΠΌΡΠ½ΠΈΠΊΠ°ΡΠΈΠΉ ΠΈ ΡΠΈΡΡΠ΅ΠΌ ΡΠ»Π΅ΠΊΡΡΠΎ- ΠΈ Π³Π°Π·ΠΎΡΠ½Π°Π±ΠΆΠ΅Π½ΠΈΡΒ», β ΠΏΠΎΠ΄ΡΠ΅ΡΠΊΠΈΠ²Π°Π΅Ρ ΠΠΌΠΈΡΡΠΈΠΉ ΠΡΠΏΠ°Π²ΡΠ΅Π².
ΠΡΠΈΡΠΈΠ½Π°ΠΌΠΈ ΠΏΠ°Π΄Π΅Π½ΠΈΡ, ΠΏΠΎ ΡΠ»ΠΎΠ²Π°ΠΌ ΠΊΠΎΠΌΠΌΠ΅ΡΡΠ΅ΡΠΊΠΎΠ³ΠΎ Π΄ΠΈΡΠ΅ΠΊΡΠΎΡΠ° Π³ΡΡΠΏΠΏΡ Β«Π ΠΠ‘Π’ΠΠ-Π₯ΠΠΠΠΠΠΒ» ΠΌΠΎΠ³ΡΡ Π±ΡΡΡ Π½Π΅ΡΠ°Π²Π½ΠΎΠΌΠ΅ΡΠ½ΡΠ΅ Π·Π°Π³ΡΡΠ·ΠΊΠ° ΠΈΠ»ΠΈ Π²ΡΠ³ΡΡΠ·ΠΊΠ° ΡΠΈΠ»ΠΎΡΠ°.
Β«Π‘ΠΎΠ³Π»Π°ΡΠ½ΠΎ ΠΈΠ½ΡΡΡΡΠΊΡΠΈΠΈ, Π·Π΅ΡΠ½ΠΎ Π΄ΠΎΠ»ΠΆΠ½ΠΎ ΠΏΠΎΡΡΡΠΏΠ°ΡΡ Π² ΠΏΡΡΡΠΎΠΉ ΡΠΈΠ»ΠΎΡ ΡΠ½Π°ΡΠ°Π»Π° Π² ΡΠ΅Π½ΡΡΠ°Π»ΡΠ½ΡΡ Π²ΠΎΡΠΎΠ½ΠΊΡ. Π ΡΠ»ΡΡΠ°Π΅ ΠΏΠΎΠ΄Π°ΡΠΈ Π·Π΅ΡΠ½Π° ΡΠ΅ΡΠ΅Π· ΠΊΡΠ°ΠΉΠ½ΠΈΠ΅ Π²ΠΎΡΠΎΠ½ΠΊΠΈ, ΠΈΠ·-Π·Π° ΡΠΈΠ»ΡΠ½ΠΎΠ³ΠΎ Π΄Π°Π²Π»Π΅Π½ΠΈΡ Π½Π° ΡΡΠ΅Π½ΠΊΡ ΡΠΈΠ»ΠΎΡΠ°, ΠΏΠΎΡΠ»Π΅Π΄Π½ΠΈΠΉ ΠΌΠΎΠΆΠ΅Ρ Π΄Π΅ΡΠΎΡΠΌΠΈΡΠΎΠ²Π°ΡΡΡΡ, Π±ΡΠΊΠ²Π°Π»ΡΠ½ΠΎ Β«ΡΠ»ΠΎΠΆΠΈΡΡΡΡ Π³Π°ΡΠΌΠΎΡΠΊΠΎΠΉΒ», β Π³ΠΎΠ²ΠΎΡΠΈΡ ΠΠΌΠΈΡΡΠΈΠΉ ΠΡΠΏΠ°Π²ΡΠ΅Π².
Π ΡΠ²ΠΎΡ ΠΎΡΠ΅ΡΠ΅Π΄Ρ Π½Π°ΡΠ°Π»ΡΠ½ΠΈΠΊ ΡΠ΅Ρ Π½ΠΈΡΠ΅ΡΠΊΠΎΠ³ΠΎ ΠΎΡΠ΄Π΅Π»Π° ΠΡΡΠΏΠΏΡ ΠΠΠ ΠΠ’Π ΠΠΠ Π‘Π΅ΡΠ³Π΅ΠΉ Π©Π΅ΡΠ±Π°Π½Ρ ΠΎΠ±ΡΠ°ΡΠ°Π΅Ρ Π²Π½ΠΈΠΌΠ°Π½ΠΈΠ΅, ΡΡΠΎ ΠΊ ΡΠ°Π·ΡΡΡΠ΅Π½ΠΈΡ ΡΠΈΠ»ΠΎΡΠ° ΠΌΠΎΠΆΠ΅Ρ ΠΏΡΠΈΠ²Π΅ΡΡΠΈ Π½Π΅ ΡΠΎΠ»ΡΠΊΠΎ Π½Π΅ΡΠ°Π²Π½ΠΎΠΌΠ΅ΡΠ½ΠΎΠ΅ Π½Π°ΠΏΠΎΠ»Π½Π΅Π½ΠΈΠ΅, Π½ΠΎ ΠΈ Π½Π΅ΠΏΡΠ°Π²ΠΈΠ»ΡΠ½Π°Ρ Π²ΡΠ³ΡΡΠ·ΠΊΠ°.
Β«ΠΡΠΈ Π²ΡΠ³ΡΡΠ·ΠΊΠ΅ ΡΠΈΠ»ΠΎΡΠ° ΠΎΡΠ΅Π½Ρ Π²Π°ΠΆΠ½ΠΎ ΠΊΠΎΠ½ΡΡΠΎΠ»ΠΈΡΠΎΠ²Π°ΡΡ Β«Π·Π°Π²ΠΈΡΠ°Π½ΠΈΠ΅Β» Π·Π΅ΡΠ½Π°, ΠΊΠΎΡΠΎΡΠΎΠ΅ ΠΌΠΎΠΆΠ΅Ρ ΡΠΎΡΠΌΠΈΡΠΎΠ²Π°ΡΡΡΡ ΠΈΠ·-Π·Π° ΠΎΡΠΏΠΎΡΠ΅Π²Π°Π½ΠΈΡ Π·Π΅ΡΠ½Π° Π² ΠΏΡΠΎΡΠ΅ΡΡΠ΅ Π΄Π»ΠΈΡΠ΅Π»ΡΠ½ΠΎΠ³ΠΎ Ρ ΡΠ°Π½Π΅Π½ΠΈΡ. ΠΠ°Π½Π½Π°Ρ ΡΠΈΡΡΠ°ΡΠΈΡ ΠΌΠΎΠΆΠ΅Ρ ΠΏΡΠΈΠ²Π΅ΡΡΠΈ ΠΊ ΡΠΎΠΌΡ, ΡΡΠΎ Π½ΠΈΠΆΠ½ΡΡ ΡΠ°ΡΡΡ ΡΠΈΠ»ΠΎΡΠ° Π²ΡΠ³ΡΡΠ·ΠΈΡΡΡ ΠΏΠΎΠ»Π½ΠΎΡΡΡΡ, Π° Π² Π²Π΅ΡΡ Π½Π΅ΠΉ Π±ΡΠ΄Π΅Ρ ΠΎΡΡΠ°Π²Π°ΡΡΡΡ Π·Π΅ΡΠ½ΠΎ, ΡΡΠΎ ΠΌΠΎΠΆΠ΅Ρ ΠΏΠΎΠ²Π»Π΅ΡΡ Π·Π° ΡΠΎΠ±ΠΎΠΉ Β«ΡΠΊΠ»Π°Π΄ΡΠ²Π°Π½ΠΈΠ΅Β» ΠΈΠ»ΠΈ ΠΏΠ΅ΡΠ΅Π²ΠΎΡΠ°ΡΠΈΠ²Π°Π½ΠΈΠ΅ ΡΠΈΠ»ΠΎΡΠ°Β», β ΠΎΡΠΌΠ΅ΡΠ°Π΅Ρ ΠΏΡΠ΅Π΄ΡΡΠ°Π²ΠΈΡΠ΅Π»Ρ ΠΡΡΠΏΠΏΡ ΠΠΠ ΠΠ’Π ΠΠΠ.
ΠΠΎ ΡΠ»ΠΎΠ²Π°ΠΌ ΡΠΊΡΠΏΠ΅ΡΡΠΎΠ², ΠΏΡΠΈ Π²ΡΠ³ΡΡΠ·ΠΊΠ΅ Π²Π°ΠΆΠ½ΠΎ, ΡΡΠΎΠ±Ρ Π² ΠΏΠ΅ΡΠ²ΡΡ ΠΎΡΠ΅ΡΠ΅Π΄Ρ ΠΎΡΠΊΡΡΠ²Π°Π»Π°ΡΡ ΡΠ΅Π½ΡΡΠ°Π»ΡΠ½Π°Ρ Π·Π°Π΄Π²ΠΈΠΆΠΊΠ°, Π° Π½Π΅ Π±ΠΎΠΊΠΎΠ²ΡΠ΅.
Π‘Π΅ΡΠ³Π΅ΠΉ Π©Π΅ΡΠ±Π°Π½Ρ Π³ΠΎΠ²ΠΎΡΠΈΡ, ΡΡΠΎ ΡΠ΅Π³ΠΎΠ΄Π½Ρ ΠΏΡΠ΅Π΄ΠΎΡΠ²ΡΠ°ΡΠΈΡΡ ΠΎΡΠΈΠ±ΠΊΡ Ρ Π²ΡΠ³ΡΡΠ·ΠΊΠΎΠΉ ΠΏΠΎΠΌΠΎΠ³Π°Π΅Ρ Π°Π²ΡΠΎΠΌΠ°ΡΠΈΠ·Π°ΡΠΈΡ: Β«ΠΠ»ΠΎΡΠΊΠΎΠ΄ΠΎΠ½Π½ΡΠ΅ ΡΠΈΠ»ΠΎΡΡ Π΄Π»ΠΈΡΠ΅Π»ΡΠ½ΠΎΠ³ΠΎ Ρ ΡΠ°Π½Π΅Π½ΠΈΡ, ΠΊΠ°ΠΊ ΠΏΡΠ°Π²ΠΈΠ»ΠΎ, ΠΎΠ±ΠΎΡΡΠ΄ΠΎΠ²Π°Π½Ρ Π²ΡΠ³ΡΡΠ·Π½ΡΠΌΠΈ Π²ΠΎΡΠΎΠ½ΠΊΠ°ΠΌΠΈ, ΠΊΠΎΡΠΎΡΡΡ ΠΌΠΎΠΆΠ΅Ρ Π±ΡΡΡ 4β7 ΠΈ Π±ΠΎΠ»ΡΡΠ΅. ΠΡ ΠΊΠΎΠ»ΠΈΡΠ΅ΡΡΠ²ΠΎ Π·Π°Π²ΠΈΡΠΈΡ ΠΎΡ Π΄ΠΈΠ°ΠΌΠ΅ΡΡΠ° ΡΠΈΠ»ΠΎΡΠ°. Π¦Π΅Π½ΡΡΠ°Π»ΡΠ½Π°Ρ Π²ΠΎΡΠΎΠ½ΠΊΠ° ΠΎΠ±ΠΎΡΡΠ΄ΠΎΠ²Π°Π½Π° Π°Π²ΡΠΎΠΌΠ°ΡΠΈΡΠ΅ΡΠΊΠΎΠΉ Π²ΡΠ³ΡΡΠ·Π½ΠΎΠΉ Π·Π°Π΄Π²ΠΈΠΆΠΊΠΎΠΉ, Π²ΡΠ΅ ΠΎΡΡΠ°Π»ΡΠ½ΡΠ΅ ΠΏΠΎ ΠΏΠ΅ΡΠΈΡΠ΅ΡΠΈΠΈ β ΡΡΡΠ½ΡΠΌΠΈ Π·Π°Π΄Π²ΠΈΠΆΠΊΠ°ΠΌΠΈ. ΠΡΠΎ Π΄Π΅Π»Π°Π΅ΡΡΡ Π΄Π»Ρ ΡΠΎΠ³ΠΎ, ΡΡΠΎΠ±Ρ ΠΈΠ·Π±Π΅ΠΆΠ°ΡΡ Π½Π΅ΡΡΠ°Π±Π°ΡΡΠ²Π°Π½ΠΈΡ ΠΎΠ΄Π½ΠΎΠΉ ΠΈΠ· Π·Π°Π΄Π²ΠΈΠΆΠ΅ΠΊ ΠΈ Π½Π΅Π΄ΠΎΠΏΡΡΠ΅Π½ΠΈΡ ΡΠΈΡΡΠ°ΡΠΈΠΈ Ρ Π½Π΅ΡΠ°Π²Π½ΠΎΠΌΠ΅ΡΠ½ΠΎΠΉ Π²ΡΠ³ΡΡΠ·ΠΊΠΎΠΉ ΡΠΈΠ»ΠΎΡΠ°Β».
Β«ΠΠ΅ΡΠ½ΠΎ Π² ΡΡΠΎΠΌ ΡΠ»ΡΡΠ°Π΅ ΡΡΠ΅ΠΊΠ°Π΅ΡΡΡ Π² ΠΎΠ΄Π½Ρ ΡΡΠΎΡΠΎΠ½Ρ ΠΈ Π½Π΅ΡΠ°Π²Π½ΠΎΠΌΠ΅ΡΠ½ΠΎ Π΄Π°Π²ΠΈΡ Π½Π° ΡΡΠ΅Π½ΠΊΡ ΡΠΈΠ»ΠΎΡΠ° ΠΈ Π½Π° ΡΡΠ½Π΄Π°ΠΌΠ΅Π½Ρ. ΠΡΡΠ΅ΡΡΠ²Π΅Π½Π½ΠΎ, ΡΡΠ½Π΄Π°ΠΌΠ΅Π½Ρ ΡΠΆΠ΅ Π½Π΅ Π²ΠΎΠ·Π²ΡΠ°ΡΠ°Π΅ΡΡΡ Π² ΠΏΡΠ΅ΠΆΠ½Π΅Π΅ ΠΏΠΎΠ»ΠΎΠΆΠ΅Π½ΠΈΠ΅, ΠΏΠΎΡΠΎΠΌΡ ΡΡΠΎ Π² ΠΎΡΠ»ΠΈΡΠΈΠ΅ ΠΎΡ ΠΌΠ΅ΡΠ°Π»Π»Π°, Π³ΡΡΠ½Ρ Π½Π΅ ΠΎΠ±Π»Π°Π΄Π°Π΅Ρ ΡΠ²ΠΎΠΉΡΡΠ²ΠΎΠΌ ΡΠΏΡΡΠ³ΠΎΡΡΠΈ. ΠΡΠΈ ΠΏΠΎΡΠ»Π΅Π΄ΡΡΡΠ΅ΠΉ Π½Π΅ΡΠ°Π²Π½ΠΎΠΌΠ΅ΡΠ½ΠΎΠΉ Π·Π°Π³ΡΡΠ·ΠΊΠ΅ ΠΈΠ»ΠΈ ΡΠ°Π·Π³ΡΡΠ·ΠΊΠ΅ ΡΡΠ½Π΄Π°ΠΌΠ΅Π½Ρ Π΅ΡΠ΅ Π±ΠΎΠ»ΡΡΠ΅ ΠΏΠ΅ΡΠ΅ΠΊΠ°ΡΠΈΠ²Π°Π΅ΡΡΡ. Π Π΅ΡΠ»ΠΈ Ρ ΡΠΈΠ»ΠΎΡΠ° Π²ΡΡΠΎΡΠ° ΠΏΠΎΠ΄ 20 ΠΌΠ΅ΡΡΠΎΠ², ΡΠΎ ΠΏΡΠΎΠΈΠ·ΠΎΠΉΠ΄Π΅Ρ ΡΠΌΠ΅ΡΠ΅Π½ΠΈΠ΅ Π²Π΅ΡΡ Π° ΡΠΈΠ»ΠΎΡΠ° (ΠΊΡΠ΅Π½). ΠΡΠ΅Π΄ΡΡΠ°Π²Π»ΡΠ΅ΡΠ΅, ΡΡΠΎ Ρ ΡΡΠΈΠΌ ΡΠΈΠ»ΠΎΡΠΎΠΌ ΠΌΠΎΠΆΠ΅Ρ Π±ΡΡΡ? Π Π»ΡΡΡΠ΅ΠΌ ΡΠ»ΡΡΠ°Π΅ β ΠΏΡΠΎΡΡΠΎ ΡΠ°Π·Π²ΠΈΡΠΈΠ΅ Π΄Π΅ΡΠΎΡΠΌΠ°ΡΠΈΠΉ, Π² Ρ ΡΠ΄ΡΠ΅ΠΌ β ΠΎΠ±ΡΡΡΠ΅Π½ΠΈΠ΅Β», β ΠΎΠ±ΡΡΡΠ½ΡΠ΅Ρ ΠΠ»Π΅ΠΊΡΠ°Π½Π΄Ρ ΠΠΎΠ»ΠΎΠ΄Π½ΠΎΠ².
ΠΠ½ ΡΠ°ΡΡΠΊΠ°Π·ΡΠ²Π°Π΅Ρ Π΅ΡΠ΅ ΠΎΠ± ΠΎΠ΄Π½ΠΎΠΉ ΠΎΡΠΈΠ±ΠΊΠ΅, ΠΊΠΎΡΠΎΡΠ°Ρ ΡΡΠ°Π»Π° ΠΏΡΠΈΡΠΈΠ½ΠΎΠΉ ΡΠ°Π·ΡΡΡΠ΅Π½ΠΈΡ ΠΊΡΡΡΠΈ Π½Π° ΠΎΠ΄Π½ΠΎΠΌ ΡΠΊΡΠ°ΠΈΠ½ΡΠΊΠΎΠΌ ΡΠ»Π΅Π²Π°ΡΠΎΡΠ΅.
Β«ΠΡΠ»ΠΈ Π·Π°ΠΊΡΡΡΡ Π²Π΅Π½ΡΠΈΠ»ΡΡΠΈΠΎΠ½Π½ΡΠ΅ ΠΎΡΠ²Π΅ΡΡΡΠΈΡ Π² ΠΊΡΡΡΠ΅, ΠΈ Π½Π°ΡΠ°ΡΡ ΡΠ΅Π·ΠΊΠΎ Π²ΡΠ³ΡΡΠΆΠ°ΡΡ Π·Π΅ΡΠ½ΠΎ, Π²Π°ΠΊΡΡΠΌ Π·Π°ΡΡΠ½Π΅Ρ ΠΊΡΡΡΡ ΠΎΠ±ΡΠ°ΡΠ½ΡΠΌ ΠΏΠΎΠ΄ΡΠΎΡΠΎΠΌ, ΠΈ ΠΎΠ½Π° ΠΏΡΠΎΡΡΠΎ ΡΠ»ΠΎΠΆΠΈΡΡΡ Π² ΡΠ΅ΡΠ΅Π΄ΠΈΠ½Ρ ΡΠΈΠ»ΠΎΡΠ°. Π’Π°ΠΊ ΠΈ ΠΏΡΠΎΠΈΠ·ΠΎΡΠ»ΠΎ ΡΡΠ°Π·Ρ Ρ Π½Π΅ΡΠΊΠΎΠ»ΡΠΊΠΈΠΌΠΈ ΡΠΈΠ»ΠΎΡΠ°ΠΌΠΈ Π½Π° ΠΎΠ΄Π½ΠΎΠΌ ΡΠ»Π΅Π²Π°ΡΠΎΡΠ΅Β», β ΠΎΠ±ΡΡΡΠ½ΡΠ΅Ρ ΠΠ»Π΅ΠΊΡΠ°Π½Π΄Ρ ΠΠΎΠ»ΠΎΠ΄Π½ΠΎΠ².
ΠΠ΄Π½Π°ΠΊΠΎ ΡΠ°ΠΌΠΎΠΉ Π³Π»Π°Π²Π½ΠΎΠΉ ΠΏΡΠΎΠ±Π»Π΅ΠΌΠΎΠΉ ΡΠΊΡΠΏΠ΅ΡΡ ΡΡΠΈΡΠ°Π΅Ρ ΠΈΡΠΏΠΎΠ»ΡΠ·ΠΎΠ²Π°Π½ΠΈΠ΅ ΡΠΈΠ»ΠΎΡΠΎΠ² Π½Π΅ Π² ΡΠΎΠΌ ΡΠ΅ΠΆΠΈΠΌΠ΅, Π΄Π»Ρ ΠΊΠΎΡΠΎΡΠΎΠ³ΠΎ ΠΎΠ½ΠΈ ΠΏΡΠ΅Π΄Π½Π°Π·Π½Π°ΡΠ΅Π½Ρ.
Β«Π§ΡΠΎΠ±Ρ ΡΠΈΠ»ΠΎΡΡ Π±ΡΠ»ΠΈ Π½Π°Π΄Π΅ΠΆΠ½Ρ Π² ΡΠΊΡΠΏΠ»ΡΠ°ΡΠ°ΡΠΈΠΈ, ΠΎΠ½ΠΈ Π΄ΠΎΠ»ΠΆΠ½Ρ ΠΈΡΠΏΠΎΠ»ΡΠ·ΠΎΠ²Π°ΡΡΡΡ Π»ΠΈΠ±ΠΎ Π΄Π»Ρ Π΄Π»ΠΈΡΠ΅Π»ΡΠ½ΠΎΠ³ΠΎ Ρ ΡΠ°Π½Π΅Π½ΠΈΡ Π·Π΅ΡΠ½Π°, Π»ΠΈΠ±ΠΎ Π΄Π»Ρ Π²ΡΠ΅ΠΌΠ΅Π½Π½ΠΎΠ³ΠΎ. ΠΡΠΎΡ ΠΏΠΎΠΊΠ°Π·Π°ΡΠ΅Π»Ρ Π½Π΅ΠΎΠ±Ρ ΠΎΠ΄ΠΈΠΌΠΎ ΠΏΡΠΎΠΏΠΈΡΠ°ΡΡ Π² Π½ΠΎΡΠΌΠ°ΡΠΈΠ²Π½ΡΡ Π΄ΠΎΠΊΡΠΌΠ΅Π½ΡΠ°Ρ . ΠΠ΄Π½ΠΎ Π΄Π΅Π»ΠΎ, ΠΊΠΎΠ³Π΄Π° ΡΠΈΠ»ΠΎΡ Π² ΡΠ΅ΡΠ΅Π½ΠΈΠ΅ ΠΏΠΎΠ»ΡΠ³ΠΎΠ΄Π° ΠΎΠ΄ΠΈΠ½ ΡΠ°Π· Π·Π°Π³ΡΡΠ·ΠΈΠ»ΡΡ ΠΈ ΡΠ°Π·Π³ΡΡΠ·ΠΈΠ»ΡΡ, ΠΈ ΡΠΎΠ²ΡΠ΅ΠΌ Π΄ΡΡΠ³ΠΎΠ΅ β ΠΊΠΎΠ³Π΄Π° ΠΎΠ½ ΠΏΡΠΈ Π±ΠΎΠ»ΡΡΠΎΠΌ ΠΊΠΎΠ»ΠΈΡΠ΅ΡΡΠ²Π΅ ΡΠΈΠΊΠ»ΠΎΠ² Β«Π·Π°Π³ΡΡΠ·ΠΊΠ°-ΡΠ°Π·Π³ΡΡΠ·ΠΊΠ°Β» ΠΏΠΎΡΡΠΎΡΠ½Π½ΠΎ ΡΠ°ΡΡΡΠ³ΠΈΠ²Π°Π΅ΡΡΡ ΠΈ ΡΠΆΠΈΠΌΠ°Π΅ΡΡΡ. Π£ ΡΠΈΠ»ΠΎΡΠΎΠ², ΠΏΡΠ΅Π΄Π½Π°Π·Π½Π°ΡΠ΅Π½Π½ΡΡ Π΄Π»Ρ Π²ΡΠ΅ΠΌΠ΅Π½Π½ΠΎΠ³ΠΎ Ρ ΡΠ°Π½Π΅Π½ΠΈΡ, Π΄ΠΎΠ»ΠΆΠ½Ρ Π±ΡΡΡ Π±ΠΎΠ»Π΅Π΅ Π²ΡΡΠΎΠΊΠΈΠ΅ ΠΊΠ»Π°ΡΡ ΠΈ ΠΊΠ°ΡΠ΅Π³ΠΎΡΠΈΡ ΠΎΡΠ²Π΅ΡΡΡΠ²Π΅Π½Π½ΠΎΡΡΠΈ. ΠΡΠΎ Π·Π½Π°ΡΠΈΡ, ΡΡΠΎ ΠΏΡΠΈ ΡΠ°ΡΡΠ΅ΡΠ°Ρ Π½Π΅ΠΎΠ±Ρ ΠΎΠ΄ΠΈΠΌΠΎ ΠΏΡΠΈΠΌΠ΅Π½ΠΈΡΡ Π±ΠΎΠ»Π΅Π΅ Π²ΡΡΠΎΠΊΠΈΠΉ ΠΊΠΎΡΡΡΠΈΡΠΈΠ΅Π½Ρ ΠΎΡΠ²Π΅ΡΡΡΠ²Π΅Π½Π½ΠΎΡΡΠΈ β Π½Π΅ 0,95, Π°, ΠΊ ΠΏΡΠΈΠΌΠ΅ΡΡ, 1,25. Π’Π°ΠΊΠΎΠΉ ΡΠΈΠ»ΠΎΡ Π±ΡΠ΄Π΅Ρ Π΄ΠΎΡΠΎΠΆΠ΅, Π½ΠΎ ΠΈ ΠΊΠΎΠ½ΡΡΡΡΠΊΡΠΈΡ Π±ΡΠ΄Π΅Ρ ΡΡΠΎΡΡΡ Π΄ΠΎΠ»Π³ΠΎ, Π° ΡΠ°ΠΌΠΎΠ΅ Π³Π»Π°Π²Π½ΠΎΠ΅, Π½Π°Π΄Π΅ΠΆΠ½ΠΎΒ», β ΡΠ΅Π·ΡΠΌΠΈΡΡΠ΅Ρ ΠΠ»Π΅ΠΊΡΠ°Π½Π΄Ρ ΠΠΎΠ»ΠΎΠ΄Π½ΠΎΠ².
ΠΠ ΠΠ€ΠΠΠΠΠ’ΠΠΠ β ΠΠΠΠΠ ΠΠΠΠΠΠΠΠ’ΠΠ― Π‘ΠΠΠΠ‘Π
ΠΠ°ΠΆΠ΅ Π΅ΡΠ»ΠΈ Π½Π° ΡΠ»Π΅Π²Π°ΡΠΎΡΠ΅ Π½Π΅ ΡΠ΄Π°Π»ΠΎΡΡ ΠΈΠ·Π±Π΅ΠΆΠ°ΡΡ ΠΏΡΠΎΠ΅ΠΊΡΠ½ΡΡ , ΡΡΡΠΎΠΈΡΠ΅Π»ΡΠ½ΡΡ ΠΈΠ»ΠΈ ΠΌΠΎΠ½ΡΠ°ΠΆΠ½ΡΡ ΠΎΡΠΈΠ±ΠΎΠΊ, ΠΏΡΠ΅Π΄ΠΎΡΠ²ΡΠ°ΡΠΈΡΡ ΡΠ°Π·ΡΡΡΠ΅Π½ΠΈΠ΅ ΡΠΈΠ»ΠΎΡΠ° ΠΌΠΎΠΆΠ½ΠΎ Π±Π»Π°Π³ΠΎΠ΄Π°ΡΡ ΡΠ²ΠΎΠ΅Π²ΡΠ΅ΠΌΠ΅Π½Π½ΠΎΠΌΡ ΠΎΠ±Π½Π°ΡΡΠΆΠ΅Π½ΠΈΡ Π½Π΅ΠΏΠΎΠ»Π°Π΄ΠΎΠΊ. ΠΠ»Ρ ΡΡΠΎΠ³ΠΎ Π½Π΅ΠΎΠ±Ρ ΠΎΠ΄ΠΈΠΌΠΎ ΠΏΠΎΡΡΠΎΡΠ½Π½ΠΎ Π½Π°Π±Π»ΡΠ΄Π°ΡΡ, ΡΡΠΎ ΠΏΡΠΎΠΈΡΡ ΠΎΠ΄ΠΈΡ Π½Π° ΠΎΠ±ΡΠ΅ΠΊΡΠ΅.
Β«Π‘ΠΏΠ΅ΡΠΈΠ°Π»ΡΠ½Π°Ρ ΡΠ»ΡΠΆΠ±Π° Π΄ΠΎΠ»ΠΆΠ½Π° Π½Π°Π±Π»ΡΠ΄Π°ΡΡ Π·Π° ΡΠΎΡΡΠΎΡΠ½ΠΈΠ΅ΠΌ Π±ΠΎΠ»ΡΠΎΠ²ΡΡ ΡΠΎΠ΅Π΄ΠΈΠ½Π΅Π½ΠΈΠΉ. ΠΠ½ΠΈ Π²Π΅Π΄Ρ Π² Π»ΡΠ±ΠΎΠΌ ΡΠ»ΡΡΠ°Π΅ Π½ΠΈΠΊΡΠ΄Π° Π½Π΅ Π΄Π΅Π½ΡΡΡΡ, ΡΠΏΠ°Π΄ΡΡ Π½Π° Π·Π΅ΠΌΠ»Ρ. ΠΠΎΡΠ΅Π» ΠΎΡΡΡΡΠ΅Π» Π±ΠΎΠ»ΡΠΎΠ² β Π·Π½Π°ΡΠΈΡ, Π½Π°ΡΠ°Π»ΠΈΡΡ Π»ΠΎΠΊΠ°Π»ΡΠ½ΡΠ΅ ΠΏΡΠΎΡΠ΅ΡΡΡ ΡΠ°Π·ΡΡΡΠ΅Π½ΠΈΡ, ΠΊΠΎΡΠΎΡΡΠ΅ ΠΌΠΎΠ³ΡΡ ΠΏΡΠΈΠ²Π΅ΡΡΠΈ ΠΊ Π°Π²Π°ΡΠΈΠΈ Π²ΡΠ΅ΠΉ ΠΊΠΎΠ½ΡΡΡΡΠΊΡΠΈΠΈ. ΠΠ΅ΠΎΠ±Ρ ΠΎΠ΄ΠΈΠΌΠΎ ΡΠ΅Π³ΡΠ»ΡΡΠ½ΠΎ Π·Π°ΠΌΠ΅Π½ΡΡΡ ΡΡΠ΅Π·Π°Π½Π½ΡΠ΅ Π±ΠΎΠ»ΡΡ, Π²Π΅ΡΡΠΈ Π½Π°Π±Π»ΡΠ΄Π΅Π½ΠΈΡ Π·Π° ΠΊΠΎΠ½ΡΡΡΡΠΊΡΠΈΡΠΌΠΈ, ΡΠΈΠΊΡΠΈΡΠΎΠ²Π°ΡΡ ΠΏΠΎΡΠ²Π»Π΅Π½ΠΈΠ΅ ΠΈ ΡΠ°Π·Π²ΠΈΡΠΈΠ΅ Π΄Π΅ΡΠ΅ΠΊΡΠΎΠ² ΠΈ ΠΏΠΎΠ²ΡΠ΅ΠΆΠ΄Π΅Π½ΠΈΠΉΒ», β Π³ΠΎΠ²ΠΎΡΠΈΡ ΠΠ»Π΅ΠΊΡΠ°Π½Π΄Ρ ΠΠΎΠ»ΠΎΠ΄Π½ΠΎΠ².
ΠΠ½ ΡΠΎΠ²Π΅ΡΡΠ΅Ρ ΠΏΠΎΠ»ΡΠ·ΠΎΠ²Π°ΡΡΡΡ ΡΠΏΠ΅ΡΠΈΠ°Π»ΡΠ½ΡΠΌΠΈ ΠΏΡΠΈΠ±ΠΎΡΠ°ΠΌΠΈ, Ρ ΠΏΠΎΠΌΠΎΡΡΡ ΠΊΠΎΡΠΎΡΡΡ ΠΌΠΎΠΆΠ½ΠΎ Π²Π΅ΡΡΠΈ Π½Π°Π±Π»ΡΠ΄Π΅Π½ΠΈΡ Π·Π° Π½Π°ΠΏΡΡΠΆΠ΅Π½Π½ΠΎ-Π΄Π΅ΡΠΎΡΠΌΠΈΡΠΎΠ²Π°Π½Π½ΡΠΌ ΡΠΎΡΡΠΎΡΠ½ΠΈΠ΅ΠΌ ΠΊΠΎΠ½ΡΡΡΡΠΊΡΠΈΠΉ.
Β«ΠΠΎΠΆΠ½ΠΎ Π½Π°Π±Π»ΡΠ΄Π°ΡΡ Π·Π° ΡΡΠ½Π΄Π°ΠΌΠ΅Π½ΡΠ°ΠΌΠΈ ΠΈ ΠΊΠΎΠ½ΡΡΡΡΠΊΡΠΈΡΠΌΠΈ ΡΠΈΠ»ΠΎΡΠΎΠ², ΠΈΡΠΏΠΎΠ»ΡΠ·ΡΡ Π³Π΅ΠΎΠ΄Π΅Π·ΠΈΡΠ΅ΡΠΊΠΈΠ΅ ΠΌΠ΅ΡΠΎΠ΄Ρ. Π‘Π΅ΠΉΡΠ°Ρ ΠΌΠ½ΠΎΠ³ΠΎ Π³Π΅ΠΎΠ΄Π΅Π·ΠΈΡΠ΅ΡΠΊΠΈΡ ΠΏΡΠΈΠ±ΠΎΡΠΎΠ². ΠΡΡΡ ΠΈ ΡΠ°ΠΊΠΈΠ΅, ΠΊΠΎΡΠΎΡΡΠ΅ ΠΏΠΎΠ·Π²ΠΎΠ»ΡΡΡ Π²Π΅ΡΡΠΈ Π½Π°Π±Π»ΡΠ΄Π΅Π½ΠΈΡ Π² ΡΠ΅ΠΆΠΈΠΌΠ΅ ΡΠ΅Π°Π»ΡΠ½ΠΎΠ³ΠΎ Π²ΡΠ΅ΠΌΠ΅Π½ΠΈ Ρ Π²ΡΠ²ΠΎΠ΄ΠΎΠΌ ΠΈΠ½ΡΠΎΡΠΌΠ°ΡΠΈΠΈ Π½Π° ΠΊΠΎΠΌΠΏΡΡΡΠ΅Ρ. ΠΠ½ΠΈ ΠΌΠΎΠ³ΡΡ ΡΠΎΠΎΠ±ΡΠ°ΡΡ ΠΎΠ± ΠΎΡΠΊΠ»ΠΎΠ½Π΅Π½ΠΈΡΡ ΠΎΡ Π½ΠΎΡΠΌΡ, Π½Π°ΠΏΡΠΈΠΌΠ΅Ρ, Π΅ΡΠ»ΠΈ ΡΠΈΠ»ΠΎΡ Π½Π°ΡΠ°Π» ΡΠ°ΡΡΠΈΡΡΡΡΡΡ Π±ΠΎΠ»ΡΡΠ΅, ΡΠ΅ΠΌ Π½Π°Π΄ΠΎ. Π Π΄Π΅Π»ΠΎ ΡΠΏΠ΅ΡΠΈΠ°Π»ΠΈΡΡΠΎΠ² β ΠΏΡΠ°Π²ΠΈΠ»ΡΠ½ΠΎ ΠΎΡΠ΅Π½ΠΈΡΡ ΠΏΠΎΠ»ΡΡΠ΅Π½Π½ΡΡ ΠΈΠ½ΡΠΎΡΠΌΠ°ΡΠΈΡ ΠΈ ΡΠ΄Π΅Π»Π°ΡΡ ΡΠΎΠΎΡΠ²Π΅ΡΡΡΠ²ΡΡΡΠΈΠ΅ Π²ΡΠ²ΠΎΠ΄ΡΒ», β ΡΠ°ΡΡΠΊΠ°Π·ΡΠ²Π°Π΅Ρ ΠΠ»Π΅ΠΊΡΠ°Π½Π΄Ρ ΠΠΎΠ»ΠΎΠ΄Π½ΠΎΠ².
Π‘ΠΏΠ΅ΡΠΈΠ°Π»ΠΈΡΡΡ-ΡΠΊΡΠΏΠ»ΡΠ°ΡΠ°ΡΠΈΠΎΠ½Π½ΠΈΠΊΠΈ Π² ΡΠ²ΠΎΡ ΠΎΡΠ΅ΡΠ΅Π΄Ρ Π³ΠΎΠ²ΠΎΡΡΡ, ΡΡΠΎ ΠΈΠ·Π±Π΅ΠΆΠ°ΡΡ ΡΠ°Π·ΡΡΡΠ΅Π½ΠΈΡ ΡΠΈΠ»ΠΎΡΠ° ΠΏΠΎΠΌΠΎΠ³Π°Π΅Ρ ΡΠΈΡΡΠ΅ΠΌΠ° Π°Π²ΡΠΎΠΌΠ°ΡΠΈΠ·Π°ΡΠΈΠΈ.
Β«ΠΡΠ»ΠΈ ΡΠ΅ΡΡ ΠΈΠ΄Π΅Ρ ΠΎΠ± ΡΠ»Π΅Π²Π°ΡΠΎΡΠ΅, ΠΊΠΎΡΠΎΡΡΠΉ ΡΠΌΠΎΠ½ΡΠΈΡΠΎΠ²Π°Π½ ΠΈΠ· ΠΈΠΌΠΏΠΎΡΡΠ½ΠΎΠ³ΠΎ ΠΎΠ±ΠΎΡΡΠ΄ΠΎΠ²Π°Π½ΠΈΡ, ΡΠΎ Π±Π»Π°Π³ΠΎΠ΄Π°ΡΡ ΠΏΡΠ°ΠΊΡΠΈΡΠ΅ΡΠΊΠΈ ΠΏΠΎΠ»Π½ΠΎΠΉ Π°Π²ΡΠΎΠΌΠ°ΡΠΈΠ·Π°ΡΠΈΠΈ ΠΌΠΎΠΆΠ½ΠΎ ΠΌΠΈΠ½ΠΈΠΌΠΈΠ·ΠΈΡΠΎΠ²Π°ΡΡ ΠΈΠ»ΠΈ Π΄Π°ΠΆΠ΅ ΠΈΡΠΊΠ»ΡΡΠΈΡΡ Π²Π»ΠΈΡΠ½ΠΈΠ΅ Β«ΡΠ΅Π»ΠΎΠ²Π΅ΡΠ΅ΡΠΊΠΎΠ³ΠΎ ΡΠ°ΠΊΡΠΎΡΠ°Β», β Π³ΠΎΠ²ΠΎΡΠΈΡ ΠΊΠΎΠΌΠΌΠ΅ΡΡΠ΅ΡΠΊΠΈΠΉ Π΄ΠΈΡΠ΅ΠΊΡΠΎΡ Π³ΡΡΠΏΠΏΡ Β«Π ΠΠ‘Π’ΠΠ-Π₯ΠΠΠΠΠΠΒ» ΠΠΌΠΈΡΡΠΈΠΉ ΠΡΠΏΠ°Π²ΡΠ΅Π².
ΠΠ½Π½Π° ΠΠΎΡΠΎΠ±ΡΠ΅Π²Π°, Πlevatorist.com
elevatorist.com
ΠΡΠΎΠΈΠ·Π²ΠΎΠ΄ΡΡΠ²ΠΎ ΡΠΈΠ»ΠΎΡΠΎΠ² Π΄Π»Ρ ΡΡΠΏΡΡΠΈΡ ΠΌΠ°ΡΠ΅ΡΠΈΠ°Π»ΠΎΠ²
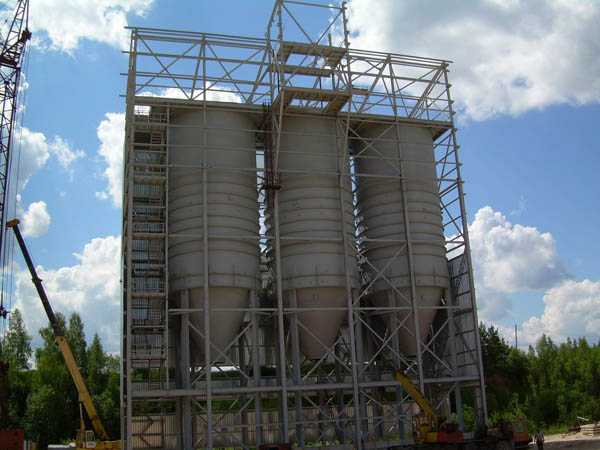
ΠΡΠΎΠΈΠ·Π²ΠΎΠ΄ΡΡΠ²ΠΎ ΡΠΈΠ»ΠΎΡΠΎΠ² β Π½Π΅ Π»Π΅Π³ΠΊΠΈΠΉ.., Π½ΠΎ Π±Π»Π°Π³ΠΎΠ΄Π°ΡΠ½ΡΠΉ ΡΡΡΠ΄!..
Π‘ ΠΊΠ°ΠΆΠ΄ΡΠΌ Π³ΠΎΠ΄ΠΎΠΌ ΡΠ°ΡΡΡΡ ΠΎΠ±ΡΠ΅ΠΌΡ Ρ
ΡΠ°Π½Π΅Π½ΠΈΡ ΡΠ΅ΠΌΠ΅Π½ΡΠ°, Π³ΠΈΠΏΡΠ°, Π΄ΡΡΠ³ΠΈΡ
ΡΡΡΠΎΠΈΡΠ΅Π»ΡΠ½ΡΡ
ΡΠΌΠ΅ΡΠ΅ΠΉ Π² Π ΠΎΡΡΠΈΠΈ ΠΈ ΡΡΡΠ°Π½Π°Ρ
Π‘ΠΠ.
Π‘ ΠΊΠ°ΠΆΠ΄ΡΠΌ Π³ΠΎΠ΄ΠΎΠΌ ΡΠ°ΡΡΠ΅Ρ ΠΈ ΠΏΠ°ΠΊΠ΅Ρ Π·Π°ΠΊΠ°Π·ΠΎΠ² Π½Π°ΡΠ΅Π³ΠΎ Π·Π°Π²ΠΎΠ΄Π° Π½Π° ΠΏΡΠΎΠΈΠ·Π²ΠΎΠ΄ΡΡΠ²ΠΎ ΡΠΈΠ»ΠΎΡΠΎΠ² ΠΈΠ· ΡΠ΅ΡΠ½ΠΎΠΉ ΡΡΠ°Π»ΠΈ.
ΠΡΠΎΠΈΠ·Π²ΠΎΠ΄ΡΡΠ²ΠΎ ΡΠΈΠ»ΠΎΡΠΎΠ² Π»ΡΠ±ΡΡ
ΠΎΠ±ΡΠ΅ΠΌΠΎΠ², ΡΠ»Π΅Π΄ΡΡΡΠΈΡ
ΡΠΈΠΏΠΎΠ²:
β ΡΠ΅Π»ΡΠ½ΠΎΡΠ²Π°ΡΠ½ΡΠ΅ ΠΌΠ΅ΡΠ°Π»Π»ΠΈΡΠ΅ΡΠΊΠΈΠ΅ ΡΠΈΠ»ΠΎΡΡ β ΠΎΡΠ»ΠΈΡΠ°ΡΡΡΡ ΡΠ΅ΠΌ ΡΡΠΎ ΠΎΠ½ΠΈ Π½Π° 100% Π³ΠΎΡΠΎΠ²Ρ ΠΊ Π²ΡΠΏΠΎΠ»Π½Π΅Π½ΠΈΡ Π·Π°Π΄Π°Ρ ΠΏΠΎ Ρ
ΡΠ°Π½Π΅Π½ΠΈΡ ΡΠ΅ΠΌΠ΅Π½ΡΠ° ΠΈ Π΄ΡΡΠ³ΠΈΡ
ΡΡΠΏΡΡΠΈΡ
Π²Π΅ΡΠ΅ΡΡΠ²; ΠΈΡ
Π½ΡΠΆΠ½ΠΎ ΡΠΎΠ»ΡΠΊΠΎ ΡΠ³ΡΡΠ·ΠΈΡΡ ΠΈ ΡΡΡΠ°Π½ΠΎΠ²ΠΈΡΡ Π½Π° ΡΡΠ½Π΄Π°ΠΌΠ΅Π½Ρ.
β ΠΌΠ΅ΡΠ°Π»Π»ΠΈΡΠ΅ΡΠΊΠΈΠ΅ ΡΠΈΠ»ΠΎΡΡ ΠΏΠΎΠ»ΠΈΡΡΠΎΠ²ΠΎΠΉ ΡΠ±ΠΎΡΠΊΠΈ; ΡΠ±ΠΎΡΠΊΠ° ΠΈ ΠΌΠΎΠ½ΡΠ°ΠΆ ΠΏΡΠΎΠΈΡΡ
ΠΎΠ΄ΠΈΡ ΠΏΠΎΡΡΠ΅Π΄ΡΡΠ²ΠΎΠΌ ΡΡΡΠ½ΠΎΠΉ Π΄ΡΠ³ΠΎΠ²ΠΎΠΉ (Π Π) ΠΈΠ»ΠΈ ΠΏΠΎΠ»ΡΠ°Π²ΡΠΎΠΌΠ°ΡΠΈΡΠ΅ΡΠΊΠΎΠΉ (ΠΠ) ΡΠ²Π°ΡΠΊΠΈ ΡΠ»Π΅ΠΌΠ΅Π½ΡΠΎΠ² ΡΠΈΠ»ΠΎΡΠ° ΠΏΡΡΠΌΠΎ Π½Π° ΠΌΠΎΠ½ΡΠ°ΠΆΠ½ΠΎΠΉ ΠΏΠ»ΠΎΡΠ°Π΄ΠΊΠ΅.
β ΠΌΠ΅ΡΠ°Π»Π»ΠΈΡΠ΅ΡΠΊΠΈΠ΅ ΡΠΈΠ»ΠΎΡΡ ΡΡΠ»ΠΎΠ½Π½ΠΎΠΉ ΡΠ±ΠΎΡΠΊΠΈ; ΡΠ±ΠΎΡΠΊΠ° ΠΈ ΠΌΠΎΠ½ΡΠ°ΠΆ ΠΏΡΠΎΠΈΡΡ
ΠΎΠ΄ΠΈΡ ΠΏΠΎΡΡΠ΅Π΄ΡΡΠ²ΠΎΠΌ ΡΡΡΠ½ΠΎΠΉ Π΄ΡΠ³ΠΎΠ²ΠΎΠΉ (Π Π) ΠΈΠ»ΠΈ ΠΏΠΎΠ»ΡΠ°Π²ΡΠΎΠΌΠ°ΡΠΈΡΠ΅ΡΠΊΠΎΠΉ (ΠΠ) ΡΠ²Π°ΡΠΊΠΈ ΡΡΠ»ΠΎΠ½Π½ΡΡ
ΡΠ»Π΅ΠΌΠ΅Π½ΡΠΎΠ² ΡΠΈΠ»ΠΎΡΠ° ΠΏΡΡΠΌΠΎ Π½Π° ΠΌΠΎΠ½ΡΠ°ΠΆΠ½ΠΎΠΉ ΠΏΠ»ΠΎΡΠ°Π΄ΠΊΠ΅.
β ΠΌΠ΅ΡΠ°Π»Π»ΠΈΡΠ΅ΡΠΊΠΈΠ΅ ΡΠΈΠ»ΠΎΡΡ ΡΠ±ΠΎΡΠ½ΡΠ΅ β ΡΠ°Π·Π±ΠΎΡΠ½ΡΠ΅, ΠΏΠΎΡΠ»Π΅ΠΌΠ΅Π½ΡΠ½ΠΎΠΉ ΡΠ±ΠΎΡΠΊΠΈ Β«Π½Π° Π±ΠΎΠ»ΡΠ°Ρ
Β»; ΡΠ±ΠΎΡΠΊΠ° ΠΈ ΠΌΠΎΠ½ΡΠ°ΠΆ ΠΏΡΠΎΠΈΡΡ
ΠΎΠ΄ΠΈΡ ΠΏΠΎΡΡΠ΅Π΄ΡΡΠ²ΠΎΠΌ ΡΠΎΠ΅Π΄ΠΈΠ½Π΅Π½ΠΈΡ ΡΠ»Π΅ΠΌΠ΅Π½ΡΠΎΠ² ΡΠΈΠ»ΠΎΡΠ° Π±ΠΎΠ»ΡΠ°ΠΌΠΈ ΠΏΡΡΠΌΠΎ Π½Π° ΠΌΠΎΠ½ΡΠ°ΠΆΠ½ΠΎΠΉ ΠΏΠ»ΠΎΡΠ°Π΄ΠΊΠ΅.
Π‘ΠΈΠ»ΠΎΡΡ ΠΈ Π±ΡΠ½ΠΊΠ΅ΡΡ Π΄Π»Ρ ΡΠ΅ΠΌΠ΅Π½ΡΠ° ΠΈ Π΄ΡΡΠ³ΠΈΡ
ΡΡΠΏΡΡΠΈΡ
ΠΌΠ°ΡΠ΅ΡΠΈΠ°Π»ΠΎΠ² ΠΈΠ· ΡΠ΅ΡΠ½ΠΎΠΉ ΠΈ Π½Π΅ΡΠΆΠ°Π²Π΅ΡΡΠ΅ΠΉ ΡΡΠ°Π»ΠΈ β ΡΡΠΎ ΠΎΡΠ½ΠΎΠ²Π½ΠΎΠ΅ Π½Π°ΠΏΡΠ°Π²Π»Π΅Π½ΠΈΠ΅ ΠΏΡΠΎΠΈΠ·Π²ΠΎΠ΄ΡΡΠ²Π΅Π½Π½ΠΎΠΉ Π΄Π΅ΡΡΠ΅Π»ΡΠ½ΠΎΡΡΠΈ Π½Π°ΡΠ΅Π³ΠΎ Π·Π°Π²ΠΎΠ΄Π°!
ΠΡΠΏΠΎΠ»Π½ΡΠ΅ΠΌ ΠΏΡΠΎΠΈΠ·Π²ΠΎΠ΄ΡΡΠ²ΠΎ ΡΠΈΠ»ΠΎΡΠΎΠ² Π΄Π»Ρ ΡΠ΅ΠΌΠ΅Π½ΡΠ°, Π±ΡΠ½ΠΊΠ΅ΡΠΎΠ² Π΄Π»Ρ ΡΠ΅ΠΌΠ΅Π½ΡΠ°, Π·Π΅ΡΠ½Π°, ΡΡΡ
ΠΎΠ³ΠΎ ΠΈ ΠΌΠΎΠΊΡΠΎΠ³ΠΎ ΠΏΠ΅ΡΠΊΠ°, ΠΊΠ²Π°ΡΡΠ°, ΠΌΠ΅Π»Π°, Π³ΠΈΠΏΡΠΎΠ²ΠΎΠ³ΠΎ ΠΏΠΎΡΠΎΡΠΊΠ° ΠΈ Π΄ΡΡΠ³ΠΈΡ
ΡΡΡ
ΠΈΡ
Π²Π΅ΡΠ΅ΡΡΠ² ΠΎΠ±ΡΠ΅ΠΌΠΎΠΌ 5, 10, 15, 20, 25, 30, 35, 40, 45, 50, 60, 70, 80, 90, 100, 130, 150, 200, 250, 300, 350, 400, 500, 1000 ΡΠΎΠ½Π½ ΠΈ Π±ΠΎΠ»Π΅Π΅.
Π‘ΠΈΠ»ΠΎΡ ΡΠ΅ΠΌΠ΅Π½ΡΠ° ΡΡΠΎ ΠΌΠ΅ΡΠ°Π»Π»ΠΈΡΠ΅ΡΠΊΠ°Ρ ΡΠΌΠΊΠΎΡΡΡ Π² Π²ΠΈΠ΄Π΅ ΡΠΈΠ»ΠΈΠ½Π΄ΡΠ° (Π±ΠΎΡΠΊΠΈ), Π² ΠΊΠΎΡΠΎΡΠΎΠΉ Ρ ΡΠ°Π½ΡΡΡΡ ΡΡΠΏΡΡΠΈΠ΅ Π²Π΅ΡΠ΅ΡΡΠ²Π°, Π² ΡΠΎΠΌ ΡΠΈΡΠ»Π΅ ΡΠ΅ΠΌΠ΅Π½Ρ, ΠΈΠ·Π²Π΅ΡΡΡ, ΠΏΠ΅ΡΠΎΠΊ, Π·Π΅ΡΠ½ΠΎ ΠΈ Ρ.ΠΏ.
ΠΠΎΠ½ΡΠ°ΠΆ ΡΠΈΠ»ΠΎΡΠ° ΠΏΡΠΎΠΈΠ·Π²ΠΎΠ΄ΠΈΡΡΡ Π²Π΅ΡΡΠΈΠΊΠ°Π»ΡΠ½ΠΎ Π½Π° ΠΎΠΏΠΎΡΠ°Ρ ΠΈΠ·Π³ΠΎΡΠΎΠ²Π»Π΅Π½Π½ΡΡ ΠΈΠ· ΡΡΡΠ± ΠΈΠ»ΠΈ ΡΠ²Π΅Π»Π»Π΅ΡΠ° (ΠΌΠ΅ΡΠ°Π»Π»ΠΎΠΏΡΠΎΠΊΠ°Ρ).
Π‘ΠΈΠ»ΠΎΡ ΡΠ΅ΠΌΠ΅Π½ΡΠ° ΠΊΠ°ΠΊ ΠΈ Π»ΡΠ±ΠΎΠΉ Π΄ΡΡΠ³ΠΎ ΡΠΈΠ»ΠΎΡ Π·Π°ΠΊΠ°Π½ΡΠΈΠ²Π°Π΅ΡΡΡ ΠΊΠΎΠ½ΡΡΠΎΠΌ, Π½Π° ΠΊΠΎΠ½ΡΠ΅ ΠΊΠΎΡΠΎΡΠΎΠ³ΠΎ ΡΡΡΠ°Π½ΠΎΠ²Π»Π΅Π½ ΡΠΈΠ±Π΅ΡΠ½ΡΠΉ Π·Π°ΡΠ²ΠΎΡ. Π‘ ΠΏΠΎΠΌΠΎΡΡΡ Π³Π΅ΠΎΠΌΠ΅ΡΡΠΈΠΈ ΠΊΠΎΠ½ΡΡΠ°, ΡΠ΅ΠΌΠ΅Π½Ρ Π² ΡΠΈΠ»ΠΎΡΠ΅ ΡΠ°ΠΌΠΎΡΠ΅ΠΊΠΎΠΌ ΠΏΠΎΡΡΡΠΏΠ°Π΅Ρ Π² ΡΠΈΠ±Π΅ΡΠ½ΡΠΉ Π·Π°ΡΠ²ΠΎΡ, Π° ΠΎΡΡΡΠ΄Π° ΠΏΠΎΠΏΠ°Π΄Π°Π΅Ρ Π΄Π»Ρ Π΄Π°Π»ΡΠ½Π΅ΠΉΡΠ΅ΠΉ ΡΠ°Π·Π΄Π°ΡΠΈ Π² ΡΠ½Π΅ΠΊ ΠΈΠ»ΠΈ Π² ΡΠ΅ΠΌΠ΅Π½ΡΠ½ΡΠΉ Π½Π°ΡΠΎΡ.
Π‘ΠΊΠ»Π°Π΄ ΡΠ΅ΠΌΠ΅Π½ΡΠ° (ΡΠΈΠ»ΠΎΡΠ½ΡΠΉ ΡΠΊΠ»Π°Π΄) β ΡΡΠΎ ΡΠΈΡΡΠ΅ΠΌΠ° ΠΎΠ±ΠΎΡΡΠ΄ΠΎΠ²Π°Π½ΠΈΡ, ΠΏΡΠ΅Π΄Π½Π°Π·Π½Π°ΡΠ΅Π½Π½Π°Ρ Π΄Π»Ρ Π·Π°Π³ΡΡΠ·ΠΊΠΈ ΡΠΈΠ»ΠΎΡΠΎΠ² ΡΠ΅ΠΌΠ΅Π½ΡΠΎΠΌ Ρ ΡΡΠ°Π½ΡΠΏΠΎΡΡΠ½ΡΡ ΡΡΠ΅Π΄ΡΡΠ², Ρ ΡΠ°Π½Π΅Π½ΠΈΡ ΡΠ΅ΠΌΠ΅Π½ΡΠ° Π² ΡΠΈΠ»ΠΎΡΠ°Ρ , Π° ΡΠ°ΠΊΠΆΠ΅ Π²ΡΠ³ΡΡΠ·ΠΊΠΈ ΡΠ΅ΠΌΠ΅Π½ΡΠ° Π΄Π»Ρ Π΅Π³ΠΎ Π΄Π°Π»ΡΠ½Π΅ΠΉΡΠ΅Π³ΠΎ ΠΏΠΎΡΡΠ΅Π±Π»Π΅Π½ΠΈΡ ΡΠ°ΠΊΠΈΠΌΠΈ ΠΏΡΠ΅Π΄ΠΏΡΠΈΡΡΠΈΡΠΌΠΈ ΠΊΠ°ΠΊ ΠΠ‘Π£ (Π±Π΅ΡΠΎΠ½Π½ΠΎ-ΡΠΌΠ΅ΡΠΈΡΠ΅Π»ΡΠ½ΡΠΉ ΡΠ·Π΅Π»), ΠΠΠ (Π°ΡΡΠ°Π»ΡΡΠΎΠ±Π΅ΡΠΎΠ½Π½ΡΠΉ Π·Π°Π²ΠΎΠ΄) ΠΈ Π΄ΡΡΠ³ΠΈΠΌΠΈ Π±Π΅ΡΠΎΠ½Π½ΡΠΌΠΈ Π·Π°Π²ΠΎΠ΄Π°ΠΌΠΈ.
Π‘ΠΊΠ»Π°Π΄ ΡΠ΅ΠΌΠ΅Π½ΡΠ° (ΡΠΈΠ»ΠΎΡΠ½ΡΠΉ ΡΠΊΠ»Π°Π΄) Π²ΠΊΠ»ΡΡΠ°Π΅Ρ Π² ΡΠ΅Π±Ρ ΠΎΠ΄ΠΈΠ½ Π½Π΅ΡΠΊΠΎΠ»ΡΠΊΠΎ ΡΠΈΠ»ΠΎΡΠΎΠ², ΠΎΠ±ΠΎΡΡΠ΄ΠΎΠ²Π°Π½ΠΈΠ΅ Π΄Π»Ρ Π·Π°Π³ΡΡΠ·ΠΊΠΈ ΡΠ΅ΠΌΠ΅Π½ΡΠ°, ΡΠ΅ΠΌΠ΅Π½ΡΠΎΠΏΡΠΎΠ²ΠΎΠ΄, ΠΈ ΠΎΠ±ΠΎΡΡΠ΄ΠΎΠ²Π°Π½ΠΈΠ΅ Π΄Π»Ρ Π²ΡΠ³ΡΡΠ·ΠΊΠΈ ΡΠ΅ΠΌΠ΅Π½ΡΠ°. ΠΠ±ΠΎΡΡΠ΄ΠΎΠ²Π°Π½ΠΈΠ΅ Π΄Π»Ρ Π·Π°Π³ΡΡΠ·ΠΊΠΈ ΡΠΈΠ»ΠΎΡΠΎΠ² Π²ΠΊΠ»ΡΡΠ°Π΅Ρ Π² ΡΠ΅Π±Ρ ΠΎΠ±ΠΎΡΡΠ΄ΠΎΠ²Π°Π½ΠΈΠ΅ Π΄Π»Ρ ΡΠ°Π·Π³ΡΡΠ·ΠΊΠΈ ΠΆΠ΅Π»Π΅Π·Π½ΠΎΠ΄ΠΎΡΠΎΠΆΠ½ΡΡ
Ρ
ΠΎΠΏΡΠΎΠ², ΡΡΡΠ°Π½ΠΎΠ²ΠΊΠ° Π΄Π»Ρ ΡΠ°ΡΡΠ°ΡΠΊΠΈ ΠΊΠΎΠ½ΡΠ΅ΠΉΠ½Π΅ΡΠΎΠ² Β«Π±ΠΈΠ³-Π±Π΅Π³ΠΎΠ²Β».
ΠΠ°Ρ Π·Π°Π²ΠΎΠ΄ ΡΠ°ΠΊΠΆΠ΅ ΠΏΡΠΎΠΈΠ·Π²ΠΎΠ΄ΠΈΡ ΠΎΠ±ΠΎΡΡΠ΄ΠΎΠ²Π°Π½ΠΈΠ΅ Π΄Π»Ρ ΡΠ°Π·Π³ΡΡΠ·ΠΊΠΈ Π΄Π»Ρ ΡΠ°Π·Π³ΡΡΠ·ΠΊΠΈ ΠΆΠ΅Π»Π΅Π·Π½ΠΎΠ΄ΠΎΡΠΎΠΆΠ½Ρ Ρ
ΠΎΠΏΡΠΎΠ², ΡΡΡΠ°Π½ΠΎΠ²ΠΊΠΈ ΡΠ°ΡΡΠ°ΡΠΊΠΈ ΠΊΠΎΠ½ΡΠ΅ΠΉΠ½Π΅ΡΠΎΠ² Β«Π±ΠΈΠ³-Π±Π΅Π³ΠΎΠ²Β», Π²ΠΈΠ½ΡΠΎΠ²ΡΠ΅ ΡΠ΅ΠΌΠ΅Π½ΡΠ½ΡΡ
Π½Π°ΡΠΎΡΡ, ΠΊΠ°ΠΌΠ΅ΡΠ½ΡΠ΅ ΡΠ΅ΠΌΠ΅Π½ΡΠ½ΡΠ΅ Π½Π°ΡΠΎΡΡ.
Π‘ΠΈΠ»ΠΎΡΡ ΡΠ΅ΠΌΠ΅Π½ΡΠ° ΠΏΡΠ΅Π΄Π½Π°Π·Π½Π°ΡΠ΅Π½Ρ Π΄Π»Ρ Ρ ΡΠ°Π½Π΅Π½ΠΈΡ ΡΠ°Π·Π»ΠΈΡΠ½ΡΡ ΡΡΠΏΡΡΠΈΡ Π²Π΅ΡΠ΅ΡΡΠ², Π² ΡΠΎΠΌ ΡΠΈΡΠ»Π΅ ΡΠ΅ΠΌΠ΅Π½ΡΠ°, ΠΏΠ΅ΡΠΊΠ°, ΠΈΠ·Π²Π΅ΡΡΠΈ, Π·Π΅ΡΠ½Π° ΠΈ.ΠΏ. Π‘ΠΈΠ»ΠΎΡΠ° Π²ΡΠΏΠΎΠ»Π½ΡΡΡ ΡΡΠ½ΠΊΡΠΈΠΈ Ρ ΡΠ°Π½Π΅Π½ΠΈΡ ΠΈ ΠΏΠΎΠ΄Π°ΡΠΈ ΡΠ΅ΠΌΠ΅Π½ΡΠ° Π² Π²Π΅ΡΠΎΠ²ΠΎΠΉ Π΄ΠΎΠ·Π°ΡΠΎΡ Π±Π΅ΡΠΎΠ½Π½ΠΎΠ³ΠΎ Π·Π°Π²ΠΎΠ΄Π°, Π±Π΅ΡΠΎΠ½ΠΎΡΠΌΠ΅ΡΠΈΡΠ΅Π»ΡΠ½ΠΎΠΉ ΡΡΡΠ°Π½ΠΎΠ²ΠΊΠΈ (ΠΠ‘Π£), ΡΠ΅ΠΌΠ΅Π½ΡΠΎΠ²ΠΎΠ·Π° ΠΈ Ρ.ΠΏ.
Π¦Π΅ΠΌΠ΅Π½Ρ ΠΏΡΠΎΠΈΠ·Π²Π΅Π΄Π΅Π½Π½ΡΠΉ Π² ΠΏΠΎΠΌΠΎΠ»ΡΠ½ΠΎΠΌ ΠΎΡΠ΄Π΅Π»Π΅Π½ΠΈΠΈ, ΡΡΠ°Π½ΡΠΏΠΎΡΡΠΈΡΡΒΠ΅ΡΡΡ ΡΠΈΡΡΠ΅ΠΌΠΎΠΉ ΠΏΠ½Π΅Π²ΠΌΠΎΡΡΠ°Π½ΡΠΏΠΎΡΡΠ° Π² ΡΠ΅ΠΌΠ΅Π½ΡΠ½ΡΠ΅ ΡΠΈΠ»ΠΎΒΡΡ Π΄Π»Ρ Ρ ΡΠ°Π½Π΅Π½ΠΈΡ.
ΠΠΎΠ»ΠΈΡΠ΅ΡΡΠ²ΠΎ Π΅ΠΌΠΊΠΎΡΡΠ΅ΠΉ (ΡΠΈΠ»ΠΎΡΠ½ΡΡ Π±Π°Π½ΠΎΠΊ) Π΄Π»Ρ Ρ ΡΠ°Π½Π΅Π½ΠΈΡ ΡΠ΅ΠΌΠ΅Π½ΡΠ° ΠΎΠΏΡΠ΅Π΄Π΅Π»ΡΠ΅ΡΡΡ Π°ΡΡΠΎΡΡΠΈΠΌΠ΅Π½ΡΠΎΠΌ ΠΈ ΡΡΡΠΎΡΠ½ΠΎΠΉ Π²ΡΡΠ°Π±ΠΎΡΠΊΠΎΠΉ ΡΡΠΏΡΡΠΈΡ ΠΌΠ΅ΡΠ°ΡΠΈΠ°Π»ΠΎΠ².
ΠΠ»Ρ Ρ ΡΠ°Π½Π΅Π½ΠΈΡ ΡΠ΅ΠΌΠ΅Π½ΡΠ° ΠΎΠ±ΡΡΠ½ΠΎ ΠΈΡΠΏΠΎΠ»ΡΠ·ΡΡΡ Π²Π΅ΡΡΠΈΠΊΠ°Π»ΡΠ½ΡΠ΅ ΡΠΈΠ»ΠΈΠ½Π΄ΡΠΈΡΠ΅ΡΠΊΠΈΠ΅ ΡΠΈΠ»ΠΎΡΡ ΠΈΠ»ΠΈ Π±ΡΠ½ΠΊΠ΅ΡΡ.
Π‘ΠΈΠ»ΠΎΡΡ ΠΈ Π±ΡΠ½ΠΊΠ΅ΡΡ ΠΎΠ±Π΅ΡΠΏΠ΅ΡΠΈΠ²Π°ΡΡ Ρ ΠΎΡΠΎΡΠΈΠ΅ ΡΡΠ»ΠΎΠ²ΠΈΡ Π΄Π»Ρ Ρ ΡΠ°Π½Π΅Π½ΠΈΡ ΠΈ ΡΠ°Π·Π³ΡΡΠ·ΠΊΠΈ ΡΠ΅ΠΌΠ΅Π½ΡΠ°. Π Π°Π·ΡΡΡΠ΅Π½ΠΈΠ΅ ΡΠ²ΠΎΠ΄Π° ΡΠΎΠΏΡΠΎΠ²ΠΎΠΆΠ΄Π°Π΅ΡΡΡ ΠΏΠ°Π΄Π΅Π½ΠΈΠ΅ΠΌ Π±ΠΎΠ»ΡΡΠΈΡ ΠΌΠ°ΡΡ ΠΌΠ°ΡΠ΅ΡΠΈΠ°Π»Π° ΠΈ ΠΌΠΎΠΆΠ΅Ρ Π²ΡΠ·Π²Π°ΡΡ ΡΠ°Π·ΡΡΡΠ΅Π½ΠΈΠ΅ ΡΠΈΠ»ΠΎΡΠ°.
Π£Π΄Π΅Π»ΡΠ½Π°Ρ ΡΡΠΎΠΈΠΌΠΎΡΡΡ ΡΠΈΠ»ΠΎΡΠ½ΠΎΠΉ ΡΡΠ»ΠΎΠ½Π½ΠΎΠΉ ΠΈΠ»ΠΈ ΠΏΠΎΠ»ΠΈΡΡΠΎΠ²ΠΎΠΉ ΠΊΠΎΠ½ΡΡΡΡΠΊΡΠΈΠΈ ΡΠ½ΠΈΠΆΠ°Π΅ΡΡΡ Ρ ΡΠ²Π΅Π»ΠΈΡΠ΅Π½ΠΈΠ΅ΠΌ Π²ΠΎΠ±ΡΠ΅ΠΌΠ° ΡΠΈΠ»ΠΎΡΠ°, ΠΏΠΎΡΡΠΎΠΌΡ ΡΡΡΠΎΠΈΡΠ΅Π»ΡΡΡΠ²ΠΎ Π½Π΅Π±ΠΎΠ»ΡΡΠΎΠ³ΠΎ ΠΊΠΎΠ»ΠΈΡΠ΅ΡΡΠ²Π° ΠΊΡΡΠΏΠ½ΡΡ ΡΠ΅ΠΌΠ΅Π½ΡΠ½ΡΡ ΡΠΈΠ»ΠΎΡΠΎΠ² Π±ΠΎΠ»Π΅Π΅ Π²ΡΠ³ΠΎΠ΄Π½ΠΎ, ΡΠ΅ΠΌ ΠΈΡΠΏΠΎΠ»ΡΠ·ΠΎΠ²Π°Π½ΠΈΠ΅ Π±ΠΎΠ»ΡΡΠ΅Π³ΠΎ ΡΠΈΡΠ»Π° ΠΌΠ°Π»Π΅Π½ΡΠΊΠΈΡ ΡΠΈΠ»ΠΎΡΠΎΠ².
ΠΠΌΠ΅ΡΡΠΈΠΌΠΎΡΡΡ ΠΎΡΠ΄Π΅Π»ΡΠ½ΡΡ ΡΠΈΠ»ΠΎΡΠΎΠ² Π΄Π»Ρ ΡΠ΅ΠΌΠ΅Π½ΡΠ° Π΄ΠΎΡΡΠΈΠ³Π°Π΅Ρ ΠΈ 1000 ΠΈ 2000 ΠΈ Π΄Π°ΠΆΠ΅ 30000 ΡΠΎΠ½Π½, ΠΏΡΠΈ ΡΡΠΎΠΌ ΠΈΡ Π΄ΠΈΠ°ΠΌΠ΅ΡΡ Π΄ΠΎΡΡΠΈΠ³Π°Π΅Ρ 28 ΠΌ, Π° Π²ΡΡΠΎΡΠ° Π΄ΠΎΡ ΠΎΠ΄ΠΈΡ Π΄ΠΎ 55 ΠΌ. ΠΠ°ΡΡΠ° ΡΠ΅ΠΌΠ΅Π½ΡΠ°, Π½Π°Ρ ΠΎΠ΄ΡΡΠ΅Π³ΠΎΡΡ Π² ΡΠΈΠ»ΠΎΡΠ΅, Π·Π°Π²ΠΈΡΠΈΡ ΠΎΡ ΡΡΠ΅ΠΏΠ΅Π½ΠΈ Π΅Π³ΠΎ ΡΠΏΠ»ΠΎΡΠ½Π΅Π½ΠΈΡ ΠΈ Π²ΠΈΠ΄Π° ΡΠ΅ΠΌΠ΅Π½ΡΠ°. Π ΡΠΏΠ»ΠΎΡΠ½Π΅Π½Π½ΠΎΠΌ ΡΠΎΡΡΠΎΒΡΠ½ΠΈΠΈ ΠΏΠ»ΠΎΡΠ½ΠΎΡΡΡ ΡΠΈΠ»ΠΎΡΠ° Π΄ΠΎΡΡΠΈΠ³Π°Π΅Ρ 1,3 Π΄ΠΎ 1,5 Ρ/ΠΌ3. ΠΠ»Ρ ΡΠ°ΡΡΠ΅ΡΠ° ΡΠΈΠ»ΠΎΡΠ½ΡΡ ΠΊΠΎΠ½ΡΡΡΡΠΊΡΠΈΠΉ ΠΏΠ»ΠΎΡΠ½ΠΎΡΡΡ ΠΏΡΠΈΠ½ΠΈΠΌΠ°Π΅ΡΡΡ ΡΠ°Π²Π½ΠΎΠΉ 1,6 Ρ/ΠΌ3, Π° ΠΏΡΠΈ ΠΎΠΏΡΠ΅Π΄Π΅Π»Π΅Π½ΠΈΠΈ ΠΎΠ±ΡΠ΅ΠΌΠ° ΡΠΈΠ»ΠΎΡΠΎΠ² β 1,4 Ρ/ΠΌ3.
ΠΠ°ΠΊ ΠΏΡΠ°Π²ΠΈΠ»ΠΎ, Π½Π° ΡΠ΅ΠΌΠ΅Π½ΡΠ½ΡΡ Π·Π°Π²ΠΎΠ΄Π°Ρ Π ΠΎΡΡΠΈΠΈ ΠΈΡΠΏΠΎΠ»ΡΠ·ΡΡΡ ΡΠΈΒΠ»ΠΎΡΡ Π΄ΠΈΠ°ΠΌΠ΅ΡΡΠΎΠΌ 2, 3, 6, 12 ΠΈ 18 ΠΌΠ΅ΡΡΠΎΠ². ΠΠΎΡΠΌΠ°ΠΌΠΈ ΡΠ΅Ρ Π½ΠΎΠ»ΠΎΠ³ΠΈΡΠ΅ΡΠΊΠΎΠ³ΠΎ ΠΏΡΠΎΠ΅ΠΊΡΠΈΡΠΎΠ²Π°Π½ΠΈΡ ΠΏΡΠ΅Π΄ΡΡΠΌΠ°ΡΡΠΈΠ²Π°Π΅ΡΡΡ ΠΎΠ±ΡΠ΅ΠΌ Π·Π°ΠΏΠ°ΡΠ° Ρ ΡΠ°Π½ΠΈΠΌΠΎΠ³ΠΎ ΡΠ΅ΒΠΌΠ΅Π½ΡΠ° ΠΎΡ 10 Π΄ΠΎ 20 ΡΡΡΠΎΠΊ, Π² Π·Π°Π²ΠΈΡΠΈΠΌΠΎΡΡΠΈ ΠΎΡ ΠΎΠ±ΡΠ΅Π³ΠΎ ΠΎΠ±ΡΠ΅ΠΌΠ° Π²ΡΠΏΡΡΠΊΠ° ΡΠ΅ΠΌΠ΅Π½ΡΠ°.
ΠΡΠΎΠΈΠ·Π²ΠΎΠ΄ΡΡΠ²ΠΎ ΡΠΊΠ»Π°Π΄ΠΎΠ² ΡΠ΅ΠΌΠ΅Π½ΡΠ° ΠΎΡΡΡΠ΅ΡΡΠ²Π»ΡΠ΅ΡΡΡ Ρ ΡΡΠ΅ΡΠΎΠΌ ΡΠΎΠ³ΠΎ, ΡΡΠΎ ΡΠΈΠ»ΠΎΡΡ Π΄ΠΈΠ°ΠΌΠ΅ΡΒΡΠΎΠΌ 12 ΠΌ ΠΈ ΠΌΠ΅Π½Π΅Π΅ ΡΠ°ΡΠΏΠΎΠ»Π°Π³Π°ΡΡΡΡ Π² Π΄Π²Π° ΡΡΠ΄Π°, Π° Π΄ΠΈΠ°ΠΌΠ΅ΡΡΠΎΠΌ Π±ΠΎΠ»Π΅Π΅ 12ΠΌ β Π² ΠΎΠ΄ΠΈΠ½ ΡΡΠ΄. ΠΠ°Π΄ ΡΠΈΠ»ΠΎΡΠ°ΠΌΠΈ ΠΏΡΠ΅Π΄ΡΡΠΌΠ°ΡΡΠΈΠ²Π°Π΅ΡΡΡ Π³Π°Π»Π΅ΡΠ΅Ρ, Π² ΠΊΠΎΡΠΎΡΠΎΠΉ ΡΠ°Π·ΠΌΠ΅ΡΠ°ΡΡΡΡ ΡΡΡΠ±ΠΎΠΏΡΠΎΠ²ΠΎΠ΄Ρ, ΡΠΈΠ»ΡΡΡΡ, ΠΏΠ΅ΡΠ΅ΠΊΠ»ΡΡΠ°ΡΠ΅Π»ΠΈ ΠΈ Ρ.Π΄.
Π‘ΠΈΠ»ΠΎΡΠ½ΡΠ΅ Π΅ΠΌΠΊΠΎΡΡΠΈ ΡΡΡΠ°Π½Π°Π²Π»ΠΈΠ²Π°ΡΡΡΡ Π½Π° ΠΌΠ΅ΡΠ°Π»Π»ΠΈΡΠ΅ΡΠΊΠΈΡ ΠΎΠΏΠΎΡΠ°Ρ (ΠΊΠΎΠ»ΠΎΠ½Π½Π°Ρ ) ΡΠ°ΠΊΠΈΠΌ ΠΎΠ±ΡΠ°Π·ΠΎΠΌ, ΡΡΠΎΠ±Ρ ΠΎΠ±Π΅ΡΠΏΠ΅ΡΠΈΡΡ ΠΏΡΠΎΠΏΡΡΠΊ ΠΆΠ΅Π»Π΅Π·Π½ΠΎΠ΄ΠΎΡΠΎΠΆΠ½ΡΡ ΡΠΎΒΡΡΠ°Π²ΠΎΠ² Π΄Π»Ρ Π·Π°Π³ΡΡΠ·ΠΊΠΈ Π²Π°Π³ΠΎΠ½ΠΎΠ² ΡΠ΅ΠΌΠ΅Π½ΡΠΎΠΌ ΠΈΠ· ΡΠΈΠ»ΠΎΡΠΎΠ² ΡΠ°ΠΌΠΎΡΠ΅ΠΊΠΎΠΌ (ΡΠ΅Π½ΡΡΠ°Π»ΡΠ½Π°Ρ ΡΠ°Π·Π³ΡΡΠ·ΠΊΠ°).
ΠΠ»Ρ Π·Π°Π³ΡΡΠ·ΠΊΠΈ ΠΆΠ΅Π»Π΅Π·Π½ΠΎΠ΄ΠΎΡΠΎΠΆΠ½ΡΡ ΡΠΎΡΡΠ°Π²ΠΎΠ² ΠΏΠΎΠ΄ ΠΊΠ°ΠΆΠ΄ΡΠΌ ΡΡΠ΄ΠΎΠΌ ΡΠΈΠ»ΠΎΡΠΎΠ² Π΄ΠΈΠ°ΠΌΠ΅ΡΡΠΎΠΌ 12 ΠΌ, ΡΡΡΠ°Π½ΠΎΠ²Π»Π΅Π½Π½ΡΡ Π½Π° ΠΌΠ΅ΡΠ°Π»Π»ΠΈΡΠ΅ΡΠΊΠΈΡ ΠΎΠΏΠΎΡΠ°Ρ , ΡΠΊΠ»Π°Π΄ΡΠ²Π°ΒΠ΅ΡΡΡ ΠΏΠΎ ΠΎΠ΄Π½ΠΎΠΌΡ ΠΆΠ΅Π»Π΅Π·Π½ΠΎΠ΄ΠΎΡΠΎΠΆΠ½ΠΎΠΌΡ ΠΏΡΡΠΈ ΠΈ ΠΏΠΎΠ΄ ΠΊΠ°ΠΆΠ΄ΡΠΌ ΡΠΈΠ»ΠΎΡΠΎΠΌ ΠΏΡΠ΅Π΄ΡΡΠΌΠ°ΡΡΠΈΠ²Π°Π΅ΡΡΡ ΡΡΡΠ°Π½ΠΎΠ²ΠΊΠ° ΠΎΠ΄Π½ΠΈΡ ΠΆΠ΅Π»Π΅Π·Π½ΠΎΠ΄ΠΎΡΠΎΠΆΠ½ΡΡ Π²Π΅ΡΠΎΠ² Π³ΡΡΒΠ·ΠΎΠΏΠΎΠ΄ΡΠ΅ΠΌΠ½ΠΎΡΡΡΡ 150 ΡΠΎΠ½Π½. ΠΠΎΠ΄ ΡΠΈΠ»ΠΎΡΠ°ΠΌΠΈ Π΄ΠΈΠ°ΠΌΠ΅ΡΡΠΎΠΌ 18 ΠΌ ΠΏΡΠ΅Π΄ΡΡΠΌΠ°ΡΡΠΈΠ²Π°ΡΡΡΡ Π΄Π²Π° ΠΆΠ΅Π»Π΅Π·Π½ΠΎΠ΄ΠΎΡΠΎΠΆΠ½ΡΡ ΠΏΡΡΠΈ ΠΈ Π΄Π²ΠΎΠ΅ ΠΆΠ΅Π»Π΅Π·Π½ΠΎΠ΄ΠΎΡΠΎΠΆΠ½ΡΡ Π²Π΅ΡΠΎΠ² Π³ΡΡΠ·ΠΎΠΏΠΎΠ΄ΡΠ΅ΠΌΠ½ΠΎΡΡΡΡ 150 ΡΠΎΠ½Π½ ΠΏΠΎΠ΄ ΠΊΠ°ΠΆΠ΄ΡΠΌ ΡΠΈΠ»ΠΎΡΠΎΠΌ. Π‘ΠΈΠ»ΠΎΡΡ Π΄ΠΈΠ°ΠΌΠ΅ΡΡΠΎΠΌ 12 ΠΌ ΡΡΡΠ°Π½Π°Π²Π»ΠΈΠ²Π°ΡΡΡΡ Π±Π»ΠΎΠΊΠ°ΠΌΠΈ ΠΏΠΎ 4 ΡΠΈΠ»ΠΎΡΠ° Π² ΠΊΠ°ΠΆΠ΄ΠΎΠΌ Π±Π»ΠΎΠΊΠ΅, Π° ΡΠΈΠ»ΠΎΡΡ Π΄ΠΈΠ°ΠΌΠ΅ΡΡΠΎΠΌ 18ΠΌ β Π² ΠΎΠ΄ΠΈΠ½ ΡΡΠ΄ Ρ ΡΠ°ΡΡΡΠΎΡΠ½ΠΈΠ΅ΠΌ ΠΌΠ΅ΠΆΠ΄Ρ ΠΎΡΡΠΌΠΈ 24 ΠΌ.
Π¦Π΅ΠΌΠ΅Π½Ρ ΠΌΠΎΠΆΠ½ΠΎ ΠΎΡΠ³ΡΡΠΆΠ°ΡΡ Π½Π°Π²Π°Π»ΠΎΠΌ Π² ΠΆΠ΅Π»Π΅Π·Π½ΠΎΠ΄ΠΎΡΠΎΠΆΠ½ΡΠ΅ Π²Π°Π³ΠΎΒΠ½Ρ, Π² ΠΆΠ΅Π»Π΅Π·Π½ΠΎΠ΄ΠΎΡΠΎΠΆΠ½ΡΠ΅ ΡΠΈΡΡΠ΅ΡΠ½Ρ β ΡΠ΅ΠΌΠ΅Π½ΡΠΎΠ²ΠΎΠ·Ρ, Π² Π°Π²ΡΠΎΡΠ΅ΠΌΠ΅Π½ΒΡΠΎΠ²ΠΎΠ·Ρ, Π° ΡΠ°ΠΊΠΆΠ΅ Π² Π·Π°ΡΠ°ΡΠ΅Π½Π½ΠΎΠΌ Π²ΠΈΠ΄Π΅ β Π² ΠΌΠ΅ΡΠΊΠ°Ρ Π²Π΅ΡΠΎΠΌ 50 ΠΊΠ³.
ΠΡΠ³ΡΡΠ·ΠΊΠ° ΡΠ΅ΠΌΠ΅Π½ΡΠ° ΠΌΠΎΠΆΠ΅Ρ ΠΎΡΡΡΠ΅ΡΡΠ²Π»ΡΡΡΡΡ ΡΠ°ΠΊΠΆΠ΅ ΡΠ΅ΡΠ½ΡΠΌ ΠΈΠ»ΠΈ ΠΌΠΎΡΒΡΠΊΠΈΠΌ ΡΡΠ°Π½ΡΠΏΠΎΡΡΠΎΠΌ ΠΊΠ°ΠΊ Π½Π°Π²Π°Π»ΠΎΠΌ, ΡΠ°ΠΊ ΠΈ Π² Π·Π°ΡΠ°ΡΠ΅Π½Π½ΠΎΠΌ Π²ΠΈΠ΄Π΅ β Π² ΠΌΠ΅ΡΠΊΠ°Ρ ΠΈΠ»ΠΈ Π² Π±ΠΎΠ»ΡΡΠ΅Π³ΡΡΠ·Π½ΡΡ ΠΊΠΎΠ½ΡΠ΅ΠΉΠ½Π΅ΡΠ°Ρ ΠΈΠ· ΠΏΠΎΠ»ΠΈΠΌΠ΅ΡΠ½ΡΡ ΠΌΠ°ΒΡΠ΅ΡΠΈΠ°Π»ΠΎΠ². ΠΠ°ΡΠ°ΡΠΈΠ²Π°Π½ΠΈΠ΅ ΡΠ΅ΠΌΠ΅Π½ΡΠ° ΠΏΡΠΎΠΈΠ·Π²ΠΎΠ΄ΠΈΡΡΡ Π² ΡΠΏΠ΅ΡΠΈΠ°Π»ΡΠ½ΡΡ ΡΠΏΠ°ΒΠΊΠΎΠ²ΠΎΡΠ½ΡΡ ΠΎΡΠ΄Π΅Π»Π΅Π½ΠΈΡΡ , ΠΎΡΠ½Π°ΡΠ΅Π½Π½ΡΡ Π²ΡΡΠΎΠΊΠΎΠΏΡΠΎΠΈΠ·Π²ΠΎΠ΄ΠΈΡΠ΅Π»ΡΠ½ΡΠΌΠΈ ΡΠΏΠ°ΠΊΠΎΠ²ΠΎΡΠ½ΡΠΌΠΈ ΠΌΠ°ΡΠΈΠ½Π°ΠΌΠΈ.
Π ΠΏΡΠΎΡΠ΅ΡΡΠ΅ ΡΠ°ΡΠΈΡΠΎΠ²Π°Π½ΠΈΡ ΡΠ΅ΠΌΠ΅Π½ΡΠ° Π²ΡΠ΄Π΅Π»ΡΠ΅ΡΡΡ Π·Π½Π°ΡΠΈΡΠ΅Π»ΡΠ½ΠΎΠ΅ ΠΊΠΎΒΠ»ΠΈΡΠ΅ΡΡΠ²ΠΎ ΠΏΡΠ»ΠΈ, ΠΏΠΎΡΡΠΎΠΌΡ ΡΠΏΠ°ΠΊΠΎΠ²ΠΎΡΠ½Π°Ρ ΠΌΠ°ΡΠΈΠ½Π° ΠΎΠ±ΠΎΡΡΠ΄ΠΎΠ²Π°Π½Π° Π°ΡΠΏΠΈΡΠ°ΡΠΈΠΎΠ½Π½ΠΎΠΉ ΡΡΡΠ°Π½ΠΎΠ²ΠΊΠΎΠΉ, ΡΠΎΡΡΠΎΡΡΠ΅ΠΉ ΠΈΠ· ΡΡΠΊΠ°Π²Π½ΠΎΠ³ΠΎ ΡΠΈΠ»ΡΡΡΠ° ΠΈ Π²ΡΡΡΠΆΠ½ΠΎΠ³ΠΎ Π²Π΅Π½ΡΠΈΠ»ΡΡΠΎΡΠ°. ΠΠΎΡΡΡΠΏΠ°ΡΡΠΈΠΉ ΠΈΠ· ΡΠΈΠ»ΠΎΡΠΎΠ² ΡΠ΅ΠΌΠ΅Π½Ρ ΠΏΡΠ΅Π΄Π²Π°ΒΡΠΈΡΠ΅Π»ΡΠ½ΠΎ ΠΏΡΠΎΠΏΡΡΠΊΠ°Π΅ΡΡΡ ΡΠ΅ΡΠ΅Π· ΠΏΡΠΎΡΠ΅ΠΈΠ²Π°ΡΡΠΈΠΉ ΡΠ½Π΅ΠΊ (Π΄Π»Ρ Π²ΡΠ΄Π΅Π»Π΅Π½ΠΈΡ ΡΠ»ΡΡΠ°ΠΉΠ½ΠΎ ΠΏΠΎΠΏΠ°Π²ΡΠΈΡ Π² Π½Π΅Π³ΠΎ ΠΎΡΡΠ°ΡΠΊΠΎΠ² ΠΌΠ΅Π»ΡΡΠΈΡ ΡΠ΅Π» ΠΈ ΠΊΡΡΠΏΠ½ΡΡ ΡΠ°ΡΡΠΈΡ ΠΌΠ°ΡΠ΅ΡΠΈΠ°Π»Π°), ΠΏΠΎΡΠ»Π΅ ΡΠ΅Π³ΠΎ ΠΏΠΎΠ΄Π°Π΅ΡΡΡ Π² ΡΠΏΠ°ΠΊΠΎΠ²ΠΎΡΠ½ΡΡ ΠΌΠ°ΡΠΈΠ½Ρ. ΠΡΠ»ΠΈ ΠΊΠΎΠ»ΠΈΡΠ΅ΡΡΠ²ΠΎ ΠΏΠΎΠ΄Π°Π²Π°Π΅ΠΌΠΎΠ³ΠΎ ΡΠ΅ΠΌΠ΅Π½ΡΠ° ΠΏΡΠ΅Π²ΡΡΠ°Π΅Ρ ΠΏΡΠΎΠΏΡΡΠΊΠ½ΡΡ ΡΠΏΠΎΡΠΎΠ±Π½ΠΎΡΡΡ ΡΠΏΠ°ΠΊΠΎΠ²ΠΎΡΠ½ΠΎΠΉ ΠΌΠ°ΡΠΈΠ½Ρ, ΡΠΎ ΠΈΠ·Π±ΡΡΠΎΠΊ Π΅Π³ΠΎ ΡΠ»ΠΈΠ²Π°Π΅ΡΡΡ Π² Π±ΡΠ½ΠΊΠ΅Ρ, ΠΈΠ· ΠΊΠΎΡΠΎΡΠΎΠ³ΠΎ ΡΠ΅ΠΌΠ΅Π½Ρ Π²Π½ΠΎΠ²Ρ ΠΏΠΎΡΡΡΠΏΠ°Π΅Ρ Π² ΠΏΡΠΎΡΠ΅ΡΡ.
ΠΠ»ΠΎΡΠ°Π΄Ρ ΡΠΊΠ»Π°Π΄Π° Π΄Π»Ρ Ρ ΡΠ°Π½Π΅Π½ΠΈΡ ΡΠ°ΡΠΈΡΠΎΠ²Π°Π½Π½ΠΎΠ³ΠΎ ΡΠ΅ΠΌΠ΅Π½ΡΠ° ΡΠ°ΡΡΡΠΈΒΡΡΠ²Π°Π΅ΡΡΡ ΠΈΠ· ΡΠΎΠ³ΠΎ, ΡΡΠΎ Π½Π° 1 ΠΌ2 ΠΏΠΎΠ»Π΅Π·Π½ΠΎΠΉ ΠΏΠ»ΠΎΡΠ°Π΄ΠΈ ΠΌΠΎΠΆΠ½ΠΎ ΡΠ»ΠΎΠΆΠΈΡΡ 3 Ρ ΡΠ΅ΠΌΠ΅Π½ΡΠ° Π² Π±ΡΠΌΠ°ΠΆΠ½ΡΡ ΠΌΠ΅ΡΠΊΠ°Ρ . ΠΠ»Ρ ΠΏΡΠΎΠ΅Π·Π΄ΠΎΠ² ΠΈ ΠΏΡΠΎΡ ΠΎΠ΄ΠΎΠ² ΠΏΡΠ΅ΒΠ΄ΡΡΠΌΠ°ΡΡΠΈΠ²Π°Π΅ΡΡΡ Π΄ΠΎΠΏΠΎΠ»Π½ΠΈΡΠ΅Π»ΡΠ½Π°Ρ ΠΏΠ»ΠΎΡΠ°Π΄Ρ Π² ΡΠ°Π·ΠΌΠ΅ΡΠ΅ ΠΎΠΊΠΎΠ»ΠΎ 30β 35% ΠΎΡ ΠΏΠΎΠ»Π΅Π·Π½ΠΎΠΉ ΠΏΠ»ΠΎΡΠ°Π΄ΠΈ ΡΠΊΠ»Π°Π΄Π°.
Π‘ΠΠΠΠ‘Π« ΠΠΠ― Π‘Π«ΠΠ£Π§ΠΠ₯ ΠΠΠ’ΠΠ ΠΠΠΠΠ
ΠΡΠΈ ΠΏΡΠΎΠΈΠ·Π²ΠΎΠ΄ΡΡΠ²Π΅ ΡΠΈΠ»ΠΎΡΠΎΠ² Π΄Π»Ρ Ρ
ΡΠ°Π½Π΅Π½ΠΈΡ ΡΡΠΏΡΡΠΈΡ
ΠΌΠ°ΡΠ΅ΡΠΈΠ°Π»ΠΎΠ² (ΡΠ΅ΠΌΠ΅Π½ΡΠ°) Π΄ΠΎΠΏΡΡΠΊΠ°Π΅ΡΡΡ ΠΈΡ
ΡΠ°ΡΠΏΠΎΠ»Π°Π³Π°ΡΡ Π² Π·Π΄Π°Π½ΠΈΡΡ
ΠΈ Π½Π° ΠΎΡΠΊΡΡΡΡΡ
ΠΏΠ»ΠΎΡΠ°Π΄ΠΊΠ°Ρ
Π·Π°Π³Π»ΡΠ±Π»Π΅Π½Π½ΡΠΌΠΈ ΠΈΠ»ΠΈ Π½Π°Π·Π΅ΠΌΠ½ΡΠΌΠΈ, ΠΊΠ°ΠΊ ΠΏΡΠ°Π²ΠΈΠ»ΠΎ, ΡΠ±Π»ΠΎΠΊΠΈΡΠΎΠ²Π°Π½Π½ΡΠΌΠΈ, ΠΌΠ½ΠΎΠ³ΠΎΡΡΠ΅ΠΉΠΊΠΎΠ²ΡΠΌΠΈ.
ΠΠ΅ΡΠ΅ΡΠ΅Π½Ρ ΠΌΠ°ΡΠ΅ΡΠΈΠ°Π»ΠΎΠ² Ρ ΡΠ°Π½ΠΈΠΌΡΡ Π² ΡΠΈΠ»ΠΎΡΠ°Ρ : Π¦ΠΠΠΠΠ’, ΡΠ»Π°ΠΊ ΠΏΠ΅ΡΠ΅Π΄Π΅Π»ΡΠ½ΡΠΉ, ΠΊΠ²Π°ΡΡΠΈΡ, Π¨Π°ΠΌΠΎΡ, ΠΡΠ½ΠΈΡ, Π₯ΡΠΎΠΌΠΈΡ, Π¨Π»Π°ΠΊ, ΠΠ΅ΡΠΎΠΊ ΡΡΡΠΎΠΉ, ΠΠ·Π²Π΅ΡΡΠ½ΡΠΊ, ΠΠ»ΠΈΠ½Π°, ΠΠ·Π²Π΅ΡΡΡ, ΠΠ°Π³Π½Π΅Π·ΠΈΡΠΎΠ²ΡΠΉ ΠΏΠΎΡΠΎΡΠΎΠΊ, ΠΠ΅ΡΠΎΠΊ ΡΡΡ ΠΎΠΉ, ΠΠΎΠΊΡ ΠΈ ΠΊΠΎΠΊΡΠΈΠΊ.
Π‘ΠΈΠ»ΠΎΡ Π΄Π»Ρ ΡΠ΅ΠΌΠ΅Π½ΡΠ°, ΡΠΈΠ»ΠΎΡ Π΄Π»Ρ ΡΠ»Π°ΠΊΠ°, ΡΠΈΠ»ΠΎΡ Π΄Π»Ρ ΠΊΠ²Π°ΡΡΠΈΡΠ°, ΡΠΈΠ»ΠΎΡ Π΄Π»Ρ ΡΠ°ΠΌΠΎΡΠ°, ΡΠΈΠ»ΠΎΡ Π΄Π»Ρ Π΄ΡΠ½ΠΈΡΠ°, ΡΠΈΠ»ΠΎΡ Π΄Π»Ρ Ρ ΡΠΎΠΌΠΈΡΠ°, ΡΠΈΠ»ΠΎΡ Π΄Π»Ρ ΠΏΠ΅ΡΠΊΠ° ΡΡΡΠΎΠ³ΠΎ, ΡΠΈΠ»ΠΎΡ Π΄Π»Ρ ΠΈΠ·Π²Π΅ΡΠ½ΡΠΊΠ°, ΡΠΈΠ»ΠΎΡ Π΄Π»Ρ Π³Π»ΠΈΠ½Ρ, ΡΠΈΠ»ΠΎΡ Π΄Π»Ρ ΠΈΠ·Π²Π΅ΡΠΈ, ΡΠΈΠ»ΠΎΡ Π΄Π»Ρ ΠΏΠΎΡΠΎΡΠΊΠ°, ΡΠΈΠ»ΠΎΡ Π΄Π»Ρ ΠΏΠ΅ΡΠΊΠ° ΡΡΡ ΠΎΠ³ΠΎ, ΡΠΈΠ»ΠΎΡ Π΄Π»Ρ ΠΊΠΎΠΊΡΠ°.
ΠΠ£ΠΠΠΠ Π. ΠΡΠΈ ΠΏΡΠΎΠ΅ΠΊΡΠΈΡΠΎΠ²Π°Π½ΠΈΠΈ Π½Π°ΡΡΠΆΠ½ΡΡ Π±ΡΠ½ΠΊΠ΅ΡΠΎΠ² ΠΈ Π±ΡΠ½ΠΊΠ΅ΡΠΎΠ², ΡΠ°ΡΠΏΠΎΠ»Π°Π³Π°Π΅ΠΌΡΡ Π²Π½ΡΡΡΠΈ Π·Π΄Π°Π½ΠΈΠΉ ΠΈ ΡΠΎΠΎΡΡΠΆΠ΅Π½ΠΈΠΉ Π΄ΠΎΠ»ΠΆΠ½ΠΎ Π²ΠΊΠ»ΡΡΠ°ΡΡ Π΄Π²Π° ΠΏΠΎΡΠ»Π΅Π΄ΠΎΠ²Π°ΡΠ΅Π»ΡΠ½ΡΡ ΡΡΠ°ΠΏΠ°:
1) ΠΎΠΏΡΠ΅Π΄Π΅Π»Π΅Π½ΠΈΠ΅ Π³Π΅ΠΎΠΌΠ΅ΡΡΠΈΡΠ΅ΡΠΊΠΈΡ ΠΏΠ°ΡΠ°ΠΌΠ΅ΡΡΠΎΠ² β ΡΠΎΡΠΌΡ Π±ΡΠ½ΠΊΠ΅ΡΠ° ΠΈ Π΅Π³ΠΎ Π²ΠΎΡΠΎΠ½ΠΊΠΈ, ΡΠ³Π»ΠΎΠ² Π½Π°ΠΊΠ»ΠΎΠ½Π° ΡΡΠ΅Π½ΠΎΠΊ, ΡΠ°Π·ΠΌΠ΅ΡΠΎΠ² Π²ΡΠΏΡΡΠΊΠ½ΠΎΠ³ΠΎ ΠΎΡΠ²Π΅ΡΡΡΠΈΡ, ΠΊΠΎΡΠΎΡΡΠ΅ ΠΎΠΏΡΠ΅Π΄Π΅Π»ΡΡΡΡΡ ΡΠ°ΡΡΠ΅ΡΠΎΠΌ Π½Π° ΠΎΡΠ½ΠΎΠ²Π°Π½ΠΈΠΈ ΡΠΈΠ·ΠΈΠΊΠΎ-ΠΌΠ΅Ρ Π°Π½ΠΈΡΠ΅ΡΠΊΠΈΡ Ρ Π°ΡΠ°ΠΊΡΠ΅ΡΠΈΡΡΠΈΠΊ ΡΡΠΏΡΡΠ΅Π³ΠΎ ΠΌΠ°ΡΠ΅ΡΠΈΠ°Π»Π° Ρ ΡΡΠ΅ΡΠΎΠΌ Π½Π΅Π±Π»Π°Π³ΠΎΠΏΡΠΈΡΡΠ½ΡΡ ΠΈΡ ΠΈΠ·ΠΌΠ΅Π½Π΅Π½ΠΈΠΉ, ΠΏΡΠΈ ΡΡΠΎΠΌ Π΄ΠΎΠ»ΠΆΠ½Ρ ΠΈΡΠΊΠ»ΡΡΠ°ΡΡΡΡ ΡΠ²ΠΎΠ΄ΠΎΠΎΠ±ΡΠ°Π·ΠΎΠ²Π°Π½ΠΈΠ΅ Π½Π°Π΄ Π²ΡΠΏΡΡΠΊΠ½ΡΠΌ ΠΎΡΠ²Π΅ΡΡΡΠΈΠ΅ΠΌ ΠΈ Π·Π°Π²ΠΈΡΠ°Π½ΠΈΠ΅ Π½Π° ΡΡΠ΅Π½ΠΊΠ°Ρ ;
2) ΡΠ°ΡΡΠ΅Ρ ΠΈ ΠΏΡΠΎΠ΅ΠΊΡΠΈΡΠΎΠ²Π°Π½ΠΈΠ΅ ΠΊΠΎΠ½ΡΡΡΡΠΊΡΠΈΠΉ Π±ΡΠ½ΠΊΠ΅ΡΠΎΠ² ΠΈ ΠΈΡ Π·Π°ΡΠΈΡΡ ΠΎΡ ΡΠ΄Π°ΡΠΎΠ² ΠΈ ΠΈΡΡΠΈΡΠ°Π½ΠΈΡ.
ΠΠΏΡΠ΅Π΄Π΅Π»Π΅Π½ΠΈΠ΅ Π³Π΅ΠΎΠΌΠ΅ΡΡΠΈΡΠ΅ΡΠΊΠΈΡ ΠΏΠ°ΡΠ°ΠΌΠ΅ΡΡΠΎΠ² Π±ΡΠ½ΠΊΠ΅ΡΠΎΠ² ΡΠ°Π·Π»ΠΈΡΠ°Π΅ΡΡΡ Π΄Π»Ρ ΡΠ²ΡΠ·Π½ΡΡ (ΠΈΠΌΠ΅ΡΡΠΈΡ ΡΡΠ΅ΠΏΠ»Π΅Π½ΠΈΠ΅, ΡΠ»Π΅ΠΆΠΈΠ²Π°ΡΡΠΈΡ ΡΡ) ΠΈ Π½Π΅ΡΠ²ΡΠ·Π½ΡΡ (Π½Π΅ ΠΈΠΌΠ΅ΡΡΠΈΡ ΡΡΠ΅ΠΏΠ»Π΅Π½ΠΈΡ, Π½Π΅ΡΠ»Π΅ΠΆΠΈΠ²Π°ΡΡΠΈΡ ΡΡ) ΡΡΠΏΡΡΠΈΡ ΠΌΠ°ΡΠ΅ΡΠΈΠ°Π»ΠΎΠ². Π ΡΠ²ΡΠ·Π½ΡΠΌ ΠΎΡΠ½ΠΎΡΡΡΡΡ, ΠΊΠ°ΠΊ ΠΏΡΠ°Π²ΠΈΠ»ΠΎ, ΠΌΠ°ΡΠ΅ΡΠΈΠ°Π»Ρ, ΡΠΎΠ΄Π΅ΡΠΆΠ°ΡΠΈΠ΅ ΡΡΠ°ΠΊΡΠΈΠΈ ΠΌΠ΅Π½Π΅Π΅ 2 ΠΌΠΌ ΠΈ ΠΈΠΌΠ΅ΡΡΠΈΠ΅ Π²Π»Π°ΠΆΠ½ΠΎΡΡΡ Π±ΠΎΠ»Π΅Π΅ 2 %, Π° ΠΊ Π½Π΅ΡΠ²ΡΠ·Π½ΡΠΌ β ΡΠ΅Π±Π΅Π½Ρ, Π³Π°Π»ΡΠΊΠ° ΠΈ Π΄ΡΡΠ³ΠΈΠ΅ ΠΌΠ°ΡΠ΅ΡΠΈΠ°Π»Ρ Ρ ΠΊΡΡΠΏΠ½ΠΎΡΡΡΡ Π·Π΅ΡΠ΅Π½ 2 ΠΌΠΌ ΠΈ Π±ΠΎΠ»Π΅Π΅, Π° ΡΠ°ΠΊΠΆΠ΅ ΠΏΠ΅ΡΠΎΠΊ Ρ ΠΊΡΡΠΏΠ½ΠΎΡΡΡΡ Π·Π΅ΡΠ΅Π½ Π΄ΠΎ 2 ΠΌΠΌ ΠΈ Π²Π»Π°ΠΆΠ½ΠΎΡΡΡΡ Π΄ΠΎ 2 %.
ΠΡΠΈ ΠΏΡΠΎΠ΅ΠΊΡΠΈΡΠΎΠ²Π°Π½ΠΈΠΈ Π±ΡΠ½ΠΊΠ΅ΡΠΎΠ² Π½Π΅ΠΎΠ±Ρ ΠΎΠ΄ΠΈΠΌΠΎ ΠΏΡΠΈΠ½ΠΈΠΌΠ°ΡΡ Π²ΠΎ Π²Π½ΠΈΠΌΠ°Π½ΠΈΠ΅, ΡΡΠΎ ΠΈΠΌΠ΅ΡΡΡΡ Π΄Π²Π΅ Π²ΠΎΠ·ΠΌΠΎΠΆΠ½ΡΠ΅ ΡΠΎΡΠΌΡ ΠΈΡΡΠ΅ΡΠ΅Π½ΠΈΡ ΡΡΠΏΡΡΠ΅Π³ΠΎ ΠΌΠ°ΡΠ΅ΡΠΈΠ°Π»Π°: Π³ΠΈΠ΄ΡΠ°Π²Π»ΠΈΡΠ΅ΡΠΊΠ°Ρ, ΠΏΡΠΈ ΠΊΠΎΡΠΎΡΠΎΠΉ Π½Π°Ρ ΠΎΠ΄ΠΈΡΡΡ Π² Π΄Π²ΠΈΠΆΠ΅Π½ΠΈΠΈ ΡΡΠΏΡΡΠΈΠΉ ΠΌΠ°ΡΠ΅ΡΠΈΠ°Π» Π²ΠΎ Π²ΡΠ΅ΠΌ ΠΎΠ±ΡΠ΅ΠΌΠ΅ Π±ΡΠ½ΠΊΠ΅ΡΠ°, ΠΈ Π½Π΅Π³ΠΈΠ΄ΡΠ°Π²Π»ΠΈΡΠ΅ΡΠΊΠ°Ρ, ΠΏΡΠΈ ΠΊΠΎΡΠΎΡΠΎΠΉ Π΄Π²ΠΈΠΆΠ΅ΡΡΡ ΡΠΎΠ»ΡΠΊΠΎ ΡΠ΅Π½ΡΡΠ°Π»ΡΠ½Π°Ρ ΡΠ°ΡΡΡ Π½Π°Π΄ Π²ΡΠΏΡΡΠΊΠ½ΡΠΌ ΠΎΡΠ²Π΅ΡΡΡΠΈΠ΅ΠΌ, Π° ΠΎΡΡΠ°Π»ΡΠ½ΠΎΠΉ ΠΌΠ°ΡΠ΅ΡΠΈΠ°Π» Π½Π΅ΠΏΠΎΠ΄Π²ΠΈΠΆΠ΅Π½. ΠΠ»Ρ ΡΠ²ΡΠ·Π½ΡΡ ΠΈΠ»ΠΈ ΡΠ°ΠΌΠΎΠ²ΠΎΠ·Π³ΠΎΡΠ°ΡΡΠΈΡ ΡΡ ΡΡΠΏΡΡΠΈΡ ΠΌΠ°ΡΠ΅ΡΠΈΠ°Π»ΠΎΠ² ΡΠ»Π΅Π΄ΡΠ΅Ρ ΠΏΡΠΎΠ΅ΠΊΡΠΈΡΠΎΠ²Π°ΡΡ Π±ΡΠ½ΠΊΠ΅ΡΠ° Ρ Π³ΠΈΠ΄ΡΠ°Π²Π»ΠΈΡΠ΅ΡΠΊΠΎΠΉ ΡΠΎΡΠΌΠΎΠΉ ΠΈΡΡΠ΅ΡΠ΅Π½ΠΈΡ, Π° Π΄Π»Ρ Π½Π΅ΡΠ²ΡΠ·Π½ΡΡ , ΠΊΠ°ΠΊ ΠΏΡΠ°Π²ΠΈΠ»ΠΎ, Ρ Π½Π΅Π³ΠΈΠ΄ΡΠ°Π²Π»ΠΈΡΠ΅ΡΠΊΠΎΠΉ.
ΠΡΠ½ΠΊΠ΅ΡΠ° Π½Π΅Π³ΠΈΠ΄ΡΠ°Π²Π»ΠΈΡΠ΅ΡΠΊΠΎΠ³ΠΎ ΠΈΡΡΠ΅ΡΠ΅Π½ΠΈΡ Π΄Π»Ρ Π½Π΅ΡΠ²ΡΠ·Π½ΡΡ ΠΌΠ°ΡΠ΅ΡΠΈΠ°Π»ΠΎΠ² ΠΌΠΎΠ³ΡΡ Π±ΡΡΡ ΡΠ°Π·Π»ΠΈΡΠ½ΠΎΠΉ ΡΠΎΡΠΌΡ: ΠΏΠΈΡΠ°ΠΌΠΈΠ΄Π°Π»ΡΠ½ΠΎΠΉ, ΠΊΠΎΠ½ΠΈΡΠ΅ΡΠΊΠΎΠΉ, Ρ ΠΏΠ»ΠΎΡΠΊΠΈΠΌ Π³ΠΎΡΠΈΠ·ΠΎΠ½ΡΠ°Π»ΡΠ½ΡΠΌ Π΄Π½ΠΈΡΠ΅ΠΌ, ΠΏΠ°ΡΠ°Π±ΠΎΠ»ΠΈΡΠ΅ΡΠΊΠΎΠΉ ΠΈΠ»ΠΈ Π΄ΡΡΠ³ΠΎΠΉ ΡΠΈΠΌΠΌΠ΅ΡΡΠΈΡΠ½ΠΎΠΉ ΠΈΠ»ΠΈ Π½Π΅ΡΠΈΠΌΠΌΠ΅ΡΡΠΈΡΠ½ΠΎΠΉ ΡΠΎΡΠΌΡ. ΠΡΠΈ ΠΏΡΠΎΠ΅ΠΊΡΠΈΡΠΎΠ²Π°Π½ΠΈΠΈ Π³Π΅ΠΎΠΌΠ΅ΡΡΠΈΡΠ΅ΡΠΊΠΈΡ ΠΏΠ°ΡΠ°ΠΌΠ΅ΡΡΠΎΠ² Π΄Π»Ρ ΡΠ°ΠΊΠΈΡ Π±ΡΠ½ΠΊΠ΅ΡΠΎΠ² Π½ΠΎΡΠΌΠΈΡΡΠ΅ΡΡΡ ΡΠΎΠ»ΡΠΊΠΎ ΠΎΠ΄ΠΈΠ½ ΠΏΠ°ΡΠ°ΠΌΠ΅ΡΡ β ΡΠ°Π·ΠΌΠ΅Ρ Π²ΡΠΏΡΡΠΊΠ½ΠΎΠ³ΠΎ ΠΎΡΠ²Π΅ΡΡΡΠΈΡ, ΠΊΠΎΡΠΎΡΡΠΉ Π΄ΠΎΠ»ΠΆΠ΅Π½ ΠΎΠΏΡΠ΅Π΄Π΅Π»ΡΡΡΡΡ Π² Π·Π°Π²ΠΈΡΠΈΠΌΠΎΡΡΠΈ ΠΎΡ ΡΠ°Π·ΠΌΠ΅ΡΠ° ΠΌΠ°ΠΊΡΠΈΠΌΠ°Π»ΡΠ½ΠΎΠ³ΠΎ ΠΊΡΡΠΊΠ° ΡΡΠΏΡΡΠ΅Π³ΠΎ ΠΌΠ°ΡΠ΅ΡΠΈΠ°Π»Π°. Π£Π³ΠΎΠ» Π½Π°ΠΊΠ»ΠΎΠ½Π° ΡΡΠ΅Π½ΠΎΠΊ Π²ΠΎΡΠΎΠ½ΠΊΠΈ Π΄ΠΎΠΏΡΡΠΊΠ°Π΅ΡΡΡ ΠΏΡΠΈΠ½ΠΈΠΌΠ°ΡΡ ΠΏΡΠΎΠΈΠ·Π²ΠΎΠ»ΡΠ½ΡΠΌ, Π·Π° ΠΈΡΠΊΠ»ΡΡΠ΅Π½ΠΈΠ΅ΠΌ ΡΠ»ΡΡΠ°Π΅Π², ΠΊΠΎΠ³Π΄Π° ΠΏΠΎ ΡΡΠ»ΠΎΠ²ΠΈΡΠΌ ΡΠ΅Ρ Π½ΠΎΠ»ΠΎΠ³ΠΈΠΈ ΡΡΠ΅Π±ΡΠ΅ΡΡΡ ΠΏΠΎΠ»Π½ΠΎΠ΅ ΠΎΠΏΠΎΡΠΎΠΆΠ½Π΅Π½ΠΈΠ΅ Π±ΡΠ½ΠΊΠ΅ΡΠ°. Π ΡΡΠΎΠΌ ΡΠ»ΡΡΠ°Π΅ ΡΠ³ΠΎΠ» Π½Π°ΠΊΠ»ΠΎΠ½Π° ΡΡΠ΅Π½ΠΎΠΊ ΡΠ»Π΅Π΄ΡΠ΅Ρ ΠΏΡΠΈΠ½ΠΈΠΌΠ°ΡΡ ΠΏΠΎ ΡΠ³Π»Ρ Π΅ΡΡΠ΅ΡΡΠ²Π΅Π½Π½ΠΎΠ³ΠΎ ΠΎΡΠΊΠΎΡΠ° ΡΡΠΏΡΡΠ΅Π³ΠΎ ΠΌΠ°ΡΠ΅ΡΠΈΠ°Π»Π° Ρ ΠΏΡΠ΅Π²ΡΡΠ΅Π½ΠΈΠ΅ΠΌ ΠΏΠΎΡΠ»Π΅Π΄Π½Π΅Π³ΠΎ Π½Π° 5β 7Β°.
ΠΡΠ½ΠΊΠ΅ΡΠ° Π΄Π»Ρ ΡΠ²ΡΠ·Π½ΡΡ ΠΌΠ°ΡΠ΅ΡΠΈΠ°Π»ΠΎΠ² Π³ΠΈΠ΄ΡΠ°Π²Π»ΠΈΡΠ΅ΡΠΊΠΎΠ³ΠΎ ΠΈΡΡΠ΅ΡΠ΅Π½ΠΈΡ Π½Π°Π΄Π»Π΅ΠΆΠΈΡ Π½Π°Π·Π½Π°ΡΠ°ΡΡ ΠΊΠΎΠ½ΠΈΡΠ΅ΡΠΊΠΎΠΉ, ΠΏΠΈΡΠ°ΠΌΠΈΠ΄Π°Π»ΡΠ½ΠΎΠΉ ΠΈΠ»ΠΈ Π»ΠΎΡΠΊΠΎΠ²ΠΎΠΉ ΡΠΎΡΠΌΡ. ΠΡΡΠ³ΠΈΠ΅ ΡΠΎΡΠΌΡ (ΠΏΠ°ΡΠ°Π±ΠΎΠ»ΠΈΡΠ΅ΡΠΊΠ°Ρ, Ρ ΠΏΠ»ΠΎΡΠΊΠΈΠΌ Π΄Π½ΠΈΡΠ΅ΠΌ), Π° ΡΠ°ΠΊΠΆΠ΅ Π½Π΅ΡΠΈΠΌΠΌΠ΅ΡΡΠΈΡΠ½ΡΠ΅ Π±ΡΠ½ΠΊΠ΅ΡΠ° Π½Π΅ Π΄ΠΎΠΏΡΡΠΊΠ°ΡΡΡΡ. Π£Π³ΠΎΠ» Π½Π°ΠΊΠ»ΠΎΠ½Π° ΡΡΠ°Π½ΠΎΠΊ ΠΈ ΡΠ°Π·ΠΌΠ΅ΡΡ Π²ΡΠΏΡΡΠΊΠ½ΠΎΠ³ΠΎ ΠΎΡΠ²Π΅ΡΡΡΠΈΡ ΡΠ°ΠΊΠΈΡ Π±ΡΠ½ΠΊΠ΅ΡΠΎΠ² ΡΠ»Π΅Π΄ΡΠ΅Ρ ΡΠ°ΡΡΡΠΈΡΡΠ²Π°ΡΡ Π½Π° ΠΎΡΠ½ΠΎΠ²Π°Π½ΠΈΠΈ ΡΠΈΠ·ΠΈΠΊΠΎ-ΠΌΠ΅Ρ Π°Π½ΠΈΡΠ΅ΡΠΊΠΈΡ Ρ Π°ΡΠ°ΠΊΡΠ΅ΡΠΈΡΡΠΈΠΊ ΡΡΠΏΡΡΠ΅Π³ΠΎ ΠΌΠ°ΡΠ΅ΡΠΈΠ°Π»Π°: ΡΠ³Π»Π° Π²Π½ΡΡΡΠ΅Π½Π½Π΅Π³ΠΎ ΡΡΠ΅Π½ΠΈΡ (ΡΠ³ΠΎΠ» Π΅ΡΡΠ΅ΡΡΠ²Π΅Π½Π½ΠΎΠ³ΠΎ ΠΎΡΠΊΠΎΡΠ° Π½Π΅ Π΄ΠΎΠΏΡΡΠΊΠ°Π΅ΡΡΡ), ΡΠ΄Π΅Π»ΡΠ½ΠΎΠ³ΠΎ ΡΡΠ΅ΠΏΠ»Π΅Π½ΠΈΡ, ΡΠ³Π»Π° Π²Π½Π΅ΡΠ½Π΅Π³ΠΎ ΡΡΠ΅Π½ΠΈΡ, ΡΡΡΠ΅ΠΊΡΠΈΠ²Π½ΠΎΠ³ΠΎ ΡΠ³Π»Π° ΡΡΠ΅Π½ΠΈΡ, ΡΡΠ½ΠΊΡΠΈΠΈ ΠΈΡΡΠ΅ΡΠ΅Π½ΠΈΡ, β ΠΎΠΏΡΠ΅Π΄Π΅Π»ΡΠ΅ΠΌΡΡ Ρ ΠΏΠΎΠΌΠΎΡΡΡ ΠΏΡΠΈΠ±ΠΎΡΠΎΠ², ΠΈΠ·ΠΌΠ΅ΡΡΡΡΠΈΡ ΡΠΎΠΏΡΠΎΡΠΈΠ²Π»Π΅Π½ΠΈΠ΅ ΡΡΠΏΡΡΠ΅Π³ΠΎ ΠΌΠ°ΡΠ΅ΡΠΈΠ°Π»Π° Π½Π° ΡΠ΄Π²ΠΈΠ³. Π£Π³ΠΎΠ» Π½Π°ΠΊΠ»ΠΎΠ½Π° ΡΡΠ΅Π½ΠΎΠΊ Π΄ΠΎΠΏΡΡΠΊΠ°Π΅ΡΡΡ ΠΏΡΠΈΠ±Π»ΠΈΠΆΠ΅Π½Π½ΠΎ Π²ΡΠ±ΠΈΡΠ°ΡΡ ΠΏΠΎ ΡΠ΅ΡΡ. 6 Π² Π·Π°Π²ΠΈΡΠΈΠΌΠΎΡΡΠΈ ΠΎΡ ΡΠ³Π»Π° Π²Π½Π΅ΡΠ½Π΅Π³ΠΎ ΡΡΠ΅Π½ΠΈΡ (ΡΠ³Π»Π° ΡΡΠ΅Π½ΠΈΡ ΡΡΠΏΡΡΠ΅Π³ΠΎ ΠΌΠ°ΡΠ΅ΡΠΈΠ°Π»Π° ΠΏΠΎ ΠΌΠ°ΡΠ΅ΡΠΈΠ°Π»Ρ ΡΡΠ΅Π½ΠΊΠΈ Π±ΡΠ½ΠΊΠ΅ΡΠ°).
ΠΡΠΈ ΠΏΡΠΎΠ΅ΠΊΡΠΈΡΠΎΠ²Π°Π½ΠΈΠΈ Π±ΡΠ½ΠΊΠ΅ΡΠΎΠ² Π΄Π»Ρ ΡΠ²ΡΠ·Π½ΡΡ ΡΡΠΏΡΡΠΈΡ ΠΌΠ°ΡΠ΅ΡΠΈΠ°Π»ΠΎΠ² ΠΎΠ±ΡΠ΅ΠΌΠ½ΠΎ-ΠΏΠ»Π°Π½ΠΈΡΠΎΠ²ΠΎΡΠ½ΠΎΠ΅ ΡΠ΅ΡΠ΅Π½ΠΈΠ΅ Π±ΡΠ½ΠΊΠ΅ΡΠ½ΠΎΠ³ΠΎ ΠΏΡΠΎΠΏΠ΅ΡΠ° Π·Π΄Π°Π½ΠΈΠΉ ΡΠ»Π΅Π΄ΡΠ΅Ρ ΡΡΡΠ°Π½Π°Π²Π»ΠΈΠ²Π°ΡΡ ΠΏΠΎΡΠ»Π΅ ΠΎΠΏΡΠ΅Π΄Π΅Π»Π΅Π½ΠΈΡ Π³Π΅ΠΎΠΌΠ΅ΡΡΠΈΡΠ΅ΡΠΊΠΈΡ ΠΏΠ°ΡΠ°ΠΌΠ΅ΡΡΠΎΠ² Π±ΡΠ½ΠΊΠ΅ΡΠΎΠ². ΠΡΠ½ΠΊΠ΅ΡΠ½ΡΠ΅ ΠΏΡΠΎΠ»Π΅ΡΡ Π΄ΠΎΠ»ΠΆΠ½Ρ ΠΈΠΌΠ΅ΡΡ ΡΠ½ΠΈΡΠΈΡΠΈΡΠΎΠ²Π°Π½Π½ΡΠ΅ ΡΠ΅ΡΠΊΠΈ ΠΊΠΎΠ»ΠΎΠ½Π½ ΠΈ Π²ΡΡΠΎΡΡ ΡΡΠ°ΠΆΠ΅ΠΉ.
ΠΡΠΈ ΠΏΡΠΎΠ΅ΠΊΡΠΈΡΠΎΠ²Π°Π½ΠΈΠΈ Π±ΡΠ½ΠΊΠ΅ΡΠΎΠ² ΡΠ»Π΅Π΄ΡΠ΅Ρ ΠΎΠ±Π΅ΡΠΏΠ΅ΡΠΈΡΡ ΠΌΠ°ΠΊΡΠΈΠΌΠ°Π»ΡΠ½ΠΎΠ΅ ΠΈΡΠΏΠΎΠ»ΡΠ·ΠΎΠ²Π°Π½ΠΈΠ΅ Π²ΡΠ΅Π³ΠΎ Π³Π΅ΠΎΠΌΠ΅ΡΡΠΈΡΠ΅ΡΠΊΠΎΠ³ΠΎ ΠΎΠ±ΡΠ΅ΠΌΠ° Π±ΡΠ½ΠΊΠ΅ΡΠ° (Π½Π΅ ΠΌΠ΅Π½Π΅Π΅ 80 % ΠΏΡΠΈ Π·Π°Π³ΡΡΠ·ΠΊΠ΅).
ΠΠ°Π²Π»Π΅Π½ΠΈΠ΅ ΡΡΠΏΡΡΠ΅Π³ΠΎ ΠΌΠ°ΡΠ΅ΡΠΈΠ°Π»Π° Π½Π° ΡΡΠ΅Π½ΠΊΠΈ Π±ΡΠ½ΠΊΠ΅ΡΠ° ΡΠ»Π΅Π΄ΡΠ΅Ρ ΠΏΡΠΈΠ½ΠΈΠΌΠ°ΡΡ ΠΊΠ°ΠΊ Π΄Π»Ρ ΠΏΠΎΠ΄ΠΏΠΎΡΠ½ΠΎΠΉ ΡΡΠ΅Π½Ρ Π±Π΅Π· ΡΡΠ΅ΡΠ° ΡΠΈΠ» ΡΡΠ΅Π½ΠΈΡ ΠΌΠ΅ΠΆΠ΄Ρ ΡΡΠΏΡΡΠΈΠΌ ΠΌΠ°ΡΠ΅ΡΠΈΠ°Π»Π°ΠΌ ΠΈ ΡΡΠ΅Π½ΠΊΠ°ΠΌΠΈ Π±ΡΠ½ΠΊΠ΅ΡΠ°.
ΠΠΎΠ½ΡΡΡΡΠΊΡΠΈΠΈ Π±ΡΠ½ΠΊΠ΅ΡΠ° ΡΠ»Π΅Π΄ΡΠ΅Ρ ΡΠ°ΡΡΡΠΈΡΡΠ²Π°ΡΡ Π½Π° Π΄Π΅ΠΉΡΡΠ²ΠΈΠ΅ Π²ΡΠ΅ΠΌΠ΅Π½Π½ΠΎΠΉ Π½Π°Π³ΡΡΠ·ΠΊΠΈ ΠΎΡ Π²Π΅ΡΠ° ΡΡΠΏΡΡΠ΅Π³ΠΎ ΠΌΠ°ΡΠ΅ΡΠΈΠ°Π»Π°, Π·Π°ΠΏΠΎΠ»Π½ΡΡΡΠ΅Π³ΠΎ Π±ΡΠ½ΠΊΠ΅Ρ, ΠΏΠΎΡΡΠΎΡΠ½Π½ΡΡ Π½Π°Π³ΡΡΠ·ΠΎΠΊ ΠΎΡ ΡΠΎΠ±ΡΡΠ²Π΅Π½Π½ΠΎΠ³ΠΎ Π²Π΅ΡΠ° ΠΊΠΎΠ½ΡΡΡΡΠΊΡΠΈΠΉ, Π²Π΅ΡΠ° ΡΡΡΠ΅ΡΠΎΠ²ΠΊΠΈ, Π° ΡΠ°ΠΊΠΆΠ΅ Π½Π° Π΄Π΅ΠΉΡΡΠ²ΠΈΠ΅ ΠΏΠΎΡΡΠΎΡΠ½Π½ΡΡ ΠΈ Π²ΡΠ΅ΠΌΠ΅Π½Π½ΡΡ Π½Π°Π³ΡΡΠ·ΠΎΠΊ Π½Π°Π΄Π±ΡΠ½ΠΊΠ΅ΡΠ½ΠΎΠ³ΠΎ ΠΏΠ΅ΡΠ΅ΠΊΡΡΡΠΈΡ.
Π‘ΡΠ΅Π½ΠΊΠΈ Π±ΡΠ½ΠΊΠ΅ΡΠ° ΡΠ»Π΅Π΄ΡΠ΅Ρ ΡΠ°ΡΡΡΠΈΡΡΠ²Π°ΡΡ Π½Π° ΡΠ°ΡΡΡΠ³ΠΈΠ²Π°ΡΡΠΈΠ΅ ΡΡΠΈΠ»ΠΈΡ Π² Π³ΠΎΡΠΈΠ·ΠΎΠ½ΡΠ°Π»ΡΠ½ΠΎΠΌ ΠΈ ΡΠΊΠ°ΡΠ½ΠΎΠΌ Π½Π°ΠΏΡΠ°Π²Π»Π΅Π½ΠΈΡΡ ΠΈ ΠΈΠ·Π³ΠΈΠ±Π°ΡΡΠΈΠ΅ ΠΌΠΎΠΌΠ΅Π½ΡΡ ΠΎΡ ΠΌΠ΅ΡΡΠ½ΠΎΠ³ΠΎ ΠΈΠ·Π³ΠΈΠ±Π° ΠΈΠ· ΠΏΠ»ΠΎΡΠΊΠΎΡΡΠΈ ΡΡΠ°Π½ΠΎΠΊ. ΠΠΎΠ½ΡΡΡΡΠΊΡΠΈΠΈ Π±ΡΠ½ΠΊΠ΅ΡΠ° Π² ΡΠ΅Π»ΠΎΠΌ ΡΠ°ΡΡΡΠΈΡΡΠ²Π°ΡΡΡΡ Π½Π° ΠΎΠ±ΡΠΈΠΉ ΠΈΠ·Π³ΠΈΠ±, ΡΡΠΈΡΡΠ²Π°ΡΡΠΈΠΉ ΠΏΡΠΎΡΡΡΠ°Π½ΡΡΠ²Π΅Π½Π½ΡΡ ΡΠ°Π±ΠΎΡΡ Π±ΡΠ½ΠΊΠ΅ΡΠ°.
ΠΡΠΈ ΡΠ°ΡΡΠ΅ΡΠ΅ ΠΊΠΎΠ½ΡΡΡΡΠΊΡΠΈΠΉ Π±ΡΠ½ΠΊΠ΅ΡΠΎΠ² ΡΠ΄Π΅Π»ΡΠ½ΡΠΉ Π²Π΅Ρ g ΡΡΠΏΡΡΠ΅Π³ΠΎ ΠΌΠ°ΡΠ΅ΡΠΈΠ°Π»Π° Π½Π΅ΠΎΠ±Ρ ΠΎΠ΄ΠΈΠΌΠΎ ΠΏΡΠΈΠ½ΠΈΠΌΠ°ΡΡ ΠΏΠΎ ΡΠ΅Ρ Π½ΠΎΠ»ΠΎΠ³ΠΈΡΠ΅ΡΠΊΠΎΠΌΡ Π·Π°Π΄Π°Π½ΠΈΡ.
ΠΡΠ½ΠΊΠ΅ΡΠ° ΡΠ»Π΅Π΄ΡΠ΅Ρ ΠΏΡΠΎΠ΅ΠΊΡΠΈΡΠΎΠ²Π°ΡΡ, ΠΊΠ°ΠΊ ΠΏΡΠ°Π²ΠΈΠ»ΠΎ. ΠΆΠ΅Π»Π΅Π·ΠΎΠ±Π΅ΡΠΎΠ½Π½ΡΠΌΠΈ ΠΈΠ»ΠΈ ΡΡΠ°Π»Π΅ΠΆΠ΅Π»Π΅Π·ΠΎΠ±Π΅ΡΠΎΠ½Π½ΡΠΌΠΈ (ΠΈΠ· ΠΏΠ»ΠΎΡΠΊΠΈΡ ΠΆΠ΅Π»Π΅Π·ΠΎΠ±Π΅ΡΠΎΠ½Π½ΡΡ ΠΏΠ»ΠΈΡ ΠΈ ΡΡΠ°Π»ΡΠ½ΠΎΠ³ΠΎ ΠΊΠ°ΡΠΊΠ°ΡΠ°), ΠΈΠ»ΠΈ ΡΠ±ΠΎΡΠ½ΠΎ-ΠΌΠΎΠ½ΠΎΠ»ΠΈΡΠ½ΡΠΌΠΈ ΠΆΠ΅Π»Π΅Π·ΠΎΠ±Π΅ΡΠΎΠ½Π½ΡΠΌΠΈ. Π‘ΡΠ°Π»ΡΠ½ΡΠΌΠΈ Π΄ΠΎΠΏΡΡΠΊΠ°Π΅ΡΡΡ ΠΏΡΠΎΠ΅ΠΊΡΠΈΡΠΎΠ²Π°ΡΡ Π²ΠΎΡΠΎΠ½ΠΊΠΈ, ΡΡΠΆΠ°ΡΡΠΈΠ΅ΡΡ ΡΠ°ΡΡΠΈ Π±ΡΠ½ΠΊΠ΅ΡΠΎΠ², ΠΏΠ°ΡΠ°Π±ΠΎΠ»ΠΈΡΠ΅ΡΠΊΠΈΠ΅ (Π²ΠΈΡΡΡΠΈΠ΅ Π±ΡΠ½ΠΊΠ΅ΡΠ°), Π° ΡΠ°ΠΊΠΆΠ΅ Π±ΡΠ½ΠΊΠ΅ΡΠ°, ΠΊΠΎΡΠΎΡΡΠ΅ ΠΏΠΎ ΡΠ΅Ρ Π½ΠΎΠ»ΠΎΠ³ΠΈΡΠ΅ΡΠΊΠΈΠΌ ΡΡΠ»ΠΎΠ²ΠΈΡΠΌ ΠΏΠΎΠ΄Π²Π΅ΡΠ³Π°ΡΡΡΡ ΠΌΠ΅Ρ Π°Π½ΠΈΡΠ΅ΡΠΊΠΈΠΌ, Ρ ΠΈΠΌΠΈΡΠ΅ΡΠΊΠΈΠΌ ΠΈ ΡΠ΅ΠΌΠΏΠ΅ΡΠ°ΡΡΡΠ½ΡΠΌ β’ΠΎΠ·Π΄Π΅ΠΉΡΡΠ²ΠΈΡΠΌ ΡΡΠΏΡΡΠ΅Π³ΠΎ ΠΌΠ°ΡΠ΅ΡΠΈΠ°Π»Π° ΠΈ Π½Π΅ ΠΌΠΎΠ³ΡΡ Π±ΡΡΡ Π²ΡΠΏΠΎΠ»Π½Π΅Π½Ρ ΠΈΠ· ΠΆΠ΅Π»Π΅Π·ΠΎΠ±Π΅ΡΠΎΠ½Π°.
ΠΠ½ΡΡΡΠ΅Π½Π½ΠΈΠ΅ Π³ΡΠ°Π½ΠΈ ΡΠ³Π»ΠΎΠ² Π±ΡΠ½ΠΊΠ΅ΡΠΎΠ² Π΄Π»Ρ ΡΠ²ΡΠ·Π½ΡΡ ΠΌΠ°ΡΠ΅ΡΠΈΠ°Π»ΠΎΠ² ΡΠ»Π΅Π΄ΡΠ΅Ρ ΠΏΡΠΎΠ΅ΠΊΡΠΈΡΠΎΠ²Π°ΡΡ Ρ Π°ΡΡΠ°ΠΌΠΈ ΠΈΠ»ΠΈ Π·Π°ΠΊΡΡΠ³Π»Π΅Π½ΠΈΡΠΌΠΈ.
ΠΡΠ½ΠΊΠ΅ΡΠ° Π΄Π»Ρ ΠΏΡΠ»Π΅Π²ΠΈΠ΄Π½ΡΡ ΠΌΠ°ΡΠ΅ΡΠΈΠ°Π»ΠΎΠ² Π΄ΠΎΠ»ΠΆΠ½Ρ Π±ΡΡΡ Π³Π΅ΡΠΌΠ΅ΡΠΈΡΠ½ΡΠΌΠΈ, Π° Π±ΡΠ½ΠΊΠ΅ΡΠ°, ΠΏΡΠ΅Π΄Π½Π°Π·Π½Π°ΡΠ΅Π½Π½ΡΠ΅ Π΄Π»Ρ ΠΏΡΠ»ΡΡΠΈΡ ΠΌΠ°ΡΠ΅ΡΠΈΠ°Π»ΠΎΠ² (ΡΡΡ ΠΈΠ΅ ΠΊΡΡΠΊΠΎΠ²ΡΠ΅ ΠΌΠ°ΡΠ΅ΡΠΈΠ°Π»Ρ Π³ΠΎΡΠ½ΡΡ ΠΏΠΎΡΠΎΠ΄ ΠΌΠ°Π»ΠΎΠΉ ΠΊΡΠ΅ΠΏΠΎΡΡΠΈ, Π½Π°ΠΏΡΠΈΠΌΠ΅Ρ, ΠΈΠ·Π²Π΅ΡΡΠ½ΡΠΊ), β ΠΎΠ±ΠΎΡΡΠ΄ΠΎΠ²Π°Π½Ρ Π°ΡΠΏΠΈΡΠ°ΡΠΈΠΎΠ½Π½ΡΠΌΠΈ ΡΡΡΠ°Π½ΠΎΠ²ΠΊΠ°ΠΌΠΈ.
ΠΠ½ΡΡΡΠ΅Π½Π½ΠΈΠ΅ ΠΏΠΎΠ²Π΅ΡΡ Π½ΠΎΡΡΠΈ Π±ΡΠ½ΠΊΠ΅ΡΠΎΠ² ΡΠ»Π΅Π΄ΡΠ΅Ρ ΡΠ°Π·Π΄Π΅Π»ΡΡΡ Π½Π° ΡΡΠ°ΡΡΠΊΠΈ, ΠΏΠΎΠ΄Π²Π΅ΡΠ³Π°ΡΡΠΈΠ΅ΡΡ ΠΈΠ·Π½ΠΎΡΡ (I ΠΈ II Π·ΠΎΠ½Ρ) ΠΈ Π½Π΅ ΠΏΠΎΠ΄Π²Π΅ΡΠ³Π°ΡΡΠΈΠ΅ΡΡ ΠΈΠ·Π½ΠΎΡΡ (III Π·ΠΎΠ½Π°). I Π·ΠΎΠ½Π° β ΡΡΠ°ΡΡΠΎΠΊ, ΠΏΠΎΠ΄Π²Π΅ΡΠ³Π°ΡΡΠΈΠΉΡΡ ΡΠ΄Π°ΡΠ°ΠΌ ΠΏΠΎΡΠΎΠΊΠ° ΡΡΠΏΡΡΠ΅Π³ΠΎ ΠΌΠ°ΡΠ΅ΡΠΈΠ°Π»Π° ΠΏΡΠΈ Π·Π°Π³ΡΡΠ·ΠΊΠ΅ Π±ΡΠ½ΠΊΠ΅ΡΠ° ΠΈ ΠΈΡΡΠΈΡΠ°Π½ΠΈΡ ΠΏΡΠΈ Π΅Π³ΠΎ ΡΠ°Π·Π³ΡΡΠ·ΠΊΠ΅. I Π·ΠΎΠ½Ρ ΡΠ»Π΅Π΄ΡΠ΅Ρ Π·Π°ΡΠΈΡΠ°ΡΡ, ΠΊΠ°ΠΊ ΠΏΡΠ°Π²ΠΈΠ»ΠΎ ΠΈΡΠΏΠΎΠ»ΡΠ·ΡΡ ΠΏΡΠΈΠ½ΡΠΈΠΏ ΡΠ°ΠΌΠΎΠ·Π°ΡΠΈΡΡ, ΠΈΠ»ΠΈ ΠΈΠ·Π½ΠΎΡΠΎΡΡΠΎΠΉΠΊΠΎΠΉ Π·Π°ΡΠΈΡΡ Π½Π° ΡΠΏΡΡΠ³ΠΎΠΌ ΠΎΡΠ½ΠΎΠ²Π°Π½ΠΈΠΈ ΠΈΠ»ΠΈ ΡΠ΅Π·ΠΈΠ½ΠΎΠΉ. II Π·ΠΎΠ½Π° β ΡΡΠ°ΡΡΠΎΠΊ, ΠΏΠΎΠ΄Π²Π΅ΡΠ³Π°ΡΡΠΈΠΉΡΡ ΠΈΡΡΠΈΡΠ°Π½ΠΈΡ ΡΡΠΏΡΡΠΈΠΌ ΠΌΠ°ΡΠ΅ΡΠΈΠ°Π»ΠΎΠΌ Π² ΠΏΡΠΎΡΠ΅ΡΡΠ΅ ΡΠ°Π·Π³ΡΡΠ·ΠΊΠΈ Π±ΡΠ½ΠΊΠ΅ΡΠ°. II Π·ΠΎΠ½Ρ ΡΠ»Π΅Π΄ΡΠ΅Ρ Π·Π°ΡΠΈΡΠ°ΡΡ ΠΊΠ°ΠΌΠ΅Π½Π½ΡΠΌ Π»ΠΈΡΡΠ΅ΠΌ, ΡΠ»Π°ΠΊΠΎΡΠΈΡΠ°Π»Π»ΠΎΠΌ, ΠΏΠΎΠ»ΠΈΠΌΠ΅ΡΠ½ΡΠΌΠΈ ΠΌΠ°ΡΠ΅ΡΠΈΠ°Π»Π°ΠΌΠΈ, ΡΠ΅Π·ΠΈΠ½ΠΎΠΉ ΠΈ Π΄ΡΡΠ³ΠΈΠΌΠΈ ΠΌΠ°ΡΠ΅ΡΠΈΠ°Π»Π°ΠΌΠΈ, Π° ΠΏΡΠΈ ΡΠ΅ΠΌΠΏΠ΅ΡΠ°ΡΡΡΠ΅ ΡΡΠΏΡΡΠ΅Π³ΠΎ ΠΌΠ°ΡΠ΅ΡΠΈΠ°Π»Π° ΡΠ²ΡΡΠ΅ 50 Β°Π‘ β ΡΠ»Π°ΠΊΠΎΠΊΠ°ΠΌΠ΅Π½Π½ΡΠΌ ΠΈ ΠΊΠ°ΠΌΠ΅Π½Π½ΡΠΌ Π»ΠΈΡΡΠ΅ΠΌ ΡΠ΅ΡΠΌΠΎΡΡΠΎΠΉΠΊΠΈΡ ΡΠΎΡΡΠ°Π²ΠΎΠ². III Π·ΠΎΠ½Π° β ΡΡΠ°ΡΡΠΎΠΊ, Π½Π΅ ΡΡΠ΅Π±ΡΡΡΠΈΠΉ Π·Π°ΡΠΈΡΡ.
ΠΡΠΈ ΡΠΎΡΠ΅ΡΠ°Π½ΠΈΠΈ ΠΈΡΡΠΈΡΠ°ΡΡΠ΅Π³ΠΎ Π²ΠΎΠ·Π΄Π΅ΠΉΡΡΠ²ΠΈΡ, Π²ΡΡΠΎΠΊΠΎΠΉ ΡΠ΅ΠΌΠΏΠ΅ΡΠ°ΡΡΡΡ ΠΈ Ρ ΠΈΠΌΠΈΡΠ΅ΡΠΊΠΎΠΉ Π°Π³ΡΠ΅ΡΡΠΈΠΈ ΡΡΠΏΡΡΠ΅Π³ΠΎ ΠΌΠ°ΡΠ΅ΡΠΈΠ°Π»Π° Π²Π½ΡΡΡΠ΅Π½Π½ΠΈΠ΅ ΠΏΠΎΠ²Π΅ΡΡ Π½ΠΎΡΡΠΈ Π±ΡΠ½ΠΊΠ΅ΡΠΎΠ² ΡΠ»Π΅Π΄ΡΠ΅Ρ Π·Π°ΡΠΈΡΠ°ΡΡ ΠΏΠ»ΠΈΡΠ°ΠΌΠΈ ΠΈΠ· ΡΠ»Π°ΠΊΠΎΠΊΠ°ΠΌΠ΅Π½Π½ΠΎΠ³ΠΎ Π»ΠΈΡΡΡ, ΠΈΠ·Π½ΠΎΡΠΎΡΡΠΎΠΉΠΊΠΎΠ³ΠΎ ΠΈ ΠΆΠ°ΡΠΎΡΡΠΎΠΉΠΊΠΎΠ³ΠΎ Π±Π΅ΡΠΎΠ½Π° (Ρ Π·Π°ΠΏΠΎΠ»Π½Π΅Π½ΠΈΠ΅ΠΌ ΡΠ²ΠΎΠ² ΡΠ°ΡΡΠ²ΠΎΡΠΎΠΌ ΠΊΠΈΡΠ»ΠΎΡΠΎΡΡΠΎΠΉΠΊΠΈΡ ΠΈ ΠΆΠ°ΡΠΎΡΡΠΎΠΉΠΊΠΈΡ ΡΠΎΡΡΠ°Π²ΠΎΠ²), Π° ΡΠ°ΠΊΠΆΠ΅ Π² ΠΎΡΠ΄Π΅Π»ΡΠ½ΡΡ ΡΠ»ΡΡΠ°ΡΡ Π»ΠΈΡΡΠ°ΠΌΠΈ ΠΈΠ· ΡΠΎΠΎΡΠ²Π΅ΡΡΡΠ²ΡΡΡΠΈΡ Π²ΠΈΠ΄ΠΎΠ² ΡΡΠ°Π»Π΅ΠΉ (ΡΠ΅ΡΠΌΠΎΡΡΠΎΠΉΠΊΠΈΡ ΠΈ Π΄Ρ.).
ΠΡΠΈ ΡΠΊΡΠΏΠ»ΡΠ°ΡΠ°ΡΠΈΠΈ Π±ΡΠ½ΠΊΠ΅ΡΠΎΠ² Π² Π°Π³ΡΠ΅ΡΡΠΈΠ²Π½ΠΎΠΉ ΠΈ Π³Π°Π·ΠΎΠ²ΠΎΠΉ ΡΡΠ΅Π΄Π΅ ΠΈΡ Π½Π°ΡΡΠΆΠ½ΡΠ΅ ΠΏΠΎΠ²Π΅ΡΡ Π½ΠΎΡΡΠΈ ΡΠ»Π΅Π΄ΡΠ΅Ρ Π·Π°ΡΠΈΡΠ°ΡΡ ΠΎΡ ΠΊΠΎΡΡΠΎΠ·ΠΈΠΈ Π² ΡΠΎΠΎΡΠ²Π΅ΡΡΡΠ²ΠΈΠΈ Ρ ΡΡΠ΅Π±ΠΎΠ²Π°Π½ΠΈΡΠΌΠΈ Π‘ΠΠΈΠ 2.03.11-85. ΠΡΠΈ ΠΏΡΠΎΠ΅ΠΊΡΠΈΡΠΎΠ²Π°Π½ΠΈΠΈ Π±ΡΠ½ΠΊΠ΅ΡΠΎΠ² Π΄Π»Ρ Π²Π»Π°ΠΆΠ½ΡΡ ΡΡΠΏΡΡΠΈΡ ΠΌΠ°ΡΠ΅ΡΠΈΠ°Π»ΠΎΠ², ΡΠ°ΡΠΏΠΎΠ»Π°Π³Π°Π΅ΠΌΡΡ Π² Π½Π΅ΠΎΡΠ°ΠΏΠ»ΠΈΠ²Π°Π΅ΠΌΡΡ ΠΏΠΎΠΌΠ΅ΡΠ΅Π½ΠΈΡΡ , Π½Π΅ΠΎΠ±Ρ ΠΎΠ΄ΠΈΠΌΠΎ ΠΏΡΠ΅Π΄ΡΡΠΌΠ°ΡΡΠΈΠ²Π°ΡΡ ΡΡΡΠ΅ΠΊΡΠΈΠ²Π½ΡΠΉ ΠΎΠ±ΠΎΠ³ΡΠ΅Π² ΡΡΠ΅Π½ Π±ΡΠ½ΠΊΠ΅ΡΠΎΠ² Π² ΡΠ΅Π»ΡΡ ΠΏΡΠ΅Π΄ΠΎΡΠ²ΡΠ°ΡΠ΅Π½ΠΈΡ ΡΠΌΠ΅ΡΠ·Π°Π½ΠΈΡ ΠΌΠ°ΡΠ΅ΡΠΈΠΌΠ° Π² Π±ΡΠ½ΠΊΠ΅ΡΠ΅.
Π£ΡΠ΅ΠΏΠ»ΠΈΡΠ΅Π»Ρ ΡΡΠ΅Π½ Π±ΡΠ½ΠΊΠ΅ΡΠΎΠ² Π΄Π»Ρ ΠΏΡΠ»Π΅Π²ΠΈΠ΄Π½ΠΎΠ³ΠΎ ΠΌΠ°ΡΠ΅ΡΠΈΠ°Π»Π° Π²ΠΎ ΠΈΠ·Π±Π΅ΠΆΠ°Π½ΠΈΠ΅ ΠΊΠΎΠ½Π΄Π΅Π½ΡΠ°ΡΠΈΠΈ Π²ΠΎΠ΄ΡΠ½ΡΡ ΠΏΠ°ΡΠΎΠ² ΡΠ»Π΅Π΄ΡΠ΅Ρ ΡΠ°ΡΠΏΠΎΠ»Π°Π³Π°ΡΡ ΡΠ½Π°ΡΡΠΆΠΈ ΠΈ Π²ΡΠΏΠΎΠ»Π½ΡΡΡ ΠΈΠ· Π½Π΅ΡΠ³ΠΎΡΠ°Π΅ΠΌΡΡ ΠΌΠ°ΡΠ΅ΡΠΈΠ°Π»ΠΎΠ².
ΠΡΠΈ ΠΏΡΠΎΠ΅ΠΊΡΠΈΡΠΎΠ²Π°Π½ΠΈΠΈ Π±ΡΠ½ΠΊΠ΅ΡΠΎΠ² Π΄Π»Ρ ΡΠ²ΡΠ·Π½ΡΡ ΠΌΠ°ΡΠ΅ΡΠΈΠ°Π»ΠΎΠ², ΠΏΠΎΡΡΡΠΏΠ°ΡΡΠΈΡ Π² Π½Π°Π³ΡΠ΅ΡΠΎΠΌ ΠΈΠ»ΠΈ ΡΠΌΠ΅ΡΠ·ΡΠ΅ΠΌΡΡ ΡΠΎΡΡΠΎΡΠ½ΠΈΠΈ, Π½Π΅ΠΎΠ±Ρ ΠΎΠ΄ΠΈΠΌΠΎ ΠΏΡΠ΅Π΄ΡΡΠΌΠ°ΡΡΠΈΠ²Π°ΡΡ ΡΠ΅ΠΏΠ»ΠΎΠΈΠ·ΠΎΠ»ΡΡΠΈΡ ΡΡΠ΅Π½ Π±ΡΠ½ΠΊΠ΅ΡΠΎΠ² Π² ΡΠΎΠΎΡΠ²Π΅ΡΡΡΠ²ΠΈΠΈ Ρ ΡΠ΅ΠΏΠ»ΠΎΡΠ΅Ρ Π½ΠΈΡΠ΅ΡΠΊΠΈΠΌ ΡΠ°ΡΡΠ΅ΡΠΎΠΌ, ΠΈΡΠΊΠ»ΡΡΠ°ΡΡΡΡ ΠΊΠΎΠ½Π΄Π΅Π½ΡΠ°ΡΠΈΡ Π²ΠΎΠ΄ΡΠ½ΡΡ ΠΏΠ°ΡΠΎΠ² ΠΏΡΠΈ Π½Π°Π³ΡΠ΅ΡΠΎΠΌ ΠΌΠ°ΡΠ΅ΡΠΈΠ°Π»Π΅, Π° ΡΠ°ΠΊΠΆΠ΅ ΠΏΡΠΈΠΌΠ΅ΡΠ·Π°Π½ΠΈΠ΅ ΠΊ ΡΡΠ΅Π½Π°ΠΌ ΡΠΌΠ΅ΡΠ·ΡΠ΅Π³ΠΎΡΡ ΠΌΠ°ΡΠ΅ΡΠΈΠ°Π»Π°.
ΠΡΠ½ΠΊΠ΅ΡΠ°, ΠΊΠ°ΠΊ ΠΏΡΠ°Π²ΠΈΠ»ΠΎ, Π΄ΠΎΠ»ΠΆΠ½Ρ ΠΈΠΌΠ΅ΡΡ ΠΏΠ΅ΡΠ΅ΠΊΡΡΡΠΈΡ ΠΈΠ· Π½Π΅ΡΠ³ΠΎΡΠ°Π΅ΠΌΡΡ ΠΌΠ°ΡΠ΅ΡΠΈΠ°Π»ΠΎΠ² Ρ ΠΏΡΠΎΠ΅ΠΌΠ°ΠΌΠΈ Π΄Π»Ρ Π·Π°Π³ΡΡΠ·ΠΊΠΈ. ΠΡΠ»ΠΈ Π·Π°Π³ΡΡΠ·ΠΊΠ° ΠΏΡΠΎΠΈΠ·Π²ΠΎΠ΄ΠΈΡΡΡ ΡΡΠ΅Π΄ΡΡΠ²Π°ΠΌΠΈ Π½Π΅ Π½Π΅ΠΏΡΠ΅ΡΡΠ²Π½ΠΎΠ³ΠΎ ΡΡΠ°Π½ΡΠΏΠΎΡΡΠ° (Π²Π°Π³ΠΎΠ½Ρ, Π°Π²ΡΠΎΠΌΠ°ΡΠΈΠ½Ρ, Π³ΡΠ΅ΠΉΡΠ΅ΡΡ), Π΄ΠΎΠΏΡΡΠΊΠ°Π΅ΡΡΡ Π²ΡΠΏΠΎΠ»Π½ΡΡΡ Π±ΡΠ½ΠΊΠ΅Ρ Π±Π΅Π· ΠΏΠ΅ΡΠ΅ΠΊΡΡΡΠΈΡ, Π½ΠΎ Ρ ΠΎΠ±ΡΠ·Π°ΡΠ΅Π»ΡΠ½ΡΠΌ ΡΡΡΡΠΎΠΉΡΡΠ²ΠΎΠΌ ΡΠΏΠ»ΠΎΡΠ½ΠΎΠ³ΠΎ ΠΎΠ³ΡΠ°ΠΆΠ΄Π΅Π½ΠΈΡ Π²ΡΡΠΎΡΠΎΠΉ Π½Π΅ ΠΌΠ΅Π½Π΅Π΅ 1 ΠΌ Ρ Π±ΠΎΠΊΠΎΠ² ΠΈ ΡΠΎ ΡΡΠΎΡΠ°Π½Ρ, ΠΏΡΠΎΡΠΈΠ²ΠΎΠΏΠΎΠ»ΠΎΠΆΠ½ΠΎΠΉ Π·Π°Π³ΡΡΠ·ΠΊΠ΅. ΠΠ΅ΠΎΠ±Ρ ΠΎΠ΄ΠΈΠΌΠΎΡΡΡ ΡΡΡΡΠΎΠΉΡΡΠ²Π° ΡΡΠ°Π»ΡΠ½ΡΡ ΡΠ΅ΡΠ΅ΡΠΎΠΊ Π΄Π»Ρ ΠΏΠ΅ΡΠ΅ΠΊΡΡΡΠΈΡ ΡΠ΅Ρ Π½ΠΎΠ»ΠΎΠ³ΠΈΡΠ΅ΡΠΊΠΈΡ ΠΏΡΠΎΠ΅ΠΌΠΎΠ² ΠΈ ΡΠ°Π·ΠΌΠ΅Ρ ΡΡΠ΅Π΅ΠΊ ΡΠ΅ΡΠ΅ΡΠΎΠΊ ΠΎΠΏΡΠ΅Π΄Π΅Π»ΡΡΡΡΡ ΡΠ΅Ρ Π½ΠΎΠ»ΠΎΠ³ΠΈΡΠ΅ΡΠΊΠΈΠΌ Π·Π°Π΄Π°Π½ΠΈΠ΅ΠΌ.
Π Π±ΡΠ½ΠΊΠ΅ΡΠ°Ρ Π΄Π»Ρ ΠΏΡΠ»Π΅Π²ΠΈΠ΄Π½ΡΡ ΠΌΠ°ΡΠ΅ΡΠΈΠ°Π»ΠΎΠ² Π½Π΅ΠΎΠ±Ρ ΠΎΠ΄ΠΈΠΌΠΎ ΠΏΡΠ΅Π΄ΡΡΠΌΠ°ΡΡΠΈΠ²Π°ΡΡ ΡΠ²Π΅ΡΡ Ρ ΠΏΠ΅ΡΠ΅ΠΊΡΡΡΠΈΡ ΠΌΠΎΠ½ΠΎΠ»ΠΈΡΠ½ΡΡ Π°ΡΠΌΠΈΡΠΎΠ²Π°Π½Π½ΡΡ ΡΡΡΠΆΠΊΡ ΡΠΎΠ»ΡΠΈΠ½ΠΎΠΉ 50 ΠΌΠΌ, Π΅ΡΠ»ΠΈ ΡΠΎΠ»ΡΠΈΠ½Π° ΠΏΠ»ΠΈΡ Π° ΠΌΠ΅ΡΡΠ΅ ΡΡΡΠΊΠ° 100 ΠΌΠΌ ΠΈ ΠΌΠ΅Π½Π΅Π΅.
Π Π±ΡΠ½ΠΊΠ΅ΡΠ°Ρ , ΠΏΡΠ΅Π΄Π½Π°Π·Π½Π°ΡΠ΅Π½Π½ΡΡ Π΄Π»Ρ Π³ΠΎΡΡΡΠΈΡ ΡΡΠΏΡΡΠΈΡ ΠΌΠ°ΡΠ΅ΡΠΈΠ°Π»ΠΎΠ², ΠΌΠ΅ΠΆΠ΄Ρ ΠΈΠ·Π½ΠΎΡΠΎΡΡΠΎΠΉΠΊΠΎΠΉ Π·Π°ΡΠΈΡΠΎΠΉ ΠΈ Π½Π΅ΡΡΡΠ΅ΠΉ ΠΊΠΎΠ½ΡΡΡΡΠΊΡΠΈΠ΅ΠΉ ΡΠ»Π΅Π΄ΡΠ΅Ρ ΠΏΡΠ΅Π΄ΡΡΠΌΠ°ΡΡΠΈΠ²Π°ΡΡ ΡΠ΅ΡΠΌΠΎΠΈΠ·ΠΎΠ»ΡΡΠΈΡ ΠΈΠ· Π½Π΅ΡΠ³ΠΎΡΠ°Π΅ΠΌΡΡ ΠΌΠ°ΡΠ΅ΡΠΈΠ°Π»ΠΎΠ²: Π² ΡΡΠ°Π»ΡΠ½ΡΡ Π±ΡΠ½ΠΊΠ΅ΡΠ°Ρ β ΠΏΡΠΈ ΡΠ΅ΠΌΠΏΠ΅ΡΠ°ΡΡΡΠ΅ Π½Π°Π³ΡΠ΅Π²Π° ΡΠ²ΡΡΠ΅ 300 Β°Π‘, Π° Π² ΠΆΠ΅Π»Π΅Π·ΠΎΠ±Π΅ΡΠΎΠ½Π½ΡΡ β ΡΠ²ΡΡΠ΅ 100 Β°Π‘.
Π Π±ΡΠ½ΠΊΠ΅ΡΠ°Ρ , ΠΏΡΠ΅Π΄Π½Π°Π·Π½Π°ΡΠ΅Π½Π½ΡΡ Π΄Π»Ρ Ρ ΡΠ°Π½Π΅Π½ΠΈΡ ΡΡΠΏΡΡΠΈΡ ΠΌΠ°ΡΠ΅ΡΠΈΠ°Π»ΠΎΠ², Π²ΡΠ΄Π΅Π»ΡΡΡΠΈΡ Π²ΠΎΡΠΏΠ»Π°ΠΌΠ΅Π½ΡΡΡΠΈΠ΅ΡΡ Π³Π°Π·Ρ (Π½Π°ΠΏΡΠΈΠΌΠ΅Ρ, ΠΌΠ΅ΡΠ°Π½ ΠΈΠ· ΠΊΠ°ΠΌΠ΅Π½Π½ΠΎΠ³ΠΎ ΡΠ³Π»Ρ), ΠΊΠΎΠ½ΡΡΡΡΠΊΡΠΈΡ ΠΏΠ΅ΡΠ΅ΠΊΡΡΡΠΈΡ Π½Π΅ Π΄ΠΎΠ»ΠΆΠ½Π° ΠΈΠΌΠ΅ΡΡ Π²ΡΡΡΡΠΏΠ°ΡΡΠΈΡ Π²Π½ΠΈΠ· ΡΠ΅Π±Π΅Ρ.
Π ΠΏΠ΅ΡΠ΅ΠΊΡΡΡΠΈΡΡ Π±ΡΠ½ΠΊΠ΅ΡΠΎΠ² Π΄ΠΎΠ»ΠΆΠ½Ρ Π±ΡΡΡ ΡΡΡΡΠΎΠ΅Π½Ρ Π»ΡΠΊΠΈ, Π·Π°ΠΊΡΡΠ²Π°Π΅ΠΌΡΠ΅ Π·Π°ΠΏΠΎΠ΄Π»ΠΈΡΠΎ Ρ ΠΏΠ΅ΡΠ΅ΠΊΡΡΡΠΈΠ΅ΠΌ ΠΌΠ΅ΡΠ°Π»Π»ΠΈΡΠ΅ΡΠΊΠΈΠΌΠΈ ΠΊΡΡΡΠΊΠ°ΠΌΠΈ. Π Π½Π°Π΄Π±ΡΠ½ΠΊΠ΅ΡΠ½ΠΎΠΌ ΠΏΠΎΠΌΠ΅ΡΠ΅Π½ΠΈΠΈ Π΄ΠΎΠ»ΠΆΠ½Ρ ΠΏΡΠ΅Π΄ΡΡΠΌΠ°ΡΡΠΈΠ²Π°ΡΡΡΡ ΠΏΠΎΠ΄ΡΠ΅ΠΌΠ½ΠΎ-ΡΡΠ°Π½ΡΠΏΠΎΡΡΠ½ΡΠ΅ ΡΡΡΡΠΎΠΉΡΡΠ²Π°, Π° Π²Π½ΡΡΡΠΈ Π±ΡΠ½ΠΊΠ΅ΡΠΎΠ² ΡΠ½ΠΈΠ·Ρ ΠΏΠ΅ΡΠ΅ΠΊΡΡΡΠΈΠΉ β ΠΏΠ΅ΡΠ»ΠΈ Π΄Π»Ρ ΠΊΡΠ΅ΠΏΠ»Π΅Π½ΠΈΡ ΡΠ°Π»Π΅ΠΉ ΠΈ Π΄ΡΡΠ³ΠΈΡ ΠΌΠΎΠ½ΡΠ°ΠΆΠ½ΡΡ ΡΡΠ΅Π΄ΡΡΠ².
ΠΡΠ½ΠΊΠ΅ΡΠ° Π΄ΠΎΠ»ΠΆΠ½Ρ ΠΎΡΠ½Π°ΡΠ°ΡΡΡΡ ΡΡΡΡΠΎΠΉΡΡΠ²Π°ΠΌΠΈ Π΄Π»Ρ ΠΌΠ΅Ρ Π°Π½ΠΈΡΠ΅ΡΠΊΠΎΠΉ ΠΎΡΠΈΡΡΠΊΠΈ ΡΡΠ΅Π½ ΠΈ ΡΠ΄Π°Π»Π΅Π½ΠΈΡ Π·Π°Π²ΠΈΡΡΠ΅Π³ΠΎ ΡΡΠΏΡΡΠ΅Π³ΠΎ ΠΌΠ°ΡΠ΅ΡΠΈΠ°Π»Π°, ΡΡΠΎΠ±Ρ ΠΈΡΠΊΠ»ΡΡΠ°Π»Π°ΡΡ Π½Π΅ΠΎΠ±Ρ ΠΎΠ΄ΠΈΠΌΠΎΡΡΡ ΡΠΏΡΡΠΊΠ° Π»ΡΠ΄Π΅ΠΉ Π² Π±ΡΠ½ΠΊΠ΅ΡΠ°.
Π‘ΠΠΠΠ‘Π« Π Π‘ΠΠΠΠ‘ΠΠ«Π ΠΠΠ ΠΠ£Π‘Π ΠΠΠ― Π₯Π ΠΠΠΠΠΠ― Π‘Π«ΠΠ£Π§ΠΠ₯ ΠΠΠ’ΠΠ ΠΠΠΠΠ.
Π‘ΠΈΠ»ΠΎΡΡ Π΄Π»Ρ Ρ ΡΠ°Π½Π΅Π½ΠΈΡ Π·Π΅ΡΠ½Π° ΠΈ ΠΏΡΠΎΠ΄ΡΠΊΡΠΎΠ² Π΅Π³ΠΎ ΠΏΠ΅ΡΠ΅ΡΠ°Π±ΠΎΡΠΊΠΈ ΡΠ»Π΅Π΄ΡΠ΅Ρ ΠΏΡΠΎΠ΅ΠΊΡΠΈΡΠΎΠ²Π°ΡΡ Π² ΡΠΎΠΎΡΠ²Π΅ΡΡΡΠ²ΠΈΠΈ Ρ ΡΡΠ΅Π±ΠΎΠ²Π°Π½ΠΈΡΠΌΠΈ Π‘ΠΠΈΠ 2.10.05-85.
Π€ΠΎΡΠΌΡ, ΡΠ°Π·ΠΌΠ΅ΡΡ ΠΈ ΡΠ°ΡΠΏΠΎΠ»ΠΎΠΆΠ΅Π½ΠΈΡ ΡΠΈΠ»ΠΎΡΠΎΠ² Π² ΠΏΠ»Π°Π½Π΅ ΡΠ»Π΅Π΄ΡΠ΅Ρ ΠΏΡΠΈΠ½ΠΈΠΌΠ°ΡΡ Π² ΡΠΎΠΎΡΠ²Π΅ΡΡΡΠ²ΠΈΠΈ Ρ ΡΡΠ΅Π±ΠΎΠ²Π°Π½ΠΈΡΠΌΠΈ ΡΠ΅Ρ Π½ΠΎΠ»ΠΎΠ³ΠΈΠΈ ΠΏΡΠΎΠΈΠ·Π²ΠΎΠ΄ΡΡΠ²Π°, ΡΠ½ΠΈΡΠΈΠΊΠ°ΡΠΈΠΈ, Π³ΡΡΠ½ΡΠΎΠ²ΡΠΌΠΈ ΠΈ ΡΠ΅ΠΌΠΏΠ΅ΡΠ°ΡΡΡΠ½ΡΠΌΠΈ ΡΡΠ»ΠΎΠ²ΠΈΡΠΌΠΈ, Π° ΡΠ°ΠΊΠΆΠ΅ ΠΈΡΡ ΠΎΠ΄Ρ ΠΈΠ· ΡΠ΅Π·ΡΠ»ΡΡΠ°ΡΠΎΠ² ΡΠ΅Ρ Π½ΠΈΠΊΠΎ-ΡΠΊΠΎΠ½ΠΎΠΌΠΈΡΠ΅ΡΠΊΠΈΡ ΡΠΎΠΏΠΎΡΡΠ°Π²Π»Π΅Π½ΠΈΠΉ ΠΈ Ρ ΡΡΠ΅ΡΠΎΠΌ Π°ΡΡ ΠΈΡΠ΅ΠΊΡΡΡΠ½ΠΎ-ΠΊΠΎΠΌΠΏΠΎΠ·ΠΈΡΠΈΠΎΠ½Π½ΡΡ ΡΡΠ΅Π±ΠΎΠ²Π°Π½ΠΈΠΉ. ΠΠΎΠΏΡΡΠΊΠ°Π΅ΡΡΡ Π±Π»ΠΎΠΊΠΈΡΠΎΠ²ΠΊΠ° ΡΠΈΠ»ΠΎΡΠ½ΡΡ ΠΊΠΎΡΠΏΡΡΠΎΠ² Ρ ΠΎΠ±ΡΠ»ΡΠΆΠΈΠ²Π°ΡΡΠΈΠΌΠΈ Π·Π΄Π°Π½ΠΈΡΠΌΠΈ II ΠΊΠ°ΡΠ΅Π³ΠΎΡΠΈΠΈ ΠΎΠ³Π½Π΅ΡΡΠΎΠΉΠΊΠΎΡΡΠΈ. ΠΡΠΈ ΡΡΠΎΠΌ Π΄ΠΎΠ»ΠΆΠ½Π° Π±ΡΡΡ ΡΡΡΠ΅Π½Π° ΡΠ°Π·Π½ΠΎΡΡΡ ΠΎΡΠ°Π΄ΠΎΠΊ ΡΡΠ½Π΄Π°ΠΌΠ΅Π½ΡΠΎΠ² ΡΠΈΠ»ΠΎΡΠΎΠ² ΠΈ ΠΏΡΠΈΠΌΡΠΊΠ°ΡΡΠΈΡ Π·Π΄Π°Π½ΠΈΠΉ.
ΠΡΠΈ Π΄ΠΈΠ°ΠΌΠ΅ΡΡΠ΅ Π±ΠΎΠ»Π΅Π΅ 12 ΠΌ ΡΠΈΠ»ΠΎΡΡ ΡΠ»Π΅Π΄ΡΠ΅Ρ ΠΏΡΠΎΠ΅ΠΊΡΠΈΡΠΎΠ²Π°ΡΡ, ΠΊΠ°ΠΊ ΠΏΡΠ°Π²ΠΈΠ»ΠΎ, ΠΎΡΠ΄Π΅Π»ΡΠ½ΠΎ ΡΡΠΎΡΡΠΈΠΌΠΈ.
Π€ΠΎΡΠΌΠ° ΠΎΡΠ΄Π΅Π»ΡΠ½ΠΎΠ³ΠΎ ΡΠΈΠ»ΠΎΡΠ° Π² ΠΏΠ»Π°Π½Π΅ ΠΏΡΠΈΠ½ΠΈΠΌΠ°Π΅ΡΡΡ. ΠΊΠ°ΠΊ ΠΏΡΠ°Π²ΠΈΠ»ΠΎ, ΠΊΡΡΠ³Π»ΠΎΠΉ. ΠΠΎΠΏΡΡΠΊΠ°Π΅ΡΡΡ ΠΏΡΠΈ ΡΠΎΠΎΡΠ²Π΅ΡΡΡΠ²ΡΡΡΠ΅ΠΌ ΠΎΠ±ΠΎΡΠ½ΠΎΠ²Π°Π½ΠΈΠΈ ΠΏΡΠΈΠ½ΠΈΠΌΠ°ΡΡ ΡΠΈΠ»ΠΎΡΡ ΠΊΠ²Π°Π΄ΡΠ°ΡΠ½ΡΠΌΠΈ ΠΈ ΠΌΠ½ΠΎΠ³ΠΎΠ³ΡΠ°Π½Π½ΡΠΌΠΈ.
ΠΡΠΈ ΠΏΡΠΎΠ΅ΠΊΡΠΈΡΠΎΠ²Π°Π½ΠΈΠΈ ΡΠΈΠ»ΠΎΡΠ½ΡΡ ΠΊΠΎΡΠΏΡΡΠΎΠ² ΡΠ»Π΅Π΄ΡΠ΅Ρ, ΠΊΠ°ΠΊ ΠΏΡΠ°Π²ΠΈΠ»ΠΎ, ΠΏΡΠΈΠ½ΠΈΠΌΠ°ΡΡ: ΡΠ΅ΡΠΊΠΈ ΡΠ°Π·Π±ΠΈΠ²ΠΎΡΠ½ΡΡ ΠΎΡΠ΅ΠΉ, ΠΏΡΠΎΡ ΠΎΠ΄ΡΡΠΈΡ ΡΠ΅ΡΠ΅Π· ΡΠ΅Π½ΡΡΡ ΡΠ±Π»ΠΎΠΊΠΈΡΠΎΠ²Π°Π½Π½ΡΡ ΡΠΈΠ»ΠΎΡΠΎΠ², 3Ρ 3, 6Ρ 6 ΠΈ 12Ρ 12 ΠΌ; Π½Π°ΡΡΠΆΠ½ΡΠ΅ Π΄ΠΈΠ°ΠΌΠ΅ΡΡΡ ΠΊΡΡΠ³Π»ΡΡ ΡΠΈΠ»ΠΎΡΠΎΠ² β 3, 6, 12, 18 ΠΈ 24 ΠΌ; ΡΠ°Π·ΠΌΠ΅ΡΡ Π² ΠΎΡΡΡ ΡΡΠ΅Π½ ΠΊΠ²Π°Π΄ΡΠ°ΡΠ½ΡΡ ΡΠΈΠ»ΠΎΡΠΎΠ² β 3Ρ 3 ΠΌ; Π²ΡΡΠΎΡΡ ΡΡΠ΅Π½ ΡΠΈΠ»ΠΎΡΠΎΠ², Π° ΡΠ°ΠΊΠΆΠ΅ ΠΏΠΎΠ΄ΡΠΈΠ»ΠΎΡΠ½ΡΡ ΠΈ Π½Π°Π΄ΡΠΈΠ»ΠΎΡΠ½ΡΡ ΡΡΠ°ΠΆΠ΅ΠΉ β ΠΊΡΠ°ΡΠ½ΡΠΌΠΈ 0,6 ΠΌ.
ΠΠ΅ΡΠ°Π»Π»ΠΈΡΠ΅ΡΠΊΠΈΠ΅ ΡΠΈΠ»ΠΎΡΡ Π΄Π»ΠΈΠ½ΠΎΠΉ Π΄ΠΎ 48 ΠΌ Π΄ΠΎΠΏΡΡΠΊΠ°Π΅ΡΡΡ ΠΏΡΠΎΠ΅ΠΊΡΠΈΡΠΎΠ²Π°ΡΡ Π±Π΅Π· Π΄Π΅ΡΠΎΡΠΌΠ°ΡΠΈΠΎΠ½Π½ΡΡ ΡΠ²ΠΎΠ². ΠΡΠΈ Π½Π΅ΡΠΊΠ°Π»ΡΠ½ΡΡ Π³ΡΡΠ½ΡΠ°Ρ ΠΎΡΠ½ΠΎΠ²Π°Π½ΠΈΡ ΠΎΡΠ½ΠΎΡΠ΅Π½ΠΈΠ΅ Π΄Π»ΠΈΠΌΡ ΡΠΈΠ»ΠΎΡΠ½ΠΎΠ³ΠΎ ΠΊΠΎΡΠΏΡΡΠ° ΠΊ Π΅Π³ΠΎ ΡΠΈΡΠΈΠ½Π΅ ΠΈ Π²ΡΡΠΎΡΠ΅ Π΄ΠΎΠ»ΠΆΠ½ΠΎ Π±ΡΡΡ Π½Π΅ Π±ΠΎΠ»Π΅Π΅ 2. ΠΡΠΈ ΠΎΠ΄Π½ΠΎΡΡΠ΄Π½ΠΎΠΌ ΡΠ°ΡΠΏΠΎΠ»ΠΎΠΆΠ΅Π½ΠΈΠΈ ΡΠΈΠ»ΠΎΡΠΎΠ² ΡΡΠΎ ΠΎΡΠ½ΠΎΡΠ΅Π½ΠΈΠ΅ Π΄ΠΎΠΏΡΡΠΊΠ°Π΅ΡΡΡ ΡΠ²Π΅Π»ΠΈΡΠΈΠ²Π°ΡΡ Π΄ΠΎ 3. ΠΠΎΠΏΡΡΠΊΠ°Π΅ΡΡΡ ΡΠ²Π΅Π»ΠΈΡΠ΅Π½ΠΈΠ΅ Π΄Π»ΠΈΠ½Ρ ΠΊΠΎΡΠΏΡΡΠ° ΠΈ ΡΠΊΠ°Π·Π°Π½Π½ΡΡ ΠΎΡΠ½ΠΎΡΠ΅Π½ΠΈΠΉ ΠΏΡΠΈ ΡΠΎΠΎΡΠ²Π΅ΡΡΡΠ²ΡΡΡΠ΅ΠΌ ΠΎΠ±ΠΎΡΠ½ΠΎΠ²Π°Π½ΠΈΠΈ.
ΠΡΠΈ ΠΏΡΠΎΠ΅ΠΊΡΠΈΡΠΎΠ²Π°Π½ΠΈΠΈ ΠΌΠ½ΠΎΠ³ΠΎΡΡΠ΄Π½ΡΡ ΡΠΈΠ»ΠΎΡΠ½ΡΡ ΠΊΠΎΡΠΏΡΡΠΎΠ² Ρ ΠΊΡΡΠ³Π»ΡΠΌΠΈ Π² ΠΏΠ»Π°Π½Π΅ ΡΠΈΠ»ΠΎΡΠ°ΠΌΠΈ ΠΏΡΠΎΡΡΡΠ°Π½ΡΡΠ²ΠΎ ΠΌΠ΅ΠΆΠ΄Ρ Π½ΠΈΠΌΠΈ ΡΠ»Π΅Π΄ΡΠ΅Ρ ΠΈΡΠΏΠΎΠ»ΡΠ·ΠΎΠ²Π°ΡΡ Π΄Π»Ρ ΡΠ°Π·ΠΌΠ΅ΡΠ΅Π½ΠΈΡ Π»Π΅ΡΡΠ½ΠΈΡ, ΡΠ°Π·Π»ΠΈΡΠ½ΡΡ ΠΊΠΎΠΌΠΌΡΠ½ΠΈΠΊΠ°ΡΠΈΠΉ, ΡΡΡΠ°Π½ΠΎΠ²ΠΊΠΈ ΡΠ΅Ρ Π½ΠΎΠ»ΠΎΠ³ΠΈΡΠ΅ΡΠΊΠΎΠ³ΠΎ ΠΎΠ±ΠΎΡΡΠ΄ΠΎΠ²Π°Π½ΠΈΡ, Π½Π΅ ΡΡΠ΅Π±ΡΡΡΠ΅Π³ΠΎ ΠΎΠ±ΡΠ»ΡΠΆΠΈΠ²Π°Π½ΠΈΡ, Π° ΡΠ°ΠΊΠΆΠ΅ Π΄Π»Ρ Ρ ΡΠ°Π½Π΅Π½ΠΈΡ Π½Π΅ΡΠ²ΡΠ·Π½ΡΡ ΡΡΠΏΡΡΠΈΡ ΠΌΠ°ΡΠ΅ΡΠΈΠ°Π»ΠΎΠ².
ΠΡΠΈ ΠΏΡΠΎΠ΅ΠΊΡΠΈΡΠΎΠ²Π°Π½ΠΈΠΈ ΡΠΈΠ»ΠΎΡΠ½ΡΡ ΠΊΠΎΡΠΏΡΡΠΎΠ² ΡΠ»Π΅Π΄ΡΠ΅Ρ ΠΈΡΡ ΠΎΠ΄Ρ ΠΈΠ· Π’Π 101-81*, ΡΠ΅Ρ Π½ΠΈΠΊΠΎ-ΡΠΊΠΎΠ½ΠΎΠΌΠΈΡΠ΅ΡΠΊΠΎΠΉ ΡΠ΅Π»Π΅ΡΠΎΠΎΠ±ΡΠ°Π·Π½ΠΎΡΡΠΈ ΠΈ ΠΊΠΎΠ½ΠΊΡΠ΅ΡΠ½ΡΡ ΡΡΠ»ΠΎΠ²ΠΈΠΉ ΡΡΡΠΎΠΈΡΠ΅Π»ΡΡΡΠ²Π° ΠΏΡΠ΅Π΄ΡΡΠΌΠ°ΡΡΠΈΠ²Π°ΡΡ ΠΏΡΠΈΠΌΠ΅Π½Π΅Π½ΠΈΠ΅ ΠΌΠΎΠ½ΠΎΠ»ΠΈΡΠ½ΠΎΠ³ΠΎ ΠΆΠ΅Π»Π΅Π·ΠΎΠ±Π΅ΡΠΎΠ½Π° (ΠΏΡΠΈ Π²ΠΎΠ·Π²Π΅Π΄Π΅Π½ΠΈΠΈ ΠΈΠ½Π΄ΡΡΡΡΠΈΠ°Π»ΡΠ½ΡΠΌΠΈ ΠΌΠ΅ΡΠΎΠ΄Π°ΠΌΠΈ) ΠΈΠ»ΠΈ ΡΠ±ΠΎΡΠ½ΠΎΠ³ΠΎ ΠΆΠ΅Π»Π΅Π·ΠΎΠ±Π΅ΡΠΎΠ½Π° (ΠΈΠ· ΡΠ½ΠΈΡΠΈΡΠΈΡΠΎΠ²Π°Π½Π½ΡΡ ΠΈΠ·Π΄Π΅Π»ΠΈΠΉ). ΠΠΎΠΏΡΡΠΊΠ°Π΅ΡΡΡ ΠΏΡΠΈΠΌΠ΅Π½Π΅Π½ΠΈΠ΅ ΡΡΠ°Π»ΡΠ½ΡΡ ΡΠΈΠ»ΠΎΡΠΎΠ² Π΄Π»Ρ ΡΡΠΏΡΡΠΈΡ ΠΌΠ°ΡΠ΅ΡΠΈΠ°Π»ΠΎΠ², Ρ ΡΠ°Π½Π΅Π½ΠΈΠ΅ ΠΊΠΎΡΠΎΡΡΡ ΠΈΠ² Π΄ΠΎΠΏΡΡΠΊΠ°Π΅ΡΡΡ Π² ΠΆΠ΅Π»Π΅Π·ΠΎΠ±Π΅ΡΠΎΠ½Π½ΡΡ Π΅ΠΌΠΊΠΎΡΡΡΡ , Π° ΡΠ°ΠΊΠΆΠ΅ ΡΡΠ°Π»ΡΠ½ΡΡ ΠΈΠ½Π²Π΅Π½ΡΠ°ΡΠ½ΡΡ ΠΈ ΠΎΠΏΠ΅ΡΠ°ΡΠΈΠ²Π½ΡΡ ΡΠΈΠ»ΠΎΡΠΎΠ².
ΠΡΠΈ ΠΈΠ·Π³ΠΎΡΠΎΠ²Π»Π΅Π½ΠΈΠΈ ΡΡΠ΅Π½ΠΎΠΊ ΡΠΈΠ»ΠΎΡΠΎΠ² ΠΈΠ· ΡΡΠ°Π»ΠΈ ΡΠ»Π΅Π΄ΡΠ΅Ρ ΠΏΡΠ΅Π΄ΡΡΠΌΠ°ΡΡΠΈΠ²Π°ΡΡ ΠΈΠ½Π΄ΡΡΡΡΠΈΠ°Π»ΡΠ½ΡΠ΅ ΠΌΠ΅ΡΠΎΠ΄Ρ ΠΈΡ ΠΈΠ·Π³ΠΎΡΠΎΠ²Π»Π΅Π½ΠΈΡ ΠΈ ΠΌΠΎΠ½ΡΠ°ΠΆΠ° ΠΏΡΡΠ΅ΠΌ ΠΏΡΠΈΠΌΠ΅Π½Π΅Π½ΠΈΡ; Π»ΠΈΡΡΠΎΠ² ΠΈ Π»Π΅Π½Ρ Π±ΠΎΠ»ΡΡΠΈΡ ΡΠ°Π·ΠΌΠ΅ΡΠΎΠ²; ΡΠΏΠΎΡΠΎΠ±Π° ΡΡΠ»ΠΎΠ½ΠΈΡΠΎΠ²Π°Π½ΠΈΡ; ΠΈΠ·Π³ΠΎΡΠΎΠ²Π»Π΅Π½ΠΈΡ Π·Π°Π³ΠΎΡΠΎΠ²ΠΎΠΊ Π² Π²ΠΈΠ΄Π΅ βΡΠΊΠΎΡΠ»ΡΠΏΒ» β ΠΏΠΎΠ»ΠΈΡΡΠΎΠ²Π°Ρ ΡΠ±ΠΎΡΠΊΠ°; Π°Π²ΡΠΎΠΌΠ°ΡΠΈΡΠ΅ΡΠΊΠΎΠΉ ΡΠ²Π°ΡΠΊΠΈ Ρ ΠΌΠΈΠ½ΠΈΠΌΠ°Π»ΡΠ½ΡΠΌ ΠΊΠΎΠ»ΠΈΡΠ΅ΡΡΠ²ΠΎΠΌ ΡΠ²Π°ΡΠ½ΡΡ ΡΠ²ΠΎΠ², Π²ΡΠΏΠΎΠ»Π½ΡΠ΅ΠΌΡΡ Π½Π° ΠΌΠΎΠ½ΡΠ°ΠΆΠ΅, Π° ΡΠ°ΠΊΠΆΠ΅ Π΄ΡΡΠ³ΠΈΡ ΠΏΠ΅ΡΠ΅Π΄ΠΎΠ²ΡΡ ΠΌΠ΅ΡΠΎΠ΄ΠΎΠ².
Π‘Π±ΠΎΡΠ½ΡΠ΅ ΠΆΠ΅Π»Π΅Π·ΠΎΠ±Π΅ΡΠΎΠ½Π½ΡΠ΅ ΡΡΠ΅Π½Ρ ΡΠΈΠ»ΠΎΡΠΎΠ² ΡΠ»Π΅Π΄ΡΠ΅Ρ ΠΈΠ·Π³ΠΎΡΠ°Π²Π»ΠΈΠ²Π°ΡΡ Π΄Π»Ρ ΡΠΈΠ»ΠΎΡΠΎΠ² ΠΊΡΡΠ³Π»ΡΡ Π² ΠΏΠ»Π°Π½Π΅ Π΄ΠΈΠ°ΠΌΠ΅ΡΡΠΎΠΌ 3 ΠΌ ΠΈΠ· ΠΎΠ±ΡΠ΅ΠΌΠ½ΡΡ Π±Π»ΠΎΠΊΠΎΠ². ΠΡΠΈ Π±ΠΎΠ»ΡΡΠΈΡ ΡΠ°Π·ΠΌΠ΅ΡΠ°Ρ β ΠΈΠ· ΠΎΡΠ΄Π΅Π»ΡΠ½ΡΡ ΡΠ»Π΅ΠΌΠ΅Π½ΡΠΎΠ², ΡΠΊΡΡΠΏΠ½ΡΠ΅ΠΌΡΡ ΠΏΠ΅ΡΠ΅Π΄ ΠΌΠΎΠ½ΡΠ°ΠΆΠΎΠΌ Π² ΡΠ°ΡΠ³ΠΈ ΠΈΠ»ΠΈ Π±Π»ΠΎΠΊΠΈ, ΠΈΠ»ΠΈ ΠΈΠ· ΡΠ»Π΅ΠΌΠ΅Π½ΡΠΎΠ², ΠΌΠΎΠ½ΡΠΈΡΡΠ΅ΠΌΡΡ Π±Π΅Π· ΠΏΡΠ΅Π΄Π²Π°ΡΠΈΡΠ΅Π»ΡΠ½ΠΎΠ³ΠΎ ΡΠΊΡΡΠΏΠ½Π΅Π½ΠΈΡ.
ΠΠ½ΡΡΡΠ΅Π½Π½ΠΈΠ΅ ΠΏΠΎΠ²Π΅ΡΡ Π½ΠΎΡΡΠΈ ΡΡΠ΅Π½ ΠΈ Π΄Π½ΠΈΡΠ° ΡΠΈΠ»ΠΎΡΠΎΠ² Π½Π΅ Π΄ΠΎΠ»ΠΆΠ½Ρ ΠΈΠΌΠ΅ΡΡ Π²ΡΡΡΡΠΏΠ°ΡΡΠΈΡ Π³ΠΎΡΠΈΠ·ΠΎΠ½ΡΠ°Π»ΡΠ½ΡΡ ΡΠ΅Π±Π΅Ρ ΠΈ Π²ΠΏΠ°Π΄ΠΈΠ½.
ΠΠ½ΠΈΡΠ° ΡΠΈΠ»ΠΎΡΠΎΠ² Π² Π·Π°Π²ΠΈΡΠΈΠΌΠΎΡΡΠΈ ΠΎΡ Π΄ΠΈΠ°ΠΌΠ΅ΡΡΠ° ΡΠΈΠ»ΠΎΡΠ° ΠΈ Ρ ΡΠ°Π½ΠΈΠΌΠΎΠ³ΠΎ ΠΌΠ°ΡΠ΅ΡΠΈΠ°Π»Π° ΡΠ»Π΅Π΄ΡΠ΅Ρ ΠΏΡΠΎΠ΅ΠΊΡΠΈΡΠΎΠ²Π°ΡΡ Π² Π²ΠΈΠ΄Π΅ ΠΆΠ΅Π»Π΅Π·ΠΎΠ±Π΅ΡΠΎΠ½Π½ΠΎΠΉ ΠΏΠ»ΠΈΡΡ ΡΠΎ ΡΡΠ°Π»ΡΠ½ΠΎΠΉ ΠΏΠΎΠ»ΡΠ²ΠΎΡΠΎΠ½ΠΊΠΎΠΉ ΠΈ Π±Π΅ΡΠΎΠ½Π½ΠΎΠΉ Π·Π°Π±ΡΡΠΊΠΎΠΉ ΠΈΠ»ΠΈ Π² Π²ΠΈΠ΄Π΅ ΠΆΠ΅Π»Π΅Π·ΠΎΠ±Π΅ΡΠΎΠ½Π½ΠΎΠΉ ΠΈΠ»ΠΈ ΡΡΠ°Π»ΡΠ½ΠΎΠΉ Π²ΠΎΡΠΎΠ½ΠΊΠΈ Π½Π° Π²ΡΠ΅ ΡΠ΅ΡΠ΅Π½ΠΈΠ΅ ΡΠΈΠ»ΠΎΡΠ°.
Π‘ΡΠ΅Π½Ρ ΠΈ Π΄Π½ΠΈΡΠ° ΡΠΈΠ»ΠΎΡΠΎΠ² Π΄Π»Ρ Π°Π±ΡΠ°Π·ΠΈΠ²Π½ΡΡ ΠΈ ΠΊΡΡΠΊΠΎΠ²ΡΡ ΠΌΠ°ΡΠ΅ΡΠΈΠ°Π»ΠΎΠ² ΡΠ»Π΅Π΄ΡΠ΅Ρ Π·Π°ΡΠΈΡΠ°ΡΡ ΠΎΡ ΠΈΡΡΠΈΡΠ°Π½ΠΈΡ ΠΈ ΡΠ°Π·ΡΡΡΠ΅Π½ΠΈΡ ΠΏΡΠΈ Π·Π°Π³ΡΡΠ·ΠΊΠ΅. ΠΠ°ΡΠ΅ΡΠΈΠ°Π» Π΄Π»Ρ Π·Π°ΡΠΈΡΡ ΡΡΠ΅Π½ ΠΈ Π΄Π½ΠΈΡΠ° ΡΠΈΠ»ΠΎΡΠΎΠ² ΡΠ»Π΅Π΄ΡΠ΅Ρ Π²ΡΠ±ΠΈΡΠ°ΡΡ Π² Π·Π°Π²ΠΈΡΠΈΠΌΠΎΡΡΠΈ ΠΎΡ ΡΠΈΠ·ΠΈΠΊΠΎ-ΠΌΠ΅Ρ Π°Π½ΠΈΡΠ΅ΡΠΊΠΈΡ ΡΠ²ΠΎΠΉΡΡΠ² Ρ ΡΠ°Π½ΠΈΠΌΠΎΠ³ΠΎ ΠΌΠ°ΡΠ΅ΡΠΈΠ°Π»Π°. ΠΡΠΈ ΠΏΡΠΎΠ΅ΠΊΡΠΈΡΠΎΠ²Π°Π½ΠΈΠΈ ΡΠΈΠ»ΠΎΡΠΎΠ² Π½Π΅ΠΎΠ±Ρ ΠΎΠ΄ΠΈΠΌΠΎ ΡΡΠΈΡΡΠ²Π°ΡΡ ΡΠ°ΠΊΠΆΠ΅ Ρ ΠΈΠΌΠΈΡΠ΅ΡΠΊΡΡ Π°Π³ΡΠ΅ΡΡΠΈΡ Ρ ΡΠ°Π½ΠΈΠΌΠΎΠ³ΠΎ ΠΌΠ°ΡΠ΅ΡΠΈΠ°Π»Π° ΠΈ Π²ΠΎΠ·Π΄ΡΡΠ½ΠΎΠΉ ΡΡΠ΅Π΄Ρ.
ΠΠ»Ρ ΡΠΈΠ»ΠΎΡΠΎΠ² ΡΠΎ ΡΡΠ°Π»ΡΠ½ΡΠΌΠΈ ΡΡΠ΅Π½Π°ΠΌΠΈ ΠΏΠ΅ΡΠ΅ΠΊΡΡΡΠΈΠ΅ Π΄ΠΎΠΏΡΡΠΊΠ°Π΅ΡΡΡ ΠΏΡΠΎΠ΅ΠΊΡΠΈΡΠΎΠ²Π°ΡΡ ΠΈΠ· ΡΡΠ°Π»ΠΈ.
ΠΠΎΠΊΡΡΡΠΈΡ ΠΎΡΠ΄Π΅Π»ΡΠ½ΠΎ ΡΡΠΎΡΡΠΈΡ ΠΊΡΡΠ³Π»ΡΡ ΡΠΈΠ»ΠΎΡΠΎΠ² ΠΏΡΠΈ ΠΎΡΡΡΡΡΡΠ²ΠΈΠΈ Π½Π°Π΄ΡΠΈΠ»ΠΎΡΠ½ΠΎΠ³ΠΎ ΠΏΠΎΠΌΠ΅ΡΠ΅Π½ΠΈΡ, Π° ΡΠ°ΠΊΠΆΠ΅ ΡΠΈΠ»ΠΎΡΠΎΠ² Π΄ΠΈΠ°ΠΌΠ΅ΡΡΠΎΠΌ Π±ΠΎΠ»Π΅Π΅ 12 ΠΌ Π΄ΠΎΠΏΡΡΠΊΠ°Π΅ΡΡΡ ΠΈΠ·Π³ΠΎΡΠ°Π²Π»ΠΈΠ²Π°ΡΡ Π² Π²ΠΈΠ΄Π΅ ΠΎΠ±ΠΎΠ»ΠΎΡΠ΅ΠΊ.
ΠΠ°Π΄ΡΠΈΠ»ΠΎΡΠ½ΡΠ΅ ΠΏΠΎΠΌΠ΅ΡΠ΅Π½ΠΈΡ ΠΈ ΠΊΠΎΠ½Π²Π΅ΠΉΠ΅ΡΠ½ΡΠ΅ Π³Π°Π»Π΅ΡΠ΅ΠΈ ΡΠ»Π΅Π΄ΡΠ΅Ρ ΠΈΠ·Π³ΠΎΡΠ°Π²Π»ΠΈΠ²Π°ΡΡ, ΠΏΡΠΈΠΌΠ΅Π½ΡΡ ΠΎΠ±Π»Π΅Π³ΡΠ΅Π½Π½ΡΠ΅ ΡΡΠ΅Π½ΠΎΠ²ΡΠ΅ ΠΎΠ³ΡΠ°ΠΆΠ΄Π΅Π½ΠΈΡ ΠΈΠ· Π½Π΅ΡΠ³ΠΎΡΠ°Π΅ΠΌΡΡ ΠΌΠ°ΡΠ΅ΡΠΈΠ°Π»ΠΎΠ². ΠΠΎΠΏΡΡΠΊΠ°Π΅ΡΡΡ ΡΠ°ΠΊΠΆΠ΅ ΠΏΡΠΈΠΌΠ΅Π½Π΅Π½ΠΈΠ΅ ΡΠ±ΠΎΡΠ½ΡΡ ΠΌΠ΅ΡΠ°Π»Π»ΠΈΡΠ΅ΡΠΊΠΈΡ ΠΊΠΎΠ½ΡΡΡΡΠΊΡΠΈΠΉ.
ΠΠ·Π³ΠΎΡΠΎΠ²Π»Π΅Π½ΠΈΠ΅ ΡΠΎΠ΅Π΄ΠΈΠ½ΠΈΡΠ΅Π»ΡΠ½ΡΡ Π³Π°Π»Π΅ΡΠ΅ΠΉ ΠΌΠ΅ΠΆΠ΄Ρ ΡΠΈΠ»ΠΎΡΠ°ΠΌΠΈ ΠΈΠ»ΠΈ ΠΌΠ΅ΠΆΠ΄Ρ ΡΠΈΠ»ΠΎΡΠ½ΡΠΌΠΈ ΠΊΠΎΡΠΏΡΡΠ°ΠΌΠΈ ΡΠ»Π΅Π΄ΡΠ΅Ρ ΡΡΠΈΡΡΠ²Π°ΡΡ ΠΎΡΠ½ΠΎΡΠΈΡΠ΅Π»ΡΠ½ΡΠ΅ ΡΠΌΠ΅ΡΠ΅Π½ΠΈΡ ΡΠΈΠ»ΠΎΡΠΎΠ² ΠΈΠ»ΠΈ ΡΠΈΠ»ΠΎΡΠ½ΡΡ ΠΊΠΎΡΠΏΡΡΠΎΠ², Π²ΡΠ·ΡΠ²Π°Π΅ΠΌΡΠ΅ Π½Π΅ΡΠ°Π²Π½ΠΎΠΌΠ΅ΡΠ½ΡΠΌΠΈ ΠΎΡΠ°Π΄ΠΊΠ°ΠΌΠΈ ΠΈ ΠΊΡΠ΅Π½Π°ΠΌΠΈ.
ΠΠΎΠ»ΠΎΠ½Π½Ρ ΠΏΠΎΠ΄ΡΠΈΠ»ΠΎΡΠ½ΠΎΠ³ΠΎ ΡΡΠ°ΠΆΠ° Π½Π°Π΄Π»Π΅ΠΆΠΈΡ ΠΏΡΠΎΠ΅ΠΊΡΠΈΡΠΎΠ²Π°ΡΡ ΡΠ±ΠΎΡΠ½ΡΠΌΠΈ ΡΡΠ°Π»ΡΠ½ΡΠΌΠΈ.
Π€ΡΠ½Π΄Π°ΠΌΠ΅Π½ΡΡ ΡΠΈΠ»ΠΎΡΠΎΠ² ΠΈ ΡΠΈΠ»ΠΎΡΠ½ΡΡ ΠΊΠΎΡΠΏΡΡΠΎΠ² ΡΠ»Π΅Π΄ΡΠ΅Ρ ΠΏΡΠΎΠ΅ΠΊΡΠΈΡΠΎΠ²Π°ΡΡ Π² Π²ΠΈΠ΄Π΅ ΠΌΠΎΠ½ΠΎΠ»ΠΈΡΠ½ΡΡ ΠΆΠ΅Π»Π΅Π·ΠΎΠ±Π΅ΡΠΎΠ½Π½ΡΡ Π±Π΅Π·Π±Π°Π»ΠΎΡΠ½ΡΡ ΠΏΠ»ΠΈΡ. ΠΠ° ΡΠΊΠ°Π»ΡΠ½ΡΡ ΠΈ ΠΊΡΡΠΏΠ½ΠΎΠΎΠ±Π»ΠΎΠΌΠΎΡΠ½ΡΡ Π³ΡΡΠ½ΡΠ°Ρ Π΄ΠΎΠΏΡΡΠΊΠ°Π΅ΡΡΡ ΠΏΡΠΈΠ½ΠΈΠΌΠ°ΡΡ ΡΡΠ½Π΄Π°ΠΌΠ΅Π½ΡΡ ΠΎΡΠ΄Π΅Π»ΡΠ½ΠΎ ΡΡΠΎΡΡΠΈΠ΅, Π»Π΅Π½ΡΠΎΡΠ½ΡΠ΅ ΠΈΠ»ΠΈ ΠΊΠΎΠ»ΡΡΠ΅Π²ΡΠ΅, ΠΌΠΎΠ½ΠΎΠ»ΠΈΡΠ½ΡΠ΅ ΠΈΠ»ΠΈ ΡΠ±ΠΎΡΠ½ΡΠ΅. Π‘Π²Π°ΠΉΠ½ΡΠ΅ ΡΡΠ½Π΄Π°ΠΌΠ΅Π½ΡΡ ΡΠ»Π΅Π΄ΡΠ΅Ρ ΠΏΡΠ΅Π΄ΡΡΠΌΠ°ΡΡΠΈΠ²Π°ΡΡ, Π΅ΡΠ»ΠΈ ΡΠ°ΡΡΠ΅ΡΠ½ΡΠ΅ Π΄Π΅ΡΠΎΡΠΌΠ°ΡΠΈΠΈ Π΅ΡΡΠ΅ΡΡΠ²Π΅Π½Π½ΠΎΠ³ΠΎ ΠΎΡΠ½ΠΎΠ²Π°Π½ΠΈΡ ΠΏΡΠ΅Π²ΡΡΠ°ΡΡ ΠΏΡΠ΅Π΄Π΅Π»ΡΠ½ΡΠ΅ ΠΈΠ»ΠΈ Π½Π΅ ΠΎΠ±Π΅ΡΠΏΠ΅ΡΠΈΠ²Π°Π΅ΡΡΡ Π΅Π³ΠΎ ΡΡΡΠΎΠΉΡΠΈΠ²ΠΎΡΡΡ, Π° ΡΠ°ΠΊΠΆΠ΅ ΠΏΡΠΈ Π½Π°Π»ΠΈΡΠΈΠΈ ΠΏΡΠΎΡΠ°Π΄ΠΎΡΠ½ΡΡ Π³ΡΡΠ½ΡΠΎΠ² ΠΈ Π² Π΄ΡΡΠ³ΠΈΡ ΡΠ»ΡΡΠ°ΡΡ ΠΏΡΠΈ ΡΠΎΠΎΡΠ²Π΅ΡΡΡΠ²ΡΡΡΠ΅ΠΌ ΡΠ΅Ρ Π½ΠΈΠΊΠΎ-ΡΠΊΠΎΠ½ΠΎΠΌΠΈΡΠ΅ΡΠΊΠΎΠΌ ΠΎΠ±ΠΎΡΠ½ΠΎΠ²Π°Π½ΠΈΠΈ.
ΠΠΎΠ½ΡΡΡΡΠΊΡΠΈΠΈ ΡΠΈΠ»ΠΎΡΠΎΠ² Π½Π΅ΠΎΠ±Ρ ΠΎΠ΄ΠΈΠΌΠΎ ΡΠ°ΡΡΡΠΈΡΡΠ²Π°ΡΡ Π½Π° Π½Π°Π³ΡΡΠ·ΠΊΠΈ ΠΈ Π²ΠΎΠ·Π΄Π΅ΠΉΡΡΠ²ΠΈΡ Π² ΡΠΎΠΎΡΠ²Π΅ΡΡΡΠ²ΠΈΠΈ Ρ ΡΡΠ΅Π±ΠΎΠ²Π°Π½ΠΈΡΠΌΠΈ Π‘ΠΠΈΠ 2.01.07-85. ΠΡΠΈ ΡΠ°ΡΡΠ΅ΡΠ΅ ΡΠΈΠ»ΠΎΡΠΎΠ² Π΄ΠΎΠ»ΠΆΠ½Ρ Π±ΡΡΡ ΡΠ°ΠΊΠΆΠ΅ ΡΡΡΠ΅Π½Ρ Π½Π°Π³ΡΡΠ·ΠΊΠΈ ΠΈ Π²ΠΎΠ·Π΄Π΅ΠΉΡΡΠ²ΠΈΡ: Π²ΡΠ΅ΠΌΠ΅Π½Π½ΡΠ΅ Π΄Π»ΠΈΡΠ΅Π»ΡΠ½ΡΠ΅ β ΠΎΡ Π²Π΅ΡΠ° ΡΡΠΏΡΡΠΈΡ ΠΌΠ°ΡΠ΅ΡΠΈΠ°Π»ΠΎΠ², ΡΠ°ΡΡΠΈ Π³ΠΎΡΠΈΠ·ΠΎΠ½ΡΠ°Π»ΡΠ½ΠΎΠ³ΠΎ Π΄Π°Π²Π»Π΅Π½ΠΈΡ ΠΈ ΡΡΠ΅Π½ΠΈΡ ΡΡΠΏΡΡΠΈΡ ΠΌΠ°ΡΠ΅ΡΠΈΠ°Π»ΠΎΠ² ΠΎ ΡΡΠ΅Π½Ρ ΡΠΈΠ»ΠΎΡΠΎΠ², Π²Π΅ΡΠ° ΡΠ΅Ρ Π½ΠΎΠ»ΠΎΠ³ΠΈΡΠ΅ΡΠΊΠΎΠ³ΠΎ ΠΎΠ±ΠΎΡΡΠ΄ΠΎΠ²Π°Π½ΠΈΡ; ΠΊΡΠ°ΡΠΊΠΎΠ²ΡΠ΅ΠΌΠ΅Π½Π½ΡΠ΅ β Π²ΠΎΠ·Π½ΠΈΠΊΠ°ΡΡΠΈΠ΅ ΠΏΡΠΈ ΠΈΠ·Π³ΠΎΡΠΎΠ²Π»Π΅Π½ΠΈΠΈ. ΠΏΠ΅ΡΠ΅Π²ΠΎΠ·ΠΊΠ΅ ΠΈ ΠΌΠΎΠ½ΡΠ°ΠΆΠ° ΡΠ±ΠΎΡΠ½ΡΡ ΠΌΠ΅ΡΠ°Π»Π»ΠΈΡΠ΅ΡΠΊΠΈΡ ΠΊΠΎΠ½ΡΡΡΡΠΊΡΠΈΠΉ,
Π‘ΡΠ΅Π½Ρ ΠΊΠ²Π°Π΄ΡΠ°ΡΠ½ΡΡ ΠΈ ΠΌΠ½ΠΎΠ³ΠΎΠ³ΡΠ°Π½Π½ΡΡ ΡΠΈΠ»ΠΎΡΠΎΠ² ΡΠ»Π΅Π΄ΡΠ΅Ρ ΡΠ°ΡΡΡΠΈΡΡΠ²Π°ΡΡ Π½Π° Π²Π½Π΅ΡΠ΅Π½ΡΡΠ΅Π½Π½ΠΎΠ΅ ΡΠ°ΡΡΡΠΆΠ΅Π½ΠΈΠ΅. ΠΠΎΡΡΡΠΈΡΠΈΠ΅Π½ΡΡ ΡΡΠ»ΠΎΠ²ΠΈΠΉ ΡΠ°Π±ΠΎΡΡ ΠΏΡΠΈ ΡΠ°ΡΡΠ΅ΡΠ° ΡΡΠ°Π½ ΡΠΈΠ»ΠΎΡΠΎΠ² ΡΠ»Π΅Π΄ΡΠ΅Ρ ΠΎΠΏΡΠ΅Π΄Π΅Π»ΡΡΡ Π² ΡΠΎΠΎΡΠ²Π΅ΡΡΡΠ²ΠΈΠΈ Ρ ΡΡΠ΅Π±ΠΎΠ²Π°Π½ΠΈΡΠΌΠΈ Π‘ΠΠΈΠ 2.03.01-84, ΠΏΡΠΈΠ½ΠΈΠΌΠ°Ρ Π΄Π»Ρ ΡΡΠ΅Π½ ΡΠΈΠ»ΠΎΡΠΎΠ², Π²ΠΎΠ·Π²ΠΎΠ΄ΠΈΠΌΡΡ Π² ΡΠΊΠΎΠ»ΡΠ·ΡΡΠ΅ΠΉ ΠΎΠΏΠ°Π»ΡΠ±ΠΊΠ°
Π‘ΡΠ΅Π½Ρ ΡΡΠ°Π»ΡΠ½ΡΡ ΠΊΡΡΠ³Π»ΡΡ ΡΠΈΠ»ΠΎΡΠΎΠ² ΡΠ°ΡΡΡΠΈΡΡΠ²Π°ΡΡΡΡ Π½Π° ΡΠ΅ ΠΆΠ΅ ΡΠΎΡΠ΅ΡΠ°Π½ΠΈΡ Π½Π°Π³ΡΡΠ·ΠΎΠΊ, ΡΡΠΎ ΠΈ ΡΡΠ΅Π½Ρ ΠΆΠ΅Π»Π΅Π·ΠΎΠ±Π΅ΡΠΎΠ½Π½ΡΡ ΠΊΡΡΠ³Π»ΡΡ ΡΠΈΠ»ΠΎΡΠΎΠ². ΠΠΎΠΏΠΎΠ»Π½ΠΈΡΠ΅Π»ΡΠ½ΠΎ ΡΡΠ΅Π½Ρ ΡΡΠ°Π»ΡΠ½ΡΡ ΡΠΈΠ»ΠΎΡΠΎΠ² Π΄ΠΎΠ»ΠΆΠ½Ρ Π±ΡΡΡ ΠΏΡΠΎΠ²Π΅ΡΠ΅Π½Ρ Π½Π° ΡΡΡΠΎΠΉΡΠΈΠ²ΠΎΡΡΡ Ρ ΠΊΠΎΡΡΡΠΈΡΠΈΠ΅Π½ΡΠΎΠΌ ΡΡΠ»ΠΎΠ²ΠΈΠΉ ΡΠ°Π±ΠΎΡΡ, ΡΠ°Π²Π½ΡΠΌ 1. ΠΠ° Π²ΡΠ½ΠΎΡΠ»ΠΈΠ²ΠΎΡΡΡ ΡΡΠ°Π»ΡΠ½ΡΠ΅ ΡΡΠ΅Π½Ρ Π΄ΠΎΠΏΡΡΠΊΠ°Π΅ΡΡΡ Π½Π΅ ΡΠ°ΡΡΡΠΈΡΡΠ²Π°ΡΡ.
ΠΠ»Ρ ΡΡΠ°Π»ΡΠ½ΡΡ ΠΌΠ΅ΡΠ°Π»Π»ΠΈΡΠ΅ΡΠΊΠΈΡ ΡΠΈΠ»ΠΎΡΠΎΠ² Π΄Π»Ρ ΡΠ΅ΠΌΠ΅Π½ΡΠ° ΡΠ»Π΅Π΄ΡΠ΅Ρ ΡΡΠΈΡΡΠ²Π°ΡΡ Π²ΠΎΠ·Π΄Π΅ΠΉΡΡΠ²ΠΈΡ ΠΎΡ ΡΡΡΠΎΡΠ½ΠΎΠ³ΠΎ ΠΈΠ·ΠΌΠ΅Π½Π΅Π½ΠΈΡ ΡΠ΅ΠΌΠΏΠ΅ΡΠ°ΡΡΡΡ Π½Π°ΡΡΠΆΠ½ΠΎΠ³ΠΎ Π²ΠΎΠ·Π΄ΡΡ Π° Π² Π²ΠΈΠ΄Π΅ Π΄ΠΎΠΏΠΎΠ»Π½ΠΈΡΠ΅Π»ΡΠ½ΠΎΠ³ΠΎ Π³ΠΎΡΠΈΠ·ΠΎΠ½ΡΠ°Π»ΡΠ½ΠΎΠ³ΠΎ Π½ΠΎΡΠΌΠ°ΡΠΈΠ²Π½ΠΎΠ³ΠΎ Π΄Π°Π²Π»Π΅Π½ΠΈΡ ΡΡΠΏΡΡΠ΅Π³ΠΎ ΠΌΠ°ΡΠ΅ΡΠΈΠ°Π»Π°, ΡΡΠΈΡΠ°Ρ Π΅Π³ΠΎ ΡΠ°Π²Π½ΠΎΠΌΠ΅ΡΠ½ΠΎ ΡΠ°ΡΠΏΡΠ΅Π΄Π΅Π»Π΅Π½Π½ΡΠΌ ΠΏΠΎ ΠΏΠ΅ΡΠΈΠΌΠ΅ΡΡΡ ΠΈ ΠΏΠΎ Π²ΡΡΠΎΡΠ΅.
ΠΠΎΠ»ΠΎΠ½Π½Ρ ΠΏΠΎΠ΄ΡΠΈΠ»ΠΎΡΠ½ΠΎΠ³ΠΎ ΡΡΠ°ΠΆΠ° ΡΠ»Π΅Π΄ΡΠ΅Ρ ΡΠ°ΡΡΡΠΈΡΡΠ²Π°ΡΡ ΠΏΠΎ ΡΡ Π΅ΠΌΠ΅ ΡΡΠΎΠ΅ΠΊ, Π·Π°Π΄Π΅Π»Π°Π½Π½ΡΡ Π² ΡΡΠ½Π΄Π°ΠΌΠ΅Π½Ρ, Ρ ΡΡΠ΅ΡΠΎΠΌ ΡΠ°ΠΊΡΠΈΡΠ΅ΡΠΊΠΎΠ³ΠΎ Π·Π°ΡΠ΅ΠΌΠ»Π΅Π½ΠΈΡ Π² Π΄Π½ΠΈΡΠ΅ ΡΠΈΠ»ΠΎΡΠ°. ΠΠ°ΡΡΠΆΠ½ΡΠ΅ ΡΡΠ°Π»ΡΠ½ΡΠ΅ ΠΌΠ°ΡΡΠ΅Π²ΡΠ΅ Π»Π΅ΡΡΠ½ΠΈΡΡ, ΠΈΡΠΏΠΎΠ»ΡΠ·ΡΠ΅ΠΌΡΠ΅ Π΄Π»Ρ ΡΠ²Π°ΠΊΡΠ°ΡΠΈΠΈ Π»ΡΠ΄Π΅ΠΉ, ΡΠ»Π΅Π΄ΡΠ΅Ρ ΠΏΡΠΎΠ΅ΠΊΡΠΈΡΠΎΠ²Π°ΡΡ, ΠΊΠ°ΠΊ ΠΏΡΠ°Π²ΠΈΠ»ΠΎ, ΡΠΈΡΠΈΠ½ΠΎΠΉ Π½Π΅ ΠΌΠ΅Π½Π΅Π΅ 0,7 ΠΌ Ρ ΡΠΊΠ»ΠΎΠ½ΠΎΠΌ ΠΌΠ°ΡΡΠ΅ΠΉ Π½Π΅ Π±ΠΎΠ»Π΅Π΅ 1:1, ΠΎΠ³ΡΠ°ΠΆΠ΄Π΅Π½ΠΈΠ΅ΠΌ Π²ΡΡΠΎΡΠΎΠΉ 1,0 ΠΌΠΈ ΠΏΠ»ΠΎΡΠ°Π΄ΠΊΠ°ΠΌΠΈ, ΡΠ°ΡΠΏΠΎΠ»ΠΎΠΆΠ΅Π½Π½ΡΠΌΠΈ ΠΏΠΎ Π²ΡΡΠΎΡΠ΅ Π½Π° ΡΠ°ΡΡΡΠΎΡΠ½ΠΈΠΈ Π½Π° Π±ΠΎΠ»Π΅Π΅ 8 ΠΌ. 10.57.
ΠΡΠΈ Ρ ΡΠ°Π½Π΅Π½ΠΈΠΈ Π² ΡΠΈΠ»ΠΎΡΠ°Ρ Π½Π΅ΡΠ³ΠΎΡΠ°Π΅ΠΌΡΡ ΠΌΠ°ΡΠ΅ΡΠΈΠ°Π»ΠΎΠ² Π΄ΠΎΠΏΡΡΠΊΠ°Π΅ΡΡΡ ΠΏΡΠ΅Π΄ΡΡΠΌΠ°ΡΡΠΈΠ²Π°ΡΡ ΠΎΠ΄ΠΈΠ½ ΡΠ²Π°ΠΊΡΠ°ΡΠΈΠΎΠ½Π½ΡΠΉ Π²ΡΡ ΠΎΠ΄ (Π±Π΅Π· ΡΡΡΡΠΎΠΉΡΡΠ²Π° Π²ΡΠΎΡΠΎΠ³ΠΎ) Π½Π° Π½Π°ΡΡΠΆΠ½ΡΡ ΠΎΡΠΊΡΡΡΡΡ ΡΡΠ°Π»ΡΠ½ΡΡ Π»Π΅ΡΡΠ½ΠΈΡΡ Ρ ΡΠΊΠ»ΠΎΠ½ΠΎΠΌ 1:1.
Π Π°ΡΡΡΠΎΡΠ½ΠΈΠ΅ ΠΎΡ Π½Π°ΠΈΠ±ΠΎΠ»Π΅Π΅ ΡΠ΄Π°Π»Π΅Π½Π½ΠΎΠΉ ΡΠ°ΡΡΠΈ Π½Π°Π΄ΡΠΈΠ»ΠΎΡΠ½ΠΎΠ³ΠΎ ΠΏΠΎΠΌΠ΅ΡΠ΅Π½ΠΈΡ Π΄ΠΎ Π±Π»ΠΈΠΆΠ°ΠΉΡΠ΅Π³ΠΎ Π²ΡΡ ΠΎΠ΄Π° Π½Π° Π½Π°ΡΡΠΆΠ½ΡΡ Π»Π΅ΡΡΠ½ΠΈΡΡ ΠΈΠ»ΠΈ Π»Π΅ΡΡΠ½ΠΈΡΠ½ΡΡ ΠΊΠ»Π΅ΡΠΊΡ Π΄ΠΎΠ»ΠΆΠ½ΠΎ Π±ΡΡΡ Π½Π΅ Π±ΠΎΠ»Π΅Π² 75 ΠΌ.
ΠΡΠΈ Ρ ΡΠ°Π½Π΅Π½ΠΈΠΈ Π² ΡΠΈΠ»ΠΎΡΠ°Ρ Π½Π΅ΡΠ³ΠΎΡΠ°Π΅ΠΌΡΡ ΠΌΠ°ΡΠ΅ΡΠΈΠ°Π»ΠΎΠ² ΡΡΠΎ ΡΠ°ΡΡΡΠΎΡΠ½ΠΈΠ΅ Π΄ΠΎΠΏΡΡΠΊΠ°Π΅ΡΡΡ ΡΠ²Π΅Π»ΠΈΡΠΈΠ²Π°ΡΡ Π΄ΠΎ 100 ΠΌ.
ΠΡΠΈ ΠΏΡΠΎΠΈΠ·Π²ΠΎΠ΄ΡΡΠ²Π΅ ΡΠΈΠ»ΠΎΡΠΎΠ² Π΄Π»Ρ ΡΡΠΏΡΡΠΈΡ ΠΌΠ°ΡΠ΅ΡΠΈΠ°Π»ΠΎΠ², ΠΏΡΠ»Ρ ΠΊΠΎΡΠΎΡΡΡ ΡΠΏΠΎΡΠΎΠ±Π½Π° ΠΎΠ±ΡΠ°Π·ΠΎΠ²Π°ΡΡ ΠΏΡΠΈ Π·Π°Π³ΡΡΠ·ΠΊΠ΅ ΠΈΠ»ΠΈ ΡΠ°Π·Π³ΡΡΠ·ΠΊΠ΅ ΡΠΈΠ»ΠΎΡΠΎΠ² Π²Π·ΡΡΠ²ΠΎΠΎΠΏΠ°ΡΠ½ΡΠ΅ ΠΊΠΎΠ½ΡΠ΅Π½ΡΡΠ°ΡΠΈΠΈ, Π΄ΠΎΠ»ΠΆΠ½Ρ ΠΏΡΠ΅Π΄ΡΡΠΌΠ°ΡΡΠΈΠ²Π°ΡΡΡΡ ΠΌΠ΅ΡΠΎΠΏΡΠΈΡΡΠΈΡ, ΠΈΡΠΊΠ»ΡΡΠ°ΡΡΠΈΠ΅ Π²ΠΎΠ·ΠΌΠΎΠΆΠ½ΠΎΡΡΡ Π²Π·ΡΡΠ²ΠΎΠ², Π° ΡΠ°ΠΊΠΆΠ΅ ΠΏΡΠ΅Π΄ΡΠΏΡΠ΅ΠΆΠ΄Π°ΡΡΠΈΠ΅ ΠΏΠΎΡΠ²Π»Π΅Π½ΠΈΠ΅ ΡΠ»Π΅ΠΊΡΡΠΎΡΡΠ°ΡΠΈΡΠ΅ΡΠΊΠΈΡ ΡΠ°Π·ΡΡΠ΄ΠΎΠ².
Π‘ΠΈΠ»ΠΎΡΠ½ΡΠ΅ ΠΊΠΎΡΠΏΡΡΠ°, ΠΎΡΠ΄Π΅Π»ΡΠ½ΠΎ ΡΡΠΎΡΡΠΈΠ΅ ΡΠΈΠ»ΠΎΡΡ, Π½Π°Π΄ΡΠΈΠ»ΠΎΡΠ½ΡΠ΅ Π³Π°Π»Π΅ΡΠ΅ΠΈ, Π½Π°Π΄ΡΡΡΠΎΠΉΠΊΠΈ (Π²ΡΡΠ΅ ΡΡΠΎΠ²Π½Ρ Π½Π°Π΄ΡΠΈΠ»ΠΎΡΠ½ΠΎΠ³ΠΎ ΠΏΠ΅ΡΠ΅ΠΊΡΡΡΠΈΡ) Π΄ΠΎΠΏΡΡΠΊΠ°Π΅ΡΡΡ ΠΏΡΠΎΠ΅ΠΊΡΠΈΡΠΎΠ²Π°ΡΡ Π² ΡΠΎΠΎΡΠ²Π΅ΡΡΡΠ²ΠΈΠΈ Ρ Π’Π 101-81* ΠΈΠ· ΡΡΠ°Π»ΡΠ½ΡΡ ΠΊΠΎΠ½ΡΡΡΡΠΊΡΠΈΠΉ Ρ ΠΏΡΠ΅Π΄Π΅Π»ΠΎΠΌ ΠΎΠ³Π½Π΅ΡΡΠΎΠΉΠΊΠΎΡΡΠΈ Π½Π΅ ΠΌΠ΅Π½Π΅Π΅ 0,25 Ρ ΠΈ Π½ΡΠ»Π΅Π²ΡΠΌ ΠΏΡΠ΅Π΄Π΅Π»ΠΎΠΌ ΡΠ°ΡΠΏΡΠΎΡΡΡΠ°Π½Π΅Π½ΠΈΡ ΠΎΠ³Π½Ρ. ΠΡΠΈΠΌΠ΅ΡΠ°Π½ΠΈΠ΅. ΠΠ»Ρ ΡΡΠ°Π»ΡΠ½ΡΡ ΠΊΠΎΠ»ΠΎΠ½Π½ ΠΈ ΠΏΠ΅ΡΠ΅ΠΊΡΡΡΠΈΠΉ Π½Π°Π΄ΡΡΡΠΎΠ΅ΠΊ, ΠΊΡΠΎΠΌΠ΅ Π΄Π²ΡΡ Π²Π΅ΡΡ Π½ΠΈΡ ΡΡΠ°ΠΆΠ΅ΠΉ, Π° ΡΠ°ΠΊΠΆΠ΅ Π΄Π»Ρ Π½Π΅ΡΡΡΠΈΡ ΠΊΠΎΠ½ΡΡΡΡΠΊΡΠΈΠΉ ΠΏΠΎΠ΄ΡΠΈΠ»ΠΎΡΠ½ΡΡ ΡΡΠ°ΠΆΠ΅ΠΉ (ΠΊΠΎΠ»ΠΎΠ½Π½ ΠΈ Π±Π°Π»ΠΎΠΊ ΠΏΠΎΠ΄ ΡΡΠ΅Π½Ρ ΡΠΈΠ»ΠΎΡΠΎΠ²) Π΄ΠΎΠ»ΠΆΠ½Π° ΠΏΡΠ΅Π΄ΡΡΠΌΠ°ΡΡΠΈΠ²Π°ΡΡΡΡ ΠΎΠ³Π½Π΅Π·Π°ΡΠΈΡΠ°, ΠΎΠ±Π΅ΡΠΏΠ΅ΡΠΈΠ²Π°ΡΡΠ°Ρ ΠΏΡΠ΅Π΄Π΅Π» ΠΎΠ³Π½Π΅ΡΡΠΎΠΉΠΊΠΎΡΡΠΈ ΡΡΠΈΡ ΠΊΠΎΠ½ΡΡΡΡΠΊΡΠΈΠΉ Π½Π΅ ΠΌΠ΅Π½Π΅Π΅ 0,75 Ρ.
Π£ΠΠΠΠ¬ΠΠ«Π ΠΠΠ¨ΠΠ ΠΠΠΠ‘ΠΠ₯ΠΠΠΠ§ΠΠ‘ΠΠΠ₯ ΠΠΠΠΠΠΠ.
ΠΠΎΡΠΌΡ Π½Π°ΡΡΠΎΡΡΠ΅Π³ΠΎ ΡΠ°Π·Π΄Π΅Π»Π° ΡΠ»Π΅Π΄ΡΠ΅Ρ ΡΠΎΠ±Π»ΡΠ΄Π°ΡΡ ΠΏΡΠΈ ΠΏΡΠΎΠΈΠ·Π²ΠΎΠ΄ΡΡΠ²Π΅ ΡΠ³ΠΎΠ»ΡΠ½ΡΡ Π±Π°ΡΠ΅Π½ ΠΊΠΎΠΊΡΠΎΡ ΠΈΠΌΠ·Π°Π²ΠΎΠ΄ΠΎΠ², ΠΏΡΠ΅Π΄Π½Π°Π·Π½Π°ΡΠ΅Π½Π½ΡΡ Π΄Π»Ρ Π°ΠΊΠΊΡΠΌΡΠ»ΡΡΠΈΠΈ ΡΠ³ΠΎΠ»ΡΠ½ΠΎΠΉ ΡΠΈΡ ΡΡ ΠΏΠ΅ΡΠ΅Π΄ ΠΊΠΎΠΊΡΠΎΠ²Π°Π½ΠΈΠ΅ΠΌ ΠΈ Π΅Π΅ ΠΏΠΎΠ³ΡΡΠ·ΠΊΠΈ Π² Π·Π°Π³ΡΡΠ·ΠΎΡΠ½ΡΠ΅ Π²Π°Π³ΠΎΠ½Ρ Π΄Π»Ρ ΡΠ°ΡΠΏΡΠ΅Π΄Π΅Π»Π΅Π½ΠΈΡ ΠΏΠΎ ΠΊΠΎΠΊΡΠΎΠ²ΡΠΌ ΠΏΠ΅ΡΠ°ΠΌ.
ΠΠ±ΡΠ΅ΠΌΠ½ΠΎ-ΠΏΠ»Π°Π½ΠΈΡΠΎΠ²ΠΎΡΠ½ΡΠ΅ ΡΠ΅ΡΠ΅Π½ΠΈΡ ΡΠ³ΠΎΠ»ΡΠ½ΡΡ Π±Π°ΡΠ΅Π½ ΠΈ ΠΈΡ Π³Π°Π±Π°ΡΠΈΡΠ½ΡΠ΅ ΡΠ°Π·ΠΌΠ΅ΡΡ Π΄ΠΎΠ»ΠΆΠ½Ρ ΠΎΠ±Π΅ΡΠΏΠ΅ΡΠΈΠ²Π°ΡΡ Π²ΠΎΠ·ΠΌΠΎΠΆΠ½ΠΎΡΡΡ ΡΠ°ΡΠΈΠΎΠ½Π°Π»ΡΠ½ΠΎΠΉ ΠΊΠΎΠΌΠΏΠΎΠ½ΠΎΠ²ΠΊΠΈ Ρ ΠΊΠΎΠΊΡΠΎΠ²ΡΠΌΠΈ Π±Π°ΡΠ°ΡΠ΅ΡΠΌΠΈ ΠΈ ΡΠΎΠΎΡΠ²Π΅ΡΡΡΠ²ΡΡΡΠ΅Π΅ ΡΡΡΠΎΠΈΡΠ΅Π»ΡΠ½ΠΎΠΌΡ Π·Π°Π΄Π°Π½ΠΈΡ Π²Π·Π°ΠΈΠΌΠ½ΠΎΠ΅ ΡΠ°ΡΠΏΠΎΠ»ΠΎΠΆΠ΅Π½ΠΈΠ΅ Ρ ΠΏΠΎΠ΄Π²ΠΈΠΆΠ½ΡΠΌ ΡΠ΅Ρ Π½ΠΎΠ»ΠΎΠ³ΠΈΡΠ΅ΡΠΊΠΈΠΌ ΠΎΠ±ΠΎΡΡΠ΄ΠΎΠ²Π°Π½ΠΈΠ΅ΠΌ (ΠΊΠΎΠΊΡΠΎΠ²ΡΡΠ°Π»ΠΊΠΈΠ²Π°ΡΠ΅Π»ΡΠΌΠΈ, Π΄Π²Π΅ΡΠ΅ΡΡΠ΅ΠΌΠΎΡΠ½ΡΠΌΠΈ ΠΌΠ°ΡΠΈΠ½Π°ΠΌΠΈ, ΡΡΡΠΈΠ»ΡΠ½ΡΠΌΠΈ ΠΈ Π·Π°Π³ΡΡΠ·ΠΎΡΠ½ΡΠΌΠΈ Π²Π°Π³ΠΎΠ½Π°ΠΌΠΈ). ΠΠ°ΠΊ ΠΏΡΠ°Π²ΠΈΠ»ΠΎ, ΡΠ³ΠΎΠ»ΡΠ½ΡΠ΅ Π±Π°ΡΠ½ΠΈ Π΄ΠΎΠ»ΠΆΠ½Ρ Π±ΡΡΡ ΠΏΡΡΠΌΠΎΡΠ³ΠΎΠ»ΡΠ½ΡΠΌΠΈ Π² ΠΏΠ»Π°Π½Π΅.
ΠΡΠΈ ΠΏΡΠΎΠΈΠ·Π²ΠΎΠ΄ΡΡΠ²Π΅ Π½Π΅ΡΠΊΠΎΠ»ΡΠΊΠΈΡ ΡΠ³ΠΎΠ»ΡΠ½ΡΡ Π±Π°ΡΠ΅Π½ Π΄Π»Ρ ΠΎΠ΄Π½ΠΎΠ³ΠΎ ΠΏΡΠ΅Π΄ΠΏΡΠΈΡΡΠΈΡ ΠΈΡ ΠΊΠΎΠ½ΡΠΈΠ³ΡΡΠ°ΡΠΈΡ ΠΈ ΡΠ°Π·ΠΌΠ΅ΡΡ Π³ΠΎΡΠΈΠ·ΠΎΠ½ΡΠ°Π»ΡΠ½ΠΎΠ³ΠΎ ΡΠ΅ΡΠ΅Π½ΠΈΡ Π΄ΠΎΠ»ΠΆΠ½Ρ Π±ΡΡΡ, ΠΊΠ°ΠΊ ΠΏΡΠ°Π²ΠΈΠ»ΠΎ, ΡΠ½ΠΈΡΠΈΡΠΈΡΠΎΠ²Π°Π½Ρ. ΠΠ°Π±Π°ΡΠΈΡΡ ΡΠ³ΠΎΠ»ΡΠ½ΡΡ Π±Π°ΡΠ΅Π½ ΡΠ»Π΅Π΄ΡΠ΅Ρ ΠΏΡΠΈΠ½ΠΈΠΌΠ°ΡΡ ΠΏΠΎ Π³ΠΎΡΠΈΠ·ΠΎΠ½ΡΠ°Π»ΠΈ ΠΊΡΠ°ΡΠ½ΡΠΌΠΈ 0,3 ΠΌ, ΠΏΠΎ Π²Π΅ΡΡΠΈΠΊΠ°Π»ΠΈ β ΠΊΡΠ°ΡΠ½ΡΠΌΠΈ 0,6 ΠΌ.
Π‘Π²ΠΎΠ±ΠΎΠ΄Π½ΡΠ΅ ΠΎΡ ΡΠ΅Ρ Π½ΠΎΠ»ΠΎΠ³ΠΈΡΠ΅ΡΠΊΠΎΠ³ΠΎ ΠΎΠ±ΠΎΡΡΠ΄ΠΎΠ²Π°Π½ΠΈΡ ΠΎΡΠ½ΠΎΠ²Π½ΠΎΠ³ΠΎ Π½Π°Π·Π½Π°ΡΠ΅Π½ΠΈΡ ΠΎΠ±ΡΠ΅ΠΌΡ Π½ΠΈΠΆΠ½Π΅ΠΉ Π·ΠΎΠ½Ρ ΡΠ³ΠΎΠ»ΡΠ½ΠΎΠΉ Π±Π°ΡΠ½ΠΈ Π΄ΠΎΠΏΡΡΠΊΠ°Π΅ΡΡΡ ΠΈΡΠΏΠΎΠ»ΡΠ·ΠΎΠ²Π°ΡΡ Π΄Π»Ρ ΡΠ°Π·ΠΌΠ΅ΡΠ΅Π½ΠΈΡ Π²ΡΠΏΠΎΠΌΠΎΠ³Π°ΡΠ΅Π»ΡΠ½ΡΡ ΠΏΠΎΠΌΠ΅ΡΠ΅Π½ΠΈΠΉ: ΡΠ»Π΅ΠΊΡΡΠΎΠΏΡΠ½ΠΊΡΠΎΠ², Π²Π΅Π½ΡΠΈΠ»ΡΡΠΈΠΎΠ½Π½ΡΡ ΡΡΡΠ°Π½ΠΎΠ²ΠΎΠΊ, ΠΏΠΎΠΌΠ΅ΡΠ΅Π½ΠΈΠΉ ΠΠΠ, ΡΠ»ΡΠΆΠ΅Π±Π½ΠΎ-Π±ΡΡΠΎΠ²ΡΡ ΠΏΠΎΠΌΠ΅ΡΠ΅Π½ΠΈΠΉ ΠΊΠΎΠΊΡΠΎΠ²ΠΎΠ³ΠΎ Π±Π»ΠΎΠΊΠ° ΠΈ Ρ.Π΄.
ΠΠ½ΡΡΡΠ΅Π½Π½ΠΈΠ΅ Π³Π°Π±Π°ΡΠΈΡΡ Π² ΡΠΊΠ²ΠΎΠ·Π½ΠΎΠΉ ΡΠ°ΡΡΠΈ ΡΠ³ΠΎΠ»ΡΠ½ΠΎΠΉ Π±Π°ΡΠ½ΠΈ Π΄ΠΎΠ»ΠΆΠ½Ρ ΠΎΠ±Π΅ΡΠΏΠ΅ΡΠΈΠ²Π°ΡΡ Π½Π°Π»ΠΈΡΠΈΠ΅: ΡΡΠ΅Π±ΡΠ΅ΠΌΡΡ ΠΏΡΠ°Π²ΠΈΠ»Π°ΠΌΠΈ Π±Π΅Π·ΠΎΠΏΠ°ΡΠ½ΠΎΡΡΠΈ Π·Π°Π·ΠΎΡΠΎΠ² ΠΌΠ΅ΠΆΠ΄Ρ ΡΡΡΠΎΠΈΡΠ΅Π»ΡΠ½ΡΠΌΠΈ ΠΈ ΡΠ΅Ρ Π½ΠΎΠ»ΠΎΠ³ΠΈΡΠ΅ΡΠΊΠΈΠΌΠΈ ΠΊΠΎΠ½ΡΡΡΡΠΊΡΠΈΡΠΌΠΈ, Π½ΠΎ Π½Π΅ ΠΌΠ΅Π½Π΅Π΅ 0,1 ΠΌ; ΠΏΡΠΎΡ ΠΎΠ΄ΠΎΠΊ Ρ ΠΎΠ±Π΅ΠΈΡ ΡΡΠΎΡΠΎΠ½ Π·Π°Π³ΡΡΠ·ΠΎΡΠ½ΠΎΠ³ΠΎ Π²Π°Π³ΠΎΠ½Π° ΡΠΈΡΠΈΠ½ΠΎΠΉ Π½Π΅ ΠΌΠ΅Π½Π΅Π΅ 0,8 ΠΌ ΠΈ Π²ΡΡΠΎΡΠΎΠΉ Π½Π΅ ΠΌΠ΅Π½Π΅Π΅ 2,1 ΠΌ.
Π Π°Π·ΠΌΠ΅ΡΡ Π½Π°Π΄ΡΠ΅ΠΌΠΊΠΎΡΡΠ½ΠΎΠΉ ΡΠ°ΡΡΠΈ ΡΠ³ΠΎΠ»ΡΠ½ΠΎΠΉ Π±Π°ΡΠ½ΠΈ Π΄ΠΎΠ»ΠΆΠ½Ρ ΠΎΠ±Π΅ΡΠΏΠ΅ΡΠΈΠ²Π°ΡΡ Π²ΠΎΠ·ΠΌΠΎΠΆΠ½ΠΎΡΡΡ ΡΠ°Π·ΠΌΠ΅ΡΠ΅Π½ΠΈΡ ΠΎΠ±ΠΎΡΡΠ΄ΠΎΠ²Π°Π½ΠΈΡ, ΠΏΡΠ΅Π΄Π½Π°Π·Π½Π°ΡΠ΅Π½Π½ΠΎΠ³ΠΎ Π΄Π»Ρ ΡΠ°ΡΠΏΡΠ΅Π΄Π΅Π»Π΅Π½ΠΈΡ ΡΠΈΡ ΡΡ ΠΏΠΎ ΡΡΠ΅ΠΉΠΊΠ°ΠΌ Π΅ΠΌΠΊΠΎΡΡΠ½ΠΎΠΉ ΡΠ°ΡΡΠΈ. ΠΡΠΈ ΡΡΠΎΠΌ ΠΌΠ΅ΠΆΠ΄Ρ ΠΎΠ±ΠΎΡΡΠ΄ΠΎΠ²Π°Π½ΠΈΠ΅ΠΌ ΠΈ ΡΡΡΠΎΠΈΡΠ΅Π»ΡΠ½ΡΠΌΠΈ ΠΊΠΎΠ½ΡΡΡΡΠΊΡΠΈΡΠΌΠΈ Π΄ΠΎΠ»ΠΆΠ½Ρ ΠΏΡΠ΅Π΄ΡΡΠΌΠ°ΡΡΠΈΠ²Π°ΡΡΡΡ ΠΏΡΠΎΡ ΠΎΠ΄Ρ ΡΠΈΡΠΈΠ½ΠΎΠΉ Π½Π΅ ΠΌΠ΅Π½Π΅Π΅ 0,8 ΠΌ.
ΠΡΠΈ ΡΠ°ΡΡΠ΅ΡΠ΅ ΡΠ³ΠΎΠ»ΡΠ½ΡΡ Π±Π°ΡΠ΅Π½ ΠΈ ΠΈΡ ΡΠ»Π΅ΠΌΠ΅Π½ΡΠΎΠ² Π΄ΠΎΠ»ΠΆΠ½Ρ Π±ΡΡΡ ΡΡΡΠ΅Π½Ρ ΡΠ»Π΅Π΄ΡΡΡΠΈΠ΅ Π½Π°Π³ΡΡΠ·ΠΊΠΈ: ΡΠΎΠ±ΡΡΠ²Π΅Π½Π½ΡΠΉ Π²Π΅Ρ ΠΊΠΎΠ½ΡΡΡΡΠΊΡΠΈΠΉ, Π½Π°Π³ΡΡΠ·ΠΊΠΈ ΠΎΡ ΡΡΠ°ΡΠΈΠΎΠ½Π°ΡΠ½ΠΎΠ³ΠΎ ΠΎΠ±ΠΎΡΡΠ΄ΠΎΠ²Π°Π½ΠΈΡ ΠΈ Π·Π°Π³ΡΡΠ·ΠΎΡΠ½ΠΎΠ³ΠΎ Π²Π°Π³ΠΎΠ½Π°, Π΄Π°Π²Π»Π΅Π½ΠΈΠ΅ ΠΌΠ°ΡΠ΅ΡΠΈΠ°Π»Π° Π·Π°ΠΏΠΎΠ»Π½Π΅Π½ΠΈΡ Π΅ΠΌΠΊΠΎΡΡΠ΅ΠΉ, Π²Π΅ΡΡΠΎΠ²Π°Ρ Π½Π°Π³ΡΡΠ·ΠΊΠ°, Π΄Π°Π²Π»Π΅Π½ΠΈΠ΅ Π³ΡΡΠ½ΡΠ°, Π½Π°Π³ΡΡΠ·ΠΊΠΈ, ΠΏΠ΅ΡΠ΅Π΄Π°Π²Π°Π΅ΠΌΡΠ΅ ΠΏΡΠΈΠΌΡΠΊΠ°ΡΡΠΈΠΌΠΈ ΠΊΠΎΠ½ΡΡΡΡΠΊΡΠΈΡΠΌΠΈ. Π ΡΠ»ΡΡΠ°Π΅ Π½Π΅ΠΎΠ±Ρ ΠΎΠ΄ΠΈΠΌΠΎΡΡΠΈ ΡΡΠΈΡΡΠ²Π°ΡΡΡΡ ΠΎΡΠΎΠ±ΡΠ΅ Π½Π°Π³ΡΡΠ·ΠΊΠΈ ΠΈ Π²ΠΎΠ·Π΄Π΅ΠΉΡΡΠ²ΠΈΡ (ΡΠ΅ΠΉΡΠΌΠΈΡΠ΅ΡΠΊΠΈΠ΅, Π²Π»ΠΈΡΠ½ΠΈΠ΅ Π³ΠΎΡΠ½ΡΡ Π²ΡΡΠ°Π±ΠΎΡΠΎΠΊ ΠΈ Ρ. Π΄.).
ΠΡΠΈ ΡΠ°ΡΡΠ΅ΡΠ΅ ΡΡΠ΅Π½ Π΅ΠΌΠΊΠΎΡΡΠ½ΠΎΠΉ ΡΠ°ΡΡΠΈ Π½Π΅ΠΎΠ±Ρ
ΠΎΠ΄ΠΈΠΌΠΎ ΡΠ°ΡΡΠΌΠ°ΡΡΠΈΠ²Π°ΡΡ ΡΠ»Π΅Π΄ΡΡΡΠΈΠ΅ ΡΠΎΡΠ΅ΡΠ°Π½ΠΈΡ Π½Π°Π³ΡΡΠ·ΠΎΠΊ: Π²ΡΠ΅ Π΅ΠΌΠΊΠΎΡΡΠΈ Π·Π°ΠΏΠΎΠ»Π½Π΅Π½Ρ, Π½Π° ΠΎΠ΄Π½Ρ ΠΈΠ· ΡΡΠ΅Π½ Π΄Π΅ΠΉΡΡΠ²ΡΠ΅Ρ ΠΎΡΡΠΈΡΠ°ΡΠ΅Π»ΡΠ½ΠΎΠ΅ Π΄Π°Π²Π»Π΅Π½ΠΈΠ΅ Π²Π΅ΡΡΠ° ΠΊΠ°ΠΊ Π½Π° ΠΏΠΎΠ΄Π²Π΅ΡΡΠ΅Π½Π½ΡΡ Π²Π΅ΡΡΠΈΠΊΠ°Π»ΡΠ½ΡΡ ΠΏΠΎΠ²Π΅ΡΡ
Π½ΠΎΡΡΡ; Π΅ΠΌΠΊΠΎΡΡΠΈ Π½Π΅ Π·Π°ΠΏΠΎΠ»Π½Π΅Π½Ρ, Π½Π° ΡΡΠ΅Π½Ρ Π΄Π΅ΠΉΡΡΠ²ΡΠ΅Ρ ΠΏΠΎΠ»ΠΎΠΆΠΈΡΠ΅Π»ΡΠ½ΠΎΠ΅ Π΄Π°Π²Π»Π΅Π½ΠΈΠ΅ Π²Π΅ΡΡΠ° ΠΊΠ°ΠΊ Π½Π° Π½Π°Π²Π΅ΡΡΠ΅Π½Π½ΡΡ Π²Π΅ΡΡΠΈΠΊΠ°Π»ΡΠ½ΡΡ ΠΏΠΎΠ²Π΅ΡΡ
Π½ΠΎΡΡΡ; Π·Π°ΠΏΠΎΠ»Π½Π΅Π½Π° ΠΎΠ΄Π½Π° ΠΈΠ· Π΅ΠΌΠΊΠΎΡΡΠ΅ΠΉ (Π΄Π»Ρ ΡΠ°ΡΡΠ΅ΡΠ° Π²Π½ΡΡΡΠ΅Π½Π½Π΅ΠΉ ΠΏΠΎΠΏΠ΅ΡΠ΅ΡΠ½ΠΎΠΉ ΡΡΠ΅Π½Ρ). ΠΏΡΠΎΠΈΠ·Π²ΠΎΠ΄ΡΡΠ²ΠΎ
Π£Π³ΠΎΠ»ΡΠ½ΡΡ Π±Π°ΡΠ½Ρ ΡΠ»Π΅Π΄ΡΠ΅Ρ ΡΠ°ΡΡΡΠΈΡΡΠ²Π°ΡΡ ΠΊΠ°ΠΊ ΠΏΡΠΎΡΡΡΠ°Π½ΡΡΠ²Π΅Π½Π½ΡΡ ΡΠΈΡΡΠ΅ΠΌΡ Ρ ΡΡΠ΅ΡΠΎΠΌ ΡΠΈΠ·ΠΈΡΠ΅ΡΠΊΠΎΠΉ, Π° Π΄Π»Ρ ΡΡΠ΅Π½ Π° Π·ΠΎΠ½Π΅ ΠΏΡΠΎΠ΅Π·Π΄Π° Π·Π°Π³ΡΡΠ·ΠΎΡΠ½ΠΎΠ³ΠΎ Π²Π°Π³ΠΎΠ½Π° β ΠΈ Π΅Π³ΠΎ Π³Π΅ΠΎΠΌΠ΅ΡΡΠΈΡΠ΅ΡΠΊΠΎΠΉ Π½Π΅Π»ΠΈΠ½Π΅ΠΉΠ½ΠΎΡΡΠΈ (ΠΏΠΎ Π΄Π΅ΡΠΎΡΠΌΠΈΡΠΎΠ²Π°Π½Π½ΠΎΠΉ ΡΡ
Π΅ΠΌΠ΅ Ρ ΡΡΠ΅ΡΠΎΠΌ Π½Π΅Π²ΡΠ³ΠΎΠ΄Π½ΡΡ
Π΄Π»Ρ ΠΊΠΎΠ½ΡΡΡΡΠΊΡΠΈΠΉ ΠΎΡΠΊΠ»ΠΎΠ½Π΅Π½ΠΈΠΉ ΠΎΡ Π²Π΅ΡΡΠΈΠΊΠ°Π»ΠΈ Π² ΠΏΡΠ΅Π΄Π΅Π»Π°Ρ
, Π΄ΠΎΠΏΡΡΠΊΠ°Π΅ΠΌΡΡ
ΡΡΡΠΎΠΈΡΠ΅Π»ΡΠ½ΡΠΌΠΈ Π½ΠΎΡΠΌΠ°ΠΌΠΈ ΠΈ ΠΏΡΠ°Π²ΠΈΠ»Π°ΠΌΠΈ Π½Π° ΠΏΡΠΎΠΈΠ·Π²ΠΎΠ΄ΡΡΠ²ΠΎ ΡΠ°Π±ΠΎΡ).
ΠΠΎΠΏΡΡΠΊΠ°Π΅ΡΡΡ Π²ΡΠΏΠΎΠ»Π½ΡΡΡ ΡΠ°ΡΡΠ΅Ρ ΡΡΠ΅Π½ ΡΠ³ΠΎΠ»ΡΠ½ΠΎΠΉ Π±Π°ΡΠ½ΠΈ, ΡΠ°ΡΡΠ»Π΅Π½ΡΡ Π΅Π΅ Π½Π° ΠΎΡΠ΄Π΅Π»ΡΠ½ΡΠ΅ ΡΠ»Π΅ΠΌΠ΅Π½ΡΡ ΠΏΡΠΎΠ΄ΠΎΠ»ΡΠ½ΡΠ΅ ΠΈ ΠΏΠΎΠΏΠ΅ΡΠ΅ΡΠ½ΡΠ΅ ΡΡΠ΅Π½Ρ Π΅ΠΌΠΊΠΎΡΡΠ½ΠΎΠΉ ΡΠ°ΡΡΠΈ, ΠΏΡΠΎΠ΄ΠΎΠ»ΡΠ½ΡΠ΅ ΡΡΠ΅Π½Ρ Π² Π·ΠΎΠ½Π΅ ΠΏΡΠΎΠ΅Π·Π΄Π° Π·Π°Π³ΡΡΠ·ΠΎΡΠ½ΠΎΠ³ΠΎ Π²Π°Π³ΠΎΠ½Π°, Π½ΠΈΠΆΠ½ΡΡ Π·ΠΎΠ½Ρ ΡΡΠ΅Π½. ΠΡΠΈ ΡΠ°ΡΡΠ΅ΡΠ° ΠΏΠΎΠΏΠ΅ΡΠ΅ΡΠ½ΡΡ ΡΡΠ΅Π½ Π΅ΠΌΠΊΠΎΡΡΠ½ΠΎΠΉ ΡΠ°ΡΡΠΈ ΡΠ»Π΅Π΄ΡΠ΅Ρ ΡΡΠΈΡΡΠ²Π°ΡΡ Π½Π°Π»ΠΈΡΠΈΠ΅ ΠΏΡΠΎΠ΅ΠΌΠΎΠ² Π΄Π»Ρ ΠΏΡΠΎΠ΅Π·Π΄Π° Π·Π°Π³ΡΡΠ·ΠΎΡΠ½ΠΎΠ³ΠΎ Π²Π°Π³ΠΎΠ½Π°, ΠΏΡΠ΅Π²ΡΠ°ΡΠ°ΡΡΠΈΡ ΡΡΠΈ ΡΡΠ΅Π½Ρ ΠΏΡΠΈ ΠΏΠΎΡΠ»Π΅ΠΌΠ΅Π½ΡΠ½ΠΎΠΌ ΡΠ°ΡΡΠ΅ΡΠ° Π² Π±Π°Π»ΠΊΠΈ-ΡΡΠ΅Π½ΠΊΠΈ.
Π ΡΠ³ΠΎΠ»ΡΠ½ΡΡ Π±Π°ΡΠ½ΡΡ Π΄ΠΎΠ»ΠΆΠ΅Π½ Π±ΡΡΡ ΠΏΡΠ΅Π΄ΡΡΠΌΠΎΡΡΠ΅Π½ Π³ΡΡΠ·ΠΎΠΏΠ°ΡΡΠ°ΠΆΠΈΡΡΠΊΠΈΠΉ Π»ΠΈΡΡ Π΄ΠΎ Π½Π°Π΄ΡΠ΅ΠΌΠΊΠΎΡΡΠ½ΠΎΠΉ ΡΠ°ΡΡΠΈ. ΠΠ»Ρ ΠΎΠ±Π΅ΡΠΏΠ΅ΡΠ΅Π½ΠΈΡ ΠΏΠΎΠΆΠ°ΡΠ½ΠΎΠΉ Π±Π΅Π·ΠΎΠΏΠ°ΡΠ½ΠΎΡΡΠΈ Π½Π΅ΠΎΠ±Ρ ΠΎΠ΄ΠΈΠΌΠΎ ΠΏΡΠ΅Π΄ΡΡΠΌΠ°ΡΡΠΈΠ²Π°ΡΡ Π ΠΏΠΎΠΌΠ΅ΡΠ΅Π½ΠΈΡΡ ΡΠ³ΠΎΠ»ΡΠ½ΠΎΠΉ Π±Π°ΡΠ½ΠΈ ΠΏΠΎΠΆΠ°ΡΠ½ΠΎ-ΠΏΠΈΡΡΠ΅Π²ΠΎΠΉ Π²ΠΎΠ΄ΠΎΠΏΡΠΎΠ²ΠΎΠ΄.
rezervuar.info
Π‘ΠΈΠ»ΠΎΡΡ ΠΈ Π±ΡΠ½ΠΊΠ΅ΡΡ | ΠΠΠ «ΠΠΏΡΡΠ½ΡΠΉ Π·Π°Π²ΠΎΠ΄ ΡΠ΅Π·Π΅ΡΠ²ΡΠ°ΡΠΎΠ² ΠΈ ΠΌΠ΅ΡΠ°Π»Π»ΠΎΠΊΠΎΠ½ΡΡΡΡΠΊΡΠΈΠΉ»
Π‘ΠΈΠ»ΠΎΡΡ ΠΈ Π±ΡΠ½ΠΊΠ΅ΡΡ ΠΏΡΠΎΠΈΠ·Π²ΠΎΠ΄ΡΡΠ²Π° Π·Π°Π²ΠΎΠ΄Π° ΠΠΠ βΠΠΏΡΡΠ½ΡΠΉ Π·Π°Π²ΠΎΠ΄ ΡΠ΅Π·Π΅ΡΠ²ΡΠ°ΡΠΎΠ² ΠΈ ΠΌΠ΅ΡΠ°Π»Π»ΠΎΠΊΠΎΠ½ΡΡΡΡΠΊΡΠΈΠΉβ ΠΎΡΠ»ΠΈΡΠ°ΡΡΡΡ Π²ΡΡΠΎΠΊΠΎΠΉ Π½Π°Π΄Π΅ΠΆΠ½ΠΎΡΡΡΡ ΠΈ ΡΠ΅Ρ Π½ΠΎΠ»ΠΎΠ³ΠΈΡΠ½ΠΎΡΡΡΡ ΠΊΠΎΠ½ΡΡΡΡΠΊΡΠΈΠΈ.ΠΠ°Π²ΠΎΠ΄ βΠΠΠ Πβ Π²ΡΠΏΠΎΠ»Π½ΡΠ΅Ρ ΠΈΠ·Π³ΠΎΡΠΎΠ²Π»Π΅Π½ΠΈΠ΅ ΡΠΈΠ»ΠΎΡΠΎΠ² Π΄Π»Ρ ΡΠ΅ΠΌΠ΅Π½ΡΠ°, Π±ΡΠ½ΠΊΠ΅ΡΠΎΠ² Π΄Π»Ρ ΡΠ΅ΠΌΠ΅Π½ΡΠ°, Π·Π΅ΡΠ½Π°, ΡΡΡ ΠΎΠ³ΠΎ ΠΈ ΠΌΠΎΠΊΡΠΎΠ³ΠΎ ΠΏΠ΅ΡΠΊΠ°, ΠΊΠ²Π°ΡΡΠ°, ΠΌΠ΅Π»Π°, Π³ΠΈΠΏΡΠΎΠ²ΠΎΠ³ΠΎ ΠΏΠΎΡΠΎΡΠΊΠ° ΠΈ Π΄ΡΡΠ³ΠΈΡ ΡΡΡ ΠΈΡ Π²Π΅ΡΠ΅ΡΡΠ².
Π‘ΠΈΠ»ΠΎΡΡ Π΄Π»Ρ ΡΠ΅ΠΌΠ΅Π½ΡΠ°. ΠΠ±ΡΠ΅ΠΌΡ ΡΠΈΠ»ΠΎΡΠ½ΡΡ ΠΊΠΎΠ½ΡΡΡΡΠΊΡΠΈΠΉ: 5, 10, 15, 20, 25, 30, 35, 40, 45, 50, 60, 70, 80, 90, 100, 130, 150, 200, 250, 300, 350, 400, 500, 1000 ΡΠΎΠ½Π½ ΠΈ Π±ΠΎΠ»Π΅Π΅.
Π‘ΠΈΠ»ΠΎΡΡ Π΄Π»Ρ ΡΠ΅ΠΌΠ΅Π½ΡΠ° ΠΈΠ· ΡΠ΅ΡΠ½ΠΎΠΉ ΠΈ Π½Π΅ΡΠΆΠ°Π²Π΅ΡΡΠ΅ΠΉ ΡΡΠ°Π»ΠΈ β ΡΡΠΎ ΠΎΡΠ½ΠΎΠ²Π½ΠΎΠ΅ Π½Π°ΠΏΡΠ°Π²Π»Π΅Π½ΠΈΠ΅ ΠΏΡΠΎΠΈΠ·Π²ΠΎΠ΄ΡΡΠ²Π΅Π½Π½ΠΎΠΉ Π΄Π΅ΡΡΠ΅Π»ΡΠ½ΠΎΡΡΠΈ Π½Π°ΡΠ΅Π³ΠΎ Π·Π°Π²ΠΎΠ΄Π°!
Π¦Π΅ΠΌΠ΅Π½ΡΠ½ΡΠΉ ΡΠΈΠ»ΠΎΡ ΡΡΠΎ ΠΌΠ΅ΡΠ°Π»Π»ΠΈΡΠ΅ΡΠΊΠ°Ρ ΡΠΌΠΊΠΎΡΡΡ Π² Π²ΠΈΠ΄Π΅ ΡΠΈΠ»ΠΈΠ½Π΄ΡΠ° (Π±ΠΎΡΠΊΠΈ), Π² ΠΊΠΎΡΠΎΡΠΎΠΉ Ρ ΡΠ°Π½ΡΡΡΡ ΡΡΠΏΡΡΠΈΠ΅ Π²Π΅ΡΠ΅ΡΡΠ²Π°, Π² ΡΠΎΠΌ ΡΠΈΡΠ»Π΅ ΡΠ΅ΠΌΠ΅Π½Ρ, ΠΈΠ·Π²Π΅ΡΡΡ, ΠΏΠ΅ΡΠΎΠΊ, Π·Π΅ΡΠ½ΠΎ ΠΈ Ρ.ΠΏ.
ΠΠΎΠ½ΡΠ°ΠΆ ΡΠΈΠ»ΠΎΡΠΎΠ² ΠΏΡΠΎΠΈΠ·Π²ΠΎΠ΄ΠΈΡΡΡ Π²Π΅ΡΡΠΈΠΊΠ°Π»ΡΠ½ΠΎ Π½Π° ΠΎΠΏΠΎΡΠ°Ρ ΠΈΠ·Π³ΠΎΡΠΎΠ²Π»Π΅Π½Π½ΡΡ ΠΈΠ· ΡΡΡΠ± ΠΈΠ»ΠΈ ΡΠ²Π΅Π»Π»Π΅ΡΠ° (ΠΌΠ΅ΡΠ°Π»Π»ΠΎΠΏΡΠΎΠΊΠ°Ρ).
Π‘ΠΈΠ»ΠΎΡ ΡΠ΅ΠΌΠ΅Π½ΡΠ° ΠΊΠ°ΠΊ ΠΈ Π»ΡΠ±ΠΎΠΉ Π΄ΡΡΠ³ΠΎ ΡΠΈΠ»ΠΎΡ Π·Π°ΠΊΠ°Π½ΡΠΈΠ²Π°Π΅ΡΡΡ ΠΊΠΎΠ½ΡΡΠΎΠΌ, Π½Π° ΠΊΠΎΠ½ΡΠ΅ ΠΊΠΎΡΠΎΡΠΎΠ³ΠΎ ΡΡΡΠ°Π½ΠΎΠ²Π»Π΅Π½ ΡΠΈΠ±Π΅ΡΠ½ΡΠΉ Π·Π°ΡΠ²ΠΎΡ. Π‘ ΠΏΠΎΠΌΠΎΡΡΡ Π³Π΅ΠΎΠΌΠ΅ΡΡΠΈΠΈ ΠΊΠΎΠ½ΡΡΠ°, ΡΠ΅ΠΌΠ΅Π½Ρ Π² ΡΠΈΠ»ΠΎΡΠ΅ ΡΠ°ΠΌΠΎΡΠ΅ΠΊΠΎΠΌ ΠΏΠΎΡΡΡΠΏΠ°Π΅Ρ Π² ΡΠΈΠ±Π΅ΡΠ½ΡΠΉ Π·Π°ΡΠ²ΠΎΡ, Π° ΠΎΡΡΡΠ΄Π° ΠΏΠΎΠΏΠ°Π΄Π°Π΅Ρ Π΄Π»Ρ Π΄Π°Π»ΡΠ½Π΅ΠΉΡΠ΅ΠΉ ΡΠ°Π·Π΄Π°ΡΠΈ Π² ΡΠ½Π΅ΠΊ ΠΈΠ»ΠΈ Π² ΡΠ΅ΠΌΠ΅Π½ΡΠ½ΡΠΉ Π½Π°ΡΠΎΡ.
Π‘ΠΊΠ»Π°Π΄ ΡΠ΅ΠΌΠ΅Π½ΡΠ° (ΡΠΈΠ»ΠΎΡΠ½ΡΠΉ ΡΠΊΠ»Π°Π΄) β ΡΡΠΎ ΡΠΈΡΡΠ΅ΠΌΠ° ΠΎΠ±ΠΎΡΡΠ΄ΠΎΠ²Π°Π½ΠΈΡ, ΠΏΡΠ΅Π΄Π½Π°Π·Π½Π°ΡΠ΅Π½Π½Π°Ρ Π΄Π»Ρ Π·Π°Π³ΡΡΠ·ΠΊΠΈ ΡΠΈΠ»ΠΎΡΠΎΠ² ΡΠ΅ΠΌΠ΅Π½ΡΠΎΠΌ Ρ ΡΡΠ°Π½ΡΠΏΠΎΡΡΠ½ΡΡ
ΡΡΠ΅Π΄ΡΡΠ², Ρ
ΡΠ°Π½Π΅Π½ΠΈΡ ΡΠ΅ΠΌΠ΅Π½ΡΠ° Π² ΡΠΈΠ»ΠΎΡΠ°Ρ
, Π° ΡΠ°ΠΊΠΆΠ΅ Π²ΡΠ³ΡΡΠ·ΠΊΠΈ ΡΠ΅ΠΌΠ΅Π½ΡΠ° Π΄Π»Ρ Π΅Π³ΠΎ Π΄Π°Π»ΡΠ½Π΅ΠΉΡΠ΅Π³ΠΎ ΠΏΠΎΡΡΠ΅Π±Π»Π΅Π½ΠΈΡ ΡΠ°ΠΊΠΈΠΌΠΈ ΠΏΡΠ΅Π΄ΠΏΡΠΈΡΡΠΈΡΠΌΠΈ ΠΊΠ°ΠΊ ΠΠ‘Π£ (Π±Π΅ΡΠΎΠ½Π½ΠΎ-ΡΠΌΠ΅ΡΠΈΡΠ΅Π»ΡΠ½ΡΠΉ ΡΠ·Π΅Π»), ΠΠΠ (Π°ΡΡΠ°Π»ΡΡΠΎΠ±Π΅ΡΠΎΠ½Π½ΡΠΉ Π·Π°Π²ΠΎΠ΄) ΠΈ Π΄ΡΡΠ³ΠΈΠΌΠΈ Π±Π΅ΡΠΎΠ½Π½ΡΠΌΠΈ Π·Π°Π²ΠΎΠ΄Π°ΠΌΠΈ.
Π‘ΠΊΠ»Π°Π΄ ΡΠ΅ΠΌΠ΅Π½ΡΠ° (ΡΠΈΠ»ΠΎΡΠ½ΡΠΉ ΡΠΊΠ»Π°Π΄) Π²ΠΊΠ»ΡΡΠ°Π΅Ρ Π² ΡΠ΅Π±Ρ ΠΎΠ΄ΠΈΠ½ Π½Π΅ΡΠΊΠΎΠ»ΡΠΊΠΎ ΡΠΈΠ»ΠΎΡΠΎΠ² ΠΈΠ»ΠΈ Π±ΡΠ½ΠΊΠ΅ΡΠΎΠ², ΠΎΠ±ΠΎΡΡΠ΄ΠΎΠ²Π°Π½ΠΈΠ΅ Π΄Π»Ρ Π·Π°Π³ΡΡΠ·ΠΊΠΈ ΡΠ΅ΠΌΠ΅Π½ΡΠ°, ΡΠ΅ΠΌΠ΅Π½ΡΠΎΠΏΡΠΎΠ²ΠΎΠ΄, ΠΈ ΠΎΠ±ΠΎΡΡΠ΄ΠΎΠ²Π°Π½ΠΈΠ΅ Π΄Π»Ρ Π²ΡΠ³ΡΡΠ·ΠΊΠΈ ΡΠ΅ΠΌΠ΅Π½ΡΠ°.
ΠΠ±ΠΎΡΡΠ΄ΠΎΠ²Π°Π½ΠΈΠ΅ Π΄Π»Ρ Π·Π°Π³ΡΡΠ·ΠΊΠΈ ΡΠΈΠ»ΠΎΡΠΎΠ² Π²ΠΊΠ»ΡΡΠ°Π΅Ρ Π² ΡΠ΅Π±Ρ ΠΎΠ±ΠΎΡΡΠ΄ΠΎΠ²Π°Π½ΠΈΠ΅ Π΄Π»Ρ ΡΠ°Π·Π³ΡΡΠ·ΠΊΠΈ ΠΆΠ΅Π»Π΅Π·Π½ΠΎΠ΄ΠΎΡΠΎΠΆΠ½ΡΡ
Ρ
ΠΎΠΏΡΠΎΠ², ΡΡΡΠ°Π½ΠΎΠ²ΠΊΠ° Π΄Π»Ρ ΡΠ°ΡΡΠ°ΡΠΊΠΈ ΠΊΠΎΠ½ΡΠ΅ΠΉΠ½Π΅ΡΠΎΠ² Β«Π±ΠΈΠ³-Π±Π΅Π³ΠΎΠ²Β». Π¦Π΅ΠΌΠ΅Π½ΡΠΎΠΏΡΠΎΠ²ΠΎΠ΄ β ΡΡΠΎ ΠΌΠ΅ΡΠ°Π»Π»ΠΈΡΠ΅ΡΠΊΠΈΠ΅ ΡΡΡΠ±Ρ ΠΏΠΎΠ΄Π°ΡΡΠΈΠ΅ ΡΠ΅ΠΌΠ΅Π½Ρ ΠΎΡ ΠΌΠ΅ΡΡΠ° ΡΠ°Π·Π³ΡΡΠ·ΠΊΠΈ ΡΠ΅ΠΌΠ΅Π½ΡΠ° Π΄ΠΎ ΡΠΈΠ»ΠΎΡΠΎΠ² ΡΠ΅ΠΌΠ΅Π½ΡΠ°. ΠΠ»Ρ Π½Π°ΠΏΠΎΠ»Π½Π΅Π½ΠΈΡ Π² ΠΎΡΠ΄Π΅Π»ΡΠ½ΠΎΡΡΠΈ ΠΊΠ°ΠΆΠ΄ΠΎΠ³ΠΎ ΡΠΈΠ»ΠΎΡΠ° ΡΠ΅ΠΌΠ΅Π½ΡΠ° Π½Π° ΡΠ΅ΠΌΠ΅Π½ΡΠΎΠΏΡΠΎΠ²ΠΎΠ΄Π΅ ΠΈΡΠΏΠΎΠ»ΡΠ·ΡΡΡΡΡ ΠΏΠ΅ΡΠ΅ΠΊΠ»ΡΡΠ°ΡΠ΅Π»ΠΈ ΠΏΠΎΡΠΎΠΊΠ°, ΠΊΠΎΡΠΎΡΡΠ΅ ΠΏΠΎΠ·Π²ΠΎΠ»ΡΡΡ ΡΠ΅Π³ΡΠ»ΠΈΡΠΎΠ²Π°ΡΡ ΡΠ΅ΠΌΠ΅Π½ΡΠ½ΡΠΉ ΠΏΠΎΡΠΎΠΊ Π΄Π»Ρ Π·Π°ΠΏΠΎΠ»Π½Π΅Π½ΠΈΡ ΠΎΡΠ²ΠΎΠ±ΠΎΠ΄ΠΈΠ²ΡΠΈΡ
ΡΡ ΠΎΡ ΡΠ΅ΠΌΠ΅Π½ΡΠ° ΡΠΈΠ»ΠΎΡΠΎΠ².
ΠΠ°Ρ Π·Π°Π²ΠΎΠ΄ ΡΠ°ΠΊΠΆΠ΅ ΠΈΠ·Π³ΠΎΡΠ°Π²Π»ΠΈΠ²Π°Π΅Ρ ΠΎΠ±ΠΎΡΡΠ΄ΠΎΠ²Π°Π½ΠΈΠ΅ Π΄Π»Ρ ΡΠ°Π·Π³ΡΡΠ·ΠΊΠΈ Π΄Π»Ρ ΡΠ°Π·Π³ΡΡΠ·ΠΊΠΈ ΠΆΠ΅Π»Π΅Π·Π½ΠΎΠ΄ΠΎΡΠΎΠΆΠ½Ρ Ρ
ΠΎΠΏΡΠΎΠ², ΡΡΡΠ°Π½ΠΎΠ²ΠΊΠΈ ΡΠ°ΡΡΠ°ΡΠΊΠΈ ΠΊΠΎΠ½ΡΠ΅ΠΉΠ½Π΅ΡΠΎΠ² βΠ±ΠΈΠ³-Π±Π΅Π³ΠΎΠ²β, Π²ΠΈΠ½ΡΠΎΠ²ΡΠ΅ ΡΠ΅ΠΌΠ΅Π½ΡΠ½ΡΡ
Π½Π°ΡΠΎΡΡ, ΠΊΠ°ΠΌΠ΅ΡΠ½ΡΠ΅ ΡΠ΅ΠΌΠ΅Π½ΡΠ½ΡΠ΅ Π½Π°ΡΠΎΡΡ.
Π‘ΠΈΠ»ΠΎΡΡ ΡΠ΅ΠΌΠ΅Π½ΡΠ° ΠΏΡΠ΅Π΄Π½Π°Π·Π½Π°ΡΠ΅Π½Ρ Π΄Π»Ρ Ρ ΡΠ°Π½Π΅Π½ΠΈΡ ΡΠ°Π·Π»ΠΈΡΠ½ΡΡ ΡΡΠΏΡΡΠΈΡ Π²Π΅ΡΠ΅ΡΡΠ², Π² ΡΠΎΠΌ ΡΠΈΡΠ»Π΅ ΡΠ΅ΠΌΠ΅Π½ΡΠ°, ΠΏΠ΅ΡΠΊΠ°, ΠΈΠ·Π²Π΅ΡΡΠΈ, Π·Π΅ΡΠ½Π° ΠΈ.ΠΏ. Π‘ΠΈΠ»ΠΎΡΠ° Π²ΡΠΏΠΎΠ»Π½ΡΡΡ ΡΡΠ½ΠΊΡΠΈΠΈ Ρ ΡΠ°Π½Π΅Π½ΠΈΡ ΠΈ ΠΏΠΎΠ΄Π°ΡΠΈ ΡΠ΅ΠΌΠ΅Π½ΡΠ° Π² Π²Π΅ΡΠΎΠ²ΠΎΠΉ Π΄ΠΎΠ·Π°ΡΠΎΡ Π±Π΅ΡΠΎΠ½Π½ΠΎΠ³ΠΎ Π·Π°Π²ΠΎΠ΄Π°, Π±Π΅ΡΠΎΠ½ΠΎΡΠΌΠ΅ΡΠΈΡΠ΅Π»ΡΠ½ΠΎΠΉ ΡΡΡΠ°Π½ΠΎΠ²ΠΊΠΈ (ΠΠ‘Π£), ΡΠ΅ΠΌΠ΅Π½ΡΠΎΠ²ΠΎΠ·Π° ΠΈ Ρ.ΠΏ.
CΠΈΠ»ΠΎΡ Π΄Π»Ρ ΡΠ΅ΠΌΠ΅Π½ΡΠ° 1000 ΡΠΎΠ½Π½ (ΡΠ΅ΡΡΠ΅ΠΆ ΠΎΠ±ΡΠ΅Π³ΠΎ Π²ΠΈΠ΄Π°).
Π‘ΠΈΠ»ΠΎΡΡ ΠΈ Π±ΡΠ½ΠΊΠ΅ΡΡ. ΠΡΠΈΠΌΠ΅ΡΡ ΠΎΠ±ΠΎΠ·Π½Π°ΡΠ΅Π½ΠΈΡ ΠΏΡΠΈ Π·Π°ΠΊΠ°Π·Π΅:
Π‘ΠΈΠ»ΠΎΡ Π΄Π»Ρ ΡΠ΅ΠΌΠ΅Π½ΡΠ° 5 ΡΠΎΠ½Π½, ΡΠΈΠ»ΠΎΡ ΡΠ΅ΠΌΠ΅Π½ΡΠ° 5 ΠΌ3, ΡΠΈΠ»ΠΎΡ Π΄Π»Ρ ΡΠ΅ΠΌΠ΅Π½ΡΠ° 10 ΡΠΎΠ½Π½, ΡΠΈΠ»ΠΎΡ ΡΠ΅ΠΌΠ΅Π½ΡΠ° 10 ΠΌ3; ΡΠΈΠ»ΠΎΡ Π΄Π»Ρ ΡΠ΅ΠΌΠ΅Π½ΡΠ° 15 ΡΠΎΠ½Π½, ΡΠΈΠ»ΠΎΡ ΡΠ΅ΠΌΠ΅Π½ΡΠ° 15 ΠΌ3; ΡΠΈΠ»ΠΎΡ Π΄Π»Ρ ΡΠ΅ΠΌΠ΅Π½ΡΠ° 20 ΡΠΎΠ½Π½, ΡΠΈΠ»ΠΎΡ ΡΠ΅ΠΌΠ΅Π½ΡΠ° 20 ΠΌ3; ΡΠΈΠ»ΠΎΡ Π΄Π»Ρ ΡΠ΅ΠΌΠ΅Π½ΡΠ° 25 ΡΠΎΠ½Π½, ΡΠΈΠ»ΠΎΡ ΡΠ΅ΠΌΠ΅Π½ΡΠ° 25 ΠΌ3, ΡΠΈΠ»ΠΎΡ Π΄Π»Ρ ΡΠ΅ΠΌΠ΅Π½ΡΠ° 30 ΡΠΎΠ½Π½, ΡΠΈΠ»ΠΎΡ ΡΠ΅ΠΌΠ΅Π½ΡΠ° 30 ΠΌ3; ΡΠΈΠ»ΠΎΡ Π΄Π»Ρ ΡΠ΅ΠΌΠ΅Π½ΡΠ° 35 ΡΠΎΠ½Π½, ΡΠΈΠ»ΠΎΡ ΡΠ΅ΠΌΠ΅Π½ΡΠ° 35 ΠΌ3, ΡΠΈΠ»ΠΎΡ Π΄Π»Ρ ΡΠ΅ΠΌΠ΅Π½ΡΠ° 40 ΡΠΎΠ½Π½, ΡΠΈΠ»ΠΎΡ ΡΠ΅ΠΌΠ΅Π½ΡΠ° 40 ΠΌ3, ΡΠΈΠ»ΠΎΡ Π΄Π»Ρ ΡΠ΅ΠΌΠ΅Π½ΡΠ° 45 ΡΠΎΠ½Π½, ΡΠΈΠ»ΠΎΡ ΡΠ΅ΠΌΠ΅Π½ΡΠ° 45 ΠΌ3; ΡΠΈΠ»ΠΎΡ Π΄Π»Ρ ΡΠ΅ΠΌΠ΅Π½ΡΠ° 50 ΡΠΎΠ½Π½, ΡΠΈΠ»ΠΎΡ ΡΠ΅ΠΌΠ΅Π½ΡΠ° 50 ΠΌ3; ΡΠΈΠ»ΠΎΡ Π΄Π»Ρ ΡΠ΅ΠΌΠ΅Π½ΡΠ° 55 ΡΠΎΠ½Π½, ΡΠΈΠ»ΠΎΡ ΡΠ΅ΠΌΠ΅Π½ΡΠ° 55 ΠΌ3; ΡΠΈΠ»ΠΎΡ Π΄Π»Ρ ΡΠ΅ΠΌΠ΅Π½ΡΠ° 60 ΡΠΎΠ½Π½, ΡΠΈΠ»ΠΎΡ ΡΠ΅ΠΌΠ΅Π½ΡΠ° 60 ΠΌ3, ΡΠΈΠ»ΠΎΡ Π΄Π»Ρ ΡΠ΅ΠΌΠ΅Π½ΡΠ° 70 ΡΠΎΠ½Π½, ΡΠΈΠ»ΠΎΡ ΡΠ΅ΠΌΠ΅Π½ΡΠ° 70 ΠΌ3, ΡΠΈΠ»ΠΎΡ Π΄Π»Ρ ΡΠ΅ΠΌΠ΅Π½ΡΠ° 75 ΡΠΎΠ½Π½ (ΡΠΈΠ»ΠΎΡ ΡΠ΅ΠΌΠ΅Π½ΡΠ° 75 ΠΌ3, ΡΠΈΠ»ΠΎΡ Π΄Π»Ρ ΡΠ΅ΠΌΠ΅Π½ΡΠ° 80 ΡΠΎΠ½Π½, ΡΠΈΠ»ΠΎΡ ΡΠ΅ΠΌΠ΅Π½ΡΠ° 80 ΠΌ3,ΡΠΈΠ»ΠΎΡ Π΄Π»Ρ ΡΠ΅ΠΌΠ΅Π½ΡΠ° 90 ΡΠΎΠ½Π½, ΡΠΈΠ»ΠΎΡ ΡΠ΅ΠΌΠ΅Π½ΡΠ° 90 ΠΌ3, ΡΠΈΠ»ΠΎΡ Π΄Π»Ρ ΡΠ΅ΠΌΠ΅Π½ΡΠ° 100 ΡΠΎΠ½Π½ (ΡΠΈΠ»ΠΎΡ ΡΠ΅ΠΌΠ΅Π½ΡΠ° 100 ΠΌ3, ΡΠΈΠ»ΠΎΡ Π΄Π»Ρ ΡΠ΅ΠΌΠ΅Π½ΡΠ° 110 ΡΠΎΠ½Π½, ΡΠΈΠ»ΠΎΡ ΡΠ΅ΠΌΠ΅Π½ΡΠ° 110 ΠΌ3, ΡΠΈΠ»ΠΎΡ Π΄Π»Ρ ΡΠ΅ΠΌΠ΅Π½ΡΠ° 120 ΡΠΎΠ½Π½, ΡΠΈΠ»ΠΎΡ ΡΠ΅ΠΌΠ΅Π½ΡΠ° 120 ΠΌ3, ΡΠΈΠ»ΠΎΡ Π΄Π»Ρ ΡΠ΅ΠΌΠ΅Π½ΡΠ° 130 ΡΠΎΠ½Π½, ΡΠΈΠ»ΠΎΡ ΡΠ΅ΠΌΠ΅Π½ΡΠ° 130 ΠΌ3, ΡΠΈΠ»ΠΎΡ Π΄Π»Ρ ΡΠ΅ΠΌΠ΅Π½ΡΠ° 140 ΡΠΎΠ½Π½, ΡΠΈΠ»ΠΎΡ ΡΠ΅ΠΌΠ΅Π½ΡΠ° 140 ΠΌ3, ΡΠΈΠ»ΠΎΡ Π΄Π»Ρ ΡΠ΅ΠΌΠ΅Π½ΡΠ° 150 ΡΠΎΠ½Π½, ΡΠΈΠ»ΠΎΡ ΡΠ΅ΠΌΠ΅Π½ΡΠ° 150 ΠΌ3, ΡΠΈΠ»ΠΎΡ Π΄Π»Ρ ΡΠ΅ΠΌΠ΅Π½ΡΠ° 200 ΡΠΎΠ½Π½, ΡΠΈΠ»ΠΎΡ ΡΠ΅ΠΌΠ΅Π½ΡΠ° 200 ΠΌ3, ΡΠΈΠ»ΠΎΡ Π΄Π»Ρ ΡΠ΅ΠΌΠ΅Π½ΡΠ° 250 ΡΠΎΠ½Π½, ΡΠΈΠ»ΠΎΡ ΡΠ΅ΠΌΠ΅Π½ΡΠ° 250 ΠΌ3, ΡΠΈΠ»ΠΎΡ Π΄Π»Ρ ΡΠ΅ΠΌΠ΅Π½ΡΠ° 300 ΡΠΎΠ½Π½, ΡΠΈΠ»ΠΎΡ ΡΠ΅ΠΌΠ΅Π½ΡΠ° 300 ΠΌ3, ΡΠΈΠ»ΠΎΡ Π΄Π»Ρ ΡΠ΅ΠΌΠ΅Π½ΡΠ° 350 ΡΠΎΠ½Π½, ΡΠΈΠ»ΠΎΡ ΡΠ΅ΠΌΠ΅Π½ΡΠ° 350 ΠΌ3, ΡΠΈΠ»ΠΎΡ Π΄Π»Ρ ΡΠ΅ΠΌΠ΅Π½ΡΠ° 400 ΡΠΎΠ½Π½, ΡΠΈΠ»ΠΎΡ ΡΠ΅ΠΌΠ΅Π½ΡΠ° 400 ΠΌ3, ΡΠΈΠ»ΠΎΡ Π΄Π»Ρ ΡΠ΅ΠΌΠ΅Π½ΡΠ° 500 ΡΠΎΠ½Π½, ΡΠΈΠ»ΠΎΡ ΡΠ΅ΠΌΠ΅Π½ΡΠ° 500 ΠΌ3, ΡΠΈΠ»ΠΎΡ Π΄Π»Ρ ΡΠ΅ΠΌΠ΅Π½ΡΠ° 1000 ΡΠΎΠ½Π½, ΡΠΈΠ»ΠΎΡ ΡΠ΅ΠΌΠ΅Π½ΡΠ° 1000 ΠΌ3, ΡΠΈΠ»ΠΎΡ Π΄Π»Ρ ΡΠ΅ΠΌΠ΅Π½ΡΠ° 1500 ΡΠΎΠ½Π½, ΡΠΈΠ»ΠΎΡ ΡΠ΅ΠΌΠ΅Π½ΡΠ° 1500 ΠΌ3,
ΡΠΈΠ»ΠΎΡ Π΄Π»Ρ ΡΠ΅ΠΌΠ΅Π½ΡΠ° 2000 ΡΠΎΠ½Π½, ΡΠΈΠ»ΠΎΡ ΡΠ΅ΠΌΠ΅Π½ΡΠ° 2000 ΠΌ3.
Π¦Π΅ΠΌΠ΅Π½Ρ, ΠΏΠΎΠ»ΡΡΠ΅Π½Π½ΡΠΉ Π² ΠΏΠΎΠΌΠΎΠ»ΡΠ½ΠΎΠΌ ΠΎΡΠ΄Π΅Π»Π΅Π½ΠΈΠΈ, ΡΡΠ°Π½ΡΠΏΠΎΡΡΠΈΡΡΒΠ΅ΡΡΡ ΡΠΈΡΡΠ΅ΠΌΠΎΠΉ ΠΏΠ½Π΅Π²ΠΌΠΎΡΡΠ°Π½ΡΠΏΠΎΡΡΠ° Π² ΡΠ΅ΠΌΠ΅Π½ΡΠ½ΡΠ΅ ΡΠΈΠ»ΠΎΒΡΡ Π΄Π»Ρ Ρ
ΡΠ°Π½Π΅Π½ΠΈΡ.
ΠΠΎΠ»ΠΈΡΠ΅ΡΡΠ²ΠΎ Π΅ΠΌΠΊΠΎΡΡΠ΅ΠΉ (ΡΠΈΠ»ΠΎΡΠ½ΡΡ
Π±Π°Π½ΠΎΠΊ) Π΄Π»Ρ Ρ
ΡΠ°Π½Π΅Π½ΠΈΡ ΡΠ΅ΠΌΠ΅Π½ΡΠ° ΠΎΠΏΡΠ΅Π΄Π΅Π»ΡΠ΅ΡΡΡ Π°ΡΡΠΎΡΡΠΈΠΌΠ΅Π½ΡΠΎΠΌ ΠΈ ΡΡΡΠΎΡΠ½ΠΎΠΉ Π²ΡΡΠ°Π±ΠΎΡΠΊΠΎΠΉ ΡΡΠΏΡΡΠΈΡ
ΠΌΠ΅ΡΠ°ΡΠΈΠ°Π»ΠΎΠ².
ΠΠ»Ρ Ρ
ΡΠ°Π½Π΅Π½ΠΈΡ ΡΠ΅ΠΌΠ΅Π½ΡΠ° ΠΎΠ±ΡΡΠ½ΠΎ ΠΈΡΠΏΠΎΠ»ΡΠ·ΡΡΡ Π²Π΅ΡΡΠΈΠΊΠ°Π»ΡΠ½ΡΠ΅ ΡΠΈΠ»ΠΈΠ½Π΄ΡΠΈΡΠ΅ΡΠΊΠΈΠ΅ ΡΠΈΠ»ΠΎΡΡ ΠΈΠ»ΠΈ Π±ΡΠ½ΠΊΠ΅ΡΡ.
Π‘ΠΈΠ»ΠΎΡΡ ΠΈ Π±ΡΠ½ΠΊΠ΅ΡΡ ΠΎΠ±Π΅ΡΠΏΠ΅ΡΠΈΠ²Π°ΡΡ Ρ
ΠΎΡΠΎΡΠΈΠ΅ ΡΡΠ»ΠΎΠ²ΠΈΡ Π΄Π»Ρ Ρ
ΡΠ°Π½Π΅Π½ΠΈΡ ΠΈ ΡΠ°Π·Π³ΡΡΠ·ΠΊΠΈ ΡΠ΅ΠΌΠ΅Π½ΡΠ°. Π Π°Π·ΡΡΡΠ΅Π½ΠΈΠ΅ ΡΠ²ΠΎΠ΄Π° ΡΠΎΠΏΡΠΎΠ²ΠΎΠΆΠ΄Π°Π΅ΡΡΡ ΠΏΠ°Π΄Π΅Π½ΠΈΠ΅ΠΌ Π±ΠΎΠ»ΡΡΠΈΡ
ΠΌΠ°ΡΡ ΠΌΠ°ΡΠ΅ΡΠΈΠ°Π»Π° ΠΈ ΠΌΠΎΠΆΠ΅Ρ Π²ΡΠ·Π²Π°ΡΡ ΡΠ°Π·ΡΡΡΠ΅Π½ΠΈΠ΅ ΡΠΈΠ»ΠΎΡΠ°.
Π£Π΄Π΅Π»ΡΠ½Π°Ρ ΡΡΠΎΠΈΠΌΠΎΡΡΡ ΡΠΈΠ»ΠΎΡΠ½ΠΎΠΉ ΡΡΠ»ΠΎΠ½Π½ΠΎΠΉ ΠΈΠ»ΠΈ ΠΏΠΎΠ»ΠΈΡΡΠΎΠ²ΠΎΠΉ ΠΊΠΎΠ½ΡΡΡΡΠΊΡΠΈΠΈ ΡΠ½ΠΈΠΆΠ°Π΅ΡΡΡ Ρ ΡΠ²Π΅Π»ΠΈΡΠ΅Π½ΠΈΠ΅ΠΌ Π²ΠΎΠ±ΡΠ΅ΠΌΠ° ΡΠΈΠ»ΠΎΡΠ°, ΠΏΠΎΡΡΠΎΠΌΡ ΡΡΡΠΎΠΈΡΠ΅Π»ΡΡΡΠ²ΠΎ Π½Π΅Π±ΠΎΠ»ΡΡΠΎΠ³ΠΎ ΠΊΠΎΠ»ΠΈΡΠ΅ΡΡΠ²Π° ΠΊΡΡΠΏΠ½ΡΡ
ΡΠ΅ΠΌΠ΅Π½ΡΠ½ΡΡ
ΡΠΈΠ»ΠΎΡΠΎΠ² Π±ΠΎΠ»Π΅Π΅ Π²ΡΠ³ΠΎΠ΄Π½ΠΎ, ΡΠ΅ΠΌ ΠΈΡΠΏΠΎΠ»ΡΠ·ΠΎΠ²Π°Π½ΠΈΠ΅ Π±ΠΎΠ»ΡΡΠ΅Π³ΠΎ ΡΠΈΡΠ»Π° ΠΌΠ°Π»Π΅Π½ΡΠΊΠΈΡ
ΡΠΈΠ»ΠΎΡΠΎΠ².
ΠΠΌΠ΅ΡΡΠΈΠΌΠΎΡΡΡ ΠΎΡΠ΄Π΅Π»ΡΠ½ΡΡ
ΡΠΈΠ»ΠΎΡΠΎΠ² Π΄Π»Ρ ΡΠ΅ΠΌΠ΅Π½ΡΠ° Π΄ΠΎΡΡΠΈΠ³Π°Π΅Ρ ΠΈ 1000 ΠΈ 2000 ΠΈ Π΄Π°ΠΆΠ΅ 30000 ΡΠΎΠ½Π½, ΠΏΡΠΈ ΡΡΠΎΠΌ ΠΈΡ
Π΄ΠΈΠ°ΠΌΠ΅ΡΡ Π΄ΠΎΡΡΠΈΠ³Π°Π΅Ρ 28 ΠΌ, Π° Π²ΡΡΠΎΡΠ° Π΄ΠΎΡ
ΠΎΠ΄ΠΈΡ Π΄ΠΎ 55 ΠΌ. ΠΠ°ΡΡΠ° ΡΠ΅ΠΌΠ΅Π½ΡΠ°, Π½Π°Ρ
ΠΎΠ΄ΡΡΠ΅Π³ΠΎΡΡ Π² ΡΠΈΠ»ΠΎΡΠ΅, Π·Π°Π²ΠΈΡΠΈΡ ΠΎΡ ΡΡΠ΅ΠΏΠ΅Π½ΠΈ Π΅Π³ΠΎ ΡΠΏΠ»ΠΎΡΠ½Π΅Π½ΠΈΡ ΠΈ Π²ΠΈΠ΄Π° ΡΠ΅ΠΌΠ΅Π½ΡΠ°. Π ΡΠΏΠ»ΠΎΡΠ½Π΅Π½Π½ΠΎΠΌ ΡΠΎΡΡΠΎΒΡΠ½ΠΈΠΈ ΠΏΠ»ΠΎΡΠ½ΠΎΡΡΡ ΡΠΈΠ»ΠΎΡΠ° Π΄ΠΎΡΡΠΈΠ³Π°Π΅Ρ 1,3 Π΄ΠΎ 1,5 Ρ/ΠΌ3. ΠΠ»Ρ ΡΠ°ΡΡΠ΅ΡΠ° ΡΠΈΠ»ΠΎΡΠ½ΡΡ
ΠΊΠΎΠ½ΡΡΡΡΠΊΡΠΈΠΉ ΠΏΠ»ΠΎΡΠ½ΠΎΡΡΡ ΠΏΡΠΈΠ½ΠΈΠΌΠ°Π΅ΡΡΡ ΡΠ°Π²Π½ΠΎΠΉ 1,6 Ρ/ΠΌ3, Π° ΠΏΡΠΈ ΠΎΠΏΡΠ΅Π΄Π΅Π»Π΅Π½ΠΈΠΈ ΠΎΠ±ΡΠ΅ΠΌΠ° ΡΠΈΠ»ΠΎΡΠΎΠ² β 1,4 Ρ/ΠΌ3.
ΠΠ°ΠΊ ΠΏΡΠ°Π²ΠΈΠ»ΠΎ, Π½Π° ΡΠ΅ΠΌΠ΅Π½ΡΠ½ΡΡ
Π·Π°Π²ΠΎΠ΄Π°Ρ
Π ΠΎΡΡΠΈΠΈ ΠΈΡΠΏΠΎΠ»ΡΠ·ΡΡΡ ΡΠΈΒΠ»ΠΎΡΡ Π΄ΠΈΠ°ΠΌΠ΅ΡΡΠΎΠΌ 12 ΠΈ 18 ΠΌΠ΅ΡΡΠΎΠ². ΠΠΎΡΠΌΠ°ΠΌΠΈ ΡΠ΅Ρ
Π½ΠΎΠ»ΠΎΠ³ΠΈΡΠ΅ΡΠΊΠΎΠ³ΠΎ ΠΏΡΠΎΠ΅ΠΊΡΠΈΡΠΎΠ²Π°Π½ΠΈΡ ΠΏΡΠ΅Π΄ΡΡΠΌΠ°ΡΡΠΈΠ²Π°Π΅ΡΡΡ ΠΎΠ±ΡΠ΅ΠΌ Π·Π°ΠΏΠ°ΡΠ° Ρ
ΡΠ°Π½ΠΈΠΌΠΎΠ³ΠΎ ΡΠ΅ΒΠΌΠ΅Π½ΡΠ° ΠΎΡ 10 Π΄ΠΎ 20 ΡΡΡΠΎΠΊ, Π² Π·Π°Π²ΠΈΡΠΈΠΌΠΎΡΡΠΈ ΠΎΡ ΠΎΠ±ΡΠ΅Π³ΠΎ ΠΎΠ±ΡΠ΅ΠΌΠ° Π²ΡΠΏΡΡΠΊΠ° ΡΠ΅ΠΌΠ΅Π½ΡΠ°.
ΠΡΠΎΠ΅ΠΊΡΠΈΡΠΎΠ²Π°Π½ΠΈΠ΅ ΡΠΊΠ»Π°Π΄ΠΎΠ² ΡΠ΅ΠΌΠ΅Π½ΡΠ° ΠΎΡΡΡΠ΅ΡΡΠ²Π»ΡΠ΅ΡΡΡ Ρ ΡΡΠ΅ΡΠΎΠΌ ΡΠΎΠ³ΠΎ, ΡΡΠΎ ΡΠΈΠ»ΠΎΡΡ Π΄ΠΈΠ°ΠΌΠ΅ΡΒΡΠΎΠΌ 12 ΠΌ ΠΈ ΠΌΠ΅Π½Π΅Π΅ ΡΠ°ΡΠΏΠΎΠ»Π°Π³Π°ΡΡΡΡ Π² Π΄Π²Π° ΡΡΠ΄Π°, Π° Π΄ΠΈΠ°ΠΌΠ΅ΡΡΠΎΠΌ Π±ΠΎΠ»Π΅Π΅ 12ΠΌ β Π² ΠΎΠ΄ΠΈΠ½ ΡΡΠ΄. ΠΠ°Π΄ ΡΠΈΠ»ΠΎΡΠ°ΠΌΠΈ ΠΏΡΠ΅Π΄ΡΡΠΌΠ°ΡΡΠΈΠ²Π°Π΅ΡΡΡ Π³Π°Π»Π΅ΡΠ΅Ρ, Π² ΠΊΠΎΡΠΎΡΠΎΠΉ ΡΠ°Π·ΠΌΠ΅ΡΠ°ΡΡΡΡ ΡΡΡΠ±ΠΎΠΏΡΠΎΠ²ΠΎΠ΄Ρ, ΡΠΈΠ»ΡΡΡΡ, ΠΏΠ΅ΡΠ΅ΠΊΠ»ΡΡΠ°ΡΠ΅Π»ΠΈ ΠΈ Ρ.Π΄.
Π‘ΠΈΠ»ΠΎΡΠ½ΡΠ΅ Π΅ΠΌΠΊΠΎΡΡΠΈ ΡΡΡΠ°Π½Π°Π²Π»ΠΈΠ²Π°ΡΡΡΡ Π½Π° ΠΌΠ΅ΡΠ°Π»Π»ΠΈΡΠ΅ΡΠΊΠΈΡ
ΠΎΠΏΠΎΡΠ°Ρ
(ΠΊΠΎΠ»ΠΎΠ½Π½Π°Ρ
) ΡΠ°ΠΊΠΈΠΌ ΠΎΠ±ΡΠ°Π·ΠΎΠΌ, ΡΡΠΎΠ±Ρ ΠΎΠ±Π΅ΡΠΏΠ΅ΡΠΈΡΡ ΠΏΡΠΎΠΏΡΡΠΊ ΠΆΠ΅Π»Π΅Π·Π½ΠΎΠ΄ΠΎΡΠΎΠΆΠ½ΡΡ
ΡΠΎΒΡΡΠ°Π²ΠΎΠ² Π΄Π»Ρ Π·Π°Π³ΡΡΠ·ΠΊΠΈ Π²Π°Π³ΠΎΠ½ΠΎΠ² ΡΠ΅ΠΌΠ΅Π½ΡΠΎΠΌ ΠΈΠ· ΡΠΈΠ»ΠΎΡΠΎΠ² ΡΠ°ΠΌΠΎΡΠ΅ΠΊΠΎΠΌ (ΡΠ΅Π½ΡΡΠ°Π»ΡΠ½Π°Ρ ΡΠ°Π·Π³ΡΡΠ·ΠΊΠ°).
ΠΠ»Ρ Π·Π°Π³ΡΡΠ·ΠΊΠΈ ΠΆΠ΅Π»Π΅Π·Π½ΠΎΠ΄ΠΎΡΠΎΠΆΠ½ΡΡ
ΡΠΎΡΡΠ°Π²ΠΎΠ² ΠΏΠΎΠ΄ ΠΊΠ°ΠΆΠ΄ΡΠΌ ΡΡΠ΄ΠΎΠΌ ΡΠΈΠ»ΠΎΡΠΎΠ² Π΄ΠΈΠ°ΠΌΠ΅ΡΡΠΎΠΌ 12 ΠΌ, ΡΡΡΠ°Π½ΠΎΠ²Π»Π΅Π½Π½ΡΡ
Π½Π° ΠΌΠ΅ΡΠ°Π»Π»ΠΈΡΠ΅ΡΠΊΠΈΡ
ΠΎΠΏΠΎΡΠ°Ρ
, ΡΠΊΠ»Π°Π΄ΡΠ²Π°ΒΠ΅ΡΡΡ ΠΏΠΎ ΠΎΠ΄Π½ΠΎΠΌΡ ΠΆΠ΅Π»Π΅Π·Π½ΠΎΠ΄ΠΎΡΠΎΠΆΠ½ΠΎΠΌΡ ΠΏΡΡΠΈ ΠΈ ΠΏΠΎΠ΄ ΠΊΠ°ΠΆΠ΄ΡΠΌ ΡΠΈΠ»ΠΎΡΠΎΠΌ ΠΏΡΠ΅Π΄ΡΡΠΌΠ°ΡΡΠΈΠ²Π°Π΅ΡΡΡ ΡΡΡΠ°Π½ΠΎΠ²ΠΊΠ° ΠΎΠ΄Π½ΠΈΡ
ΠΆΠ΅Π»Π΅Π·Π½ΠΎΠ΄ΠΎΡΠΎΠΆΠ½ΡΡ
Π²Π΅ΡΠΎΠ² Π³ΡΡΒΠ·ΠΎΠΏΠΎΠ΄ΡΠ΅ΠΌΠ½ΠΎΡΡΡΡ 150 ΡΠΎΠ½Π½. ΠΠΎΠ΄ ΡΠΈΠ»ΠΎΡΠ°ΠΌΠΈ Π΄ΠΈΠ°ΠΌΠ΅ΡΡΠΎΠΌ 18 ΠΌ ΠΏΡΠ΅Π΄ΡΡΠΌΠ°ΡΡΠΈΠ²Π°ΡΡΡΡ Π΄Π²Π° ΠΆΠ΅Π»Π΅Π·Π½ΠΎΠ΄ΠΎΡΠΎΠΆΠ½ΡΡ
ΠΏΡΡΠΈ ΠΈ Π΄Π²ΠΎΠ΅ ΠΆΠ΅Π»Π΅Π·Π½ΠΎΠ΄ΠΎΡΠΎΠΆΠ½ΡΡ
Π²Π΅ΡΠΎΠ² Π³ΡΡΠ·ΠΎΠΏΠΎΠ΄ΡΠ΅ΠΌΠ½ΠΎΡΡΡΡ 150 ΡΠΎΠ½Π½ ΠΏΠΎΠ΄ ΠΊΠ°ΠΆΠ΄ΡΠΌ ΡΠΈΠ»ΠΎΡΠΎΠΌ. Π‘ΠΈΠ»ΠΎΡΡ Π΄ΠΈΠ°ΠΌΠ΅ΡΡΠΎΠΌ 12 ΠΌ ΡΡΡΠ°Π½Π°Π²Π»ΠΈΠ²Π°ΡΡΡΡ Π±Π»ΠΎΠΊΠ°ΠΌΠΈ ΠΏΠΎ 4 ΡΠΈΠ»ΠΎΡΠ° Π² ΠΊΠ°ΠΆΠ΄ΠΎΠΌ Π±Π»ΠΎΠΊΠ΅, Π° ΡΠΈΠ»ΠΎΡΡ Π΄ΠΈΠ°ΠΌΠ΅ΡΡΠΎΠΌ 18ΠΌ β Π² ΠΎΠ΄ΠΈΠ½ ΡΡΠ΄ Ρ ΡΠ°ΡΡΡΠΎΡΠ½ΠΈΠ΅ΠΌ ΠΌΠ΅ΠΆΠ΄Ρ ΠΎΡΡΠΌΠΈ 24 ΠΌ.
Π¦Π΅ΠΌΠ΅Π½Ρ ΠΌΠΎΠΆΠ½ΠΎ ΠΎΡΠ³ΡΡΠΆΠ°ΡΡ Π½Π°Π²Π°Π»ΠΎΠΌ Π² ΠΆΠ΅Π»Π΅Π·Π½ΠΎΠ΄ΠΎΡΠΎΠΆΠ½ΡΠ΅ Π²Π°Π³ΠΎΒΠ½Ρ, Π² ΠΆΠ΅Π»Π΅Π·Π½ΠΎΠ΄ΠΎΡΠΎΠΆΠ½ΡΠ΅ ΡΠΈΡΡΠ΅ΡΠ½Ρ β ΡΠ΅ΠΌΠ΅Π½ΡΠΎΠ²ΠΎΠ·Ρ, Π² Π°Π²ΡΠΎΡΠ΅ΠΌΠ΅Π½ΒΡΠΎΠ²ΠΎΠ·Ρ, Π° ΡΠ°ΠΊΠΆΠ΅ Π² Π·Π°ΡΠ°ΡΠ΅Π½Π½ΠΎΠΌ Π²ΠΈΠ΄Π΅ β Π² ΠΌΠ΅ΡΠΊΠ°Ρ
Π²Π΅ΡΠΎΠΌ 50 ΠΊΠ³.
ΠΡΠ³ΡΡΠ·ΠΊΠ° ΡΠ΅ΠΌΠ΅Π½ΡΠ° ΠΌΠΎΠΆΠ΅Ρ ΠΎΡΡΡΠ΅ΡΡΠ²Π»ΡΡΡΡΡ ΡΠ°ΠΊΠΆΠ΅ ΡΠ΅ΡΠ½ΡΠΌ ΠΈΠ»ΠΈ ΠΌΠΎΡΒΡΠΊΠΈΠΌ ΡΡΠ°Π½ΡΠΏΠΎΡΡΠΎΠΌ ΠΊΠ°ΠΊ Π½Π°Π²Π°Π»ΠΎΠΌ, ΡΠ°ΠΊ ΠΈ Π² Π·Π°ΡΠ°ΡΠ΅Π½Π½ΠΎΠΌ Π²ΠΈΠ΄Π΅ β Π² ΠΌΠ΅ΡΠΊΠ°Ρ
ΠΈΠ»ΠΈ Π² Π±ΠΎΠ»ΡΡΠ΅Π³ΡΡΠ·Π½ΡΡ
ΠΊΠΎΠ½ΡΠ΅ΠΉΠ½Π΅ΡΠ°Ρ
ΠΈΠ· ΠΏΠΎΠ»ΠΈΠΌΠ΅ΡΠ½ΡΡ
ΠΌΠ°ΒΡΠ΅ΡΠΈΠ°Π»ΠΎΠ². ΠΠ°ΡΠ°ΡΠΈΠ²Π°Π½ΠΈΠ΅ ΡΠ΅ΠΌΠ΅Π½ΡΠ° ΠΏΡΠΎΠΈΠ·Π²ΠΎΠ΄ΠΈΡΡΡ Π² ΡΠΏΠ΅ΡΠΈΠ°Π»ΡΠ½ΡΡ
ΡΠΏΠ°ΒΠΊΠΎΠ²ΠΎΡΠ½ΡΡ
ΠΎΡΠ΄Π΅Π»Π΅Π½ΠΈΡΡ
, ΠΎΡΠ½Π°ΡΠ΅Π½Π½ΡΡ
Π²ΡΡΠΎΠΊΠΎΠΏΡΠΎΠΈΠ·Π²ΠΎΠ΄ΠΈΡΠ΅Π»ΡΠ½ΡΠΌΠΈ ΡΠΏΠ°ΠΊΠΎΠ²ΠΎΡΠ½ΡΠΌΠΈ ΠΌΠ°ΡΠΈΠ½Π°ΠΌΠΈ.
Π ΠΏΡΠΎΡΠ΅ΡΡΠ΅ ΡΠ°ΡΠΈΡΠΎΠ²Π°Π½ΠΈΡ ΡΠ΅ΠΌΠ΅Π½ΡΠ° Π²ΡΠ΄Π΅Π»ΡΠ΅ΡΡΡ Π·Π½Π°ΡΠΈΡΠ΅Π»ΡΠ½ΠΎΠ΅ ΠΊΠΎΒΠ»ΠΈΡΠ΅ΡΡΠ²ΠΎ ΠΏΡΠ»ΠΈ, ΠΏΠΎΡΡΠΎΠΌΡ ΡΠΏΠ°ΠΊΠΎΠ²ΠΎΡΠ½Π°Ρ ΠΌΠ°ΡΠΈΠ½Π° ΠΎΠ±ΠΎΡΡΠ΄ΠΎΠ²Π°Π½Π° Π°ΡΠΏΠΈΡΠ°ΡΠΈΠΎΠ½Π½ΠΎΠΉ ΡΡΡΠ°Π½ΠΎΠ²ΠΊΠΎΠΉ, ΡΠΎΡΡΠΎΡΡΠ΅ΠΉ ΠΈΠ· ΡΡΠΊΠ°Π²Π½ΠΎΠ³ΠΎ ΡΠΈΠ»ΡΡΡΠ° ΠΈ Π²ΡΡΡΠΆΠ½ΠΎΠ³ΠΎ Π²Π΅Π½ΡΠΈΠ»ΡΡΠΎΡΠ°. ΠΠΎΡΡΡΠΏΠ°ΡΡΠΈΠΉ ΠΈΠ· ΡΠΈΠ»ΠΎΡΠΎΠ² ΡΠ΅ΠΌΠ΅Π½Ρ ΠΏΡΠ΅Π΄Π²Π°ΒΡΠΈΡΠ΅Π»ΡΠ½ΠΎ ΠΏΡΠΎΠΏΡΡΠΊΠ°Π΅ΡΡΡ ΡΠ΅ΡΠ΅Π· ΠΏΡΠΎΡΠ΅ΠΈΠ²Π°ΡΡΠΈΠΉ ΡΠ½Π΅ΠΊ (Π΄Π»Ρ Π²ΡΠ΄Π΅Π»Π΅Π½ΠΈΡ ΡΠ»ΡΡΠ°ΠΉΠ½ΠΎ ΠΏΠΎΠΏΠ°Π²ΡΠΈΡ
Π² Π½Π΅Π³ΠΎ ΠΎΡΡΠ°ΡΠΊΠΎΠ² ΠΌΠ΅Π»ΡΡΠΈΡ
ΡΠ΅Π» ΠΈ ΠΊΡΡΠΏΠ½ΡΡ
ΡΠ°ΡΡΠΈΡ ΠΌΠ°ΡΠ΅ΡΠΈΠ°Π»Π°), ΠΏΠΎΡΠ»Π΅ ΡΠ΅Π³ΠΎ ΠΏΠΎΠ΄Π°Π΅ΡΡΡ Π² ΡΠΏΠ°ΠΊΠΎΠ²ΠΎΡΠ½ΡΡ ΠΌΠ°ΡΠΈΠ½Ρ. ΠΡΠ»ΠΈ ΠΊΠΎΠ»ΠΈΡΠ΅ΡΡΠ²ΠΎ ΠΏΠΎΠ΄Π°Π²Π°Π΅ΠΌΠΎΠ³ΠΎ ΡΠ΅ΠΌΠ΅Π½ΡΠ° ΠΏΡΠ΅Π²ΡΡΠ°Π΅Ρ ΠΏΡΠΎΠΏΡΡΠΊΠ½ΡΡ ΡΠΏΠΎΡΠΎΠ±Π½ΠΎΡΡΡ ΡΠΏΠ°ΠΊΠΎΠ²ΠΎΡΠ½ΠΎΠΉ ΠΌΠ°ΡΠΈΠ½Ρ, ΡΠΎ ΠΈΠ·Π±ΡΡΠΎΠΊ Π΅Π³ΠΎ ΡΠ»ΠΈΠ²Π°Π΅ΡΡΡ Π² Π±ΡΠ½ΠΊΠ΅Ρ, ΠΈΠ· ΠΊΠΎΡΠΎΡΠΎΠ³ΠΎ ΡΠ΅ΠΌΠ΅Π½Ρ Π²Π½ΠΎΠ²Ρ ΠΏΠΎΡΡΡΠΏΠ°Π΅Ρ Π² ΠΏΡΠΎΡΠ΅ΡΡ.
ΠΡΠΈ ΡΠΏΠ°ΠΊΠΎΠ²ΠΎΡΠ½ΠΎΠΌ ΠΎΡΠ΄Π΅Π»Π΅Π½ΠΈΠΈ ΠΈΠΌΠ΅Π΅ΡΡΡ ΡΠΊΠ»Π°Π΄ Π±ΡΠΌΠ°ΠΆΠ½ΡΡ
ΠΌΠ΅ΡΠΊΠΎΠ², ΡΠ°ΡΠΏΠΎΠ»Π°Π³Π°Π΅ΠΌΡΠΉ Π² Π½Π΅ΠΏΠΎΡΡΠ΅Π΄ΡΡΠ²Π΅Π½Π½ΠΎΠΉ Π±Π»ΠΈΠ·ΠΎΡΡΠΈ ΠΎΡ ΡΠΏΠ°ΠΊΠΎΠ²ΠΎΡΠ½ΠΎΠΉ ΠΌΠ°ΒΡΠΈΠ½Ρ. Π‘ΠΊΠ»Π°Π΄Ρ ΠΎΡΠ½Π°ΡΠ°ΡΡΡΡ ΠΌΠ΅Ρ
Π°Π½ΠΈΠ·ΠΈΡΠΎΠ²Π°Π½Π½ΡΠΌΠΈ ΡΠ΅Π»ΡΡΠ΅ΡΠ°ΠΌΠΈ ΠΈΠ»ΠΈ Π°Π²ΡΠΎΠΏΠΎΠ³ΡΡΠ·ΡΠΈΠΊΠ°ΠΌΠΈ Π΄Π»Ρ ΠΏΠΎΠ΄Π°ΡΠΈ ΠΏΡΡΡΡΡ
ΠΌΠ΅ΡΠΊΠΎΠ² Π² ΠΊΠΈΠΏΠ°Ρ
ΠΊ ΡΠΏΠ°ΠΊΠΎΒΠ²ΠΎΡΠ½ΡΠΌ ΠΌΠ°ΡΠΈΠ½Π°ΠΌ.
ΠΠ»ΠΎΡΠ°Π΄Ρ ΡΠΊΠ»Π°Π΄Π° Π΄Π»Ρ Ρ
ΡΠ°Π½Π΅Π½ΠΈΡ ΡΠ°ΡΠΈΡΠΎΠ²Π°Π½Π½ΠΎΠ³ΠΎ ΡΠ΅ΠΌΠ΅Π½ΡΠ° ΡΠ°ΡΡΡΠΈΒΡΡΠ²Π°Π΅ΡΡΡ ΠΈΠ· ΡΠΎΠ³ΠΎ, ΡΡΠΎ Π½Π° 1 ΠΌ2 ΠΏΠΎΠ»Π΅Π·Π½ΠΎΠΉ ΠΏΠ»ΠΎΡΠ°Π΄ΠΈ ΠΌΠΎΠΆΠ½ΠΎ ΡΠ»ΠΎΠΆΠΈΡΡ 3 Ρ ΡΠ΅ΠΌΠ΅Π½ΡΠ° Π² Π±ΡΠΌΠ°ΠΆΠ½ΡΡ
ΠΌΠ΅ΡΠΊΠ°Ρ
. ΠΠ»Ρ ΠΏΡΠΎΠ΅Π·Π΄ΠΎΠ² ΠΈ ΠΏΡΠΎΡ
ΠΎΠ΄ΠΎΠ² ΠΏΡΠ΅ΒΠ΄ΡΡΠΌΠ°ΡΡΠΈΠ²Π°Π΅ΡΡΡ Π΄ΠΎΠΏΠΎΠ»Π½ΠΈΡΠ΅Π»ΡΠ½Π°Ρ ΠΏΠ»ΠΎΡΠ°Π΄Ρ Π² ΡΠ°Π·ΠΌΠ΅ΡΠ΅ ΠΎΠΊΠΎΠ»ΠΎ 30β 35% ΠΎΡ ΠΏΠΎΠ»Π΅Π·Π½ΠΎΠΉ ΠΏΠ»ΠΎΡΠ°Π΄ΠΈ ΡΠΊΠ»Π°Π΄Π°.
ΠΠ΅Ρ
Π°Π½ΠΈΠ·ΠΈΡΠΎΠ²Π°Π½Π½Π°Ρ ΠΏΠΎΠ³ΡΡΠ·ΠΊΠ° ΡΠ΅ΠΌΠ΅Π½ΡΠ½ΡΡ
ΠΌΠ΅ΡΠΊΠΎΠ² Π² ΠΆΠ΅Π»Π΅Π·Π½ΠΎΠ΄ΠΎΒΡΠΎΠΆΠ½ΡΠ΅ Π²Π°Π³ΠΎΠ½Ρ ΠΎΡΡΡΠ΅ΡΡΠ²Π»ΡΠ΅ΡΡΡ ΡΠΏΠ΅ΡΠΈΠ°Π»ΡΠ½ΡΠΌΠΈ ΠΏΠΎΠ³ΡΡΠ·ΠΎΡΠ½ΡΠΌΠΈ ΠΌΠ°ΒΡΠΈΠ½Π°ΠΌΠΈ, ΡΠΎΡΡΠΎΡΡΠΈΠΌΠΈ ΠΈΠ· Π½Π΅ΡΠΊΠΎΠ»ΡΠΊΠΈΡ
ΠΏΠΎΠ΄Π²ΠΈΠΆΠ½ΠΎ ΡΠΎΠ΅Π΄ΠΈΠ½Π΅Π½Π½ΡΡ
ΠΌΠ΅ΠΆΠ΄Ρ ΡΠΎΠ±ΠΎΠΉ ΠΏΠ΅ΡΠ΅Π΄Π°ΡΠΎΡΠ½ΡΡ
ΡΡΠ°Π½ΡΠΏΠΎΡΡΠ΅ΡΠΎΠ² ΠΈ ΡΡΠ°Π½ΡΠΏΠΎΡΡΠ΅ΡΠ°-ΡΡΠ°Π±Π΅Π»Π΅ΡΠΊΒΠ»Π°Π΄ΡΠΈΠΊΠ°. Π’Π°ΠΊΠ°Ρ ΠΌΠ°ΡΠΈΠ½Π° Π²Π΄Π²ΠΈΠ³Π°Π΅ΡΡΡ Π² ΠΊΡΡΡΡΠΉ Π²Π°Π³ΠΎΠ½ ΠΈ ΠΎΠ±Π΅ΡΠΏΠ΅ΡΠΈΒΠ²Π°Π΅Ρ Π΅Π³ΠΎ ΡΠ°Π²Π½ΠΎΠΌΠ΅ΡΠ½ΠΎΠ΅ ΠΏΠ»ΠΎΡΠ½ΠΎΠ΅ Π·Π°ΠΏΠΎΠ»Π½Π΅Π½ΠΈΠ΅ ΠΌΠ΅ΡΠΊΠ°ΠΌΠΈ Ρ ΡΠ΅ΠΌΠ΅Π½ΡΠΎΠΌ. ΠΠ΅ΡΠ΅Π΄Π½ΡΡ ΡΠ°ΡΡΡ ΡΠ°ΠΊΠΎΠΉ ΠΏΠΎΠ³ΡΡΠ·ΠΎΡΠ½ΠΎΠΉ ΠΌΠ°ΡΠΈΠ½Ρ ΠΌΠΎΠΆΠ΅Ρ ΠΏΠ΅ΡΠ΅ΠΌΠ΅ΡΠ°ΡΡΡΡ Π² ΡΡΠ΅Ρ
ΠΈΠ·ΠΌΠ΅ΡΠ΅Π½ΠΈΡΡ
, Ρ. Π΅. ΠΏΠΎΠ²ΠΎΡΠ°ΡΠΈΠ²Π°ΡΡΡΡ, ΠΏΠΎΠ΄Π½ΠΈΠΌΠ°ΡΡΡΡ ΠΈ ΠΎΠΏΡΡΠΊΠ°ΡΡΒΡΡ, Π° ΡΠ°ΠΊΠΆΠ΅ Π²ΡΠ΄Π²ΠΈΠ³Π°ΡΡΡΡ.
ΠΡΠ½ΠΊΠ΅ΡΡ ΡΡΠΏΡΡΠΈΡ ΠΌΠ°ΡΠ΅ΡΠΈΠ°Π»ΠΎΠ². ΠΡΠ½ΠΊΠ΅ΡΡ Π΄Π»Ρ ΡΠ΅ΠΌΠ΅Π½ΡΠ°. ΠΠ±ΡΠ΅ΠΌΡ Π±ΡΠ½ΠΊΠ΅ΡΠ½ΡΡ ΠΊΠΎΠ½ΡΡΡΡΠΊΡΠΈΠΉ: 5, 10, 15, 20, 25, 30, 35, 40, 45, 50, 60, 70, 80, 90, 100, 130, 150, 200, 250, 300, 350, 400, 500, 1000 ΡΠΎΠ½Π½ ΠΈ Π±ΠΎΠ»Π΅Π΅.
ΠΡΠΈ ΠΏΡΠΎΠ΅ΠΊΡΠΈΡΠΎΠ²Π°Π½ΠΈΠΈ ΠΎΡΠΊΡΡΡΡΡ
ΡΠΈΠ»ΠΎΡΠΎΠ² Π΄Π»Ρ Ρ
ΡΠ°Π½Π΅Π½ΠΈΡ ΡΡΠΏΡΡΠΈΡ
ΠΈ ΡΡΡΡΠ½ΡΡ
ΠΌΠ°ΡΠ΅ΡΠΈΠ°Π»ΠΎΠ² Π΄ΠΎΠΏΡΡΠΊΠ°Π΅ΡΡΡ ΠΈΡ
ΡΠ°ΡΠΏΠΎΠ»Π°Π³Π°ΡΡ Π² Π·Π΄Π°Π½ΠΈΡΡ
ΠΈ Π½Π° ΠΎΡΠΊΡΡΡΡΡ
ΠΏΠ»ΠΎΡΠ°Π΄ΠΊΠ°Ρ
Π·Π°Π³Π»ΡΠ±Π»Π΅Π½Π½ΡΠΌΠΈ ΠΈΠ»ΠΈ Π½Π°Π·Π΅ΠΌΠ½ΡΠΌΠΈ, ΠΊΠ°ΠΊ ΠΏΡΠ°Π²ΠΈΠ»ΠΎ, ΡΠ±Π»ΠΎΠΊΠΈΡΠΎΠ²Π°Π½Π½ΡΠΌΠΈ, ΠΌΠ½ΠΎΠ³ΠΎΡΡΠ΅ΠΉΠΊΠΎΠ²ΡΠΌΠΈ.
ΠΠ΅ΡΠ΅ΡΠ΅Π½Ρ ΠΌΠ°ΡΠ΅ΡΠΈΠ°Π»ΠΎΠ² Ρ
ΡΠ°Π½ΠΈΠΌΡΡ
Π² ΡΠΈΠ»ΠΎΡΠ°Ρ
: ΡΠ»Π°ΠΊ ΠΏΠ΅ΡΠ΅Π΄Π΅Π»ΡΠ½ΡΠΉ, ΠΊΠ²Π°ΡΡΠΈΡ, Π¨Π°ΠΌΠΎΡ, ΠΡΠ½ΠΈΡ, Π₯ΡΠΎΠΌΠΈΡ, Π¨Π»Π°ΠΊ, ΠΠ΅ΡΠΎΠΊ ΡΡΡΠΎΠΉ, ΠΠ·Π²Π΅ΡΡΠ½ΡΠΊ, ΠΠ»ΠΈΠ½Π°, ΠΠ·Π²Π΅ΡΡΡ, ΠΠ°Π³Π½Π΅Π·ΠΈΡΠΎΠ²ΡΠΉ ΠΏΠΎΡΠΎΡΠΎΠΊ, ΠΠ΅ΡΠΎΠΊ ΡΡΡ
ΠΎΠΉ, ΠΠΎΠΊΡ ΠΈ ΠΊΠΎΠΊΡΠΈΠΊ.
ΠΡΠ½ΠΊΠ΅ΡΡ ΠΌΠ΅ΡΠ°Π»Π»ΠΈΡΠ΅ΡΠΊΠΈΠ΅. ΠΡΠΈ ΠΏΡΠΎΠ΅ΠΊΡΠΈΡΠΎΠ²Π°Π½ΠΈΠΈ Π½Π°ΡΡΠΆΠ½ΡΡ
Π±ΡΠ½ΠΊΠ΅ΡΠΎΠ² ΠΈ Π±ΡΠ½ΠΊΠ΅ΡΠΎΠ², ΡΠ°ΡΠΏΠΎΠ»Π°Π³Π°Π΅ΠΌΡΡ
Π²Π½ΡΡΡΠΈ Π·Π΄Π°Π½ΠΈΠΉ ΠΈ ΡΠΎΠΎΡΡΠΆΠ΅Π½ΠΈΠΉ Π΄ΠΎΠ»ΠΆΠ½ΠΎ Π²ΠΊΠ»ΡΡΠ°ΡΡ Π΄Π²Π° ΠΏΠΎΡΠ»Π΅Π΄ΠΎΠ²Π°ΡΠ΅Π»ΡΠ½ΡΡ
ΡΡΠ°ΠΏΠ°:
1) ΠΎΠΏΡΠ΅Π΄Π΅Π»Π΅Π½ΠΈΠ΅ Π³Π΅ΠΎΠΌΠ΅ΡΡΠΈΡΠ΅ΡΠΊΠΈΡ
ΠΏΠ°ΡΠ°ΠΌΠ΅ΡΡΠΎΠ² β ΡΠΎΡΠΌΡ Π±ΡΠ½ΠΊΠ΅ΡΠ° ΠΈ Π΅Π³ΠΎ Π²ΠΎΡΠΎΠ½ΠΊΠΈ, ΡΠ³Π»ΠΎΠ² Π½Π°ΠΊΠ»ΠΎΠ½Π° ΡΡΠ΅Π½ΠΎΠΊ, ΡΠ°Π·ΠΌΠ΅ΡΠΎΠ² Π²ΡΠΏΡΡΠΊΠ½ΠΎΠ³ΠΎ ΠΎΡΠ²Π΅ΡΡΡΠΈΡ, ΠΊΠΎΡΠΎΡΡΠ΅ ΠΎΠΏΡΠ΅Π΄Π΅Π»ΡΡΡΡΡ ΡΠ°ΡΡΠ΅ΡΠΎΠΌ Π½Π° ΠΎΡΠ½ΠΎΠ²Π°Π½ΠΈΠΈ ΡΠΈΠ·ΠΈΠΊΠΎ-ΠΌΠ΅Ρ
Π°Π½ΠΈΡΠ΅ΡΠΊΠΈΡ
Ρ
Π°ΡΠ°ΠΊΡΠ΅ΡΠΈΡΡΠΈΠΊ ΡΡΠΏΡΡΠ΅Π³ΠΎ ΠΌΠ°ΡΠ΅ΡΠΈΠ°Π»Π° Ρ ΡΡΠ΅ΡΠΎΠΌ Π½Π΅Π±Π»Π°Π³ΠΎΠΏΡΠΈΡΡΠ½ΡΡ
ΠΈΡ
ΠΈΠ·ΠΌΠ΅Π½Π΅Π½ΠΈΠΉ, ΠΏΡΠΈ ΡΡΠΎΠΌ Π΄ΠΎΠ»ΠΆΠ½Ρ ΠΈΡΠΊΠ»ΡΡΠ°ΡΡΡΡ ΡΠ²ΠΎΠ΄ΠΎΠΎΠ±ΡΠ°Π·ΠΎΠ²Π°Π½ΠΈΠ΅ Π½Π°Π΄ Π²ΡΠΏΡΡΠΊΠ½ΡΠΌ ΠΎΡΠ²Π΅ΡΡΡΠΈΠ΅ΠΌ ΠΈ Π·Π°Π²ΠΈΡΠ°Π½ΠΈΠ΅ Π½Π° ΡΡΠ΅Π½ΠΊΠ°Ρ
;
2) ΡΠ°ΡΡΠ΅Ρ ΠΈ ΠΏΡΠΎΠ΅ΠΊΡΠΈΡΠΎΠ²Π°Π½ΠΈΠ΅ ΠΊΠΎΠ½ΡΡΡΡΠΊΡΠΈΠΉ Π±ΡΠ½ΠΊΠ΅ΡΠΎΠ² ΠΈ ΠΈΡ
Π·Π°ΡΠΈΡΡ ΠΎΡ ΡΠ΄Π°ΡΠΎΠ² ΠΈ ΠΈΡΡΠΈΡΠ°Π½ΠΈΡ.
ΠΠΏΡΠ΅Π΄Π΅Π»Π΅Π½ΠΈΠ΅ Π³Π΅ΠΎΠΌΠ΅ΡΡΠΈΡΠ΅ΡΠΊΠΈΡ
ΠΏΠ°ΡΠ°ΠΌΠ΅ΡΡΠΎΠ² Π±ΡΠ½ΠΊΠ΅ΡΠΎΠ² ΡΠ°Π·Π»ΠΈΡΠ°Π΅ΡΡΡ Π΄Π»Ρ ΡΠ²ΡΠ·Π½ΡΡ
(ΠΈΠΌΠ΅ΡΡΠΈΡ
ΡΡΠ΅ΠΏΠ»Π΅Π½ΠΈΠ΅, ΡΠ»Π΅ΠΆΠΈΠ²Π°ΡΡΠΈΡ
ΡΡ) ΠΈ Π½Π΅ΡΠ²ΡΠ·Π½ΡΡ
(Π½Π΅ ΠΈΠΌΠ΅ΡΡΠΈΡ
ΡΡΠ΅ΠΏΠ»Π΅Π½ΠΈΡ, Π½Π΅ΡΠ»Π΅ΠΆΠΈΠ²Π°ΡΡΠΈΡ
ΡΡ) ΡΡΠΏΡΡΠΈΡ
ΠΌΠ°ΡΠ΅ΡΠΈΠ°Π»ΠΎΠ². Π ΡΠ²ΡΠ·Π½ΡΠΌ ΠΎΡΠ½ΠΎΡΡΡΡΡ, ΠΊΠ°ΠΊ ΠΏΡΠ°Π²ΠΈΠ»ΠΎ, ΠΌΠ°ΡΠ΅ΡΠΈΠ°Π»Ρ, ΡΠΎΠ΄Π΅ΡΠΆΠ°ΡΠΈΠ΅ ΡΡΠ°ΠΊΡΠΈΠΈ ΠΌΠ΅Π½Π΅Π΅ 2 ΠΌΠΌ ΠΈ ΠΈΠΌΠ΅ΡΡΠΈΠ΅ Π²Π»Π°ΠΆΠ½ΠΎΡΡΡ Π±ΠΎΠ»Π΅Π΅ 2 %, Π° ΠΊ Π½Π΅ΡΠ²ΡΠ·Π½ΡΠΌ β ΡΠ΅Π±Π΅Π½Ρ, Π³Π°Π»ΡΠΊΠ° ΠΈ Π΄ΡΡΠ³ΠΈΠ΅ ΠΌΠ°ΡΠ΅ΡΠΈΠ°Π»Ρ Ρ ΠΊΡΡΠΏΠ½ΠΎΡΡΡΡ Π·Π΅ΡΠ΅Π½ 2 ΠΌΠΌ ΠΈ Π±ΠΎΠ»Π΅Π΅, Π° ΡΠ°ΠΊΠΆΠ΅ ΠΏΠ΅ΡΠΎΠΊ Ρ ΠΊΡΡΠΏΠ½ΠΎΡΡΡΡ Π·Π΅ΡΠ΅Π½ Π΄ΠΎ 2 ΠΌΠΌ ΠΈ Π²Π»Π°ΠΆΠ½ΠΎΡΡΡΡ Π΄ΠΎ 2 %.
ΠΡΠΈ ΠΏΡΠΎΠ΅ΠΊΡΠΈΡΠΎΠ²Π°Π½ΠΈΠΈ Π±ΡΠ½ΠΊΠ΅ΡΠΎΠ² Π½Π΅ΠΎΠ±Ρ
ΠΎΠ΄ΠΈΠΌΠΎ ΠΏΡΠΈΠ½ΠΈΠΌΠ°ΡΡ Π²ΠΎ Π²Π½ΠΈΠΌΠ°Π½ΠΈΠ΅, ΡΡΠΎ ΠΈΠΌΠ΅ΡΡΡΡ Π΄Π²Π΅ Π²ΠΎΠ·ΠΌΠΎΠΆΠ½ΡΠ΅ ΡΠΎΡΠΌΡ ΠΈΡΡΠ΅ΡΠ΅Π½ΠΈΡ ΡΡΠΏΡΡΠ΅Π³ΠΎ ΠΌΠ°ΡΠ΅ΡΠΈΠ°Π»Π°: Π³ΠΈΠ΄ΡΠ°Π²Π»ΠΈΡΠ΅ΡΠΊΠ°Ρ, ΠΏΡΠΈ ΠΊΠΎΡΠΎΡΠΎΠΉ Π½Π°Ρ
ΠΎΠ΄ΠΈΡΡΡ Π² Π΄Π²ΠΈΠΆΠ΅Π½ΠΈΠΈ ΡΡΠΏΡΡΠΈΠΉ ΠΌΠ°ΡΠ΅ΡΠΈΠ°Π» Π²ΠΎ Π²ΡΠ΅ΠΌ ΠΎΠ±ΡΠ΅ΠΌΠ΅ Π±ΡΠ½ΠΊΠ΅ΡΠ°, ΠΈ Π½Π΅Π³ΠΈΠ΄ΡΠ°Π²Π»ΠΈΡΠ΅ΡΠΊΠ°Ρ, ΠΏΡΠΈ ΠΊΠΎΡΠΎΡΠΎΠΉ Π΄Π²ΠΈΠΆΠ΅ΡΡΡ ΡΠΎΠ»ΡΠΊΠΎ ΡΠ΅Π½ΡΡΠ°Π»ΡΠ½Π°Ρ ΡΠ°ΡΡΡ Π½Π°Π΄ Π²ΡΠΏΡΡΠΊΠ½ΡΠΌ ΠΎΡΠ²Π΅ΡΡΡΠΈΠ΅ΠΌ, Π° ΠΎΡΡΠ°Π»ΡΠ½ΠΎΠΉ ΠΌΠ°ΡΠ΅ΡΠΈΠ°Π» Π½Π΅ΠΏΠΎΠ΄Π²ΠΈΠΆΠ΅Π½. ΠΠ»Ρ ΡΠ²ΡΠ·Π½ΡΡ
ΠΈΠ»ΠΈ ΡΠ°ΠΌΠΎΠ²ΠΎΠ·Π³ΠΎΡΠ°ΡΡΠΈΡ
ΡΡ ΡΡΠΏΡΡΠΈΡ
ΠΌΠ°ΡΠ΅ΡΠΈΠ°Π»ΠΎΠ² ΡΠ»Π΅Π΄ΡΠ΅Ρ ΠΏΡΠΎΠ΅ΠΊΡΠΈΡΠΎΠ²Π°ΡΡ Π±ΡΠ½ΠΊΠ΅ΡΠ° Ρ Π³ΠΈΠ΄ΡΠ°Π²Π»ΠΈΡΠ΅ΡΠΊΠΎΠΉ ΡΠΎΡΠΌΠΎΠΉ ΠΈΡΡΠ΅ΡΠ΅Π½ΠΈΡ, Π° Π΄Π»Ρ Π½Π΅ΡΠ²ΡΠ·Π½ΡΡ
, ΠΊΠ°ΠΊ ΠΏΡΠ°Π²ΠΈΠ»ΠΎ, Ρ Π½Π΅Π³ΠΈΠ΄ΡΠ°Π²Π»ΠΈΡΠ΅ΡΠΊΠΎΠΉ.
ΠΡΠ½ΠΊΠ΅ΡΡ ΡΡΠ°Π»ΡΠ½ΡΠ΅ Π½Π΅Π³ΠΈΠ΄ΡΠ°Π²Π»ΠΈΡΠ΅ΡΠΊΠΎΠ³ΠΎ ΠΈΡΡΠ΅ΡΠ΅Π½ΠΈΡ Π΄Π»Ρ Π½Π΅ΡΠ²ΡΠ·Π½ΡΡ
ΠΌΠ°ΡΠ΅ΡΠΈΠ°Π»ΠΎΠ² ΠΌΠΎΠ³ΡΡ Π±ΡΡΡ ΡΠ°Π·Π»ΠΈΡΠ½ΠΎΠΉ ΡΠΎΡΠΌΡ: ΠΏΠΈΡΠ°ΠΌΠΈΠ΄Π°Π»ΡΠ½ΠΎΠΉ, ΠΊΠΎΠ½ΠΈΡΠ΅ΡΠΊΠΎΠΉ, Ρ ΠΏΠ»ΠΎΡΠΊΠΈΠΌ Π³ΠΎΡΠΈΠ·ΠΎΠ½ΡΠ°Π»ΡΠ½ΡΠΌ Π΄Π½ΠΈΡΠ΅ΠΌ, ΠΏΠ°ΡΠ°Π±ΠΎΠ»ΠΈΡΠ΅ΡΠΊΠΎΠΉ ΠΈΠ»ΠΈ Π΄ΡΡΠ³ΠΎΠΉ ΡΠΈΠΌΠΌΠ΅ΡΡΠΈΡΠ½ΠΎΠΉ ΠΈΠ»ΠΈ Π½Π΅ΡΠΈΠΌΠΌΠ΅ΡΡΠΈΡΠ½ΠΎΠΉ ΡΠΎΡΠΌΡ. ΠΡΠΈ ΠΏΡΠΎΠ΅ΠΊΡΠΈΡΠΎΠ²Π°Π½ΠΈΠΈ Π³Π΅ΠΎΠΌΠ΅ΡΡΠΈΡΠ΅ΡΠΊΠΈΡ
ΠΏΠ°ΡΠ°ΠΌΠ΅ΡΡΠΎΠ² Π΄Π»Ρ ΡΠ°ΠΊΠΈΡ
Π±ΡΠ½ΠΊΠ΅ΡΠΎΠ² Π½ΠΎΡΠΌΠΈΡΡΠ΅ΡΡΡ ΡΠΎΠ»ΡΠΊΠΎ ΠΎΠ΄ΠΈΠ½ ΠΏΠ°ΡΠ°ΠΌΠ΅ΡΡ β ΡΠ°Π·ΠΌΠ΅Ρ Π²ΡΠΏΡΡΠΊΠ½ΠΎΠ³ΠΎ ΠΎΡΠ²Π΅ΡΡΡΠΈΡ, ΠΊΠΎΡΠΎΡΡΠΉ Π΄ΠΎΠ»ΠΆΠ΅Π½ ΠΎΠΏΡΠ΅Π΄Π΅Π»ΡΡΡΡΡ Π² Π·Π°Π²ΠΈΡΠΈΠΌΠΎΡΡΠΈ ΠΎΡ ΡΠ°Π·ΠΌΠ΅ΡΠ° ΠΌΠ°ΠΊΡΠΈΠΌΠ°Π»ΡΠ½ΠΎΠ³ΠΎ ΠΊΡΡΠΊΠ° ΡΡΠΏΡΡΠ΅Π³ΠΎ ΠΌΠ°ΡΠ΅ΡΠΈΠ°Π»Π°. Π£Π³ΠΎΠ» Π½Π°ΠΊΠ»ΠΎΠ½Π° ΡΡΠ΅Π½ΠΎΠΊ Π²ΠΎΡΠΎΠ½ΠΊΠΈ Π΄ΠΎΠΏΡΡΠΊΠ°Π΅ΡΡΡ ΠΏΡΠΈΠ½ΠΈΠΌΠ°ΡΡ ΠΏΡΠΎΠΈΠ·Π²ΠΎΠ»ΡΠ½ΡΠΌ, Π·Π° ΠΈΡΠΊΠ»ΡΡΠ΅Π½ΠΈΠ΅ΠΌ ΡΠ»ΡΡΠ°Π΅Π², ΠΊΠΎΠ³Π΄Π° ΠΏΠΎ ΡΡΠ»ΠΎΠ²ΠΈΡΠΌ ΡΠ΅Ρ
Π½ΠΎΠ»ΠΎΠ³ΠΈΠΈ ΡΡΠ΅Π±ΡΠ΅ΡΡΡ ΠΏΠΎΠ»Π½ΠΎΠ΅ ΠΎΠΏΠΎΡΠΎΠΆΠ½Π΅Π½ΠΈΠ΅ Π±ΡΠ½ΠΊΠ΅ΡΠ°. Π ΡΡΠΎΠΌ ΡΠ»ΡΡΠ°Π΅ ΡΠ³ΠΎΠ» Π½Π°ΠΊΠ»ΠΎΠ½Π° ΡΡΠ΅Π½ΠΎΠΊ ΡΠ»Π΅Π΄ΡΠ΅Ρ ΠΏΡΠΈΠ½ΠΈΠΌΠ°ΡΡ ΠΏΠΎ ΡΠ³Π»Ρ Π΅ΡΡΠ΅ΡΡΠ²Π΅Π½Π½ΠΎΠ³ΠΎ ΠΎΡΠΊΠΎΡΠ° ΡΡΠΏΡΡΠ΅Π³ΠΎ ΠΌΠ°ΡΠ΅ΡΠΈΠ°Π»Π° Ρ ΠΏΡΠ΅Π²ΡΡΠ΅Π½ΠΈΠ΅ΠΌ ΠΏΠΎΡΠ»Π΅Π΄Π½Π΅Π³ΠΎ Π½Π° 5β 7Β°.
ΠΡΠ½ΠΊΠ΅ΡΡ ΠΌΠ΅ΡΠ°Π»Π»ΠΈΡΠ΅ΡΠΊΠΈΠ΅ Π΄Π»Ρ ΡΠ²ΡΠ·Π½ΡΡ
ΠΌΠ°ΡΠ΅ΡΠΈΠ°Π»ΠΎΠ² Π³ΠΈΠ΄ΡΠ°Π²Π»ΠΈΡΠ΅ΡΠΊΠΎΠ³ΠΎ ΠΈΡΡΠ΅ΡΠ΅Π½ΠΈΡ Π½Π°Π΄Π»Π΅ΠΆΠΈΡ Π½Π°Π·Π½Π°ΡΠ°ΡΡ ΠΊΠΎΠ½ΠΈΡΠ΅ΡΠΊΠΎΠΉ, ΠΏΠΈΡΠ°ΠΌΠΈΠ΄Π°Π»ΡΠ½ΠΎΠΉ ΠΈΠ»ΠΈ Π»ΠΎΡΠΊΠΎΠ²ΠΎΠΉ ΡΠΎΡΠΌΡ. ΠΡΡΠ³ΠΈΠ΅ ΡΠΎΡΠΌΡ (ΠΏΠ°ΡΠ°Π±ΠΎΠ»ΠΈΡΠ΅ΡΠΊΠ°Ρ, Ρ ΠΏΠ»ΠΎΡΠΊΠΈΠΌ Π΄Π½ΠΈΡΠ΅ΠΌ), Π° ΡΠ°ΠΊΠΆΠ΅ Π½Π΅ΡΠΈΠΌΠΌΠ΅ΡΡΠΈΡΠ½ΡΠ΅ Π±ΡΠ½ΠΊΠ΅ΡΠ° Π½Π΅ Π΄ΠΎΠΏΡΡΠΊΠ°ΡΡΡΡ. Π£Π³ΠΎΠ» Π½Π°ΠΊΠ»ΠΎΠ½Π° ΡΡΠ°Π½ΠΎΠΊ ΠΈ ΡΠ°Π·ΠΌΠ΅ΡΡ Π²ΡΠΏΡΡΠΊΠ½ΠΎΠ³ΠΎ ΠΎΡΠ²Π΅ΡΡΡΠΈΡ ΡΠ°ΠΊΠΈΡ
Π±ΡΠ½ΠΊΠ΅ΡΠΎΠ² ΡΠ»Π΅Π΄ΡΠ΅Ρ ΡΠ°ΡΡΡΠΈΡΡΠ²Π°ΡΡ Π½Π° ΠΎΡΠ½ΠΎΠ²Π°Π½ΠΈΠΈ ΡΠΈΠ·ΠΈΠΊΠΎ-ΠΌΠ΅Ρ
Π°Π½ΠΈΡΠ΅ΡΠΊΠΈΡ
Ρ
Π°ΡΠ°ΠΊΡΠ΅ΡΠΈΡΡΠΈΠΊ ΡΡΠΏΡΡΠ΅Π³ΠΎ ΠΌΠ°ΡΠ΅ΡΠΈΠ°Π»Π°: ΡΠ³Π»Π° Π²Π½ΡΡΡΠ΅Π½Π½Π΅Π³ΠΎ ΡΡΠ΅Π½ΠΈΡ (ΡΠ³ΠΎΠ» Π΅ΡΡΠ΅ΡΡΠ²Π΅Π½Π½ΠΎΠ³ΠΎ ΠΎΡΠΊΠΎΡΠ° Π½Π΅ Π΄ΠΎΠΏΡΡΠΊΠ°Π΅ΡΡΡ), ΡΠ΄Π΅Π»ΡΠ½ΠΎΠ³ΠΎ ΡΡΠ΅ΠΏΠ»Π΅Π½ΠΈΡ, ΡΠ³Π»Π° Π²Π½Π΅ΡΠ½Π΅Π³ΠΎ ΡΡΠ΅Π½ΠΈΡ, ΡΡΡΠ΅ΠΊΡΠΈΠ²Π½ΠΎΠ³ΠΎ ΡΠ³Π»Π° ΡΡΠ΅Π½ΠΈΡ, ΡΡΠ½ΠΊΡΠΈΠΈ ΠΈΡΡΠ΅ΡΠ΅Π½ΠΈΡ, β ΠΎΠΏΡΠ΅Π΄Π΅Π»ΡΠ΅ΠΌΡΡ
Ρ ΠΏΠΎΠΌΠΎΡΡΡ ΠΏΡΠΈΠ±ΠΎΡΠΎΠ², ΠΈΠ·ΠΌΠ΅ΡΡΡΡΠΈΡ
ΡΠΎΠΏΡΠΎΡΠΈΠ²Π»Π΅Π½ΠΈΠ΅ ΡΡΠΏΡΡΠ΅Π³ΠΎ ΠΌΠ°ΡΠ΅ΡΠΈΠ°Π»Π° Π½Π° ΡΠ΄Π²ΠΈΠ³. Π£Π³ΠΎΠ» Π½Π°ΠΊΠ»ΠΎΠ½Π° ΡΡΠ΅Π½ΠΎΠΊ Π΄ΠΎΠΏΡΡΠΊΠ°Π΅ΡΡΡ ΠΏΡΠΈΠ±Π»ΠΈΠΆΠ΅Π½Π½ΠΎ Π²ΡΠ±ΠΈΡΠ°ΡΡ ΠΏΠΎ ΡΠ΅ΡΡ. 6 Π² Π·Π°Π²ΠΈΡΠΈΠΌΠΎΡΡΠΈ ΠΎΡ ΡΠ³Π»Π° Π²Π½Π΅ΡΠ½Π΅Π³ΠΎ ΡΡΠ΅Π½ΠΈΡ (ΡΠ³Π»Π° ΡΡΠ΅Π½ΠΈΡ ΡΡΠΏΡΡΠ΅Π³ΠΎ ΠΌΠ°ΡΠ΅ΡΠΈΠ°Π»Π° ΠΏΠΎ ΠΌΠ°ΡΠ΅ΡΠΈΠ°Π»Ρ ΡΡΠ΅Π½ΠΊΠΈ Π±ΡΠ½ΠΊΠ΅ΡΠ°).
ΠΡΠΈ ΠΏΡΠΎΠ΅ΠΊΡΠΈΡΠΎΠ²Π°Π½ΠΈΠΈ Π±ΡΠ½ΠΊΠ΅ΡΠΎΠ² Π΄Π»Ρ ΡΠ²ΡΠ·Π½ΡΡ
ΡΡΠΏΡΡΠΈΡ
ΠΌΠ°ΡΠ΅ΡΠΈΠ°Π»ΠΎΠ² ΠΎΠ±ΡΠ΅ΠΌΠ½ΠΎ-ΠΏΠ»Π°Π½ΠΈΡΠΎΠ²ΠΎΡΠ½ΠΎΠ΅ ΡΠ΅ΡΠ΅Π½ΠΈΠ΅ Π±ΡΠ½ΠΊΠ΅ΡΠ½ΠΎΠ³ΠΎ ΠΏΡΠΎΠΏΠ΅ΡΠ° Π·Π΄Π°Π½ΠΈΠΉ ΡΠ»Π΅Π΄ΡΠ΅Ρ ΡΡΡΠ°Π½Π°Π²Π»ΠΈΠ²Π°ΡΡ ΠΏΠΎΡΠ»Π΅ ΠΎΠΏΡΠ΅Π΄Π΅Π»Π΅Π½ΠΈΡ Π³Π΅ΠΎΠΌΠ΅ΡΡΠΈΡΠ΅ΡΠΊΠΈΡ
ΠΏΠ°ΡΠ°ΠΌΠ΅ΡΡΠΎΠ² Π±ΡΠ½ΠΊΠ΅ΡΠΎΠ². ΠΡΠ½ΠΊΠ΅ΡΠ½ΡΠ΅ ΠΏΡΠΎΠ»Π΅ΡΡ Π΄ΠΎΠ»ΠΆΠ½Ρ ΠΈΠΌΠ΅ΡΡ ΡΠ½ΠΈΡΠΈΡΠΈΡΠΎΠ²Π°Π½Π½ΡΠ΅ ΡΠ΅ΡΠΊΠΈ ΠΊΠΎΠ»ΠΎΠ½Π½ ΠΈ Π²ΡΡΠΎΡΡ ΡΡΠ°ΠΆΠ΅ΠΉ.
ΠΡΠΈ ΠΏΡΠΎΠ΅ΠΊΡΠΈΡΠΎΠ²Π°Π½ΠΈΠΈ Π±ΡΠ½ΠΊΠ΅ΡΠΎΠ² ΡΠ»Π΅Π΄ΡΠ΅Ρ ΠΎΠ±Π΅ΡΠΏΠ΅ΡΠΈΡΡ ΠΌΠ°ΠΊΡΠΈΠΌΠ°Π»ΡΠ½ΠΎΠ΅ ΠΈΡΠΏΠΎΠ»ΡΠ·ΠΎΠ²Π°Π½ΠΈΠ΅ Π²ΡΠ΅Π³ΠΎ Π³Π΅ΠΎΠΌΠ΅ΡΡΠΈΡΠ΅ΡΠΊΠΎΠ³ΠΎ ΠΎΠ±ΡΠ΅ΠΌΠ° Π±ΡΠ½ΠΊΠ΅ΡΠ° (Π½Π΅ ΠΌΠ΅Π½Π΅Π΅ 80 % ΠΏΡΠΈ Π·Π°Π³ΡΡΠ·ΠΊΠ΅).
ΠΠ°Π²Π»Π΅Π½ΠΈΠ΅ ΡΡΠΏΡΡΠ΅Π³ΠΎ ΠΌΠ°ΡΠ΅ΡΠΈΠ°Π»Π° Π½Π° ΡΡΠ΅Π½ΠΊΠΈ Π±ΡΠ½ΠΊΠ΅ΡΠ° ΡΠ»Π΅Π΄ΡΠ΅Ρ ΠΏΡΠΈΠ½ΠΈΠΌΠ°ΡΡ ΠΊΠ°ΠΊ Π΄Π»Ρ ΠΏΠΎΠ΄ΠΏΠΎΡΠ½ΠΎΠΉ ΡΡΠ΅Π½Ρ Π±Π΅Π· ΡΡΠ΅ΡΠ° ΡΠΈΠ» ΡΡΠ΅Π½ΠΈΡ ΠΌΠ΅ΠΆΠ΄Ρ ΡΡΠΏΡΡΠΈΠΌ ΠΌΠ°ΡΠ΅ΡΠΈΠ°Π»Π°ΠΌ ΠΈ ΡΡΠ΅Π½ΠΊΠ°ΠΌΠΈ Π±ΡΠ½ΠΊΠ΅ΡΠ°.
ΠΠΎΠ½ΡΡΡΡΠΊΡΠΈΠΈ Π±ΡΠ½ΠΊΠ΅ΡΠ° ΡΠ»Π΅Π΄ΡΠ΅Ρ ΡΠ°ΡΡΡΠΈΡΡΠ²Π°ΡΡ Π½Π° Π΄Π΅ΠΉΡΡΠ²ΠΈΠ΅ Π²ΡΠ΅ΠΌΠ΅Π½Π½ΠΎΠΉ Π½Π°Π³ΡΡΠ·ΠΊΠΈ ΠΎΡ Π²Π΅ΡΠ° ΡΡΠΏΡΡΠ΅Π³ΠΎ ΠΌΠ°ΡΠ΅ΡΠΈΠ°Π»Π°, Π·Π°ΠΏΠΎΠ»Π½ΡΡΡΠ΅Π³ΠΎ Π±ΡΠ½ΠΊΠ΅Ρ, ΠΏΠΎΡΡΠΎΡΠ½Π½ΡΡ
Π½Π°Π³ΡΡΠ·ΠΎΠΊ ΠΎΡ ΡΠΎΠ±ΡΡΠ²Π΅Π½Π½ΠΎΠ³ΠΎ Π²Π΅ΡΠ° ΠΊΠΎΠ½ΡΡΡΡΠΊΡΠΈΠΉ, Π²Π΅ΡΠ° ΡΡΡΠ΅ΡΠΎΠ²ΠΊΠΈ, Π° ΡΠ°ΠΊΠΆΠ΅ Π½Π° Π΄Π΅ΠΉΡΡΠ²ΠΈΠ΅ ΠΏΠΎΡΡΠΎΡΠ½Π½ΡΡ
ΠΈ Π²ΡΠ΅ΠΌΠ΅Π½Π½ΡΡ
Π½Π°Π³ΡΡΠ·ΠΎΠΊ Π½Π°Π΄Π±ΡΠ½ΠΊΠ΅ΡΠ½ΠΎΠ³ΠΎ ΠΏΠ΅ΡΠ΅ΠΊΡΡΡΠΈΡ.
Π‘ΡΠ΅Π½ΠΊΠΈ Π±ΡΠ½ΠΊΠ΅ΡΠ° ΡΠ»Π΅Π΄ΡΠ΅Ρ ΡΠ°ΡΡΡΠΈΡΡΠ²Π°ΡΡ Π½Π° ΡΠ°ΡΡΡΠ³ΠΈΠ²Π°ΡΡΠΈΠ΅ ΡΡΠΈΠ»ΠΈΡ Π² Π³ΠΎΡΠΈΠ·ΠΎΠ½ΡΠ°Π»ΡΠ½ΠΎΠΌ ΠΈ ΡΠΊΠ°ΡΠ½ΠΎΠΌ Π½Π°ΠΏΡΠ°Π²Π»Π΅Π½ΠΈΡΡ
ΠΈ ΠΈΠ·Π³ΠΈΠ±Π°ΡΡΠΈΠ΅ ΠΌΠΎΠΌΠ΅Π½ΡΡ ΠΎΡ ΠΌΠ΅ΡΡΠ½ΠΎΠ³ΠΎ ΠΈΠ·Π³ΠΈΠ±Π° ΠΈΠ· ΠΏΠ»ΠΎΡΠΊΠΎΡΡΠΈ ΡΡΠ°Π½ΠΎΠΊ. ΠΠΎΠ½ΡΡΡΡΠΊΡΠΈΠΈ Π±ΡΠ½ΠΊΠ΅ΡΠ° Π² ΡΠ΅Π»ΠΎΠΌ ΡΠ°ΡΡΡΠΈΡΡΠ²Π°ΡΡΡΡ Π½Π° ΠΎΠ±ΡΠΈΠΉ ΠΈΠ·Π³ΠΈΠ±, ΡΡΠΈΡΡΠ²Π°ΡΡΠΈΠΉ ΠΏΡΠΎΡΡΡΠ°Π½ΡΡΠ²Π΅Π½Π½ΡΡ ΡΠ°Π±ΠΎΡΡ Π±ΡΠ½ΠΊΠ΅ΡΠ°.
ΠΡΠΈ ΡΠ°ΡΡΠ΅ΡΠ΅ ΠΊΠΎΠ½ΡΡΡΡΠΊΡΠΈΠΉ Π±ΡΠ½ΠΊΠ΅ΡΠΎΠ² ΡΠ΄Π΅Π»ΡΠ½ΡΠΉ Π²Π΅Ρ g ΡΡΠΏΡΡΠ΅Π³ΠΎ ΠΌΠ°ΡΠ΅ΡΠΈΠ°Π»Π° Π½Π΅ΠΎΠ±Ρ
ΠΎΠ΄ΠΈΠΌΠΎ ΠΏΡΠΈΠ½ΠΈΠΌΠ°ΡΡ ΠΏΠΎ ΡΠ΅Ρ
Π½ΠΎΠ»ΠΎΠ³ΠΈΡΠ΅ΡΠΊΠΎΠΌΡ Π·Π°Π΄Π°Π½ΠΈΡ.
ΠΡΠ½ΠΊΠ΅ΡΡ Π΄Π»Ρ ΡΠ΅ΠΌΠ΅Π½ΡΠ° ΠΈ Π΄ΡΡΠ³ΠΈΡ
ΠΌΠ°ΡΠ΅ΡΠΈΠ°Π»ΠΎΠ² ΡΠ»Π΅Π΄ΡΠ΅Ρ ΠΏΡΠΎΠ΅ΠΊΡΠΈΡΠΎΠ²Π°ΡΡ, ΠΊΠ°ΠΊ ΠΏΡΠ°Π²ΠΈΠ»ΠΎ. ΠΆΠ΅Π»Π΅Π·ΠΎΠ±Π΅ΡΠΎΠ½Π½ΡΠΌΠΈ ΠΈΠ»ΠΈ ΡΡΠ°Π»Π΅ΠΆΠ΅Π»Π΅Π·ΠΎΠ±Π΅ΡΠΎΠ½Π½ΡΠΌΠΈ (ΠΈΠ· ΠΏΠ»ΠΎΡΠΊΠΈΡ
ΠΆΠ΅Π»Π΅Π·ΠΎΠ±Π΅ΡΠΎΠ½Π½ΡΡ
ΠΏΠ»ΠΈΡ ΠΈ ΡΡΠ°Π»ΡΠ½ΠΎΠ³ΠΎ ΠΊΠ°ΡΠΊΠ°ΡΠ°), ΠΈΠ»ΠΈ ΡΠ±ΠΎΡΠ½ΠΎ-ΠΌΠΎΠ½ΠΎΠ»ΠΈΡΠ½ΡΠΌΠΈ ΠΆΠ΅Π»Π΅Π·ΠΎΠ±Π΅ΡΠΎΠ½Π½ΡΠΌΠΈ. Π‘ΡΠ°Π»ΡΠ½ΡΠΌΠΈ Π΄ΠΎΠΏΡΡΠΊΠ°Π΅ΡΡΡ ΠΏΡΠΎΠ΅ΠΊΡΠΈΡΠΎΠ²Π°ΡΡ Π²ΠΎΡΠΎΠ½ΠΊΠΈ, ΡΡΠΆΠ°ΡΡΠΈΠ΅ΡΡ ΡΠ°ΡΡΠΈ Π±ΡΠ½ΠΊΠ΅ΡΠΎΠ², ΠΏΠ°ΡΠ°Π±ΠΎΠ»ΠΈΡΠ΅ΡΠΊΠΈΠ΅ (Π²ΠΈΡΡΡΠΈΠ΅ Π±ΡΠ½ΠΊΠ΅ΡΠ°), Π° ΡΠ°ΠΊΠΆΠ΅ Π±ΡΠ½ΠΊΠ΅ΡΠ°, ΠΊΠΎΡΠΎΡΡΠ΅ ΠΏΠΎ ΡΠ΅Ρ
Π½ΠΎΠ»ΠΎΠ³ΠΈΡΠ΅ΡΠΊΠΈΠΌ ΡΡΠ»ΠΎΠ²ΠΈΡΠΌ ΠΏΠΎΠ΄Π²Π΅ΡΠ³Π°ΡΡΡΡ ΠΌΠ΅Ρ
Π°Π½ΠΈΡΠ΅ΡΠΊΠΈΠΌ, Ρ
ΠΈΠΌΠΈΡΠ΅ΡΠΊΠΈΠΌ ΠΈ ΡΠ΅ΠΌΠΏΠ΅ΡΠ°ΡΡΡΠ½ΡΠΌ β’ΠΎΠ·Π΄Π΅ΠΉΡΡΠ²ΠΈΡΠΌ ΡΡΠΏΡΡΠ΅Π³ΠΎ ΠΌΠ°ΡΠ΅ΡΠΈΠ°Π»Π° ΠΈ Π½Π΅ ΠΌΠΎΠ³ΡΡ Π±ΡΡΡ Π²ΡΠΏΠΎΠ»Π½Π΅Π½Ρ ΠΈΠ· ΠΆΠ΅Π»Π΅Π·ΠΎΠ±Π΅ΡΠΎΠ½Π°.
ΠΠ½ΡΡΡΠ΅Π½Π½ΠΈΠ΅ Π³ΡΠ°Π½ΠΈ ΡΠ³Π»ΠΎΠ² Π±ΡΠ½ΠΊΠ΅ΡΠΎΠ² Π΄Π»Ρ ΡΠ²ΡΠ·Π½ΡΡ
ΠΌΠ°ΡΠ΅ΡΠΈΠ°Π»ΠΎΠ² ΡΠ»Π΅Π΄ΡΠ΅Ρ ΠΏΡΠΎΠ΅ΠΊΡΠΈΡΠΎΠ²Π°ΡΡ Ρ Π°ΡΡΠ°ΠΌΠΈ ΠΈΠ»ΠΈ Π·Π°ΠΊΡΡΠ³Π»Π΅Π½ΠΈΡΠΌΠΈ.
ΠΡΠ½ΠΊΠ΅ΡΠ° Π΄Π»Ρ ΠΏΡΠ»Π΅Π²ΠΈΠ΄Π½ΡΡ
ΠΌΠ°ΡΠ΅ΡΠΈΠ°Π»ΠΎΠ² Π΄ΠΎΠ»ΠΆΠ½Ρ Π±ΡΡΡ Π³Π΅ΡΠΌΠ΅ΡΠΈΡΠ½ΡΠΌΠΈ, Π° Π±ΡΠ½ΠΊΠ΅ΡΠ°, ΠΏΡΠ΅Π΄Π½Π°Π·Π½Π°ΡΠ΅Π½Π½ΡΠ΅ Π΄Π»Ρ ΠΏΡΠ»ΡΡΠΈΡ
ΠΌΠ°ΡΠ΅ΡΠΈΠ°Π»ΠΎΠ² (ΡΡΡ
ΠΈΠ΅ ΠΊΡΡΠΊΠΎΠ²ΡΠ΅ ΠΌΠ°ΡΠ΅ΡΠΈΠ°Π»Ρ Π³ΠΎΡΠ½ΡΡ
ΠΏΠΎΡΠΎΠ΄ ΠΌΠ°Π»ΠΎΠΉ ΠΊΡΠ΅ΠΏΠΎΡΡΠΈ, Π½Π°ΠΏΡΠΈΠΌΠ΅Ρ, ΠΈΠ·Π²Π΅ΡΡΠ½ΡΠΊ), β ΠΎΠ±ΠΎΡΡΠ΄ΠΎΠ²Π°Π½Ρ Π°ΡΠΏΠΈΡΠ°ΡΠΈΠΎΠ½Π½ΡΠΌΠΈ ΡΡΡΠ°Π½ΠΎΠ²ΠΊΠ°ΠΌΠΈ.
ΠΠ½ΡΡΡΠ΅Π½Π½ΠΈΠ΅ ΠΏΠΎΠ²Π΅ΡΡ
Π½ΠΎΡΡΠΈ Π±ΡΠ½ΠΊΠ΅ΡΠΎΠ² ΡΠ»Π΅Π΄ΡΠ΅Ρ ΡΠ°Π·Π΄Π΅Π»ΡΡΡ Π½Π° ΡΡΠ°ΡΡΠΊΠΈ, ΠΏΠΎΠ΄Π²Π΅ΡΠ³Π°ΡΡΠΈΠ΅ΡΡ ΠΈΠ·Π½ΠΎΡΡ (I ΠΈ II Π·ΠΎΠ½Ρ) ΠΈ Π½Π΅ ΠΏΠΎΠ΄Π²Π΅ΡΠ³Π°ΡΡΠΈΠ΅ΡΡ ΠΈΠ·Π½ΠΎΡΡ (III Π·ΠΎΠ½Π°). I Π·ΠΎΠ½Π° β ΡΡΠ°ΡΡΠΎΠΊ, ΠΏΠΎΠ΄Π²Π΅ΡΠ³Π°ΡΡΠΈΠΉΡΡ ΡΠ΄Π°ΡΠ°ΠΌ ΠΏΠΎΡΠΎΠΊΠ° ΡΡΠΏΡΡΠ΅Π³ΠΎ ΠΌΠ°ΡΠ΅ΡΠΈΠ°Π»Π° ΠΏΡΠΈ Π·Π°Π³ΡΡΠ·ΠΊΠ΅ Π±ΡΠ½ΠΊΠ΅ΡΠ° ΠΈ ΠΈΡΡΠΈΡΠ°Π½ΠΈΡ ΠΏΡΠΈ Π΅Π³ΠΎ ΡΠ°Π·Π³ΡΡΠ·ΠΊΠ΅. I Π·ΠΎΠ½Ρ ΡΠ»Π΅Π΄ΡΠ΅Ρ Π·Π°ΡΠΈΡΠ°ΡΡ, ΠΊΠ°ΠΊ ΠΏΡΠ°Π²ΠΈΠ»ΠΎ ΠΈΡΠΏΠΎΠ»ΡΠ·ΡΡ ΠΏΡΠΈΠ½ΡΠΈΠΏ ΡΠ°ΠΌΠΎΠ·Π°ΡΠΈΡΡ, ΠΈΠ»ΠΈ ΠΈΠ·Π½ΠΎΡΠΎΡΡΠΎΠΉΠΊΠΎΠΉ Π·Π°ΡΠΈΡΡ Π½Π° ΡΠΏΡΡΠ³ΠΎΠΌ ΠΎΡΠ½ΠΎΠ²Π°Π½ΠΈΠΈ ΠΈΠ»ΠΈ ΡΠ΅Π·ΠΈΠ½ΠΎΠΉ. II Π·ΠΎΠ½Π° β ΡΡΠ°ΡΡΠΎΠΊ, ΠΏΠΎΠ΄Π²Π΅ΡΠ³Π°ΡΡΠΈΠΉΡΡ ΠΈΡΡΠΈΡΠ°Π½ΠΈΡ ΡΡΠΏΡΡΠΈΠΌ ΠΌΠ°ΡΠ΅ΡΠΈΠ°Π»ΠΎΠΌ Π² ΠΏΡΠΎΡΠ΅ΡΡΠ΅ ΡΠ°Π·Π³ΡΡΠ·ΠΊΠΈ Π±ΡΠ½ΠΊΠ΅ΡΠ°. II Π·ΠΎΠ½Ρ ΡΠ»Π΅Π΄ΡΠ΅Ρ Π·Π°ΡΠΈΡΠ°ΡΡ ΠΊΠ°ΠΌΠ΅Π½Π½ΡΠΌ Π»ΠΈΡΡΠ΅ΠΌ, ΡΠ»Π°ΠΊΠΎΡΠΈΡΠ°Π»Π»ΠΎΠΌ, ΠΏΠΎΠ»ΠΈΠΌΠ΅ΡΠ½ΡΠΌΠΈ ΠΌΠ°ΡΠ΅ΡΠΈΠ°Π»Π°ΠΌΠΈ, ΡΠ΅Π·ΠΈΠ½ΠΎΠΉ ΠΈ Π΄ΡΡΠ³ΠΈΠΌΠΈ ΠΌΠ°ΡΠ΅ΡΠΈΠ°Π»Π°ΠΌΠΈ, Π° ΠΏΡΠΈ ΡΠ΅ΠΌΠΏΠ΅ΡΠ°ΡΡΡΠ΅ ΡΡΠΏΡΡΠ΅Π³ΠΎ ΠΌΠ°ΡΠ΅ΡΠΈΠ°Π»Π° ΡΠ²ΡΡΠ΅ 50 Β°Π‘ β ΡΠ»Π°ΠΊΠΎΠΊΠ°ΠΌΠ΅Π½Π½ΡΠΌ ΠΈ ΠΊΠ°ΠΌΠ΅Π½Π½ΡΠΌ Π»ΠΈΡΡΠ΅ΠΌ ΡΠ΅ΡΠΌΠΎΡΡΠΎΠΉΠΊΠΈΡ
ΡΠΎΡΡΠ°Π²ΠΎΠ². III Π·ΠΎΠ½Π° β ΡΡΠ°ΡΡΠΎΠΊ, Π½Π΅ ΡΡΠ΅Π±ΡΡΡΠΈΠΉ Π·Π°ΡΠΈΡΡ.
ΠΡΠΈ ΡΠΎΡΠ΅ΡΠ°Π½ΠΈΠΈ ΠΈΡΡΠΈΡΠ°ΡΡΠ΅Π³ΠΎ Π²ΠΎΠ·Π΄Π΅ΠΉΡΡΠ²ΠΈΡ, Π²ΡΡΠΎΠΊΠΎΠΉ ΡΠ΅ΠΌΠΏΠ΅ΡΠ°ΡΡΡΡ ΠΈ Ρ
ΠΈΠΌΠΈΡΠ΅ΡΠΊΠΎΠΉ Π°Π³ΡΠ΅ΡΡΠΈΠΈ ΡΡΠΏΡΡΠ΅Π³ΠΎ ΠΌΠ°ΡΠ΅ΡΠΈΠ°Π»Π° Π²Π½ΡΡΡΠ΅Π½Π½ΠΈΠ΅ ΠΏΠΎΠ²Π΅ΡΡ
Π½ΠΎΡΡΠΈ Π±ΡΠ½ΠΊΠ΅ΡΠΎΠ² ΡΠ»Π΅Π΄ΡΠ΅Ρ Π·Π°ΡΠΈΡΠ°ΡΡ ΠΏΠ»ΠΈΡΠ°ΠΌΠΈ ΠΈΠ· ΡΠ»Π°ΠΊΠΎΠΊΠ°ΠΌΠ΅Π½Π½ΠΎΠ³ΠΎ Π»ΠΈΡΡΡ, ΠΈΠ·Π½ΠΎΡΠΎΡΡΠΎΠΉΠΊΠΎΠ³ΠΎ ΠΈ ΠΆΠ°ΡΠΎΡΡΠΎΠΉΠΊΠΎΠ³ΠΎ Π±Π΅ΡΠΎΠ½Π° (Ρ Π·Π°ΠΏΠΎΠ»Π½Π΅Π½ΠΈΠ΅ΠΌ ΡΠ²ΠΎΠ² ΡΠ°ΡΡΠ²ΠΎΡΠΎΠΌ ΠΊΠΈΡΠ»ΠΎΡΠΎΡΡΠΎΠΉΠΊΠΈΡ
ΠΈ ΠΆΠ°ΡΠΎΡΡΠΎΠΉΠΊΠΈΡ
ΡΠΎΡΡΠ°Π²ΠΎΠ²), Π° ΡΠ°ΠΊΠΆΠ΅ Π² ΠΎΡΠ΄Π΅Π»ΡΠ½ΡΡ
ΡΠ»ΡΡΠ°ΡΡ
Π»ΠΈΡΡΠ°ΠΌΠΈ ΠΈΠ· ΡΠΎΠΎΡΠ²Π΅ΡΡΡΠ²ΡΡΡΠΈΡ
Π²ΠΈΠ΄ΠΎΠ² ΡΡΠ°Π»Π΅ΠΉ (ΡΠ΅ΡΠΌΠΎΡΡΠΎΠΉΠΊΠΈΡ
ΠΈ Π΄Ρ.).
ΠΡΠΈ ΡΠΊΡΠΏΠ»ΡΠ°ΡΠ°ΡΠΈΠΈ Π±ΡΠ½ΠΊΠ΅ΡΠΎΠ² Π² Π°Π³ΡΠ΅ΡΡΠΈΠ²Π½ΠΎΠΉ ΠΈ Π³Π°Π·ΠΎΠ²ΠΎΠΉ ΡΡΠ΅Π΄Π΅ ΠΈΡ
Π½Π°ΡΡΠΆΠ½ΡΠ΅ ΠΏΠΎΠ²Π΅ΡΡ
Π½ΠΎΡΡΠΈ ΡΠ»Π΅Π΄ΡΠ΅Ρ Π·Π°ΡΠΈΡΠ°ΡΡ ΠΎΡ ΠΊΠΎΡΡΠΎΠ·ΠΈΠΈ Π² ΡΠΎΠΎΡΠ²Π΅ΡΡΡΠ²ΠΈΠΈ Ρ ΡΡΠ΅Π±ΠΎΠ²Π°Π½ΠΈΡΠΌΠΈ Π‘ΠΠΈΠ 2.03.11-85. ΠΡΠΈ ΠΏΡΠΎΠ΅ΠΊΡΠΈΡΠΎΠ²Π°Π½ΠΈΠΈ Π±ΡΠ½ΠΊΠ΅ΡΠΎΠ² Π΄Π»Ρ Π²Π»Π°ΠΆΠ½ΡΡ
ΡΡΠΏΡΡΠΈΡ
ΠΌΠ°ΡΠ΅ΡΠΈΠ°Π»ΠΎΠ², ΡΠ°ΡΠΏΠΎΠ»Π°Π³Π°Π΅ΠΌΡΡ
Π² Π½Π΅ΠΎΡΠ°ΠΏΠ»ΠΈΠ²Π°Π΅ΠΌΡΡ
ΠΏΠΎΠΌΠ΅ΡΠ΅Π½ΠΈΡΡ
, Π½Π΅ΠΎΠ±Ρ
ΠΎΠ΄ΠΈΠΌΠΎ ΠΏΡΠ΅Π΄ΡΡΠΌΠ°ΡΡΠΈΠ²Π°ΡΡ ΡΡΡΠ΅ΠΊΡΠΈΠ²Π½ΡΠΉ ΠΎΠ±ΠΎΠ³ΡΠ΅Π² ΡΡΠ΅Π½ Π±ΡΠ½ΠΊΠ΅ΡΠΎΠ² Π² ΡΠ΅Π»ΡΡ
ΠΏΡΠ΅Π΄ΠΎΡΠ²ΡΠ°ΡΠ΅Π½ΠΈΡ ΡΠΌΠ΅ΡΠ·Π°Π½ΠΈΡ ΠΌΠ°ΡΠ΅ΡΠΈΠΌΠ° Π² Π±ΡΠ½ΠΊΠ΅ΡΠ΅.
Π£ΡΠ΅ΠΏΠ»ΠΈΡΠ΅Π»Ρ ΡΡΠ΅Π½ Π±ΡΠ½ΠΊΠ΅ΡΠΎΠ² Π΄Π»Ρ ΠΏΡΠ»Π΅Π²ΠΈΠ΄Π½ΠΎΠ³ΠΎ ΠΌΠ°ΡΠ΅ΡΠΈΠ°Π»Π° Π²ΠΎ ΠΈΠ·Π±Π΅ΠΆΠ°Π½ΠΈΠ΅ ΠΊΠΎΠ½Π΄Π΅Π½ΡΠ°ΡΠΈΠΈ Π²ΠΎΠ΄ΡΠ½ΡΡ
ΠΏΠ°ΡΠΎΠ² ΡΠ»Π΅Π΄ΡΠ΅Ρ ΡΠ°ΡΠΏΠΎΠ»Π°Π³Π°ΡΡ ΡΠ½Π°ΡΡΠΆΠΈ ΠΈ Π²ΡΠΏΠΎΠ»Π½ΡΡΡ ΠΈΠ· Π½Π΅ΡΠ³ΠΎΡΠ°Π΅ΠΌΡΡ
ΠΌΠ°ΡΠ΅ΡΠΈΠ°Π»ΠΎΠ².
ΠΡΠΈ ΠΏΡΠΎΠ΅ΠΊΡΠΈΡΠΎΠ²Π°Π½ΠΈΠΈ Π±ΡΠ½ΠΊΠ΅ΡΠΎΠ² Π΄Π»Ρ ΡΠ²ΡΠ·Π½ΡΡ
ΠΌΠ°ΡΠ΅ΡΠΈΠ°Π»ΠΎΠ², ΠΏΠΎΡΡΡΠΏΠ°ΡΡΠΈΡ
Π² Π½Π°Π³ΡΠ΅ΡΠΎΠΌ ΠΈΠ»ΠΈ ΡΠΌΠ΅ΡΠ·ΡΠ΅ΠΌΡΡ ΡΠΎΡΡΠΎΡΠ½ΠΈΠΈ, Π½Π΅ΠΎΠ±Ρ
ΠΎΠ΄ΠΈΠΌΠΎ ΠΏΡΠ΅Π΄ΡΡΠΌΠ°ΡΡΠΈΠ²Π°ΡΡ ΡΠ΅ΠΏΠ»ΠΎΠΈΠ·ΠΎΠ»ΡΡΠΈΡ ΡΡΠ΅Π½ Π±ΡΠ½ΠΊΠ΅ΡΠΎΠ² Π² ΡΠΎΠΎΡΠ²Π΅ΡΡΡΠ²ΠΈΠΈ Ρ ΡΠ΅ΠΏΠ»ΠΎΡΠ΅Ρ
Π½ΠΈΡΠ΅ΡΠΊΠΈΠΌ ΡΠ°ΡΡΠ΅ΡΠΎΠΌ, ΠΈΡΠΊΠ»ΡΡΠ°ΡΡΡΡ ΠΊΠΎΠ½Π΄Π΅Π½ΡΠ°ΡΠΈΡ Π²ΠΎΠ΄ΡΠ½ΡΡ
ΠΏΠ°ΡΠΎΠ² ΠΏΡΠΈ Π½Π°Π³ΡΠ΅ΡΠΎΠΌ ΠΌΠ°ΡΠ΅ΡΠΈΠ°Π»Π΅, Π° ΡΠ°ΠΊΠΆΠ΅ ΠΏΡΠΈΠΌΠ΅ΡΠ·Π°Π½ΠΈΠ΅ ΠΊ ΡΡΠ΅Π½Π°ΠΌ ΡΠΌΠ΅ΡΠ·ΡΠ΅Π³ΠΎΡΡ ΠΌΠ°ΡΠ΅ΡΠΈΠ°Π»Π°.
ΠΡΠ½ΠΊΠ΅ΡΠ°, ΠΊΠ°ΠΊ ΠΏΡΠ°Π²ΠΈΠ»ΠΎ, Π΄ΠΎΠ»ΠΆΠ½Ρ ΠΈΠΌΠ΅ΡΡ ΠΏΠ΅ΡΠ΅ΠΊΡΡΡΠΈΡ ΠΈΠ· Π½Π΅ΡΠ³ΠΎΡΠ°Π΅ΠΌΡΡ
ΠΌΠ°ΡΠ΅ΡΠΈΠ°Π»ΠΎΠ² Ρ ΠΏΡΠΎΠ΅ΠΌΠ°ΠΌΠΈ Π΄Π»Ρ Π·Π°Π³ΡΡΠ·ΠΊΠΈ. ΠΡΠ»ΠΈ Π·Π°Π³ΡΡΠ·ΠΊΠ° ΠΏΡΠΎΠΈΠ·Π²ΠΎΠ΄ΠΈΡΡΡ ΡΡΠ΅Π΄ΡΡΠ²Π°ΠΌΠΈ Π½Π΅ Π½Π΅ΠΏΡΠ΅ΡΡΠ²Π½ΠΎΠ³ΠΎ ΡΡΠ°Π½ΡΠΏΠΎΡΡΠ° (Π²Π°Π³ΠΎΠ½Ρ, Π°Π²ΡΠΎΠΌΠ°ΡΠΈΠ½Ρ, Π³ΡΠ΅ΠΉΡΠ΅ΡΡ), Π΄ΠΎΠΏΡΡΠΊΠ°Π΅ΡΡΡ Π²ΡΠΏΠΎΠ»Π½ΡΡΡ Π±ΡΠ½ΠΊΠ΅Ρ Π±Π΅Π· ΠΏΠ΅ΡΠ΅ΠΊΡΡΡΠΈΡ, Π½ΠΎ Ρ ΠΎΠ±ΡΠ·Π°ΡΠ΅Π»ΡΠ½ΡΠΌ ΡΡΡΡΠΎΠΉΡΡΠ²ΠΎΠΌ ΡΠΏΠ»ΠΎΡΠ½ΠΎΠ³ΠΎ ΠΎΠ³ΡΠ°ΠΆΠ΄Π΅Π½ΠΈΡ Π²ΡΡΠΎΡΠΎΠΉ Π½Π΅ ΠΌΠ΅Π½Π΅Π΅ 1 ΠΌ Ρ Π±ΠΎΠΊΠΎΠ² ΠΈ ΡΠΎ ΡΡΠΎΡΠ°Π½Ρ, ΠΏΡΠΎΡΠΈΠ²ΠΎΠΏΠΎΠ»ΠΎΠΆΠ½ΠΎΠΉ Π·Π°Π³ΡΡΠ·ΠΊΠ΅. ΠΠ΅ΠΎΠ±Ρ
ΠΎΠ΄ΠΈΠΌΠΎΡΡΡ ΡΡΡΡΠΎΠΉΡΡΠ²Π° ΡΡΠ°Π»ΡΠ½ΡΡ
ΡΠ΅ΡΠ΅ΡΠΎΠΊ Π΄Π»Ρ ΠΏΠ΅ΡΠ΅ΠΊΡΡΡΠΈΡ ΡΠ΅Ρ
Π½ΠΎΠ»ΠΎΠ³ΠΈΡΠ΅ΡΠΊΠΈΡ
ΠΏΡΠΎΠ΅ΠΌΠΎΠ² ΠΈ ΡΠ°Π·ΠΌΠ΅Ρ ΡΡΠ΅Π΅ΠΊ ΡΠ΅ΡΠ΅ΡΠΎΠΊ ΠΎΠΏΡΠ΅Π΄Π΅Π»ΡΡΡΡΡ ΡΠ΅Ρ
Π½ΠΎΠ»ΠΎΠ³ΠΈΡΠ΅ΡΠΊΠΈΠΌ Π·Π°Π΄Π°Π½ΠΈΠ΅ΠΌ.
Π Π±ΡΠ½ΠΊΠ΅ΡΠ°Ρ
Π΄Π»Ρ ΠΏΡΠ»Π΅Π²ΠΈΠ΄Π½ΡΡ
ΠΌΠ°ΡΠ΅ΡΠΈΠ°Π»ΠΎΠ² Π½Π΅ΠΎΠ±Ρ
ΠΎΠ΄ΠΈΠΌΠΎ ΠΏΡΠ΅Π΄ΡΡΠΌΠ°ΡΡΠΈΠ²Π°ΡΡ ΡΠ²Π΅ΡΡ
Ρ ΠΏΠ΅ΡΠ΅ΠΊΡΡΡΠΈΡ ΠΌΠΎΠ½ΠΎΠ»ΠΈΡΠ½ΡΡ Π°ΡΠΌΠΈΡΠΎΠ²Π°Π½Π½ΡΡ ΡΡΡΠΆΠΊΡ ΡΠΎΠ»ΡΠΈΠ½ΠΎΠΉ 50 ΠΌΠΌ, Π΅ΡΠ»ΠΈ ΡΠΎΠ»ΡΠΈΠ½Π° ΠΏΠ»ΠΈΡ Π° ΠΌΠ΅ΡΡΠ΅ ΡΡΡΠΊΠ° 100 ΠΌΠΌ ΠΈ ΠΌΠ΅Π½Π΅Π΅.
Π Π±ΡΠ½ΠΊΠ΅ΡΠ°Ρ
, ΠΏΡΠ΅Π΄Π½Π°Π·Π½Π°ΡΠ΅Π½Π½ΡΡ
Π΄Π»Ρ Π³ΠΎΡΡΡΠΈΡ
ΡΡΠΏΡΡΠΈΡ
ΠΌΠ°ΡΠ΅ΡΠΈΠ°Π»ΠΎΠ², ΠΌΠ΅ΠΆΠ΄Ρ ΠΈΠ·Π½ΠΎΡΠΎΡΡΠΎΠΉΠΊΠΎΠΉ Π·Π°ΡΠΈΡΠΎΠΉ ΠΈ Π½Π΅ΡΡΡΠ΅ΠΉ ΠΊΠΎΠ½ΡΡΡΡΠΊΡΠΈΠ΅ΠΉ ΡΠ»Π΅Π΄ΡΠ΅Ρ ΠΏΡΠ΅Π΄ΡΡΠΌΠ°ΡΡΠΈΠ²Π°ΡΡ ΡΠ΅ΡΠΌΠΎΠΈΠ·ΠΎΠ»ΡΡΠΈΡ ΠΈΠ· Π½Π΅ΡΠ³ΠΎΡΠ°Π΅ΠΌΡΡ
ΠΌΠ°ΡΠ΅ΡΠΈΠ°Π»ΠΎΠ²: Π² ΡΡΠ°Π»ΡΠ½ΡΡ
Π±ΡΠ½ΠΊΠ΅ΡΠ°Ρ
β ΠΏΡΠΈ ΡΠ΅ΠΌΠΏΠ΅ΡΠ°ΡΡΡΠ΅ Π½Π°Π³ΡΠ΅Π²Π° ΡΠ²ΡΡΠ΅ 300 Β°Π‘, Π° Π² ΠΆΠ΅Π»Π΅Π·ΠΎΠ±Π΅ΡΠΎΠ½Π½ΡΡ
β ΡΠ²ΡΡΠ΅ 100 Β°Π‘.
Π Π±ΡΠ½ΠΊΠ΅ΡΠ°Ρ
, ΠΏΡΠ΅Π΄Π½Π°Π·Π½Π°ΡΠ΅Π½Π½ΡΡ
Π΄Π»Ρ Ρ
ΡΠ°Π½Π΅Π½ΠΈΡ ΡΡΠΏΡΡΠΈΡ
ΠΌΠ°ΡΠ΅ΡΠΈΠ°Π»ΠΎΠ², Π²ΡΠ΄Π΅Π»ΡΡΡΠΈΡ
Π²ΠΎΡΠΏΠ»Π°ΠΌΠ΅Π½ΡΡΡΠΈΠ΅ΡΡ Π³Π°Π·Ρ (Π½Π°ΠΏΡΠΈΠΌΠ΅Ρ, ΠΌΠ΅ΡΠ°Π½ ΠΈΠ· ΠΊΠ°ΠΌΠ΅Π½Π½ΠΎΠ³ΠΎ ΡΠ³Π»Ρ), ΠΊΠΎΠ½ΡΡΡΡΠΊΡΠΈΡ ΠΏΠ΅ΡΠ΅ΠΊΡΡΡΠΈΡ Π½Π΅ Π΄ΠΎΠ»ΠΆΠ½Π° ΠΈΠΌΠ΅ΡΡ Π²ΡΡΡΡΠΏΠ°ΡΡΠΈΡ
Π²Π½ΠΈΠ· ΡΠ΅Π±Π΅Ρ.
Π ΠΏΠ΅ΡΠ΅ΠΊΡΡΡΠΈΡΡ
Π±ΡΠ½ΠΊΠ΅ΡΠΎΠ² Π΄ΠΎΠ»ΠΆΠ½Ρ Π±ΡΡΡ ΡΡΡΡΠΎΠ΅Π½Ρ Π»ΡΠΊΠΈ, Π·Π°ΠΊΡΡΠ²Π°Π΅ΠΌΡΠ΅ Π·Π°ΠΏΠΎΠ΄Π»ΠΈΡΠΎ Ρ ΠΏΠ΅ΡΠ΅ΠΊΡΡΡΠΈΠ΅ΠΌ ΠΌΠ΅ΡΠ°Π»Π»ΠΈΡΠ΅ΡΠΊΠΈΠΌΠΈ ΠΊΡΡΡΠΊΠ°ΠΌΠΈ. Π Π½Π°Π΄Π±ΡΠ½ΠΊΠ΅ΡΠ½ΠΎΠΌ ΠΏΠΎΠΌΠ΅ΡΠ΅Π½ΠΈΠΈ Π΄ΠΎΠ»ΠΆΠ½Ρ ΠΏΡΠ΅Π΄ΡΡΠΌΠ°ΡΡΠΈΠ²Π°ΡΡΡΡ ΠΏΠΎΠ΄ΡΠ΅ΠΌΠ½ΠΎ-ΡΡΠ°Π½ΡΠΏΠΎΡΡΠ½ΡΠ΅ ΡΡΡΡΠΎΠΉΡΡΠ²Π°, Π° Π²Π½ΡΡΡΠΈ Π±ΡΠ½ΠΊΠ΅ΡΠΎΠ² ΡΠ½ΠΈΠ·Ρ ΠΏΠ΅ΡΠ΅ΠΊΡΡΡΠΈΠΉ β ΠΏΠ΅ΡΠ»ΠΈ Π΄Π»Ρ ΠΊΡΠ΅ΠΏΠ»Π΅Π½ΠΈΡ ΡΠ°Π»Π΅ΠΉ ΠΈ Π΄ΡΡΠ³ΠΈΡ
ΠΌΠΎΠ½ΡΠ°ΠΆΠ½ΡΡ
ΡΡΠ΅Π΄ΡΡΠ².
ΠΡΠ½ΠΊΠ΅ΡΠ° Π΄ΠΎΠ»ΠΆΠ½Ρ ΠΎΡΠ½Π°ΡΠ°ΡΡΡΡ ΡΡΡΡΠΎΠΉΡΡΠ²Π°ΠΌΠΈ Π΄Π»Ρ ΠΌΠ΅Ρ
Π°Π½ΠΈΡΠ΅ΡΠΊΠΎΠΉ ΠΎΡΠΈΡΡΠΊΠΈ ΡΡΠ΅Π½ ΠΈ ΡΠ΄Π°Π»Π΅Π½ΠΈΡ Π·Π°Π²ΠΈΡΡΠ΅Π³ΠΎ ΡΡΠΏΡΡΠ΅Π³ΠΎ ΠΌΠ°ΡΠ΅ΡΠΈΠ°Π»Π°, ΡΡΠΎΠ±Ρ ΠΈΡΠΊΠ»ΡΡΠ°Π»Π°ΡΡ Π½Π΅ΠΎΠ±Ρ
ΠΎΠ΄ΠΈΠΌΠΎΡΡΡ ΡΠΏΡΡΠΊΠ° Π»ΡΠ΄Π΅ΠΉ Π² Π±ΡΠ½ΠΊΠ΅ΡΠ°.
Π‘ΠΈΠ»ΠΎΡΡ ΠΈ ΡΠΈΠ»ΠΎΡΠ½ΡΠ΅ ΠΊΠΎΠ½ΡΡΡΡΠΊΡΠΈΠΈ Π΄Π»Ρ Ρ
ΡΠ°Π½Π΅Π½ΠΈΡ ΡΡΠΏΡΡΠΈΡ
ΠΌΠ°ΡΠ΅ΡΠΈΠ»ΠΎΠ².
Π‘ΠΈΠ»ΠΎΡΡ Π΄Π»Ρ Ρ
ΡΠ°Π½Π΅Π½ΠΈΡ Π·Π΅ΡΠ½Π° ΠΈ ΠΏΡΠΎΠ΄ΡΠΊΡΠΎΠ² Π΅Π³ΠΎ ΠΏΠ΅ΡΠ΅ΡΠ°Π±ΠΎΡΠΊΠΈ ΡΠ»Π΅Π΄ΡΠ΅Ρ ΠΏΡΠΎΠ΅ΠΊΡΠΈΡΠΎΠ²Π°ΡΡ Π² ΡΠΎΠΎΡΠ²Π΅ΡΡΡΠ²ΠΈΠΈ Ρ ΡΡΠ΅Π±ΠΎΠ²Π°Π½ΠΈΡΠΌΠΈ Π‘ΠΠΈΠ 2.10.05-85.
Π€ΠΎΡΠΌΡ, ΡΠ°Π·ΠΌΠ΅ΡΡ ΠΈ ΡΠ°ΡΠΏΠΎΠ»ΠΎΠΆΠ΅Π½ΠΈΡ ΡΠΈΠ»ΠΎΡΠΎΠ² Π² ΠΏΠ»Π°Π½Π΅ ΡΠ»Π΅Π΄ΡΠ΅Ρ ΠΏΡΠΈΠ½ΠΈΠΌΠ°ΡΡ Π² ΡΠΎΠΎΡΠ²Π΅ΡΡΡΠ²ΠΈΠΈ Ρ ΡΡΠ΅Π±ΠΎΠ²Π°Π½ΠΈΡΠΌΠΈ ΡΠ΅Ρ
Π½ΠΎΠ»ΠΎΠ³ΠΈΠΈ ΠΏΡΠΎΠΈΠ·Π²ΠΎΠ΄ΡΡΠ²Π°, ΡΠ½ΠΈΡΠΈΠΊΠ°ΡΠΈΠΈ, Π³ΡΡΠ½ΡΠΎΠ²ΡΠΌΠΈ ΠΈ ΡΠ΅ΠΌΠΏΠ΅ΡΠ°ΡΡΡΠ½ΡΠΌΠΈ ΡΡΠ»ΠΎΠ²ΠΈΡΠΌΠΈ, Π° ΡΠ°ΠΊΠΆΠ΅ ΠΈΡΡ
ΠΎΠ΄Ρ ΠΈΠ· ΡΠ΅Π·ΡΠ»ΡΡΠ°ΡΠΎΠ² ΡΠ΅Ρ
Π½ΠΈΠΊΠΎ-ΡΠΊΠΎΠ½ΠΎΠΌΠΈΡΠ΅ΡΠΊΠΈΡ
ΡΠΎΠΏΠΎΡΡΠ°Π²Π»Π΅Π½ΠΈΠΉ ΠΈ Ρ ΡΡΠ΅ΡΠΎΠΌ Π°ΡΡ
ΠΈΡΠ΅ΠΊΡΡΡΠ½ΠΎ-ΠΊΠΎΠΌΠΏΠΎΠ·ΠΈΡΠΈΠΎΠ½Π½ΡΡ
ΡΡΠ΅Π±ΠΎΠ²Π°Π½ΠΈΠΉ. ΠΠΎΠΏΡΡΠΊΠ°Π΅ΡΡΡ Π±Π»ΠΎΠΊΠΈΡΠΎΠ²ΠΊΠ° ΡΠΈΠ»ΠΎΡΠ½ΡΡ
ΠΊΠΎΡΠΏΡΡΠΎΠ² Ρ ΠΎΠ±ΡΠ»ΡΠΆΠΈΠ²Π°ΡΡΠΈΠΌΠΈ Π·Π΄Π°Π½ΠΈΡΠΌΠΈ II ΠΊΠ°ΡΠ΅Π³ΠΎΡΠΈΠΈ ΠΎΠ³Π½Π΅ΡΡΠΎΠΉΠΊΠΎΡΡΠΈ. ΠΡΠΈ ΡΡΠΎΠΌ Π΄ΠΎΠ»ΠΆΠ½Π° Π±ΡΡΡ ΡΡΡΠ΅Π½Π° ΡΠ°Π·Π½ΠΎΡΡΡ ΠΎΡΠ°Π΄ΠΎΠΊ ΡΡΠ½Π΄Π°ΠΌΠ΅Π½ΡΠΎΠ² ΡΠΈΠ»ΠΎΡΠΎΠ² ΠΈ ΠΏΡΠΈΠΌΡΠΊΠ°ΡΡΠΈΡ
Π·Π΄Π°Π½ΠΈΠΉ.
ΠΡΠΈ Π΄ΠΈΠ°ΠΌΠ΅ΡΡΠ΅ Π±ΠΎΠ»Π΅Π΅ 12 ΠΌ ΡΠΈΠ»ΠΎΡΡ ΡΠ»Π΅Π΄ΡΠ΅Ρ ΠΏΡΠΎΠ΅ΠΊΡΠΈΡΠΎΠ²Π°ΡΡ, ΠΊΠ°ΠΊ ΠΏΡΠ°Π²ΠΈΠ»ΠΎ, ΠΎΡΠ΄Π΅Π»ΡΠ½ΠΎ ΡΡΠΎΡΡΠΈΠΌΠΈ.
Π€ΠΎΡΠΌΠ° ΠΎΡΠ΄Π΅Π»ΡΠ½ΠΎΠ³ΠΎ ΡΠΈΠ»ΠΎΡΠ° Π² ΠΏΠ»Π°Π½Π΅ ΠΏΡΠΈΠ½ΠΈΠΌΠ°Π΅ΡΡΡ. ΠΊΠ°ΠΊ ΠΏΡΠ°Π²ΠΈΠ»ΠΎ, ΠΊΡΡΠ³Π»ΠΎΠΉ. ΠΠΎΠΏΡΡΠΊΠ°Π΅ΡΡΡ ΠΏΡΠΈ ΡΠΎΠΎΡΠ²Π΅ΡΡΡΠ²ΡΡΡΠ΅ΠΌ ΠΎΠ±ΠΎΡΠ½ΠΎΠ²Π°Π½ΠΈΠΈ ΠΏΡΠΈΠ½ΠΈΠΌΠ°ΡΡ ΡΠΈΠ»ΠΎΡΡ ΠΊΠ²Π°Π΄ΡΠ°ΡΠ½ΡΠΌΠΈ ΠΈ ΠΌΠ½ΠΎΠ³ΠΎΠ³ΡΠ°Π½Π½ΡΠΌΠΈ.
ΠΡΠΈ ΠΏΡΠΎΠ΅ΠΊΡΠΈΡΠΎΠ²Π°Π½ΠΈΠΈ ΡΠΈΠ»ΠΎΡΠ½ΡΡ
ΠΊΠΎΡΠΏΡΡΠΎΠ² ΡΠ»Π΅Π΄ΡΠ΅Ρ, ΠΊΠ°ΠΊ ΠΏΡΠ°Π²ΠΈΠ»ΠΎ, ΠΏΡΠΈΠ½ΠΈΠΌΠ°ΡΡ: ΡΠ΅ΡΠΊΠΈ ΡΠ°Π·Π±ΠΈΠ²ΠΎΡΠ½ΡΡ
ΠΎΡΠ΅ΠΉ, ΠΏΡΠΎΡ
ΠΎΠ΄ΡΡΠΈΡ
ΡΠ΅ΡΠ΅Π· ΡΠ΅Π½ΡΡΡ ΡΠ±Π»ΠΎΠΊΠΈΡΠΎΠ²Π°Π½Π½ΡΡ
ΡΠΈΠ»ΠΎΡΠΎΠ², 3Ρ
3, 6Ρ
6 ΠΈ 12Ρ
12 ΠΌ; Π½Π°ΡΡΠΆΠ½ΡΠ΅ Π΄ΠΈΠ°ΠΌΠ΅ΡΡΡ ΠΊΡΡΠ³Π»ΡΡ
ΡΠΈΠ»ΠΎΡΠΎΠ² β 3, 6, 12, 18 ΠΈ 24 ΠΌ; ΡΠ°Π·ΠΌΠ΅ΡΡ Π² ΠΎΡΡΡ
ΡΡΠ΅Π½ ΠΊΠ²Π°Π΄ΡΠ°ΡΠ½ΡΡ
ΡΠΈΠ»ΠΎΡΠΎΠ² β 3Ρ
3 ΠΌ; Π²ΡΡΠΎΡΡ ΡΡΠ΅Π½ ΡΠΈΠ»ΠΎΡΠΎΠ², Π° ΡΠ°ΠΊΠΆΠ΅ ΠΏΠΎΠ΄ΡΠΈΠ»ΠΎΡΠ½ΡΡ
ΠΈ Π½Π°Π΄ΡΠΈΠ»ΠΎΡΠ½ΡΡ
ΡΡΠ°ΠΆΠ΅ΠΉ β ΠΊΡΠ°ΡΠ½ΡΠΌΠΈ 0,6 ΠΌ.
ΠΠ΅ΡΠ°Π»Π»ΠΈΡΠ΅ΡΠΊΠΈΠ΅ ΡΠΈΠ»ΠΎΡΡ Π΄Π»ΠΈΠ½ΠΎΠΉ Π΄ΠΎ 48 ΠΌ Π΄ΠΎΠΏΡΡΠΊΠ°Π΅ΡΡΡ ΠΏΡΠΎΠ΅ΠΊΡΠΈΡΠΎΠ²Π°ΡΡ Π±Π΅Π· Π΄Π΅ΡΠΎΡΠΌΠ°ΡΠΈΠΎΠ½Π½ΡΡ
ΡΠ²ΠΎΠ². ΠΡΠΈ Π½Π΅ΡΠΊΠ°Π»ΡΠ½ΡΡ
Π³ΡΡΠ½ΡΠ°Ρ
ΠΎΡΠ½ΠΎΠ²Π°Π½ΠΈΡ ΠΎΡΠ½ΠΎΡΠ΅Π½ΠΈΠ΅ Π΄Π»ΠΈΠΌΡ ΡΠΈΠ»ΠΎΡΠ½ΠΎΠ³ΠΎ ΠΊΠΎΡΠΏΡΡΠ° ΠΊ Π΅Π³ΠΎ ΡΠΈΡΠΈΠ½Π΅ ΠΈ Π²ΡΡΠΎΡΠ΅ Π΄ΠΎΠ»ΠΆΠ½ΠΎ Π±ΡΡΡ Π½Π΅ Π±ΠΎΠ»Π΅Π΅ 2. ΠΡΠΈ ΠΎΠ΄Π½ΠΎΡΡΠ΄Π½ΠΎΠΌ ΡΠ°ΡΠΏΠΎΠ»ΠΎΠΆΠ΅Π½ΠΈΠΈ ΡΠΈΠ»ΠΎΡΠΎΠ² ΡΡΠΎ ΠΎΡΠ½ΠΎΡΠ΅Π½ΠΈΠ΅ Π΄ΠΎΠΏΡΡΠΊΠ°Π΅ΡΡΡ ΡΠ²Π΅Π»ΠΈΡΠΈΠ²Π°ΡΡ Π΄ΠΎ 3. ΠΠΎΠΏΡΡΠΊΠ°Π΅ΡΡΡ ΡΠ²Π΅Π»ΠΈΡΠ΅Π½ΠΈΠ΅ Π΄Π»ΠΈΠ½Ρ ΠΊΠΎΡΠΏΡΡΠ° ΠΈ ΡΠΊΠ°Π·Π°Π½Π½ΡΡ
ΠΎΡΠ½ΠΎΡΠ΅Π½ΠΈΠΉ ΠΏΡΠΈ ΡΠΎΠΎΡΠ²Π΅ΡΡΡΠ²ΡΡΡΠ΅ΠΌ ΠΎΠ±ΠΎΡΠ½ΠΎΠ²Π°Π½ΠΈΠΈ.
ΠΡΠΈ ΠΏΡΠΎΠ΅ΠΊΡΠΈΡΠΎΠ²Π°Π½ΠΈΠΈ ΠΌΠ½ΠΎΠ³ΠΎΡΡΠ΄Π½ΡΡ
ΡΠΈΠ»ΠΎΡΠ½ΡΡ
ΠΊΠΎΡΠΏΡΡΠΎΠ² Ρ ΠΊΡΡΠ³Π»ΡΠΌΠΈ Π² ΠΏΠ»Π°Π½Π΅ ΡΠΈΠ»ΠΎΡΠ°ΠΌΠΈ ΠΏΡΠΎΡΡΡΠ°Π½ΡΡΠ²ΠΎ ΠΌΠ΅ΠΆΠ΄Ρ Π½ΠΈΠΌΠΈ ΡΠ»Π΅Π΄ΡΠ΅Ρ ΠΈΡΠΏΠΎΠ»ΡΠ·ΠΎΠ²Π°ΡΡ Π΄Π»Ρ ΡΠ°Π·ΠΌΠ΅ΡΠ΅Π½ΠΈΡ Π»Π΅ΡΡΠ½ΠΈΡ, ΡΠ°Π·Π»ΠΈΡΠ½ΡΡ
ΠΊΠΎΠΌΠΌΡΠ½ΠΈΠΊΠ°ΡΠΈΠΉ, ΡΡΡΠ°Π½ΠΎΠ²ΠΊΠΈ ΡΠ΅Ρ
Π½ΠΎΠ»ΠΎΠ³ΠΈΡΠ΅ΡΠΊΠΎΠ³ΠΎ ΠΎΠ±ΠΎΡΡΠ΄ΠΎΠ²Π°Π½ΠΈΡ, Π½Π΅ ΡΡΠ΅Π±ΡΡΡΠ΅Π³ΠΎ ΠΎΠ±ΡΠ»ΡΠΆΠΈΠ²Π°Π½ΠΈΡ, Π° ΡΠ°ΠΊΠΆΠ΅ Π΄Π»Ρ Ρ
ΡΠ°Π½Π΅Π½ΠΈΡ Π½Π΅ΡΠ²ΡΠ·Π½ΡΡ
ΡΡΠΏΡΡΠΈΡ
ΠΌΠ°ΡΠ΅ΡΠΈΠ°Π»ΠΎΠ².
ΠΡΠΈ ΠΏΡΠΎΠ΅ΠΊΡΠΈΡΠΎΠ²Π°Π½ΠΈΠΈ ΡΠΈΠ»ΠΎΡΠ½ΡΡ
ΠΊΠΎΡΠΏΡΡΠΎΠ² ΡΠ»Π΅Π΄ΡΠ΅Ρ ΠΈΡΡ
ΠΎΠ΄Ρ ΠΈΠ· Π’Π 101-81*, ΡΠ΅Ρ
Π½ΠΈΠΊΠΎ-ΡΠΊΠΎΠ½ΠΎΠΌΠΈΡΠ΅ΡΠΊΠΎΠΉ ΡΠ΅Π»Π΅ΡΠΎΠΎΠ±ΡΠ°Π·Π½ΠΎΡΡΠΈ ΠΈ ΠΊΠΎΠ½ΠΊΡΠ΅ΡΠ½ΡΡ
ΡΡΠ»ΠΎΠ²ΠΈΠΉ ΡΡΡΠΎΠΈΡΠ΅Π»ΡΡΡΠ²Π° ΠΏΡΠ΅Π΄ΡΡΠΌΠ°ΡΡΠΈΠ²Π°ΡΡ ΠΏΡΠΈΠΌΠ΅Π½Π΅Π½ΠΈΠ΅ ΠΌΠΎΠ½ΠΎΠ»ΠΈΡΠ½ΠΎΠ³ΠΎ ΠΆΠ΅Π»Π΅Π·ΠΎΠ±Π΅ΡΠΎΠ½Π° (ΠΏΡΠΈ Π²ΠΎΠ·Π²Π΅Π΄Π΅Π½ΠΈΠΈ ΠΈΠ½Π΄ΡΡΡΡΠΈΠ°Π»ΡΠ½ΡΠΌΠΈ ΠΌΠ΅ΡΠΎΠ΄Π°ΠΌΠΈ) ΠΈΠ»ΠΈ ΡΠ±ΠΎΡΠ½ΠΎΠ³ΠΎ ΠΆΠ΅Π»Π΅Π·ΠΎΠ±Π΅ΡΠΎΠ½Π° (ΠΈΠ· ΡΠ½ΠΈΡΠΈΡΠΈΡΠΎΠ²Π°Π½Π½ΡΡ
ΠΈΠ·Π΄Π΅Π»ΠΈΠΉ). ΠΠΎΠΏΡΡΠΊΠ°Π΅ΡΡΡ ΠΏΡΠΈΠΌΠ΅Π½Π΅Π½ΠΈΠ΅ ΡΡΠ°Π»ΡΠ½ΡΡ
ΡΠΈΠ»ΠΎΡΠΎΠ² Π΄Π»Ρ ΡΡΠΏΡΡΠΈΡ
ΠΌΠ°ΡΠ΅ΡΠΈΠ°Π»ΠΎΠ², Ρ
ΡΠ°Π½Π΅Π½ΠΈΠ΅ ΠΊΠΎΡΠΎΡΡΡ
ΠΈΠ² Π΄ΠΎΠΏΡΡΠΊΠ°Π΅ΡΡΡ Π² ΠΆΠ΅Π»Π΅Π·ΠΎΠ±Π΅ΡΠΎΠ½Π½ΡΡ
Π΅ΠΌΠΊΠΎΡΡΡΡ
, Π° ΡΠ°ΠΊΠΆΠ΅ ΡΡΠ°Π»ΡΠ½ΡΡ
ΠΈΠ½Π²Π΅Π½ΡΠ°ΡΠ½ΡΡ
ΠΈ ΠΎΠΏΠ΅ΡΠ°ΡΠΈΠ²Π½ΡΡ
ΡΠΈΠ»ΠΎΡΠΎΠ².
ΠΡΠΈ ΠΈΠ·Π³ΠΎΡΠΎΠ²Π»Π΅Π½ΠΈΠΈ ΡΡΠ΅Π½ΠΎΠΊ ΡΠΈΠ»ΠΎΡΠΎΠ² ΠΈΠ· ΡΡΠ°Π»ΠΈ ΡΠ»Π΅Π΄ΡΠ΅Ρ ΠΏΡΠ΅Π΄ΡΡΠΌΠ°ΡΡΠΈΠ²Π°ΡΡ ΠΈΠ½Π΄ΡΡΡΡΠΈΠ°Π»ΡΠ½ΡΠ΅ ΠΌΠ΅ΡΠΎΠ΄Ρ ΠΈΡ
ΠΈΠ·Π³ΠΎΡΠΎΠ²Π»Π΅Π½ΠΈΡ ΠΈ ΠΌΠΎΠ½ΡΠ°ΠΆΠ° ΠΏΡΡΠ΅ΠΌ ΠΏΡΠΈΠΌΠ΅Π½Π΅Π½ΠΈΡ; Π»ΠΈΡΡΠΎΠ² ΠΈ Π»Π΅Π½Ρ Π±ΠΎΠ»ΡΡΠΈΡ
ΡΠ°Π·ΠΌΠ΅ΡΠΎΠ²; ΡΠΏΠΎΡΠΎΠ±Π° ΡΡΠ»ΠΎΠ½ΠΈΡΠΎΠ²Π°Π½ΠΈΡ; ΠΈΠ·Π³ΠΎΡΠΎΠ²Π»Π΅Π½ΠΈΡ Π·Π°Π³ΠΎΡΠΎΠ²ΠΎΠΊ Π² Π²ΠΈΠ΄Π΅ βΡΠΊΠΎΡΠ»ΡΠΏΒ» β ΠΏΠΎΠ»ΠΈΡΡΠΎΠ²Π°Ρ ΡΠ±ΠΎΡΠΊΠ°; Π°Π²ΡΠΎΠΌΠ°ΡΠΈΡΠ΅ΡΠΊΠΎΠΉ ΡΠ²Π°ΡΠΊΠΈ Ρ ΠΌΠΈΠ½ΠΈΠΌΠ°Π»ΡΠ½ΡΠΌ ΠΊΠΎΠ»ΠΈΡΠ΅ΡΡΠ²ΠΎΠΌ ΡΠ²Π°ΡΠ½ΡΡ
ΡΠ²ΠΎΠ², Π²ΡΠΏΠΎΠ»Π½ΡΠ΅ΠΌΡΡ
Π½Π° ΠΌΠΎΠ½ΡΠ°ΠΆΠ΅, Π° ΡΠ°ΠΊΠΆΠ΅ Π΄ΡΡΠ³ΠΈΡ
ΠΏΠ΅ΡΠ΅Π΄ΠΎΠ²ΡΡ
ΠΌΠ΅ΡΠΎΠ΄ΠΎΠ².
Π‘Π±ΠΎΡΠ½ΡΠ΅ ΠΆΠ΅Π»Π΅Π·ΠΎΠ±Π΅ΡΠΎΠ½Π½ΡΠ΅ ΡΡΠ΅Π½Ρ ΡΠΈΠ»ΠΎΡΠΎΠ² ΡΠ»Π΅Π΄ΡΠ΅Ρ ΠΈΠ·Π³ΠΎΡΠ°Π²Π»ΠΈΠ²Π°ΡΡ Π΄Π»Ρ ΡΠΈΠ»ΠΎΡΠΎΠ² ΠΊΡΡΠ³Π»ΡΡ
Π² ΠΏΠ»Π°Π½Π΅ Π΄ΠΈΠ°ΠΌΠ΅ΡΡΠΎΠΌ 3 ΠΌ ΠΈΠ· ΠΎΠ±ΡΠ΅ΠΌΠ½ΡΡ
Π±Π»ΠΎΠΊΠΎΠ². ΠΡΠΈ Π±ΠΎΠ»ΡΡΠΈΡ
ΡΠ°Π·ΠΌΠ΅ΡΠ°Ρ
β ΠΈΠ· ΠΎΡΠ΄Π΅Π»ΡΠ½ΡΡ
ΡΠ»Π΅ΠΌΠ΅Π½ΡΠΎΠ², ΡΠΊΡΡΠΏΠ½ΡΠ΅ΠΌΡΡ
ΠΏΠ΅ΡΠ΅Π΄ ΠΌΠΎΠ½ΡΠ°ΠΆΠΎΠΌ Π² ΡΠ°ΡΠ³ΠΈ ΠΈΠ»ΠΈ Π±Π»ΠΎΠΊΠΈ, ΠΈΠ»ΠΈ ΠΈΠ· ΡΠ»Π΅ΠΌΠ΅Π½ΡΠΎΠ², ΠΌΠΎΠ½ΡΠΈΡΡΠ΅ΠΌΡΡ
Π±Π΅Π· ΠΏΡΠ΅Π΄Π²Π°ΡΠΈΡΠ΅Π»ΡΠ½ΠΎΠ³ΠΎ ΡΠΊΡΡΠΏΠ½Π΅Π½ΠΈΡ.
ΠΠ½ΡΡΡΠ΅Π½Π½ΠΈΠ΅ ΠΏΠΎΠ²Π΅ΡΡ
Π½ΠΎΡΡΠΈ ΡΡΠ΅Π½ ΠΈ Π΄Π½ΠΈΡΠ° ΡΠΈΠ»ΠΎΡΠΎΠ² Π½Π΅ Π΄ΠΎΠ»ΠΆΠ½Ρ ΠΈΠΌΠ΅ΡΡ Π²ΡΡΡΡΠΏΠ°ΡΡΠΈΡ
Π³ΠΎΡΠΈΠ·ΠΎΠ½ΡΠ°Π»ΡΠ½ΡΡ
ΡΠ΅Π±Π΅Ρ ΠΈ Π²ΠΏΠ°Π΄ΠΈΠ½.
ΠΠ½ΠΈΡΠ° ΡΠΈΠ»ΠΎΡΠΎΠ² Π² Π·Π°Π²ΠΈΡΠΈΠΌΠΎΡΡΠΈ ΠΎΡ Π΄ΠΈΠ°ΠΌΠ΅ΡΡΠ° ΡΠΈΠ»ΠΎΡΠ° ΠΈ Ρ
ΡΠ°Π½ΠΈΠΌΠΎΠ³ΠΎ ΠΌΠ°ΡΠ΅ΡΠΈΠ°Π»Π° ΡΠ»Π΅Π΄ΡΠ΅Ρ ΠΏΡΠΎΠ΅ΠΊΡΠΈΡΠΎΠ²Π°ΡΡ Π² Π²ΠΈΠ΄Π΅ ΠΆΠ΅Π»Π΅Π·ΠΎΠ±Π΅ΡΠΎΠ½Π½ΠΎΠΉ ΠΏΠ»ΠΈΡΡ ΡΠΎ ΡΡΠ°Π»ΡΠ½ΠΎΠΉ ΠΏΠΎΠ»ΡΠ²ΠΎΡΠΎΠ½ΠΊΠΎΠΉ ΠΈ Π±Π΅ΡΠΎΠ½Π½ΠΎΠΉ Π·Π°Π±ΡΡΠΊΠΎΠΉ ΠΈΠ»ΠΈ Π² Π²ΠΈΠ΄Π΅ ΠΆΠ΅Π»Π΅Π·ΠΎΠ±Π΅ΡΠΎΠ½Π½ΠΎΠΉ ΠΈΠ»ΠΈ ΡΡΠ°Π»ΡΠ½ΠΎΠΉ Π²ΠΎΡΠΎΠ½ΠΊΠΈ Π½Π° Π²ΡΠ΅ ΡΠ΅ΡΠ΅Π½ΠΈΠ΅ ΡΠΈΠ»ΠΎΡΠ°.
Π‘ΡΠ΅Π½Ρ ΠΈ Π΄Π½ΠΈΡΠ° ΡΠΈΠ»ΠΎΡΠΎΠ² Π΄Π»Ρ Π°Π±ΡΠ°Π·ΠΈΠ²Π½ΡΡ
ΠΈ ΠΊΡΡΠΊΠΎΠ²ΡΡ
ΠΌΠ°ΡΠ΅ΡΠΈΠ°Π»ΠΎΠ² ΡΠ»Π΅Π΄ΡΠ΅Ρ Π·Π°ΡΠΈΡΠ°ΡΡ ΠΎΡ ΠΈΡΡΠΈΡΠ°Π½ΠΈΡ ΠΈ ΡΠ°Π·ΡΡΡΠ΅Π½ΠΈΡ ΠΏΡΠΈ Π·Π°Π³ΡΡΠ·ΠΊΠ΅. ΠΠ°ΡΠ΅ΡΠΈΠ°Π» Π΄Π»Ρ Π·Π°ΡΠΈΡΡ ΡΡΠ΅Π½ ΠΈ Π΄Π½ΠΈΡΠ° ΡΠΈΠ»ΠΎΡΠΎΠ² ΡΠ»Π΅Π΄ΡΠ΅Ρ Π²ΡΠ±ΠΈΡΠ°ΡΡ Π² Π·Π°Π²ΠΈΡΠΈΠΌΠΎΡΡΠΈ ΠΎΡ ΡΠΈΠ·ΠΈΠΊΠΎ-ΠΌΠ΅Ρ
Π°Π½ΠΈΡΠ΅ΡΠΊΠΈΡ
ΡΠ²ΠΎΠΉΡΡΠ² Ρ
ΡΠ°Π½ΠΈΠΌΠΎΠ³ΠΎ ΠΌΠ°ΡΠ΅ΡΠΈΠ°Π»Π°. ΠΡΠΈ ΠΏΡΠΎΠ΅ΠΊΡΠΈΡΠΎΠ²Π°Π½ΠΈΠΈ ΡΠΈΠ»ΠΎΡΠΎΠ² Π½Π΅ΠΎΠ±Ρ
ΠΎΠ΄ΠΈΠΌΠΎ ΡΡΠΈΡΡΠ²Π°ΡΡ ΡΠ°ΠΊΠΆΠ΅ Ρ
ΠΈΠΌΠΈΡΠ΅ΡΠΊΡΡ Π°Π³ΡΠ΅ΡΡΠΈΡ Ρ
ΡΠ°Π½ΠΈΠΌΠΎΠ³ΠΎ ΠΌΠ°ΡΠ΅ΡΠΈΠ°Π»Π° ΠΈ Π²ΠΎΠ·Π΄ΡΡΠ½ΠΎΠΉ ΡΡΠ΅Π΄Ρ.
ΠΠ»Ρ ΡΠΈΠ»ΠΎΡΠΎΠ² ΡΠΎ ΡΡΠ°Π»ΡΠ½ΡΠΌΠΈ ΡΡΠ΅Π½Π°ΠΌΠΈ ΠΏΠ΅ΡΠ΅ΠΊΡΡΡΠΈΠ΅ Π΄ΠΎΠΏΡΡΠΊΠ°Π΅ΡΡΡ ΠΏΡΠΎΠ΅ΠΊΡΠΈΡΠΎΠ²Π°ΡΡ ΠΈΠ· ΡΡΠ°Π»ΠΈ.
ΠΠΎΠΊΡΡΡΠΈΡ ΠΎΡΠ΄Π΅Π»ΡΠ½ΠΎ ΡΡΠΎΡΡΠΈΡ
ΠΊΡΡΠ³Π»ΡΡ
ΡΠΈΠ»ΠΎΡΠΎΠ² ΠΏΡΠΈ ΠΎΡΡΡΡΡΡΠ²ΠΈΠΈ Π½Π°Π΄ΡΠΈΠ»ΠΎΡΠ½ΠΎΠ³ΠΎ ΠΏΠΎΠΌΠ΅ΡΠ΅Π½ΠΈΡ, Π° ΡΠ°ΠΊΠΆΠ΅ ΡΠΈΠ»ΠΎΡΠΎΠ² Π΄ΠΈΠ°ΠΌΠ΅ΡΡΠΎΠΌ Π±ΠΎΠ»Π΅Π΅ 12 ΠΌ Π΄ΠΎΠΏΡΡΠΊΠ°Π΅ΡΡΡ ΠΈΠ·Π³ΠΎΡΠ°Π²Π»ΠΈΠ²Π°ΡΡ Π² Π²ΠΈΠ΄Π΅ ΠΎΠ±ΠΎΠ»ΠΎΡΠ΅ΠΊ.
ΠΠ°Π΄ΡΠΈΠ»ΠΎΡΠ½ΡΠ΅ ΠΏΠΎΠΌΠ΅ΡΠ΅Π½ΠΈΡ ΠΈ ΠΊΠΎΠ½Π²Π΅ΠΉΠ΅ΡΠ½ΡΠ΅ Π³Π°Π»Π΅ΡΠ΅ΠΈ ΡΠ»Π΅Π΄ΡΠ΅Ρ ΠΈΠ·Π³ΠΎΡΠ°Π²Π»ΠΈΠ²Π°ΡΡ, ΠΏΡΠΈΠΌΠ΅Π½ΡΡ ΠΎΠ±Π»Π΅Π³ΡΠ΅Π½Π½ΡΠ΅ ΡΡΠ΅Π½ΠΎΠ²ΡΠ΅ ΠΎΠ³ΡΠ°ΠΆΠ΄Π΅Π½ΠΈΡ ΠΈΠ· Π½Π΅ΡΠ³ΠΎΡΠ°Π΅ΠΌΡΡ
ΠΌΠ°ΡΠ΅ΡΠΈΠ°Π»ΠΎΠ². ΠΠΎΠΏΡΡΠΊΠ°Π΅ΡΡΡ ΡΠ°ΠΊΠΆΠ΅ ΠΏΡΠΈΠΌΠ΅Π½Π΅Π½ΠΈΠ΅ ΡΠ±ΠΎΡΠ½ΡΡ
ΠΌΠ΅ΡΠ°Π»Π»ΠΈΡΠ΅ΡΠΊΠΈΡ
ΠΊΠΎΠ½ΡΡΡΡΠΊΡΠΈΠΉ.
ΠΠ·Π³ΠΎΡΠΎΠ²Π»Π΅Π½ΠΈΠ΅ ΡΠΎΠ΅Π΄ΠΈΠ½ΠΈΡΠ΅Π»ΡΠ½ΡΡ
Π³Π°Π»Π΅ΡΠ΅ΠΉ ΠΌΠ΅ΠΆΠ΄Ρ ΡΠΈΠ»ΠΎΡΠ°ΠΌΠΈ ΠΈΠ»ΠΈ ΠΌΠ΅ΠΆΠ΄Ρ ΡΠΈΠ»ΠΎΡΠ½ΡΠΌΠΈ ΠΊΠΎΡΠΏΡΡΠ°ΠΌΠΈ ΡΠ»Π΅Π΄ΡΠ΅Ρ ΡΡΠΈΡΡΠ²Π°ΡΡ ΠΎΡΠ½ΠΎΡΠΈΡΠ΅Π»ΡΠ½ΡΠ΅ ΡΠΌΠ΅ΡΠ΅Π½ΠΈΡ ΡΠΈΠ»ΠΎΡΠΎΠ² ΠΈΠ»ΠΈ ΡΠΈΠ»ΠΎΡΠ½ΡΡ
ΠΊΠΎΡΠΏΡΡΠΎΠ², Π²ΡΠ·ΡΠ²Π°Π΅ΠΌΡΠ΅ Π½Π΅ΡΠ°Π²Π½ΠΎΠΌΠ΅ΡΠ½ΡΠΌΠΈ ΠΎΡΠ°Π΄ΠΊΠ°ΠΌΠΈ ΠΈ ΠΊΡΠ΅Π½Π°ΠΌΠΈ.
ΠΠΎΠ»ΠΎΠ½Π½Ρ ΠΏΠΎΠ΄ΡΠΈΠ»ΠΎΡΠ½ΠΎΠ³ΠΎ ΡΡΠ°ΠΆΠ° Π½Π°Π΄Π»Π΅ΠΆΠΈΡ ΠΏΡΠΎΠ΅ΠΊΡΠΈΡΠΎΠ²Π°ΡΡ ΡΠ±ΠΎΡΠ½ΡΠΌΠΈ ΡΡΠ°Π»ΡΠ½ΡΠΌΠΈ.
Π€ΡΠ½Π΄Π°ΠΌΠ΅Π½ΡΡ ΡΠΈΠ»ΠΎΡΠΎΠ² ΠΈ ΡΠΈΠ»ΠΎΡΠ½ΡΡ
ΠΊΠΎΡΠΏΡΡΠΎΠ² ΡΠ»Π΅Π΄ΡΠ΅Ρ ΠΏΡΠΎΠ΅ΠΊΡΠΈΡΠΎΠ²Π°ΡΡ Π² Π²ΠΈΠ΄Π΅ ΠΌΠΎΠ½ΠΎΠ»ΠΈΡΠ½ΡΡ
ΠΆΠ΅Π»Π΅Π·ΠΎΠ±Π΅ΡΠΎΠ½Π½ΡΡ
Π±Π΅Π·Π±Π°Π»ΠΎΡΠ½ΡΡ
ΠΏΠ»ΠΈΡ. ΠΠ° ΡΠΊΠ°Π»ΡΠ½ΡΡ
ΠΈ ΠΊΡΡΠΏΠ½ΠΎΠΎΠ±Π»ΠΎΠΌΠΎΡΠ½ΡΡ
Π³ΡΡΠ½ΡΠ°Ρ
Π΄ΠΎΠΏΡΡΠΊΠ°Π΅ΡΡΡ ΠΏΡΠΈΠ½ΠΈΠΌΠ°ΡΡ ΡΡΠ½Π΄Π°ΠΌΠ΅Π½ΡΡ ΠΎΡΠ΄Π΅Π»ΡΠ½ΠΎ ΡΡΠΎΡΡΠΈΠ΅, Π»Π΅Π½ΡΠΎΡΠ½ΡΠ΅ ΠΈΠ»ΠΈ ΠΊΠΎΠ»ΡΡΠ΅Π²ΡΠ΅, ΠΌΠΎΠ½ΠΎΠ»ΠΈΡΠ½ΡΠ΅ ΠΈΠ»ΠΈ ΡΠ±ΠΎΡΠ½ΡΠ΅. Π‘Π²Π°ΠΉΠ½ΡΠ΅ ΡΡΠ½Π΄Π°ΠΌΠ΅Π½ΡΡ ΡΠ»Π΅Π΄ΡΠ΅Ρ ΠΏΡΠ΅Π΄ΡΡΠΌΠ°ΡΡΠΈΠ²Π°ΡΡ, Π΅ΡΠ»ΠΈ ΡΠ°ΡΡΠ΅ΡΠ½ΡΠ΅ Π΄Π΅ΡΠΎΡΠΌΠ°ΡΠΈΠΈ Π΅ΡΡΠ΅ΡΡΠ²Π΅Π½Π½ΠΎΠ³ΠΎ ΠΎΡΠ½ΠΎΠ²Π°Π½ΠΈΡ ΠΏΡΠ΅Π²ΡΡΠ°ΡΡ ΠΏΡΠ΅Π΄Π΅Π»ΡΠ½ΡΠ΅ ΠΈΠ»ΠΈ Π½Π΅ ΠΎΠ±Π΅ΡΠΏΠ΅ΡΠΈΠ²Π°Π΅ΡΡΡ Π΅Π³ΠΎ ΡΡΡΠΎΠΉΡΠΈΠ²ΠΎΡΡΡ, Π° ΡΠ°ΠΊΠΆΠ΅ ΠΏΡΠΈ Π½Π°Π»ΠΈΡΠΈΠΈ ΠΏΡΠΎΡΠ°Π΄ΠΎΡΠ½ΡΡ
Π³ΡΡΠ½ΡΠΎΠ² ΠΈ Π² Π΄ΡΡΠ³ΠΈΡ
ΡΠ»ΡΡΠ°ΡΡ
ΠΏΡΠΈ ΡΠΎΠΎΡΠ²Π΅ΡΡΡΠ²ΡΡΡΠ΅ΠΌ ΡΠ΅Ρ
Π½ΠΈΠΊΠΎ-ΡΠΊΠΎΠ½ΠΎΠΌΠΈΡΠ΅ΡΠΊΠΎΠΌ ΠΎΠ±ΠΎΡΠ½ΠΎΠ²Π°Π½ΠΈΠΈ.
ΠΠΎΠ½ΡΡΡΡΠΊΡΠΈΠΈ ΡΠΈΠ»ΠΎΡΠΎΠ² Π½Π΅ΠΎΠ±Ρ
ΠΎΠ΄ΠΈΠΌΠΎ ΡΠ°ΡΡΡΠΈΡΡΠ²Π°ΡΡ Π½Π° Π½Π°Π³ΡΡΠ·ΠΊΠΈ ΠΈ Π²ΠΎΠ·Π΄Π΅ΠΉΡΡΠ²ΠΈΡ Π² ΡΠΎΠΎΡΠ²Π΅ΡΡΡΠ²ΠΈΠΈ Ρ ΡΡΠ΅Π±ΠΎΠ²Π°Π½ΠΈΡΠΌΠΈ Π‘ΠΠΈΠ 2.01.07-85. ΠΡΠΈ ΡΠ°ΡΡΠ΅ΡΠ΅ ΡΠΈΠ»ΠΎΡΠΎΠ² Π΄ΠΎΠ»ΠΆΠ½Ρ Π±ΡΡΡ ΡΠ°ΠΊΠΆΠ΅ ΡΡΡΠ΅Π½Ρ Π½Π°Π³ΡΡΠ·ΠΊΠΈ ΠΈ Π²ΠΎΠ·Π΄Π΅ΠΉΡΡΠ²ΠΈΡ: Π²ΡΠ΅ΠΌΠ΅Π½Π½ΡΠ΅ Π΄Π»ΠΈΡΠ΅Π»ΡΠ½ΡΠ΅ β ΠΎΡ Π²Π΅ΡΠ° ΡΡΠΏΡΡΠΈΡ
ΠΌΠ°ΡΠ΅ΡΠΈΠ°Π»ΠΎΠ², ΡΠ°ΡΡΠΈ Π³ΠΎΡΠΈΠ·ΠΎΠ½ΡΠ°Π»ΡΠ½ΠΎΠ³ΠΎ Π΄Π°Π²Π»Π΅Π½ΠΈΡ ΠΈ ΡΡΠ΅Π½ΠΈΡ ΡΡΠΏΡΡΠΈΡ
ΠΌΠ°ΡΠ΅ΡΠΈΠ°Π»ΠΎΠ² ΠΎ ΡΡΠ΅Π½Ρ ΡΠΈΠ»ΠΎΡΠΎΠ², Π²Π΅ΡΠ° ΡΠ΅Ρ
Π½ΠΎΠ»ΠΎΠ³ΠΈΡΠ΅ΡΠΊΠΎΠ³ΠΎ ΠΎΠ±ΠΎΡΡΠ΄ΠΎΠ²Π°Π½ΠΈΡ; ΠΊΡΠ°ΡΠΊΠΎΠ²ΡΠ΅ΠΌΠ΅Π½Π½ΡΠ΅ β Π²ΠΎΠ·Π½ΠΈΠΊΠ°ΡΡΠΈΠ΅ ΠΏΡΠΈ ΠΈΠ·Π³ΠΎΡΠΎΠ²Π»Π΅Π½ΠΈΠΈ. ΠΏΠ΅ΡΠ΅Π²ΠΎΠ·ΠΊΠ΅ ΠΈ ΠΌΠΎΠ½ΡΠ°ΠΆΠ° ΡΠ±ΠΎΡΠ½ΡΡ
ΠΌΠ΅ΡΠ°Π»Π»ΠΈΡΠ΅ΡΠΊΠΈΡ
ΠΊΠΎΠ½ΡΡΡΡΠΊΡΠΈΠΉ,
Π‘ΡΠ΅Π½Ρ ΠΊΠ²Π°Π΄ΡΠ°ΡΠ½ΡΡ
ΠΈ ΠΌΠ½ΠΎΠ³ΠΎΠ³ΡΠ°Π½Π½ΡΡ
ΡΠΈΠ»ΠΎΡΠΎΠ² ΡΠ»Π΅Π΄ΡΠ΅Ρ ΡΠ°ΡΡΡΠΈΡΡΠ²Π°ΡΡ Π½Π° Π²Π½Π΅ΡΠ΅Π½ΡΡΠ΅Π½Π½ΠΎΠ΅ ΡΠ°ΡΡΡΠΆΠ΅Π½ΠΈΠ΅. ΠΠΎΡΡΡΠΈΡΠΈΠ΅Π½ΡΡ ΡΡΠ»ΠΎΠ²ΠΈΠΉ ΡΠ°Π±ΠΎΡΡ ΠΏΡΠΈ ΡΠ°ΡΡΠ΅ΡΠ° ΡΡΠ°Π½ ΡΠΈΠ»ΠΎΡΠΎΠ² ΡΠ»Π΅Π΄ΡΠ΅Ρ ΠΎΠΏΡΠ΅Π΄Π΅Π»ΡΡΡ Π² ΡΠΎΠΎΡΠ²Π΅ΡΡΡΠ²ΠΈΠΈ Ρ ΡΡΠ΅Π±ΠΎΠ²Π°Π½ΠΈΡΠΌΠΈ Π‘ΠΠΈΠ 2.03.01-84, ΠΏΡΠΈΠ½ΠΈΠΌΠ°Ρ Π΄Π»Ρ ΡΡΠ΅Π½ ΡΠΈΠ»ΠΎΡΠΎΠ², Π²ΠΎΠ·Π²ΠΎΠ΄ΠΈΠΌΡΡ
Π² ΡΠΊΠΎΠ»ΡΠ·ΡΡΠ΅ΠΉ ΠΎΠΏΠ°Π»ΡΠ±ΠΊΠ°
Π‘ΡΠ΅Π½Ρ ΡΡΠ°Π»ΡΠ½ΡΡ
ΠΊΡΡΠ³Π»ΡΡ
ΡΠΈΠ»ΠΎΡΠΎΠ² ΡΠ°ΡΡΡΠΈΡΡΠ²Π°ΡΡΡΡ Π½Π° ΡΠ΅ ΠΆΠ΅ ΡΠΎΡΠ΅ΡΠ°Π½ΠΈΡ Π½Π°Π³ΡΡΠ·ΠΎΠΊ, ΡΡΠΎ ΠΈ ΡΡΠ΅Π½Ρ ΠΆΠ΅Π»Π΅Π·ΠΎΠ±Π΅ΡΠΎΠ½Π½ΡΡ
ΠΊΡΡΠ³Π»ΡΡ
ΡΠΈΠ»ΠΎΡΠΎΠ². ΠΠΎΠΏΠΎΠ»Π½ΠΈΡΠ΅Π»ΡΠ½ΠΎ ΡΡΠ΅Π½Ρ ΡΡΠ°Π»ΡΠ½ΡΡ
ΡΠΈΠ»ΠΎΡΠΎΠ² Π΄ΠΎΠ»ΠΆΠ½Ρ Π±ΡΡΡ ΠΏΡΠΎΠ²Π΅ΡΠ΅Π½Ρ Π½Π° ΡΡΡΠΎΠΉΡΠΈΠ²ΠΎΡΡΡ Ρ ΠΊΠΎΡΡΡΠΈΡΠΈΠ΅Π½ΡΠΎΠΌ ΡΡΠ»ΠΎΠ²ΠΈΠΉ ΡΠ°Π±ΠΎΡΡ, ΡΠ°Π²Π½ΡΠΌ 1. ΠΠ° Π²ΡΠ½ΠΎΡΠ»ΠΈΠ²ΠΎΡΡΡ ΡΡΠ°Π»ΡΠ½ΡΠ΅ ΡΡΠ΅Π½Ρ Π΄ΠΎΠΏΡΡΠΊΠ°Π΅ΡΡΡ Π½Π΅ ΡΠ°ΡΡΡΠΈΡΡΠ²Π°ΡΡ.
ΠΠ»Ρ ΡΡΠ°Π»ΡΠ½ΡΡ
ΠΌΠ΅ΡΠ°Π»Π»ΠΈΡΠ΅ΡΠΊΠΈΡ
ΡΠΈΠ»ΠΎΡΠΎΠ² Π΄Π»Ρ ΡΠ΅ΠΌΠ΅Π½ΡΠ° ΡΠ»Π΅Π΄ΡΠ΅Ρ ΡΡΠΈΡΡΠ²Π°ΡΡ Π²ΠΎΠ·Π΄Π΅ΠΉΡΡΠ²ΠΈΡ ΠΎΡ ΡΡΡΠΎΡΠ½ΠΎΠ³ΠΎ ΠΈΠ·ΠΌΠ΅Π½Π΅Π½ΠΈΡ ΡΠ΅ΠΌΠΏΠ΅ΡΠ°ΡΡΡΡ Π½Π°ΡΡΠΆΠ½ΠΎΠ³ΠΎ Π²ΠΎΠ·Π΄ΡΡ
Π° Π² Π²ΠΈΠ΄Π΅ Π΄ΠΎΠΏΠΎΠ»Π½ΠΈΡΠ΅Π»ΡΠ½ΠΎΠ³ΠΎ Π³ΠΎΡΠΈΠ·ΠΎΠ½ΡΠ°Π»ΡΠ½ΠΎΠ³ΠΎ Π½ΠΎΡΠΌΠ°ΡΠΈΠ²Π½ΠΎΠ³ΠΎ Π΄Π°Π²Π»Π΅Π½ΠΈΡ ΡΡΠΏΡΡΠ΅Π³ΠΎ ΠΌΠ°ΡΠ΅ΡΠΈΠ°Π»Π°, ΡΡΠΈΡΠ°Ρ Π΅Π³ΠΎ ΡΠ°Π²Π½ΠΎΠΌΠ΅ΡΠ½ΠΎ ΡΠ°ΡΠΏΡΠ΅Π΄Π΅Π»Π΅Π½Π½ΡΠΌ ΠΏΠΎ ΠΏΠ΅ΡΠΈΠΌΠ΅ΡΡΡ ΠΈ ΠΏΠΎ Π²ΡΡΠΎΡΠ΅.
ΠΠΎΠ»ΠΎΠ½Π½Ρ ΠΏΠΎΠ΄ΡΠΈΠ»ΠΎΡΠ½ΠΎΠ³ΠΎ ΡΡΠ°ΠΆΠ° ΡΠ»Π΅Π΄ΡΠ΅Ρ ΡΠ°ΡΡΡΠΈΡΡΠ²Π°ΡΡ ΠΏΠΎ ΡΡ
Π΅ΠΌΠ΅ ΡΡΠΎΠ΅ΠΊ, Π·Π°Π΄Π΅Π»Π°Π½Π½ΡΡ
Π² ΡΡΠ½Π΄Π°ΠΌΠ΅Π½Ρ, Ρ ΡΡΠ΅ΡΠΎΠΌ ΡΠ°ΠΊΡΠΈΡΠ΅ΡΠΊΠΎΠ³ΠΎ Π·Π°ΡΠ΅ΠΌΠ»Π΅Π½ΠΈΡ Π² Π΄Π½ΠΈΡΠ΅ ΡΠΈΠ»ΠΎΡΠ°. ΠΠ°ΡΡΠΆΠ½ΡΠ΅ ΡΡΠ°Π»ΡΠ½ΡΠ΅ ΠΌΠ°ΡΡΠ΅Π²ΡΠ΅ Π»Π΅ΡΡΠ½ΠΈΡΡ, ΠΈΡΠΏΠΎΠ»ΡΠ·ΡΠ΅ΠΌΡΠ΅ Π΄Π»Ρ ΡΠ²Π°ΠΊΡΠ°ΡΠΈΠΈ Π»ΡΠ΄Π΅ΠΉ, ΡΠ»Π΅Π΄ΡΠ΅Ρ ΠΏΡΠΎΠ΅ΠΊΡΠΈΡΠΎΠ²Π°ΡΡ, ΠΊΠ°ΠΊ ΠΏΡΠ°Π²ΠΈΠ»ΠΎ, ΡΠΈΡΠΈΠ½ΠΎΠΉ Π½Π΅ ΠΌΠ΅Π½Π΅Π΅ 0,7 ΠΌ Ρ ΡΠΊΠ»ΠΎΠ½ΠΎΠΌ ΠΌΠ°ΡΡΠ΅ΠΉ Π½Π΅ Π±ΠΎΠ»Π΅Π΅ 1:1, ΠΎΠ³ΡΠ°ΠΆΠ΄Π΅Π½ΠΈΠ΅ΠΌ Π²ΡΡΠΎΡΠΎΠΉ 1,0 ΠΌΠΈ ΠΏΠ»ΠΎΡΠ°Π΄ΠΊΠ°ΠΌΠΈ, ΡΠ°ΡΠΏΠΎΠ»ΠΎΠΆΠ΅Π½Π½ΡΠΌΠΈ ΠΏΠΎ Π²ΡΡΠΎΡΠ΅ Π½Π° ΡΠ°ΡΡΡΠΎΡΠ½ΠΈΠΈ Π½Π° Π±ΠΎΠ»Π΅Π΅ 8 ΠΌ. 10.57.
ΠΡΠΈ Ρ
ΡΠ°Π½Π΅Π½ΠΈΠΈ Π² ΡΠΈΠ»ΠΎΡΠ°Ρ
Π½Π΅ΡΠ³ΠΎΡΠ°Π΅ΠΌΡΡ
ΠΌΠ°ΡΠ΅ΡΠΈΠ°Π»ΠΎΠ² Π΄ΠΎΠΏΡΡΠΊΠ°Π΅ΡΡΡ ΠΏΡΠ΅Π΄ΡΡΠΌΠ°ΡΡΠΈΠ²Π°ΡΡ ΠΎΠ΄ΠΈΠ½ ΡΠ²Π°ΠΊΡΠ°ΡΠΈΠΎΠ½Π½ΡΠΉ Π²ΡΡ
ΠΎΠ΄ (Π±Π΅Π· ΡΡΡΡΠΎΠΉΡΡΠ²Π° Π²ΡΠΎΡΠΎΠ³ΠΎ) Π½Π° Π½Π°ΡΡΠΆΠ½ΡΡ ΠΎΡΠΊΡΡΡΡΡ ΡΡΠ°Π»ΡΠ½ΡΡ Π»Π΅ΡΡΠ½ΠΈΡΡ Ρ ΡΠΊΠ»ΠΎΠ½ΠΎΠΌ 1:1.
Π Π°ΡΡΡΠΎΡΠ½ΠΈΠ΅ ΠΎΡ Π½Π°ΠΈΠ±ΠΎΠ»Π΅Π΅ ΡΠ΄Π°Π»Π΅Π½Π½ΠΎΠΉ ΡΠ°ΡΡΠΈ Π½Π°Π΄ΡΠΈΠ»ΠΎΡΠ½ΠΎΠ³ΠΎ ΠΏΠΎΠΌΠ΅ΡΠ΅Π½ΠΈΡ Π΄ΠΎ Π±Π»ΠΈΠΆΠ°ΠΉΡΠ΅Π³ΠΎ Π²ΡΡ
ΠΎΠ΄Π° Π½Π° Π½Π°ΡΡΠΆΠ½ΡΡ Π»Π΅ΡΡΠ½ΠΈΡΡ ΠΈΠ»ΠΈ Π»Π΅ΡΡΠ½ΠΈΡΠ½ΡΡ ΠΊΠ»Π΅ΡΠΊΡ Π΄ΠΎΠ»ΠΆΠ½ΠΎ Π±ΡΡΡ Π½Π΅ Π±ΠΎΠ»Π΅Π² 75 ΠΌ.
ΠΡΠΈ Ρ
ΡΠ°Π½Π΅Π½ΠΈΠΈ Π² ΡΠΈΠ»ΠΎΡΠ°Ρ
Π½Π΅ΡΠ³ΠΎΡΠ°Π΅ΠΌΡΡ
ΠΌΠ°ΡΠ΅ΡΠΈΠ°Π»ΠΎΠ² ΡΡΠΎ ΡΠ°ΡΡΡΠΎΡΠ½ΠΈΠ΅ Π΄ΠΎΠΏΡΡΠΊΠ°Π΅ΡΡΡ ΡΠ²Π΅Π»ΠΈΡΠΈΠ²Π°ΡΡ Π΄ΠΎ 100 ΠΌ.
ΠΡΠΈ ΠΏΡΠΎΠΈΠ·Π²ΠΎΠ΄ΡΡΠ²Π΅ ΡΠΈΠ»ΠΎΡΠΎΠ² Π΄Π»Ρ ΡΡΠΏΡΡΠΈΡ
ΠΌΠ°ΡΠ΅ΡΠΈΠ°Π»ΠΎΠ², ΠΏΡΠ»Ρ ΠΊΠΎΡΠΎΡΡΡ
ΡΠΏΠΎΡΠΎΠ±Π½Π° ΠΎΠ±ΡΠ°Π·ΠΎΠ²Π°ΡΡ ΠΏΡΠΈ Π·Π°Π³ΡΡΠ·ΠΊΠ΅ ΠΈΠ»ΠΈ ΡΠ°Π·Π³ΡΡΠ·ΠΊΠ΅ ΡΠΈΠ»ΠΎΡΠΎΠ² Π²Π·ΡΡΠ²ΠΎΠΎΠΏΠ°ΡΠ½ΡΠ΅ ΠΊΠΎΠ½ΡΠ΅Π½ΡΡΠ°ΡΠΈΠΈ, Π΄ΠΎΠ»ΠΆΠ½Ρ ΠΏΡΠ΅Π΄ΡΡΠΌΠ°ΡΡΠΈΠ²Π°ΡΡΡΡ ΠΌΠ΅ΡΠΎΠΏΡΠΈΡΡΠΈΡ, ΠΈΡΠΊΠ»ΡΡΠ°ΡΡΠΈΠ΅ Π²ΠΎΠ·ΠΌΠΎΠΆΠ½ΠΎΡΡΡ Π²Π·ΡΡΠ²ΠΎΠ², Π° ΡΠ°ΠΊΠΆΠ΅ ΠΏΡΠ΅Π΄ΡΠΏΡΠ΅ΠΆΠ΄Π°ΡΡΠΈΠ΅ ΠΏΠΎΡΠ²Π»Π΅Π½ΠΈΠ΅ ΡΠ»Π΅ΠΊΡΡΠΎΡΡΠ°ΡΠΈΡΠ΅ΡΠΊΠΈΡ
ΡΠ°Π·ΡΡΠ΄ΠΎΠ².
Π‘ΠΈΠ»ΠΎΡΠ½ΡΠ΅ ΠΊΠΎΡΠΏΡΡΠ°, ΠΎΡΠ΄Π΅Π»ΡΠ½ΠΎ ΡΡΠΎΡΡΠΈΠ΅ ΡΠΈΠ»ΠΎΡΡ, Π½Π°Π΄ΡΠΈΠ»ΠΎΡΠ½ΡΠ΅ Π³Π°Π»Π΅ΡΠ΅ΠΈ, Π½Π°Π΄ΡΡΡΠΎΠΉΠΊΠΈ (Π²ΡΡΠ΅ ΡΡΠΎΠ²Π½Ρ Π½Π°Π΄ΡΠΈΠ»ΠΎΡΠ½ΠΎΠ³ΠΎ ΠΏΠ΅ΡΠ΅ΠΊΡΡΡΠΈΡ) Π΄ΠΎΠΏΡΡΠΊΠ°Π΅ΡΡΡ ΠΏΡΠΎΠ΅ΠΊΡΠΈΡΠΎΠ²Π°ΡΡ Π² ΡΠΎΠΎΡΠ²Π΅ΡΡΡΠ²ΠΈΠΈ Ρ Π’Π 101-81* ΠΈΠ· ΡΡΠ°Π»ΡΠ½ΡΡ
ΠΊΠΎΠ½ΡΡΡΡΠΊΡΠΈΠΉ Ρ ΠΏΡΠ΅Π΄Π΅Π»ΠΎΠΌ ΠΎΠ³Π½Π΅ΡΡΠΎΠΉΠΊΠΎΡΡΠΈ Π½Π΅ ΠΌΠ΅Π½Π΅Π΅ 0,25 Ρ ΠΈ Π½ΡΠ»Π΅Π²ΡΠΌ ΠΏΡΠ΅Π΄Π΅Π»ΠΎΠΌ ΡΠ°ΡΠΏΡΠΎΡΡΡΠ°Π½Π΅Π½ΠΈΡ ΠΎΠ³Π½Ρ. ΠΡΠΈΠΌΠ΅ΡΠ°Π½ΠΈΠ΅. ΠΠ»Ρ ΡΡΠ°Π»ΡΠ½ΡΡ
ΠΊΠΎΠ»ΠΎΠ½Π½ ΠΈ ΠΏΠ΅ΡΠ΅ΠΊΡΡΡΠΈΠΉ Π½Π°Π΄ΡΡΡΠΎΠ΅ΠΊ, ΠΊΡΠΎΠΌΠ΅ Π΄Π²ΡΡ
Π²Π΅ΡΡ
Π½ΠΈΡ
ΡΡΠ°ΠΆΠ΅ΠΉ, Π° ΡΠ°ΠΊΠΆΠ΅ Π΄Π»Ρ Π½Π΅ΡΡΡΠΈΡ
ΠΊΠΎΠ½ΡΡΡΡΠΊΡΠΈΠΉ ΠΏΠΎΠ΄ΡΠΈΠ»ΠΎΡΠ½ΡΡ
ΡΡΠ°ΠΆΠ΅ΠΉ (ΠΊΠΎΠ»ΠΎΠ½Π½ ΠΈ Π±Π°Π»ΠΎΠΊ ΠΏΠΎΠ΄ ΡΡΠ΅Π½Ρ ΡΠΈΠ»ΠΎΡΠΎΠ²) Π΄ΠΎΠ»ΠΆΠ½Π° ΠΏΡΠ΅Π΄ΡΡΠΌΠ°ΡΡΠΈΠ²Π°ΡΡΡΡ ΠΎΠ³Π½Π΅Π·Π°ΡΠΈΡΠ°, ΠΎΠ±Π΅ΡΠΏΠ΅ΡΠΈΠ²Π°ΡΡΠ°Ρ ΠΏΡΠ΅Π΄Π΅Π» ΠΎΠ³Π½Π΅ΡΡΠΎΠΉΠΊΠΎΡΡΠΈ ΡΡΠΈΡ
ΠΊΠΎΠ½ΡΡΡΡΠΊΡΠΈΠΉ Π½Π΅ ΠΌΠ΅Π½Π΅Π΅ 0,75 Ρ.
Π£Π³ΠΎΠ»ΡΠ½ΡΠ΅ Π±Π°ΡΠ½ΠΈ ΠΊΠΎΠΊΡΠΎΡ
ΠΈΠΌΠΈΡΠ΅ΡΠΊΠΈΡ
Π·Π°Π²ΠΎΠ΄ΠΎΠ².
ΠΠΎΡΠΌΡ Π½Π°ΡΡΠΎΡΡΠ΅Π³ΠΎ ΡΠ°Π·Π΄Π΅Π»Π° ΡΠ»Π΅Π΄ΡΠ΅Ρ ΡΠΎΠ±Π»ΡΠ΄Π°ΡΡ ΠΏΡΠΈ ΠΏΡΠΎΠΈΠ·Π²ΠΎΠ΄ΡΡΠ²Π΅ ΡΠ³ΠΎΠ»ΡΠ½ΡΡ
Π±Π°ΡΠ΅Π½ ΠΊΠΎΠΊΡΠΎΡ
ΠΈΠΌΠ·Π°Π²ΠΎΠ΄ΠΎΠ², ΠΏΡΠ΅Π΄Π½Π°Π·Π½Π°ΡΠ΅Π½Π½ΡΡ
Π΄Π»Ρ Π°ΠΊΠΊΡΠΌΡΠ»ΡΡΠΈΠΈ ΡΠ³ΠΎΠ»ΡΠ½ΠΎΠΉ ΡΠΈΡ
ΡΡ ΠΏΠ΅ΡΠ΅Π΄ ΠΊΠΎΠΊΡΠΎΠ²Π°Π½ΠΈΠ΅ΠΌ ΠΈ Π΅Π΅ ΠΏΠΎΠ³ΡΡΠ·ΠΊΠΈ Π² Π·Π°Π³ΡΡΠ·ΠΎΡΠ½ΡΠ΅ Π²Π°Π³ΠΎΠ½Ρ Π΄Π»Ρ ΡΠ°ΡΠΏΡΠ΅Π΄Π΅Π»Π΅Π½ΠΈΡ ΠΏΠΎ ΠΊΠΎΠΊΡΠΎΠ²ΡΠΌ ΠΏΠ΅ΡΠ°ΠΌ.
ΠΠ±ΡΠ΅ΠΌΠ½ΠΎ-ΠΏΠ»Π°Π½ΠΈΡΠΎΠ²ΠΎΡΠ½ΡΠ΅ ΡΠ΅ΡΠ΅Π½ΠΈΡ ΡΠ³ΠΎΠ»ΡΠ½ΡΡ
Π±Π°ΡΠ΅Π½ ΠΈ ΠΈΡ
Π³Π°Π±Π°ΡΠΈΡΠ½ΡΠ΅ ΡΠ°Π·ΠΌΠ΅ΡΡ Π΄ΠΎΠ»ΠΆΠ½Ρ ΠΎΠ±Π΅ΡΠΏΠ΅ΡΠΈΠ²Π°ΡΡ Π²ΠΎΠ·ΠΌΠΎΠΆΠ½ΠΎΡΡΡ ΡΠ°ΡΠΈΠΎΠ½Π°Π»ΡΠ½ΠΎΠΉ ΠΊΠΎΠΌΠΏΠΎΠ½ΠΎΠ²ΠΊΠΈ Ρ ΠΊΠΎΠΊΡΠΎΠ²ΡΠΌΠΈ Π±Π°ΡΠ°ΡΠ΅ΡΠΌΠΈ ΠΈ ΡΠΎΠΎΡΠ²Π΅ΡΡΡΠ²ΡΡΡΠ΅Π΅ ΡΡΡΠΎΠΈΡΠ΅Π»ΡΠ½ΠΎΠΌΡ Π·Π°Π΄Π°Π½ΠΈΡ Π²Π·Π°ΠΈΠΌΠ½ΠΎΠ΅ ΡΠ°ΡΠΏΠΎΠ»ΠΎΠΆΠ΅Π½ΠΈΠ΅ Ρ ΠΏΠΎΠ΄Π²ΠΈΠΆΠ½ΡΠΌ ΡΠ΅Ρ
Π½ΠΎΠ»ΠΎΠ³ΠΈΡΠ΅ΡΠΊΠΈΠΌ ΠΎΠ±ΠΎΡΡΠ΄ΠΎΠ²Π°Π½ΠΈΠ΅ΠΌ (ΠΊΠΎΠΊΡΠΎΠ²ΡΡΠ°Π»ΠΊΠΈΠ²Π°ΡΠ΅Π»ΡΠΌΠΈ, Π΄Π²Π΅ΡΠ΅ΡΡΠ΅ΠΌΠΎΡΠ½ΡΠΌΠΈ ΠΌΠ°ΡΠΈΠ½Π°ΠΌΠΈ, ΡΡΡΠΈΠ»ΡΠ½ΡΠΌΠΈ ΠΈ Π·Π°Π³ΡΡΠ·ΠΎΡΠ½ΡΠΌΠΈ Π²Π°Π³ΠΎΠ½Π°ΠΌΠΈ). ΠΠ°ΠΊ ΠΏΡΠ°Π²ΠΈΠ»ΠΎ, ΡΠ³ΠΎΠ»ΡΠ½ΡΠ΅ Π±Π°ΡΠ½ΠΈ Π΄ΠΎΠ»ΠΆΠ½Ρ Π±ΡΡΡ ΠΏΡΡΠΌΠΎΡΠ³ΠΎΠ»ΡΠ½ΡΠΌΠΈ Π² ΠΏΠ»Π°Π½Π΅.
ΠΡΠΈ ΠΏΡΠΎΠΈΠ·Π²ΠΎΠ΄ΡΡΠ²Π΅ Π½Π΅ΡΠΊΠΎΠ»ΡΠΊΠΈΡ
ΡΠ³ΠΎΠ»ΡΠ½ΡΡ
Π±Π°ΡΠ΅Π½ Π΄Π»Ρ ΠΎΠ΄Π½ΠΎΠ³ΠΎ ΠΏΡΠ΅Π΄ΠΏΡΠΈΡΡΠΈΡ ΠΈΡ
ΠΊΠΎΠ½ΡΠΈΠ³ΡΡΠ°ΡΠΈΡ ΠΈ ΡΠ°Π·ΠΌΠ΅ΡΡ Π³ΠΎΡΠΈΠ·ΠΎΠ½ΡΠ°Π»ΡΠ½ΠΎΠ³ΠΎ ΡΠ΅ΡΠ΅Π½ΠΈΡ Π΄ΠΎΠ»ΠΆΠ½Ρ Π±ΡΡΡ, ΠΊΠ°ΠΊ ΠΏΡΠ°Π²ΠΈΠ»ΠΎ, ΡΠ½ΠΈΡΠΈΡΠΈΡΠΎΠ²Π°Π½Ρ. ΠΠ°Π±Π°ΡΠΈΡΡ ΡΠ³ΠΎΠ»ΡΠ½ΡΡ
Π±Π°ΡΠ΅Π½ ΡΠ»Π΅Π΄ΡΠ΅Ρ ΠΏΡΠΈΠ½ΠΈΠΌΠ°ΡΡ ΠΏΠΎ Π³ΠΎΡΠΈΠ·ΠΎΠ½ΡΠ°Π»ΠΈ ΠΊΡΠ°ΡΠ½ΡΠΌΠΈ 0,3 ΠΌ, ΠΏΠΎ Π²Π΅ΡΡΠΈΠΊΠ°Π»ΠΈ β ΠΊΡΠ°ΡΠ½ΡΠΌΠΈ 0,6 ΠΌ.
Π‘Π²ΠΎΠ±ΠΎΠ΄Π½ΡΠ΅ ΠΎΡ ΡΠ΅Ρ
Π½ΠΎΠ»ΠΎΠ³ΠΈΡΠ΅ΡΠΊΠΎΠ³ΠΎ ΠΎΠ±ΠΎΡΡΠ΄ΠΎΠ²Π°Π½ΠΈΡ ΠΎΡΠ½ΠΎΠ²Π½ΠΎΠ³ΠΎ Π½Π°Π·Π½Π°ΡΠ΅Π½ΠΈΡ ΠΎΠ±ΡΠ΅ΠΌΡ Π½ΠΈΠΆΠ½Π΅ΠΉ Π·ΠΎΠ½Ρ ΡΠ³ΠΎΠ»ΡΠ½ΠΎΠΉ Π±Π°ΡΠ½ΠΈ Π΄ΠΎΠΏΡΡΠΊΠ°Π΅ΡΡΡ ΠΈΡΠΏΠΎΠ»ΡΠ·ΠΎΠ²Π°ΡΡ Π΄Π»Ρ ΡΠ°Π·ΠΌΠ΅ΡΠ΅Π½ΠΈΡ Π²ΡΠΏΠΎΠΌΠΎΠ³Π°ΡΠ΅Π»ΡΠ½ΡΡ
ΠΏΠΎΠΌΠ΅ΡΠ΅Π½ΠΈΠΉ: ΡΠ»Π΅ΠΊΡΡΠΎΠΏΡΠ½ΠΊΡΠΎΠ², Π²Π΅Π½ΡΠΈΠ»ΡΡΠΈΠΎΠ½Π½ΡΡ
ΡΡΡΠ°Π½ΠΎΠ²ΠΎΠΊ, ΠΏΠΎΠΌΠ΅ΡΠ΅Π½ΠΈΠΉ ΠΠΠ, ΡΠ»ΡΠΆΠ΅Π±Π½ΠΎ-Π±ΡΡΠΎΠ²ΡΡ
ΠΏΠΎΠΌΠ΅ΡΠ΅Π½ΠΈΠΉ ΠΊΠΎΠΊΡΠΎΠ²ΠΎΠ³ΠΎ Π±Π»ΠΎΠΊΠ° ΠΈ Ρ.Π΄.
ΠΠ½ΡΡΡΠ΅Π½Π½ΠΈΠ΅ Π³Π°Π±Π°ΡΠΈΡΡ Π² ΡΠΊΠ²ΠΎΠ·Π½ΠΎΠΉ ΡΠ°ΡΡΠΈ ΡΠ³ΠΎΠ»ΡΠ½ΠΎΠΉ Π±Π°ΡΠ½ΠΈ Π΄ΠΎΠ»ΠΆΠ½Ρ ΠΎΠ±Π΅ΡΠΏΠ΅ΡΠΈΠ²Π°ΡΡ Π½Π°Π»ΠΈΡΠΈΠ΅: ΡΡΠ΅Π±ΡΠ΅ΠΌΡΡ
ΠΏΡΠ°Π²ΠΈΠ»Π°ΠΌΠΈ Π±Π΅Π·ΠΎΠΏΠ°ΡΠ½ΠΎΡΡΠΈ Π·Π°Π·ΠΎΡΠΎΠ² ΠΌΠ΅ΠΆΠ΄Ρ ΡΡΡΠΎΠΈΡΠ΅Π»ΡΠ½ΡΠΌΠΈ ΠΈ ΡΠ΅Ρ
Π½ΠΎΠ»ΠΎΠ³ΠΈΡΠ΅ΡΠΊΠΈΠΌΠΈ ΠΊΠΎΠ½ΡΡΡΡΠΊΡΠΈΡΠΌΠΈ, Π½ΠΎ Π½Π΅ ΠΌΠ΅Π½Π΅Π΅ 0,1 ΠΌ; ΠΏΡΠΎΡ
ΠΎΠ΄ΠΎΠΊ Ρ ΠΎΠ±Π΅ΠΈΡ
ΡΡΠΎΡΠΎΠ½ Π·Π°Π³ΡΡΠ·ΠΎΡΠ½ΠΎΠ³ΠΎ Π²Π°Π³ΠΎΠ½Π° ΡΠΈΡΠΈΠ½ΠΎΠΉ Π½Π΅ ΠΌΠ΅Π½Π΅Π΅ 0,8 ΠΌ ΠΈ Π²ΡΡΠΎΡΠΎΠΉ Π½Π΅ ΠΌΠ΅Π½Π΅Π΅ 2,1 ΠΌ.
Π Π°Π·ΠΌΠ΅ΡΡ Π½Π°Π΄ΡΠ΅ΠΌΠΊΠΎΡΡΠ½ΠΎΠΉ ΡΠ°ΡΡΠΈ ΡΠ³ΠΎΠ»ΡΠ½ΠΎΠΉ Π±Π°ΡΠ½ΠΈ Π΄ΠΎΠ»ΠΆΠ½Ρ ΠΎΠ±Π΅ΡΠΏΠ΅ΡΠΈΠ²Π°ΡΡ Π²ΠΎΠ·ΠΌΠΎΠΆΠ½ΠΎΡΡΡ ΡΠ°Π·ΠΌΠ΅ΡΠ΅Π½ΠΈΡ ΠΎΠ±ΠΎΡΡΠ΄ΠΎΠ²Π°Π½ΠΈΡ, ΠΏΡΠ΅Π΄Π½Π°Π·Π½Π°ΡΠ΅Π½Π½ΠΎΠ³ΠΎ Π΄Π»Ρ ΡΠ°ΡΠΏΡΠ΅Π΄Π΅Π»Π΅Π½ΠΈΡ ΡΠΈΡ
ΡΡ ΠΏΠΎ ΡΡΠ΅ΠΉΠΊΠ°ΠΌ Π΅ΠΌΠΊΠΎΡΡΠ½ΠΎΠΉ ΡΠ°ΡΡΠΈ. ΠΡΠΈ ΡΡΠΎΠΌ ΠΌΠ΅ΠΆΠ΄Ρ ΠΎΠ±ΠΎΡΡΠ΄ΠΎΠ²Π°Π½ΠΈΠ΅ΠΌ ΠΈ ΡΡΡΠΎΠΈΡΠ΅Π»ΡΠ½ΡΠΌΠΈ ΠΊΠΎΠ½ΡΡΡΡΠΊΡΠΈΡΠΌΠΈ Π΄ΠΎΠ»ΠΆΠ½Ρ ΠΏΡΠ΅Π΄ΡΡΠΌΠ°ΡΡΠΈΠ²Π°ΡΡΡΡ ΠΏΡΠΎΡ
ΠΎΠ΄Ρ ΡΠΈΡΠΈΠ½ΠΎΠΉ Π½Π΅ ΠΌΠ΅Π½Π΅Π΅ 0,8 ΠΌ.
ΠΡΠΈ ΡΠ°ΡΡΠ΅ΡΠ΅ ΡΠ³ΠΎΠ»ΡΠ½ΡΡ
Π±Π°ΡΠ΅Π½ ΠΈ ΠΈΡ
ΡΠ»Π΅ΠΌΠ΅Π½ΡΠΎΠ² Π΄ΠΎΠ»ΠΆΠ½Ρ Π±ΡΡΡ ΡΡΡΠ΅Π½Ρ ΡΠ»Π΅Π΄ΡΡΡΠΈΠ΅ Π½Π°Π³ΡΡΠ·ΠΊΠΈ: ΡΠΎΠ±ΡΡΠ²Π΅Π½Π½ΡΠΉ Π²Π΅Ρ ΠΊΠΎΠ½ΡΡΡΡΠΊΡΠΈΠΉ, Π½Π°Π³ΡΡΠ·ΠΊΠΈ ΠΎΡ ΡΡΠ°ΡΠΈΠΎΠ½Π°ΡΠ½ΠΎΠ³ΠΎ ΠΎΠ±ΠΎΡΡΠ΄ΠΎΠ²Π°Π½ΠΈΡ ΠΈ Π·Π°Π³ΡΡΠ·ΠΎΡΠ½ΠΎΠ³ΠΎ Π²Π°Π³ΠΎΠ½Π°, Π΄Π°Π²Π»Π΅Π½ΠΈΠ΅ ΠΌΠ°ΡΠ΅ΡΠΈΠ°Π»Π° Π·Π°ΠΏΠΎΠ»Π½Π΅Π½ΠΈΡ Π΅ΠΌΠΊΠΎΡΡΠ΅ΠΉ, Π²Π΅ΡΡΠΎΠ²Π°Ρ Π½Π°Π³ΡΡΠ·ΠΊΠ°, Π΄Π°Π²Π»Π΅Π½ΠΈΠ΅ Π³ΡΡΠ½ΡΠ°, Π½Π°Π³ΡΡΠ·ΠΊΠΈ, ΠΏΠ΅ΡΠ΅Π΄Π°Π²Π°Π΅ΠΌΡΠ΅ ΠΏΡΠΈΠΌΡΠΊΠ°ΡΡΠΈΠΌΠΈ ΠΊΠΎΠ½ΡΡΡΡΠΊΡΠΈΡΠΌΠΈ. Π ΡΠ»ΡΡΠ°Π΅ Π½Π΅ΠΎΠ±Ρ
ΠΎΠ΄ΠΈΠΌΠΎΡΡΠΈ ΡΡΠΈΡΡΠ²Π°ΡΡΡΡ ΠΎΡΠΎΠ±ΡΠ΅ Π½Π°Π³ΡΡΠ·ΠΊΠΈ ΠΈ Π²ΠΎΠ·Π΄Π΅ΠΉΡΡΠ²ΠΈΡ (ΡΠ΅ΠΉΡΠΌΠΈΡΠ΅ΡΠΊΠΈΠ΅, Π²Π»ΠΈΡΠ½ΠΈΠ΅ Π³ΠΎΡΠ½ΡΡ
Π²ΡΡΠ°Π±ΠΎΡΠΎΠΊ ΠΈ Ρ. Π΄.).
ΠΡΠΈ ΡΠ°ΡΡΠ΅ΡΠ΅ ΡΡΠ΅Π½ Π΅ΠΌΠΊΠΎΡΡΠ½ΠΎΠΉ ΡΠ°ΡΡΠΈ Π½Π΅ΠΎΠ±Ρ
ΠΎΠ΄ΠΈΠΌΠΎ ΡΠ°ΡΡΠΌΠ°ΡΡΠΈΠ²Π°ΡΡ ΡΠ»Π΅Π΄ΡΡΡΠΈΠ΅ ΡΠΎΡΠ΅ΡΠ°Π½ΠΈΡ Π½Π°Π³ΡΡΠ·ΠΎΠΊ: Π²ΡΠ΅ Π΅ΠΌΠΊΠΎΡΡΠΈ Π·Π°ΠΏΠΎΠ»Π½Π΅Π½Ρ, Π½Π° ΠΎΠ΄Π½Ρ ΠΈΠ· ΡΡΠ΅Π½ Π΄Π΅ΠΉΡΡΠ²ΡΠ΅Ρ ΠΎΡΡΠΈΡΠ°ΡΠ΅Π»ΡΠ½ΠΎΠ΅ Π΄Π°Π²Π»Π΅Π½ΠΈΠ΅ Π²Π΅ΡΡΠ° ΠΊΠ°ΠΊ Π½Π° ΠΏΠΎΠ΄Π²Π΅ΡΡΠ΅Π½Π½ΡΡ Π²Π΅ΡΡΠΈΠΊΠ°Π»ΡΠ½ΡΡ ΠΏΠΎΠ²Π΅ΡΡ
Π½ΠΎΡΡΡ; Π΅ΠΌΠΊΠΎΡΡΠΈ Π½Π΅ Π·Π°ΠΏΠΎΠ»Π½Π΅Π½Ρ, Π½Π° ΡΡΠ΅Π½Ρ Π΄Π΅ΠΉΡΡΠ²ΡΠ΅Ρ ΠΏΠΎΠ»ΠΎΠΆΠΈΡΠ΅Π»ΡΠ½ΠΎΠ΅ Π΄Π°Π²Π»Π΅Π½ΠΈΠ΅ Π²Π΅ΡΡΠ° ΠΊΠ°ΠΊ Π½Π° Π½Π°Π²Π΅ΡΡΠ΅Π½Π½ΡΡ Π²Π΅ΡΡΠΈΠΊΠ°Π»ΡΠ½ΡΡ ΠΏΠΎΠ²Π΅ΡΡ
Π½ΠΎΡΡΡ; Π·Π°ΠΏΠΎΠ»Π½Π΅Π½Π° ΠΎΠ΄Π½Π° ΠΈΠ· Π΅ΠΌΠΊΠΎΡΡΠ΅ΠΉ (Π΄Π»Ρ ΡΠ°ΡΡΠ΅ΡΠ° Π²Π½ΡΡΡΠ΅Π½Π½Π΅ΠΉ ΠΏΠΎΠΏΠ΅ΡΠ΅ΡΠ½ΠΎΠΉ ΡΡΠ΅Π½Ρ). ΠΏΡΠΎΠΈΠ·Π²ΠΎΠ΄ΡΡΠ²ΠΎ
Π£Π³ΠΎΠ»ΡΠ½ΡΡ Π±Π°ΡΠ½Ρ ΡΠ»Π΅Π΄ΡΠ΅Ρ ΡΠ°ΡΡΡΠΈΡΡΠ²Π°ΡΡ ΠΊΠ°ΠΊ ΠΏΡΠΎΡΡΡΠ°Π½ΡΡΠ²Π΅Π½Π½ΡΡ ΡΠΈΡΡΠ΅ΠΌΡ Ρ ΡΡΠ΅ΡΠΎΠΌ ΡΠΈΠ·ΠΈΡΠ΅ΡΠΊΠΎΠΉ, Π° Π΄Π»Ρ ΡΡΠ΅Π½ Π° Π·ΠΎΠ½Π΅ ΠΏΡΠΎΠ΅Π·Π΄Π° Π·Π°Π³ΡΡΠ·ΠΎΡΠ½ΠΎΠ³ΠΎ Π²Π°Π³ΠΎΠ½Π° β ΠΈ Π΅Π³ΠΎ Π³Π΅ΠΎΠΌΠ΅ΡΡΠΈΡΠ΅ΡΠΊΠΎΠΉ Π½Π΅Π»ΠΈΠ½Π΅ΠΉΠ½ΠΎΡΡΠΈ (ΠΏΠΎ Π΄Π΅ΡΠΎΡΠΌΠΈΡΠΎΠ²Π°Π½Π½ΠΎΠΉ ΡΡ
Π΅ΠΌΠ΅ Ρ ΡΡΠ΅ΡΠΎΠΌ Π½Π΅Π²ΡΠ³ΠΎΠ΄Π½ΡΡ
Π΄Π»Ρ ΠΊΠΎΠ½ΡΡΡΡΠΊΡΠΈΠΉ ΠΎΡΠΊΠ»ΠΎΠ½Π΅Π½ΠΈΠΉ ΠΎΡ Π²Π΅ΡΡΠΈΠΊΠ°Π»ΠΈ Π² ΠΏΡΠ΅Π΄Π΅Π»Π°Ρ
, Π΄ΠΎΠΏΡΡΠΊΠ°Π΅ΠΌΡΡ
ΡΡΡΠΎΠΈΡΠ΅Π»ΡΠ½ΡΠΌΠΈ Π½ΠΎΡΠΌΠ°ΠΌΠΈ ΠΈ ΠΏΡΠ°Π²ΠΈΠ»Π°ΠΌΠΈ Π½Π° ΠΏΡΠΎΠΈΠ·Π²ΠΎΠ΄ΡΡΠ²ΠΎ ΡΠ°Π±ΠΎΡ).
ΠΠΎΠΏΡΡΠΊΠ°Π΅ΡΡΡ Π²ΡΠΏΠΎΠ»Π½ΡΡΡ ΡΠ°ΡΡΠ΅Ρ ΡΡΠ΅Π½ ΡΠ³ΠΎΠ»ΡΠ½ΠΎΠΉ Π±Π°ΡΠ½ΠΈ, ΡΠ°ΡΡΠ»Π΅Π½ΡΡ Π΅Π΅ Π½Π° ΠΎΡΠ΄Π΅Π»ΡΠ½ΡΠ΅ ΡΠ»Π΅ΠΌΠ΅Π½ΡΡ ΠΏΡΠΎΠ΄ΠΎΠ»ΡΠ½ΡΠ΅ ΠΈ ΠΏΠΎΠΏΠ΅ΡΠ΅ΡΠ½ΡΠ΅ ΡΡΠ΅Π½Ρ Π΅ΠΌΠΊΠΎΡΡΠ½ΠΎΠΉ ΡΠ°ΡΡΠΈ, ΠΏΡΠΎΠ΄ΠΎΠ»ΡΠ½ΡΠ΅ ΡΡΠ΅Π½Ρ Π² Π·ΠΎΠ½Π΅ ΠΏΡΠΎΠ΅Π·Π΄Π° Π·Π°Π³ΡΡΠ·ΠΎΡΠ½ΠΎΠ³ΠΎ Π²Π°Π³ΠΎΠ½Π°, Π½ΠΈΠΆΠ½ΡΡ Π·ΠΎΠ½Ρ ΡΡΠ΅Π½. ΠΡΠΈ ΡΠ°ΡΡΠ΅ΡΠ° ΠΏΠΎΠΏΠ΅ΡΠ΅ΡΠ½ΡΡ
ΡΡΠ΅Π½ Π΅ΠΌΠΊΠΎΡΡΠ½ΠΎΠΉ ΡΠ°ΡΡΠΈ ΡΠ»Π΅Π΄ΡΠ΅Ρ ΡΡΠΈΡΡΠ²Π°ΡΡ Π½Π°Π»ΠΈΡΠΈΠ΅ ΠΏΡΠΎΠ΅ΠΌΠΎΠ² Π΄Π»Ρ ΠΏΡΠΎΠ΅Π·Π΄Π° Π·Π°Π³ΡΡΠ·ΠΎΡΠ½ΠΎΠ³ΠΎ Π²Π°Π³ΠΎΠ½Π°, ΠΏΡΠ΅Π²ΡΠ°ΡΠ°ΡΡΠΈΡ
ΡΡΠΈ ΡΡΠ΅Π½Ρ ΠΏΡΠΈ ΠΏΠΎΡΠ»Π΅ΠΌΠ΅Π½ΡΠ½ΠΎΠΌ ΡΠ°ΡΡΠ΅ΡΠ° Π² Π±Π°Π»ΠΊΠΈ-ΡΡΠ΅Π½ΠΊΠΈ.
Π ΡΠ³ΠΎΠ»ΡΠ½ΡΡ
Π±Π°ΡΠ½ΡΡ
Π΄ΠΎΠ»ΠΆΠ΅Π½ Π±ΡΡΡ ΠΏΡΠ΅Π΄ΡΡΠΌΠΎΡΡΠ΅Π½ Π³ΡΡΠ·ΠΎΠΏΠ°ΡΡΠ°ΠΆΠΈΡΡΠΊΠΈΠΉ Π»ΠΈΡΡ Π΄ΠΎ Π½Π°Π΄ΡΠ΅ΠΌΠΊΠΎΡΡΠ½ΠΎΠΉ ΡΠ°ΡΡΠΈ. ΠΠ»Ρ ΠΎΠ±Π΅ΡΠΏΠ΅ΡΠ΅Π½ΠΈΡ ΠΏΠΎΠΆΠ°ΡΠ½ΠΎΠΉ Π±Π΅Π·ΠΎΠΏΠ°ΡΠ½ΠΎΡΡΠΈ Π½Π΅ΠΎΠ±Ρ
ΠΎΠ΄ΠΈΠΌΠΎ ΠΏΡΠ΅Π΄ΡΡΠΌΠ°ΡΡΠΈΠ²Π°ΡΡ Π ΠΏΠΎΠΌΠ΅ΡΠ΅Π½ΠΈΡΡ
ΡΠ³ΠΎΠ»ΡΠ½ΠΎΠΉ Π±Π°ΡΠ½ΠΈ ΠΏΠΎΠΆΠ°ΡΠ½ΠΎ-ΠΏΠΈΡΡΠ΅Π²ΠΎΠΉ Π²ΠΎΠ΄ΠΎΠΏΡΠΎΠ²ΠΎΠ΄.
ΠΡΠ½ΠΎΠ²Π½ΡΠ΅ ΠΏΠΎΠ½ΡΡΠΈΡ:
ΡΠ°ΠΌΠ°ΡΡΠΊΠΈΠΉ Π·Π°Π²ΠΎΠ΄ ΡΠΈΠ»ΠΎΡΠΎΠ², ΡΠΈΠ»ΠΎΡ ΡΠ΅ΠΌΠ΅Π½ΡΠ° ΠΊΡΠΏΠΈΡΡ, ΡΠΈΠ»ΠΎΡ ΠΊΡΠΏΠΈΡΡ, ΠΏΡΠΎΠΈΠ·Π²ΠΎΠ΄ΡΡΠ²ΠΎ ΡΠΈΠ»ΠΎΡΠΎΠ², ΠΈΠ·Π³ΠΎΡΠΎΠ²Π»Π΅Π½ΠΈΠ΅ ΡΠΈΠ»ΠΎΡΠΎΠ², Π·Π°Π²ΠΎΠ΄ ΡΠΈΠ»ΠΎΡΠΎΠ², ΡΠΈΠ»ΠΎΡ ΡΠ΅ΠΌΠ΅Π½ΡΠ°, ΡΠΈΠ»ΠΎΡ Π΄Π»Ρ ΡΠ΅ΠΌΠ΅Π½ΡΠ°, ΡΠ΅ΠΌΠ΅Π½ΡΠ½ΡΠΉ ΡΠΈΠ»ΠΎΡ, ΡΠΈΠ»ΠΎΡ Π΄Π»Ρ Π³ΠΈΠΏΡΠ°, ΡΠΈΠ»ΠΎΡ Π΄Π»Ρ ΠΌΠΈΠ½Π΅ΡΠ°Π»ΡΠ½ΠΎΠ³ΠΎ ΠΏΠΎΡΠΎΡΠΊΠ°, ΡΠΊΠ»Π°Π΄ Π³ΠΈΠΏΡΠ°, ΡΠΊΠ»Π°Π΄ ΠΏΠΎΡΠΎΡΠΊΠ°, ΡΠΊΠ»Π°Π΄ Ρ
ΡΠ°Π½Π΅Π½ΠΈΡ Π³ΠΈΠΏΡΠ°, ΡΠΊΠ»Π°Π΄ Ρ
ΡΠ°Π½Π΅Π½ΠΈΡ ΠΏΠΎΡΠΎΡΠΊΠ°, ΡΠΊΠ»Π°Π΄ ΡΠ΅ΠΌΠ΅Π½ΡΠ°, ΡΠΊΠ»Π°Π΄ Ρ
ΡΠ°Π½Π΅Π½ΠΈΡ ΡΠ΅ΠΌΠ΅Π½ΡΠ°, ΠΏΡΠΎΠ΅ΠΊΡΠΈΡΠΎΠ²Π°Π½ΠΈΠ΅ ΡΠΈΠ»ΠΎΡΠΎΠ², ΠΏΡΠΎΠ΅ΠΊΡ ΠΊΠΌ Π½Π° ΡΠΈΠ»ΠΎΡ, ΠΏΡΠΎΠ΅ΠΊΡ ΠΊΠΌΠ΄ Π½Π° ΡΠΈΠ»ΠΎΡ ΡΠ΅ΠΌΠ΅Π½ΡΠ°, ΠΏΡΠΎΠ΅ΠΊΡ ΡΠΊΠ»Π°Π΄Π° ΡΠ΅ΠΌΠ΅Π½ΡΠ°, ΡΠΈΠΏΠΎΠ²ΠΎΠΉ ΠΏΡΠΎΠ΅ΠΊΡ ΡΠΈΠ»ΠΎΡ ΡΠ΅ΠΌΠ΅Π½ΡΠ°, ΡΠΈΠ»ΠΎΡ Π΄Π»Ρ ΡΠ΅ΠΌΠ΅Π½ΡΠ° ΠΏΠΎ ΡΠΈΠΏΠΎΠ²ΠΎΠΌΡ ΠΏΡΠΎΠ΅ΠΊΡΡ, ΡΠΈΠΏΠΎΠ²ΠΎΠΉ ΠΏΡΠΎΠ΅ΠΊΡ ΡΠΊΠ»Π°Π΄ ΡΠ΅ΠΌΠ΅Π½ΡΠ°, ΠΌΠΎΠ½ΡΠ°ΠΆ ΡΠΈΠ»ΠΎΡΠΎΠ², ΠΈΠ·Π³ΠΎΡΠΎΠ²Π»Π΅Π½ΠΈΠ΅ ΠΈ ΠΌΠΎΠ½ΡΠ°ΠΆ ΡΠΈΠ»ΠΎΡΠΎΠ², ΠΏΡΠΎΠΈΠ·Π²ΠΎΠ΄ΡΡΠ²ΠΎ ΡΠΈΠ»ΠΎΡΠΎΠ² Π² Π‘Π°ΠΌΠ°ΡΠ΅, ΠΈΠ·Π³ΠΎΡΠΎΠ²Π»Π΅Π½ΠΈΠ΅ ΡΠΈΠ»ΠΎΡΠΎΠ² ΡΠ΅ΠΌΠ΅Π½ΡΠ° Π² Π‘Π°ΠΌΠ°ΡΠ΅, ΠΌΠΎΠ½ΡΠ°ΠΆ ΡΠΈΠ»ΠΎΡΠΎΠ² Π² Π‘Π°ΠΌΠ°ΡΠ΅, ΠΏΡΠΎΠ΅ΠΊΡΠΈΡΠΎΠ²Π°Π½ΠΈΠ΅ ΡΠΈΠ»ΠΎΡΠΎΠ² Π² Π‘Π°ΠΌΠ°ΡΠ΅, ΡΠΊΠ»Π°Π΄ ΡΠ΅ΠΌΠ΅Π½ΡΠ° ΠΏΠΎΠ΄ ΠΊΠ»ΡΡ, ΡΠΈΠ»ΠΎΡ 8 ΠΊΡΠ±.ΠΌ., ΡΠΈΠ»ΠΎΡ 10 ΡΠΎΠ½Π½, ΡΠΈΠ»ΠΎΡ 20 ΠΊΡΠ±.ΠΌ., ΡΠΈΠ»ΠΎΡ 26 ΡΠΎΠ½Π½, ΡΠΈΠ»ΠΎΡ 40 ΠΊΡΠ±.ΠΌ., ΡΠΈΠ»ΠΎΡ 52 ΡΠΎΠ½Π½Ρ, ΡΠΈΠ»ΠΎΡ 50 ΡΠΎΠ½Π½, ΡΠΈΠ»ΠΎΡ 60 ΠΊΡΠ±.ΠΌ., ΡΠΈΠ»ΠΎΡ 90 ΡΠΎΠ½Π½, ΡΠΈΠ»ΠΎΡ 120 ΠΊΡΠ±.ΠΌ., ΡΠΈΠ»ΠΎΡ 156 ΡΠΎΠ½Π½, ΡΠΈΠ»ΠΎΡ 150 ΡΠΎΠ½Π½, ΡΠΈΠ»ΠΎΡ 300 ΠΊΡΠ±.ΠΌ., ΡΠΈΠ»ΠΎΡ 390 ΡΠΎΠ½Π½, ΡΠΈΠ»ΠΎΡ 500 ΡΠΎΠ½Π½, ΡΠΈΠ»ΠΎΡ 1000 ΡΠΎΠ½Π½, ΡΠΊΠ»Π°Π΄ ΡΠ΅ΠΌΠ΅Π½ΡΠ° ΠΏΡΠΈΡΠ΅Π»ΡΡΠΎΠ²ΡΠΉ 360 ΡΠΎΠ½Π½, ΡΠΊΠ»Π°Π΄ ΡΠ΅ΠΌΠ΅Π½ΡΠ° ΠΏΡΠΈΡΠ΅Π»ΡΡΠΎΠ²ΡΠΉ 240 ΡΠΎΠ½Π½, ΠΌΠ΅ΡΠ°Π»Π»ΠΈΡΠ΅ΡΠΊΠΈΠΉ ΡΠΈΠ»ΠΎΡ, ΡΡΠ°Π»ΡΠ½ΠΎΠΉ ΡΠΈΠ»ΠΎΡ, ΠΌΠ΅ΡΠ°Π»Π»ΠΈΡΠ΅ΡΠΊΠΈΠΉ ΡΠΈΠ»ΠΎΡ ΡΠ΅ΠΌΠ΅Π½ΡΠ°, ΡΠΈΠ»ΠΎΡ Π±ΡΠ½ΠΊΠ΅Ρ, Π·Π°Π²ΠΎΠ΄ ΠΏΠΎ ΠΏΡΠΎΠΈΠ·Π²ΠΎΠ΄ΡΡΠ²Ρ ΡΠΈΠ»ΠΎΡΠΎΠ², Π΅ΠΌΠΊΠΎΡΡΡ ΡΠΈΠ»ΠΎΡ, ΡΠΈΠ»ΠΎΡ Π΄Π»Ρ ΡΡΠΏΡΡΠΈΡ
ΠΌΠ°ΡΠ΅ΡΠΈΠ°Π»ΠΎΠ², ΠΏΡΠΎΠΈΠ·Π²ΠΎΠ΄ΠΈΡΠ΅Π»ΠΈ ΡΠΈΠ»ΠΎΡΠΎΠ², ΠΈΠ·Π³ΠΎΡΠΎΠ²ΠΈΡΠ΅Π»ΠΈ ΡΠΈΠ»ΠΎΡΠΎΠ², Π½Π΅ΡΠΆΠ°Π²Π΅ΡΡΠΈΠΉ ΡΠΈΠ»ΠΎΡ, ΡΠΈΠ»ΠΎΡ ΠΈΠ· Π½Π΅ΡΠΆΠ°Π²Π΅ΡΡΠ΅ΠΉ ΡΡΠ°Π»ΠΈ, ΡΠΈΠ»ΠΎΡ Π΄Π»Ρ Ρ
ΡΠ°Π½Π΅Π½ΠΈΡ ΡΠ΅ΠΌΠ΅Π½ΡΠ°, ΠΌΠ΅ΡΠ°Π»Π»ΠΈΡΠ΅ΡΠΊΠΈΠΉ Π±ΡΠ½ΠΊΠ΅Ρ, Π±ΡΠ½ΠΊΠ΅Ρ ΡΠ΅ΠΌΠ΅Π½ΡΠ°, ΡΡΠ°Π»ΡΠ½ΠΎΠΉ ΡΠΈΠ»ΠΎΡ, ΡΡΠ°Π»ΡΠ½ΠΎΠΉ Π±ΡΠ½ΠΊΠ΅Ρ, ΡΠ³ΠΎΠ»ΡΠ½ΡΠ΅ Π±Π°ΡΠ½ΠΈ, Π±Π°ΡΠ½ΠΈ Π΄Π»Ρ ΡΠ³Π»Ρ, ΡΠ΅ΠΌΠ΅Π½ΡΠ½ΡΠΉ ΡΠΈΠ»ΠΎΡ.
www.ozrm.ru
Π‘ΠΈΠ»ΠΎΡΡ
Π‘ΠΈΠ»ΠΎΡ — ΡΡΠ°Π»ΡΠ½Π°Ρ, ΠΆΠ΅Π»Π΅Π·ΠΎ-Π±Π΅ΡΠΎΠ½Π½Π°Ρ ΠΈΠ»ΠΈ ΠΏΠΎΠ»ΠΈΠΌΠ΅ΡΠ½Π°Ρ Π²Π΅ΡΡΠΈΠΊΠ°Π»ΡΠ½Π°Ρ Π΅ΠΌΠΊΠΎΡΡΡ Π΄Π»Ρ Ρ ΡΠ°Π½Π΅Π½ΠΈΡ ΡΡΠΏΡΡΠΈΡ (ΠΏΠΎΡΠΎΡΠΊΠΎΠΎΠ±ΡΠ°Π·Π½ΡΡ ) ΠΌΠ°ΡΠ΅ΡΠΈΠ°Π»ΠΎΠ² ΠΈ Π²Π΅ΡΠ΅ΡΡΠ² Π² ΠΏΡΠΎΠΈΠ·Π²ΠΎΠ΄ΡΡΠ²Π΅, ΡΡΡΠΎΠΈΡΠ΅Π»ΡΡΡΠ²Π΅ ΠΈ ΡΠ΅Π»ΡΡΠΊΠΎΠΌ Ρ ΠΎΠ·ΡΠΉΡΡΠ²Π΅. ΠΠΎΠ½ΡΡΡΡΠΊΡΠΈΠ²Π½ΠΎ ΠΈΠ·Π³ΠΎΡΠ°Π²Π»ΠΈΠ²Π°ΡΡΡΡ Π² Π²ΠΈΠ΄Π΅ ΡΠΈΠ»ΠΈΠ½Π΄ΡΠΈΡΠ΅ΡΠΊΠΎΠΉ ΠΈΠ»ΠΈ ΠΏΡΡΠΌΠΎΡΠ³ΠΎΠ»ΡΠ½ΠΎΠΉ Π΅ΠΌΠΊΠΎΡΡΠΈ Ρ ΠΊΠΎΠ½ΠΈΡΠ΅ΡΠΊΠΈΠΌ Π΄Π½ΠΎΠΌ ΠΈΠΌΠ΅ΡΡΠ΅ΠΌ ΠΎΡΠ²Π΅ΡΡΡΠΈΠ΅ Π΄Π»Ρ Π²ΡΠ³ΡΡΠ·ΠΊΠΈ ΡΠΎΠ΄Π΅ΡΠΆΠΈΠΌΠΎΠ³ΠΎ, ΠΈΡ ΠΎΠ±ΡΡΠΌ Π·Π°Π²ΠΈΡΠΈΡ ΠΎΡ ΡΡΠ»ΠΎΠ²ΠΈΠΉ ΡΠΊΡΠΏΠ»ΡΠ°ΡΠ°ΡΠΈΠΈ ΠΈ ΡΡΠ΅Π±ΠΎΠ²Π°Π½ΠΈΠΉ ΠΊ ΠΎΠ±ΡΡΠΌΠ°ΠΌ ΠΏΡΠΎΠΈΠ·Π²ΠΎΠ΄ΡΡΠ²Π° ΠΈ ΠΈΡ ΠΏΡΠΎΠΈΠ·Π²ΠΎΠ΄ΡΡΠ²ΠΎ ΡΠ²ΡΠ·Π°Π½ΠΎ Ρ ΡΠ΅ΡΠ΅Π½ΠΈΠ΅ΠΌ ΡΠ΅ΡΡΡΠ·Π½ΡΡ Π·Π°Π΄Π°Ρ, ΠΊΠΎΡΠΎΡΡΠ΅ ΠΎΠ±Π΅ΡΠΏΠ΅ΡΠ°Ρ Π±Π΅Π·Π°Π²Π°ΡΠΈΠΉΠ½ΡΡ ΡΠΊΡΠΏΠ»ΡΠ°ΡΠ°ΡΠΈΡ Π² Π΄Π°Π»ΡΠ½Π΅ΠΉΡΠ΅ΠΌ.
ΠΠ½Π°ΡΠ΅Π½ΠΈΠ΅ ΡΠ»ΠΎΠ²Π° Β«ΡΠΈΠ»ΠΎΡΒ» ΡΡ ΠΎΠ΄ΠΈΡ Π² Π΄ΡΠ΅Π²Π½ΠΈΠ΅ Π²ΡΠ΅ΠΌΠ΅Π½Π°, Π³Π΄Π΅ Ρ ΡΡΠΈΠΌ ΡΠ»ΠΎΠ²ΠΎΠΌ ΡΠΎΠ΅Π΄ΠΈΠ½ΡΠ»ΠΈ ΠΏΠΎΠ½ΡΡΠΈΠ΅ ΠΈΠ·Π²Π΅ΡΡΠ½ΠΎΠΉ ΠΌΠ΅ΡΡ ΠΎΠ±ΡΠ΅ΠΌΠ°, ΠΏΠΎΠ·Π΄Π½Π΅Π΅ ΡΡΠΎΡ ΡΠ΅ΡΠΌΠΈΠ½ ΡΡΠ°Π» ΠΏΡΠΈΠΌΠ΅Π½ΡΡΡΡΡ ΠΊ ΡΠΏΠ΅ΡΠΈΠ°Π»ΡΠ½ΡΠΌ ΡΠΎΠΎΡΡΠΆΠ΅Π½ΠΈΡΠΌ Π²ΡΡΡΡΡΠΌ Π² Π·Π΅ΠΌΠ»Π΅ ΠΈΠ»ΠΈ ΠΏΠ΅ΡΠ΅ΡΠ΅, Π³Π΄Π΅ Ρ ΡΠ°Π½ΠΈΠ»ΠΎΡΡ Π·Π΅ΡΠ½ΠΎ ΠΈ ΡΠ°Π·Π»ΠΈΡΠ½ΡΠ΅ ΡΡΠΏΡΡΠΈΠ΅ ΠΌΠ°ΡΠ΅ΡΠΈΠ°Π»Ρ ΠΈ ΠΏΡΠΎΠ΄ΡΠΊΡΡ.
Π Π°Π·Π½ΠΎΠ²ΠΈΠ΄Π½ΠΎΡΡΡΡ ΡΡΠ°Π»ΡΠ½ΡΡ ΡΠΈΠ»ΠΎΡΠΎΠ² ΡΠ²Π»ΡΡΡΡΡ ΡΡΠ°Π»ΡΠ½ΡΠ΅ Π±ΡΠ½ΠΊΠ΅ΡΡ, ΠΊΠΎΡΠΎΡΡΠ΅ ΠΎΡΠ»ΠΈΡΠ°ΡΡΡΡ ΠΊΠΎΠ½ΡΡΡΡΠΊΡΠΈΠ²ΠΎΠΌ ΠΈ ΠΏΡΠΈΠΌΠ΅Π½ΡΡΡΡΡ Π² ΠΎΠΏΡΠ΅Π΄Π΅Π»ΡΠ½Π½ΡΡ ΠΎΠ±Π»Π°ΡΡΡΡ ΠΏΡΠΎΠΈΠ·Π²ΠΎΠ΄ΡΡΠ²Π°, Π½ΠΎ ΡΠ°ΠΊΠΆΠ΅ ΠΈΡΠΏΠΎΠ»ΡΠ·ΡΡΡΡΡ Π΄Π»Ρ Ρ ΡΠ°Π½Π΅Π½ΠΈΡ Π·Π΅ΡΠ½Π°, ΠΏΠ΅ΡΠΊΠ°, ΠΌΡΠΊΠΈ ΠΈ Ρ ΠΈΠΌΠΈΡΠ΅ΡΠΊΠΈΡ Π²Π΅ΡΠ΅ΡΡΠ² ΠΈ ΡΠ΄ΠΎΠ±ΡΠ΅Π½ΠΈΠΉ ΠΏΡΠΈΠΌΠ΅Π½ΡΠ΅ΠΌΡΡ Π² ΡΠ΅Π»ΡΡΠΊΠΎΠΌ Ρ ΠΎΠ·ΡΠΉΡΡΠ²Π΅.
ΠΡ ΠΏΡΠΎΠΈΠ·Π²ΠΎΠ΄ΠΈΠΌ ΡΠΈΠ»ΠΎΡΡ ΡΠ»Π΅Π΄ΡΡΡΠ΅Π³ΠΎ Π½Π°Π·Π½Π°ΡΠ΅Π½ΠΈΡ:
ΠΠ°Π·Π½Π°ΡΠ΅Π½ΠΈΠ΅ ΡΠΈΠ»ΠΎΡΠΎΠ²
Π‘ΠΈΠ»ΠΎΡΡ ΡΠ²Π»ΡΡΡΡΡ ΠΎΠ΄Π½ΠΈΠΌ ΠΈΠ· ΡΠ°ΠΌΡΡ ΡΠ°ΡΠΏΡΠΎΡΡΡΠ°Π½ΡΠ½Π½ΡΡ Π²ΠΈΠ΄ΠΎΠ² Π΅ΠΌΠΊΠΎΡΡΠ½ΠΎΠ³ΠΎ ΠΎΠ±ΠΎΡΡΠ΄ΠΎΠ²Π°Π½ΠΈΡ ΠΏΡΠ΅Π΄Π½Π°Π·Π½Π°ΡΠ΅Π½Π½ΠΎΠ³ΠΎ Π΄Π»Ρ Ρ ΡΠ°Π½Π΅Π½ΠΈΡ ΡΡΠΏΡΡΠΈΡ Π²Π΅ΡΠ΅ΡΡΠ² Π½Π° ΠΏΡΠΎΠΈΠ·Π²ΠΎΠ΄ΡΡΠ²Π΅. ΠΠ»Π°Π³ΠΎΠ΄Π°ΡΡ ΡΠ²ΠΎΠ΅ΠΉ ΠΊΠΎΠ½ΡΡΡΡΠΊΡΠΈΠΈ ΡΠΈΠ»ΠΎΡ ΠΏΠΎΠ·Π²ΠΎΠ»ΡΠ΅Ρ ΠΎΠΏΠ΅ΡΠ°ΡΠΈΠ²Π½ΠΎ ΠΏΡΠΎΠΈΠ·Π²ΠΎΠ΄ΠΈΡΡ ΠΊΠ°ΠΊ Π·Π°Π³ΡΡΠ·ΠΊΡ, ΡΠ°ΠΊ ΠΈ Π²ΡΠ³ΡΡΠ·ΠΊΡ ΡΠΎΠ΄Π΅ΡΠΆΠΈΠΌΠΎΠ³ΠΎ Ρ ΠΏΠΎΠΌΠΎΡΡΡ ΠΏΠ½Π΅Π²ΠΌΠ°ΡΠΈΡΠ΅ΡΠΊΠΈΡ Π½Π°ΡΠΎΡΠΎΠ² (Π² ΡΠ»ΡΡΠ°Π΅ Ρ ΡΡΠΏΡΡΠΈΠΌΠΈ ΠΌΠ°ΡΠ΅ΡΠΈΠ°Π»Π°ΠΌΠΈ) ΠΈΠ»ΠΈ ΠΏΠΎΡΡΠ΅Π΄ΡΡΠ²ΠΎΠΌ ΡΡΠ°Π½ΡΠΏΠΎΡΡΡΡΠ½ΠΎΠΉ Π»Π΅Π½ΡΡ ΠΏΡΠΎΠΈΠ·Π²ΠΎΠ΄ΠΈΡΡ Π·Π°Π³ΡΡΠ·ΠΊΡ, Π° Π²ΡΠ³ΡΡΠ·ΠΊΠ° ΠΏΡΠΎΠΈΡΡ ΠΎΠ΄ΠΈΡ ΠΏΡΡΡΠΌ ΠΎΡΠΊΡΡΡΠΈΡ ΠΎΠΊΠ½Π° ΡΡΡΠ°Π½ΠΎΠ²Π»Π΅Π½Π½ΠΎΠ³ΠΎ Π½Π° Π΄Π½ΠΈΡΠ΅ ΡΠΈΠ»ΠΎΡΠ°. Π‘ΠΈΠ»ΠΎΡΠ° ΠΏΠΎΠ·Π²ΠΎΠ»ΡΡΡ ΠΎΡΡΡΠ΅ΡΡΠ²Π»ΡΡΡ Π΄Π»ΠΈΡΠ΅Π»ΡΠ½ΠΎΠ΅ Ρ ΡΠ°Π½Π΅Π½ΠΈΠ΅ ΡΠΎΠ΄Π΅ΡΠΆΠΈΠΌΠΎΠ³ΠΎ, Ρ.ΠΊ. ΡΠΈΠ»ΠΎΡ Π² ΠΏΠ΅ΡΠ²ΡΡ ΠΎΡΠ΅ΡΠ΅Π΄Ρ ΠΏΡΠ΅Π΄ΡΡΠ°Π²Π»ΡΠ΅Ρ ΡΠΎΠ±ΠΎΠΉ Π·Π°ΠΊΡΡΡΡΡ Π²Π΅ΡΡΠΈΠΊΠ°Π»ΡΠ½ΡΡ Π΅ΠΌΠΊΠΎΡΡΡ Ρ ΠΊΠΎΠ½ΠΈΡΠ΅ΡΠΊΠΈΠΌ Π΄Π½ΠΎΠΌ, Π·Π°ΡΠΈΡΡΠ½Π½ΡΡ ΠΎΡ Π²Π½Π΅ΡΠ½ΠΈΡ Π²ΠΎΠ·Π΄Π΅ΠΉΡΡΠ²ΠΈΠΉ.
ΠΠ΅ΠΎΡΠΏΠΎΡΠΈΠΌΡΠΌ ΠΏΡΠ΅ΠΈΠΌΡΡΠ΅ΡΡΠ²ΠΎΠΌ ΡΡΠ°Π»ΡΠ½ΡΡ ΡΠΈΠ»ΠΎΡΠΎΠ² ΡΠ²Π»ΡΠ΅ΡΡΡ ΠΈΡ ΠΌΠ°ΡΡΡΠ°Π±ΠΈΡΡΠ΅ΠΌΠΎΡΡΡ. ΠΠ²ΠΈΠ΄Ρ ΡΠΎΠ³ΠΎ, ΡΡΠΎ ΡΠΈΠ»ΠΎΡ ΠΏΠΎ ΡΠΎΡΠΌΠ΅ ΠΏΡΠ΅Π΄ΡΡΠ°Π²Π»ΡΠ΅Ρ ΡΠΎΠ±ΠΎΠΉ Π²Π΅ΡΡΠΈΠΊΠ°Π»ΡΠ½ΡΡ ΡΠΌΠΊΠΎΡΡΡ, ΠΏΡΠΈ Π±ΠΎΠ»ΡΡΠΎΠΌ Ρ ΡΠ°Π½ΠΈΠΌΠΎΠΌ ΠΎΠ±ΡΡΠΌΠ΅ ΡΡΠΏΡΡΠΈΡ ΠΌΠ°ΡΠ΅ΡΠΈΠ°Π»ΠΎΠ² ΠΏΠ»ΠΎΡΠ°Π΄Ρ, Π·Π°Π½ΠΈΠΌΠ°Π΅ΠΌΠ°Ρ ΡΠΈΠ»ΠΎΡΠΎΠΌ Π½Π΅ΡΠΊΠΎΠ»ΡΠΊΠΎ ΠΊΠ²Π°Π΄ΡΠ°ΡΠ½ΡΡ ΠΌΠ΅ΡΡΠΎΠ². ΠΠ°ΠΏΡΠΈΠΌΠ΅Ρ ΡΡΠ°Π»ΡΠ½ΠΎΠΉ ΡΠΈΠ»ΠΎΡ ΠΎΠ±ΡΡΠΌΠΎΠΌ 100 ΠΊΡΠ±.ΠΌ. Π·Π°Π½ΠΈΠΌΠ°Π΅Ρ ΠΏΠ»ΠΎΡΠ°Π΄Ρ ΠΎΠΊΠΎΠ»ΠΎ 9 ΠΊΠ²Π°Π΄ΡΠ°ΡΠ½ΡΡ ΠΌΠ΅ΡΡΠΎΠ².
ΠΠΠ Β«ΠΠΠΒ» ΠΏΡΠΎΠΈΠ·Π²ΠΎΠ΄ΠΈΡ ΡΡΠ°Π»ΡΠ½ΡΠ΅ ΡΠΈΠ»ΠΎΡΡ Π΄Π»Ρ ΡΠ΅ΠΌΠ΅Π½ΡΠ°, ΡΠΈΠ»ΠΎΡΡ Π΄Π»Ρ Π·Π΅ΡΠ½Π°, ΡΠΈΠ»ΠΎΡΡ Π΄Π»Ρ ΠΌΡΠΊΠΈ, ΡΠΈΠ»ΠΎΡΡ Π΄Π»Ρ ΠΏΠ΅ΡΠΊΠ°, Π° ΡΠ°ΠΊΠΆΠ΅ ΠΊΠΎΠΌΠ±ΠΈΠΊΠΎΡΠΌΠ°, ΡΡΡΠΎΠΈΡΠ΅Π»ΡΠ½ΡΡ ΡΠΌΠ΅ΡΠ΅ΠΉ, ΡΠ°Π·Π»ΠΈΡΠ½ΡΡ ΡΠ΄ΠΎΠ±ΡΠ΅Π½ΠΈΠΉ ΠΈ ΠΏΡΠΎΡΠΈΡ ΡΡΠΏΡΡΠΈΡ Π²Π΅ΡΠ΅ΡΡΠ² ΠΈ ΠΌΠ°ΡΠ΅ΡΠΈΠ°Π»ΠΎΠ². ΠΠ°ΡΡΠ΄Ρ Ρ ΡΠ°Π·Π»ΠΈΡΠ½ΡΠΌΠΈ Π΅ΠΌΠΊΠΎΡΡΡΠΌΠΈ, ΡΠ΅Π·Π΅ΡΠ²ΡΠ°ΡΠ°ΠΌΠΈ ΠΈ Π±Π°ΠΊΠ°ΠΌΠΈ, ΡΡΠ°Π»ΡΠ½ΡΠ΅ ΡΠΈΠ»ΠΎΡΡ ΡΠ²Π»ΡΡΡΡΡ Π½Π΅ΡΡΠ°Π½Π΄Π°ΡΡΠ½ΡΠΌΠΈ ΠΌΠ΅ΡΠ°Π»Π»ΠΎΠΊΠΎΠ½ΡΡΡΡΠΊΡΠΈΡΠΌΠΈ, Π° Π·Π°ΡΠ°ΡΡΡΡ ΠΈ Π½Π΅Π³Π°Π±Π°ΡΠΈΡΠ½ΡΠΌΠΈ Π΅ΠΌΠΊΠΎΡΡΡΠΌΠΈ, ΡΡΠΎ ΡΡΠ΅Π±ΡΠ΅Ρ ΡΠΏΠ΅ΡΠΈΠ°Π»ΡΠ½ΡΡ ΡΡΠ»ΠΎΠ²ΠΈΠΉ ΡΡΠ°Π½ΡΠΏΠΎΡΡΠΈΡΠΎΠ²ΠΊΠΈ ΡΠΈΠ»ΠΎΡΠΎΠ² Π΄ΠΎ ΠΌΠ΅ΡΡΠ° Π½Π΅ΠΏΠΎΡΡΠ΅Π΄ΡΡΠ²Π΅Π½Π½ΠΎΠΉ ΡΠΊΡΠΏΠ»ΡΠ°ΡΠ°ΡΠΈΠΈ. Π‘ΠΏΡΠΎΡ Π½Π° ΡΡΠ°Π»ΡΠ½ΡΠ΅ ΡΠΈΠ»ΠΎΡΡ ΠΎΡΠ΅Π½Ρ Π²Π΅Π»ΠΈΠΊ, ΡΡΠΎ ΠΎΠ±ΡΡΠ»ΠΎΠ²Π»Π΅Π½ΠΎ Π±ΠΎΠ»ΡΡΠΈΠΌ ΠΊΠΎΠ»ΠΈΡΠ΅ΡΡΠ²ΠΎΠΌ ΡΠ°ΡΡΡΡΠΈΡ ΠΈ ΡΠ°ΡΡΠΈΡΡΡΡΠΈΡ ΡΡ ΠΏΡΠ΅Π΄ΠΏΡΠΈΡΡΠΈΠΉ, Π΄Π΅ΡΡΠ΅Π»ΡΠ½ΠΎΡΡΡ ΠΊΠΎΡΠΎΡΡΡ ΡΠ²ΡΠ·Π°Π½Π° Ρ ΠΏΡΠΎΠΈΠ·Π²ΠΎΠ΄ΡΡΠ²ΠΎΠΌ ΠΈΠ»ΠΈ Ρ ΡΠ°Π½Π΅Π½ΠΈΠ΅ΠΌ ΡΡΠΏΡΡΠΈΡ ΠΌΠ°ΡΠ΅ΡΠΈΠ°Π»ΠΎΠ² ΠΈ Π²Π΅ΡΠ΅ΡΡΠ². ΠΡΠΎΠΈΠ·Π²ΠΎΠ΄ΠΈΠΌΡΠ΅ ΡΠΈΠ»ΠΎΡΡ ΡΠ½Π°Π±ΠΆΠ΅Π½Ρ Π½Π΅ΠΎΠ±Ρ ΠΎΠ΄ΠΈΠΌΡΠΌΠΈ ΠΏΡΠΈΡΠΏΠΎΡΠΎΠ±Π»Π΅Π½ΠΈΡΠΌΠΈ ΠΈ ΡΡΡΡΠΎΠΉΡΡΠ²Π°ΠΌΠΈ (ΡΡΡΠ±Π½Π°Ρ ΠΎΠ±Π²ΡΠ·ΠΊΠ°), Π΄Π»Ρ ΡΠ΄ΠΎΠ±ΡΡΠ²Π° ΠΈΡ ΠΈΡΠΏΠΎΠ»ΡΠ·ΠΎΠ²Π°Π½ΠΈΡ Π² ΠΏΡΠΎΠΌΡΡΠ»Π΅Π½Π½ΠΎΡΡΠΈ ΡΠ²ΡΠ·Π°Π½Π½ΡΠΌΠΈ Ρ Ρ ΡΠ°Π½Π΅Π½ΠΈΠ΅ΠΌ ΡΡΠΏΡΡΠΈΡ Π²Π΅ΡΠ΅ΡΡΠ² ΠΈ ΠΈΡ ΠΏΠΎΠ³ΡΡΠ·ΠΊΠΎΠΉ. Π‘ΠΈΠ»ΠΎΡΡ ΠΈΠ·Π³ΠΎΡΠ°Π²Π»ΠΈΠ²Π°Π΅ΠΌΡΠ΅ Π½Π°ΡΠΈΠΌ ΠΏΡΠ΅Π΄ΠΏΡΠΈΡΡΠΈΠ΅ΠΌ ΠΎΠ±Π»Π°Π΄Π°ΡΡ Π²ΡΡΠΎΠΊΠΈΠΌ ΠΊΠ°ΡΠ΅ΡΡΠ²ΠΎΠΌ ΠΈ Π΄ΠΎΠ»Π³ΠΎΠ²Π΅ΡΠ½ΠΎΡΡΡΡ. ΠΠ° Π²ΡΠ΅ΠΌΡ Π½Π°ΡΠ΅ΠΉ ΡΠ°Π±ΠΎΡΡ ΡΠΈΠ»ΠΎΡΡ Π½Π°ΡΠ΅Π³ΠΎ ΠΏΡΠΎΠΈΠ·Π²ΠΎΠ΄ΡΡΠ²Π° ΡΡΡΠ°Π½ΠΎΠ²Π»Π΅Π½Ρ Π½Π° ΡΡΠ΄Π΅ ΠΏΡΠ΅Π΄ΠΏΡΠΈΡΡΠΈΠΉ Π ΠΎΡΡΠΈΠΈ ΠΈ ΡΡΡΠ°Π½ ΠΠ»ΠΈΠΆΠ½Π΅Π³ΠΎ ΠΠ°ΡΡΠ±Π΅ΠΆΡΡ, Π² ΡΠΎΠΌ ΡΠΈΡΠ»Π΅ ΠΈ Π² ΡΠ΅Π²Π΅ΡΠ½ΡΡ ΡΠ΅Π³ΠΈΠΎΠ½Π°Ρ .
ΠΠΎΠ½ΡΡΡΡΠΊΡΠΈΠ²Π½ΡΠ΅ ΠΎΡΠΎΠ±Π΅Π½Π½ΠΎΡΡΠΈ ΡΠΈΠ»ΠΎΡΠΎΠ²
Π§Π°ΡΠ΅ Π²ΡΠ΅Π³ΠΎ ΡΠΈΠ»ΠΎΡ ΠΈΠ·Π³ΠΎΡΠ°Π²Π»ΠΈΠ²Π°ΡΡ Π² Π²ΠΈΠ΄Π΅ ΡΠΈΠ»ΠΈΠ½Π΄ΡΠΈΡΠ΅ΡΠΊΠΎΠΉ Π²Π΅ΡΡΠΈΠΊΠ°Π»ΡΠ½ΠΎΠΉ Π΅ΠΌΠΊΠΎΡΡΠΈ ΠΈΠΌΠ΅ΡΡΠ΅ΠΉ ΠΊΠΎΠ½ΠΈΡΠ΅ΡΠΊΠΎΠ΅ Π΄Π½ΠΎ Ρ ΠΎΡΠ²Π΅ΡΡΡΠΈΠ΅ΠΌ Π΄Π»Ρ Π²ΡΠ³ΡΡΠ·ΠΊΠΈ ΡΠΎΠ΄Π΅ΡΠΆΠΈΠΌΠΎΠ³ΠΎ. Π‘Π½Π°ΡΡΠΆΠΈ ΡΠΈΠ»ΠΎΡ ΠΎΠ±ΠΎΡΡΠ΄ΠΎΠ²Π°Π½ Π½Π΅ΡΡΡΠΈΠΌΠΈ ΡΠ»Π΅ΠΌΠ΅Π½ΡΠ°ΠΌΠΈ (ΡΡΠ°Π»ΡΠ½ΠΎΠΉ ΠΊΠ°ΡΠΊΠ°Ρ ΠΈ ΠΎΡΠ½ΠΎΠ²Π°Π½ΠΈΠ΅), ΠΎΠ±ΠΎΡΡΠ΄ΠΎΠ²Π°Π½ΠΈΠ΅ΠΌ Π΄Π»Ρ Π΅Π³ΠΎ ΠΎΠ±ΡΠ»ΡΠΆΠΈΠ²Π°Π½ΠΈΡ (Π»Π΅ΡΡΠ½ΠΈΡΡ, ΠΏΠ΅ΡΠΈΠ»Π°, ΠΏΠΎΡΡΡΠ½ΠΈ ΠΈ Ρ.Π΄.), Π° ΡΠ°ΠΊΠΆΠ΅ ΡΠΏΠ΅ΡΠΈΠ°Π»ΡΠ½ΡΠΌΠΈ ΠΏΡΠΈΡΠΏΠΎΡΠΎΠ±Π»Π΅Π½ΠΈΡΠΌΠΈ Π΄Π»Ρ Π·Π°Π³ΡΡΠ·ΠΊΠΈ ΠΈ ΡΠ°Π·Π³ΡΡΠ·ΠΊΠΈ (Π·Π°Π΄Π²ΠΈΠΆΠΊΠΈ, Π½Π°ΡΠΎΡΡ ΠΈ Ρ.ΠΏ.). ΠΠΎ ΡΠΈΠ»ΠΎΡΡ Π½Π΅ ΠΎΠ³ΡΠ°Π½ΠΈΡΠΈΠ²Π°ΡΡΡΡ Π»ΠΈΡΡ ΡΠΈΠ»ΠΈΠ½Π΄ΡΠΈΡΠ΅ΡΠΊΠΎΠΉ ΡΠΎΡΠΌΠΎΠΉ, ΠΊ ΠΏΡΠΈΠΌΠ΅ΡΡ Π΄Π»Ρ Π°ΡΡΠ°Π»ΡΡΠΎΠ²ΠΎΠ³ΠΎ ΠΏΡΠΎΠΈΠ·Π²ΠΎΠ΄ΡΡΠ²ΠΎ ΠΈ Ρ ΡΠ°Π½Π΅Π½ΠΈΡ ΡΠ΄ΠΎΠ±ΡΠ΅Π½ΠΈΠΉ ΡΠ°ΡΡΠΎ ΠΈΡΠΏΠΎΠ»ΡΠ·ΡΡΡ ΡΡΠ°Π»ΡΠ½ΡΠ΅ ΡΠΈΠ»ΠΎΡΡ ΠΏΡΡΠΌΠΎΡΠ³ΠΎΠ»ΡΠ½ΠΎΠΉ ΡΠΎΡΠΌΡ.
ΠΡΠ΄Π΅Π»ΡΠ½ΠΎΠΉ ΡΠ°Π·Π½ΠΎΠ²ΠΈΠ΄Π½ΠΎΡΡΡΡ ΡΠΈΠ»ΠΎΡΠ° Π΄Π»Ρ Ρ ΡΠ°Π½Π΅Π½ΠΈΡ ΡΡΠΏΡΡΠΈΡ Π²Π΅ΡΠ΅ΡΡΠ² ΡΠ²Π»ΡΠ΅ΡΡΡ ΠΏΡΡΠΌΠΎΡΠ³ΠΎΠ»ΡΠ½ΡΠΉ Π±ΡΠ½ΠΊΠ΅Ρ.Β ΠΡΠ½ΠΊΠ΅ΡΠΎΠΌ Π½Π°Π·ΡΠ²Π°Π΅ΡΡΡ Π²ΠΌΠ΅ΡΡΠΈΠ»ΠΈΡΠ΅ Π΄Π»Ρ Π±Π΅ΡΡΠ°ΡΠ½ΠΎΠ³ΠΎ Ρ ΡΠ°Π½Π΅Π½ΠΈΡ ΡΡΠΏΡΡΠΈΡ ΠΈ ΠΊΡΡΠΊΠΎΠ²ΡΡ ΠΌΠ°ΡΠ΅ΡΠΈΠ°Π»ΠΎΠ², ΡΠ°Π·Π³ΡΡΠΆΠ°ΡΡΠ΅Π΅ΡΡ ΡΠ΅ΡΠ΅Π· Π½ΠΈΠΆΠ½ΡΡ ΡΠ°ΡΡΡ, ΠΎΠ±ΠΎΡΡΠ΄ΠΎΠ²Π°Π½Π½ΡΡ Π·Π°ΡΠ²ΠΎΡΠ°ΠΌΠΈ. Π’Π°ΠΊΠΎΠΉ Π±ΡΠ½ΠΊΠ΅Ρ ΡΠ°ΡΠ΅ Π²ΡΠ΅Π³ΠΎ ΠΏΡΠΈΠΌΠ΅Π½ΡΡΡ Π½Π° Π°ΡΡΠ°Π»ΡΡΠΎ-Π±Π΅ΡΠΎΠ½Π½ΠΎΠΌ ΠΏΡΠΎΠΈΠ·Π²ΠΎΠ΄ΡΡΠ²Π΅. ΠΡΡΠΌΠΎΡΠ³ΠΎΠ»ΡΠ½Π°Ρ ΡΠΎΡΠΌΠ° ΡΠΈΠ»ΠΎΡΠ° ΠΎΠ±ΡΡΠ»ΠΎΠ²Π»Π΅Π½Π° ΡΠ΅ΠΌ, ΡΡΠΎ Π·Π°Π³ΡΡΠ·ΠΊΠ° Π²Π΅ΡΠ΅ΡΡΠ² ΠΈ ΠΌΠ°ΡΠ΅ΡΠΈΠ°Π»ΠΎΠ² ΠΏΡΠΎΠΈΡΡ ΠΎΠ΄ΠΈΡ ΡΠ²Π΅ΡΡ Ρ ΡΠΊΡΠΊΠ°Π²Π°ΡΠΎΡΠΎΠΌ ΠΈΠ»ΠΈ Π±ΡΠ»ΡΠ΄ΠΎΠ·Π΅ΡΠΎΠΌ, ΠΈ Π² ΡΠ²ΡΠ·ΠΈ Ρ ΡΡΠΈΠΌ ΠΏΡΡΠΌΠΎΡΠ³ΠΎΠ»ΡΠ½ΡΠΉ ΡΠΈΠ»ΠΎΡ ΠΏΠΎΠ·Π²ΠΎΠ»ΡΠ΅Ρ ΠΏΠΎΠ»ΡΡΠΈΡΡ Π±ΠΎΠ»ΡΡΠΈΠΉ ΡΠ°Π·ΠΌΠ΅Ρ Π·Π°Π³ΡΡΠ·ΠΎΡΠ½ΠΎΠ³ΠΎ ΠΎΠΊΠ½Π° ΠΈ Π½Π΅ ΡΡΠ΅Π±ΡΠ΅Ρ ΠΈΠ·Π³ΠΎΡΠΎΠ²Π»Π΅Π½ΠΈΡ ΡΠΏΠ΅ΡΠΈΠ°Π»ΡΠ½ΠΎΠΉ Π²ΠΎΡΠΎΠ½ΠΊΠΈ Π΄Π»Ρ ΡΠ²Π΅Π»ΠΈΡΠ΅Π½ΠΈΡ ΠΏΠ»ΠΎΡΠ°Π΄ΠΈ Π·Π°Π³ΡΡΠ·ΠΎΡΠ½ΠΎΠ³ΠΎ ΠΎΠΊΠ½Π°.
Π Π°Π·Π³ΡΡΠ·ΠΊΠ° Π±ΡΠ½ΠΊΠ΅ΡΠ° ΠΎΡΡΡΠ΅ΡΡΠ²Π»ΡΠ΅ΡΡΡ Π³ΡΠ°Π²ΠΈΡΠ°ΡΠΈΠΎΠ½Π½ΡΠΌ ΡΠΏΠΎΡΠΎΠ±ΠΎΠΌ (ΡΠ°ΠΌΠΎΡΡΠΊΠΎΠΌ), Π½ΠΎ Π² ΠΎΡΠΎΠ±ΡΡ ΡΠ»ΡΡΠ°ΡΡ ΠΏΡΠΈΠ±Π΅Π³Π°ΡΡ ΠΊ ΠΏΡΠΈΠ½ΡΠ΄ΠΈΡΠ΅Π»ΡΠ½ΡΠΌ ΡΠΏΠΎΡΠΎΠ±Π°ΠΌ ΡΠ°Π·Π³ΡΡΠ·ΠΊΠΈ.
ΠΡΠ½ΠΊΠ΅ΡΠ° ΠΏΠΎΠ»ΡΡΠΈΠ»ΠΈ ΡΠΈΡΠΎΠΊΠΎΠ΅ ΡΠ°ΡΠΏΡΠΎΡΡΡΠ°Π½Π΅Π½ΠΈΠ΅ Π½Π° ΡΡΠ°Π½ΡΠΏΠΎΡΡΠ΅ ΠΈ Π² ΠΏΡΠΎΠΌΡΡΠ»Π΅Π½Π½ΠΎΡΡΠΈ. ΠΠ° ΡΡΠ°Π½ΡΠΏΠΎΡΡΠ΅ ΠΈΡ ΠΏΡΠΈΠΌΠ΅Π½ΡΡΡ Π² ΠΆΠ΅Π»Π΅Π·Π½ΠΎΠ΄ΠΎΡΠΎΠΆΠ½ΡΡ Π±ΡΠ½ΠΊΠ΅ΡΠ½ΡΡ ΡΡΡΠ°ΠΊΠ°Π΄Π°Ρ , ΠΏΡΠΈΡΠ΅Π»ΡΡΠΎΠ²ΡΡ ΠΈ ΠΏΠΎΡΡΠΎΠ²ΡΡ ΡΠΊΠ»Π°Π΄Π°Ρ ΡΡΠΏΡΡΠΈΡ ΠΌΠ°ΡΠ΅ΡΠΈΠ°Π»ΠΎΠ².
Π ΠΏΡΠΎΠΌΡΡΠ»Π΅Π½Π½ΠΎΡΡΠΈ Π±ΡΠ½ΠΊΠ΅Ρ ΠΎΠ±ΡΡΠ½ΠΎ ΡΠ²Π»ΡΠ΅ΡΡΡ ΡΠΎΡΡΠ°Π²Π½ΠΎΠΉ ΡΠ°ΡΡΡΡ ΡΠ΅Ρ Π½ΠΎΠ»ΠΎΠ³ΠΈΡΠ΅ΡΠΊΠΎΠ³ΠΎ ΠΏΡΠΎΡΠ΅ΡΡΠ°, Π³Π΄Π΅ ΠΎΠ½ Π²ΡΠΏΠΎΠ»Π½ΡΠ΅Ρ ΠΏΠΎ ΠΊΡΠ°ΠΉΠ½Π΅ΠΉ ΠΌΠ΅ΡΠ΅ ΡΡΠΈ ΡΡΠ½ΠΊΡΠΈΠΈ: Π°ΠΊΠΊΡΠΌΡΠ»ΠΈΡΠΎΠ²Π°Π½ΠΈΠ΅, ΡΠ°ΡΠΏΡΠ΅Π΄Π΅Π»Π΅Π½ΠΈΠ΅ ΠΈ ΡΡΡΠ΅Π΄Π½Π΅Π½ΠΈΠ΅ ΡΡΠΏΡΡΠ΅Π³ΠΎ ΠΌΠ°ΡΠ΅ΡΠΈΠ°Π»Π°.
ΠΠΎ ΠΌΠ°ΡΠ΅ΡΠΈΠ°Π»Ρ ΠΊΠΎΠ½ΡΡΡΡΠΊΡΠΈΠΉ Π±ΡΠ½ΠΊΠ΅ΡΠ° Π±ΡΠ²Π°ΡΡ ΡΡΠ°Π»ΡΠ½ΡΠ΅, ΠΆΠ΅Π»Π΅Π·ΠΎΠ±Π΅ΡΠΎΠ½Π½ΡΠ΅ ΠΊΠΎΠΌΠ±ΠΈΠ½ΠΈΡΠΎΠ²Π°Π½Π½ΡΠ΅ ΠΈ ΡΠ΅ΠΆΠ΅ Π΄Π΅ΡΠ΅Π²ΡΠ½Π½ΡΠ΅. Π‘ΡΠ°Π»ΡΠ½ΡΠ΅ Π±ΡΠ½ΠΊΠ΅ΡΠ° Π½Π°ΠΈΠ±ΠΎΠ»Π΅Π΅ ΡΠΊΠΎΠ½ΠΎΠΌΠΈΡΠ½Ρ ΠΈ ΠΈΠ½Π΄ΡΡΡΡΠΈΠ°Π»ΡΠ½Ρ. ΠΡ ΠΏΡΠΎΡΠ΅ ΡΠ΅Π°Π»ΠΈΠ·ΠΎΠ²Π°ΡΡ ΠΈ ΡΠΊΡΠΏΠ»ΡΠ°ΡΠΈΡΠΎΠ²Π°ΡΡ, Π² ΡΠΎΠΌ ΡΠΈΡΠ»Π΅ Π½Π° ΡΡΠ°Π½ΡΠΏΠΎΡΡΠ½ΡΡ ΡΡΠ΅Π΄ΡΡΠ²Π°Ρ .
ΠΠ°ΠΈΠ±ΠΎΠ»ΡΡΠ΅Π΅ ΡΠ°ΡΠΏΡΠΎΡΡΡΠ°Π½Π΅Π½ΠΈΠ΅ ΠΏΠΎΠ»ΡΡΠΈΠ»ΠΈ ΠΏΠΈΡΠ°ΠΌΠΈΠ΄Π°Π»ΡΠ½ΠΎ — ΠΏΡΠΈΠ·ΠΌΠ°ΡΠΈΡΠ΅ΡΠΊΠΈΠ΅ ΡΡΠ°Π»ΡΠ½ΡΠ΅ Π±ΡΠ½ΠΊΠ΅ΡΠ°, ΠΊΠ°ΠΊ Π½Π°ΠΈΠ±ΠΎΠ»Π΅Π΅ ΠΏΡΠΎΡΡΡΠ΅ ΠΈ Π΄ΠΎΡΡΡΠΏΠ½ΡΠ΅. ΠΠ½ΠΈ ΠΎΡΠ½ΠΎΡΡΡΡΡ ΠΊ ΡΠ°Π·ΡΡΠ΄Ρ ΡΠΎΡΠ΅ΡΠ½ΡΡ , ΠΈΠΌΠ΅ΡΡ ΠΎΠ³ΡΠ°Π½ΠΈΡΠ΅Π½Π½ΡΡ ΡΠΌΠΊΠΎΡΡΡ ( Π΄ΠΎ 1000 Ρ ), ΠΏΠΎΡΡΠΎΠΌΡ ΡΠ°ΡΡΠΎ ΠΈΡΠΏΠΎΠ»ΡΠ·ΡΡΡΡΡ Π² ΠΌΠ½ΠΎΠ³ΠΎΡΡΠ΅ΠΉΠΊΠΎΠ²ΡΡ ΡΠΈΡΡΠ΅ΠΌΠ°Ρ .
ΠΡΠΎΠΈΠ·Π²ΠΎΠ΄ΡΡΠ²ΠΎ ΡΠΈΠ»ΠΎΡΠΎΠ²
ΠΡΠΎΠΈΠ·Π²ΠΎΠ΄ΡΡΠ²ΠΎ ΡΠΈΠ»ΠΎΡΠΎΠ² Π΄Π»Ρ Ρ ΡΠ°Π½Π΅Π½ΠΈΡ ΡΡΠΏΡΡΠΈΡ Π²Π΅ΡΠ΅ΡΡΠ² ΠΈ ΠΌΠ°ΡΠ΅ΡΠΈΠ°Π»ΠΎΠ² ΠΈΠΌΠ΅Π΅Ρ Π² ΡΠ²ΠΎΠ΅ΠΉ ΠΎΡΠ½ΠΎΠ²Π΅ ΡΡΠ΄ ΡΠ΅Ρ Π½ΠΎΠ»ΠΎΠ³ΠΈΡΠ΅ΡΠΊΠΈΡ ΠΏΠΎΠ΄Ρ ΠΎΠ΄ΠΎΠ², ΠΊΠΎΡΠΎΡΡΠ΅ ΠΏΠΎΠ·Π²ΠΎΠ»ΡΡΡ ΠΎΠ±Π΅ΡΠΏΠ΅ΡΠΈΡΡ ΠΈΡ ΡΠΊΡΠΏΠ»ΡΠ°ΡΠ°ΡΠΈΡ Π±Π΅Π· ΠΏΠΎΡΠ΅ΡΡ ΠΈ Π°Π²Π°ΡΠΈΠΉ. Π ΠΎΡΠ»ΠΈΡΠΈΠΈ ΠΎΡ ΠΎΠ±ΡΡΠ½ΡΡ Π΅ΠΌΠΊΠΎΡΡΠ΅ΠΉ Π΄Π»Ρ Ρ ΡΠ°Π½Π΅Π½ΠΈΡ ΠΆΠΈΠ΄ΠΊΠΎΡΡΠ΅ΠΉ Π½Π΅ΠΎΠ±Ρ ΠΎΠ΄ΠΈΠΌΠΎ ΠΎΠ±Π΅ΡΠΏΠ΅ΡΠΈΡΡ Π±Π΅ΡΠΏΡΠ΅ΠΏΡΡΡΡΠ²Π΅Π½Π½ΠΎΠ΅ Π΄Π²ΠΈΠΆΠ΅Π½ΠΈΠ΅ ΡΠΎΠ΄Π΅ΡΠΆΠΈΠΌΠΎΠ³ΠΎ ΠΏΠΎ ΡΠΈΠ»ΠΎΡΡ, Π΅Π³ΠΎ Π²ΡΠ΄Π°ΡΡ ΠΈ Ρ ΡΠ°Π½Π΅Π½ΠΈΠ΅. ΠΡΠΎΡΠ΅ΡΡ ΠΈΠ·Π³ΠΎΡΠΎΠ²Π»Π΅Π½ΠΈΡ ΡΡΠ°Π»ΡΠ½ΠΎΠ³ΠΎ ΡΠΈΠ»ΠΎΡΠ° ΠΈΠΌΠ΅Π΅Ρ ΡΠ²ΠΎΠΈ Ρ Π°ΡΠ°ΠΊΡΠ΅ΡΠ½ΡΠ΅ ΠΎΡΠ»ΠΈΡΠΈΡ.
ΠΡ ΠΏΡΠΎΠΈΠ·Π²ΠΎΠ΄ΠΈΠΌ ΡΠΈΠ»ΠΎΡΡ ΠΊΠ°ΠΊ Π΄Π»Ρ Π²Π½ΡΡΡΠ΅Π½Π½Π΅Π³ΠΎ ΡΠ°Π·ΠΌΠ΅ΡΠ΅Π½ΠΈΡ Π² ΡΠ΅Ρ Π°Ρ , ΡΠ°ΠΊ ΠΈ Π΄Π»Ρ Π½Π°ΡΡΠΆΠ½ΠΎΠ³ΠΎ ΡΠ°Π·ΠΌΠ΅ΡΠ΅Π½ΠΈΡ ΠΏΠΎΠ΄ ΠΎΡΠΊΡΡΡΡΠΌ Π½Π΅Π±ΠΎΠΌ. Π’Π°ΠΊΠΆΠ΅ ΠΌΡ Π³ΠΎΡΠΎΠ²Ρ ΠΏΡΠ΅Π΄Π»ΠΎΠΆΠΈΡΡ ΠΈ ΡΠ±ΠΎΡΠ½ΡΠ΅ ΡΠΈΠ»ΠΎΡΡ, ΡΠ΅ΠΊΡΠΈΠΈ ΠΊΠΎΡΠΎΡΠΎΠ³ΠΎ ΠΈΠΌΠ΅ΡΡ Π±ΠΎΠ»ΡΠΎΠ²ΠΎΠ΅ ΡΠΎΠ΅Π΄ΠΈΠ½Π΅Π½ΠΈΠ΅.
Π‘ΠΈΠ»ΠΎΡΡ Π΄Π»Ρ ΡΠ΅ΠΌΠ΅Π½ΡΠ° ΠΈ ΠΏΠΎΡΡΡΠΎΠ΅Π½ΠΈΡ ΡΠ΅ΠΌΠ΅Π½ΡΠ½ΡΡ Ρ ΡΠ°Π½ΠΈΠ»ΠΈΡ
Π‘ΠΈΠ»ΠΎΡΡ Π΄Π»Ρ ΡΠ΅ΠΌΠ΅Π½ΡΠ° ΡΠ²Π»ΡΡΡΡΡ ΠΎΠ΄Π½ΠΈΠΌ ΠΈΠ· ΠΏΡΠΈΠΎΡΠΈΡΠ΅ΡΠ½ΡΡ
Π½Π°ΠΏΡΠ°Π²Π»Π΅Π½ΠΈΠΉ ΠΏΡΠΎΠΈΠ·Π²ΠΎΠ΄ΡΡΠ²Π° Π΅ΠΌΠΊΠΎΡΡΠ½ΠΎΠ³ΠΎ ΠΎΠ±ΠΎΡΡΠ΄ΠΎΠ²Π°Π½ΠΈΡ, ΠΏΡΠ΅Π΄Π½Π°Π·Π½Π°ΡΠ΅Π½Π½ΡΡ
Π΄Π»Ρ ΠΏΠΎΡΡΡΠΎΠ΅Π½ΠΈΡ Ρ
ΡΠ°Π½ΠΈΠ»ΠΈΡ ΡΠ΅ΠΌΠ΅Π½ΡΠ° Π½Π° ΠΏΡΠΎΠΈΠ·Π²ΠΎΠ΄ΡΡΠ²Π΅ ΠΈ ΡΡΡΠΎΠΈΡΠ΅Π»ΡΡΡΠ²Π΅.
Π¦Π΅ΠΌΠ΅Π½Ρ — ΡΡΠΎ Π²Π΅ΡΠ΅ΡΡΠ²ΠΎ, ΠΊΠΎΡΠΎΡΠΎΠ΅ ΠΏΡΠΈΡ ΠΎΠ΄ΠΈΡ Π² Π½Π΅Π³ΠΎΠ΄Π½ΠΎΡΡΡ, Π΅ΡΠ»ΠΈ Ρ ΡΠ°Π½ΠΈΡΡΡ ΠΏΡΠΈ Π²ΡΡΠΎΠΊΠΎΠΉ Π²Π»Π°ΠΆΠ½ΠΎΡΡΠΈ ΠΈΠ»ΠΈ Π²ΠΎΠΎΠ±ΡΠ΅ Π² ΡΡΡΠΎΠΌ ΠΏΠΎΠΌΠ΅ΡΠ΅Π½ΠΈΠΈ ΠΈΠ»ΠΈ ΡΡΡΠΎΠΉ Π΅ΠΌΠΊΠΎΡΡΠΈ. ΠΠΎΡΡΠΎΠΌΡ Π΄Π»Ρ Ρ ΡΠ°Π½Π΅Π½ΠΈΡ ΡΠ΅ΠΌΠ΅Π½ΡΠ° ΠΎΠΏΡΠΈΠΌΠ°Π»ΡΠ½ΠΎ ΠΏΠΎΠ΄Ρ ΠΎΠ΄ΠΈΡ ΡΡΠ°Π»ΡΠ½ΠΎΠΉ ΡΠΈΠ»ΠΎΡ Π΄Π»Ρ ΡΠ΅ΠΌΠ΅Π½ΡΠ°, ΠΊΠΎΡΠΎΡΡΠΉ ΠΏΠΎΠ·Π²ΠΎΠ»ΡΠ΅Ρ Ρ ΡΠ°Π½ΠΈΡΡ, Π²ΡΠ³ΡΡΠΆΠ°ΡΡ ΠΈ Π·Π°Π³ΡΡΠΆΠ°ΡΡ ΡΠ΅ΠΌΠ΅Π½Ρ ΠΏΡΠ΅Π΄ΠΎΡΠ²ΡΠ°ΡΠ°Ρ Π΅Π³ΠΎ ΡΠΎΠΏΡΠΈΠΊΠΎΡΠ½ΠΎΠ²Π΅Π½ΠΈΠ΅ Ρ ΠΎΠΊΡΡΠΆΠ°ΡΡΠ΅ΠΉ ΡΡΠ΅Π΄ΠΎΠΉ, Π° ΡΠ°ΠΊΠΆΠ΅ ΠΏΡΠΈ ΠΏΡΠΎΠΈΠ·Π²ΠΎΠ΄ΡΡΠ²Π΅ ΡΠ°Π·Π»ΠΈΡΠ½ΡΡ ΠΆΠ΅Π»Π΅Π·ΠΎΠ±Π΅ΡΠΎΠ½Π½ΡΡ ΠΈΠ·Π΄Π΅Π»ΠΈΠΉ ΠΏΠΎΠ·Π²ΠΎΠ»ΡΠ΅Ρ ΠΏΠΎΠ΄Π°Π²Π°ΡΡ ΡΠ΅ΠΌΠ΅Π½Ρ ΠΈ ΠΏΠ΅ΡΠΎΠΊ Π² Π΅ΠΌΠΊΠΎΡΡΡ Π΄Π»Ρ ΡΠΌΠ΅ΡΠΈΠ²Π°Π½ΠΈΡ. ΠΠ°ΠΊΡΡΡΠΎΡΡΡ — ΡΡΠΎ Π΄ΠΎΡΡΠΎΠΈΠ½ΡΡΠ²ΠΎ ΡΠΈΠ»ΠΎΡΠΎΠ² ΠΈΠΌΠ΅Π΅Ρ Π±ΠΎΠ»ΡΡΠΎΠ΅ Π·Π½Π°ΡΠ΅Π½ΠΈΠ΅ ΠΏΡΠΈ Ρ ΡΠ°Π½Π΅Π½ΠΈΠΈ ΡΠ΅ΠΌΠ΅Π½ΡΠ°, Ρ.ΠΊ. ΠΏΠΎΠ΄ Π²ΠΎΠ·Π΄Π΅ΠΉΡΡΠ²ΠΈΠ΅ΠΌ Π²Π»Π°Π³ΠΈ ΡΠ΅ΠΌΠ΅Π½Ρ ΡΡΠ°Π½ΠΎΠ²ΠΈΡΡΡ Π½Π΅ΠΏΡΠΈΠ³ΠΎΠ΄Π½ΡΠΌ Π΄Π»Ρ Π΄Π°Π»ΡΠ½Π΅ΠΉΡΠ΅Π³ΠΎ ΠΈΡΠΏΠΎΠ»ΡΠ·ΠΎΠ²Π°Π½ΠΈΡ. Π’.ΠΎ. ΡΠΈΠ»ΠΎΡ Π΄Π»Ρ Ρ ΡΠ°Π½Π΅Π½ΠΈΡ Π±ΠΎΠ»ΡΡΠΈΡ ΠΎΠ±ΡΡΠΌΠΎΠ² ΡΠ΅ΠΌΠ΅Π½ΡΠ° ΠΏΠΎΠ·Π²ΠΎΠ»ΡΠ΅Ρ Ρ ΡΠ°Π½ΠΈΡΡ ΡΠ΅ΠΌΠ΅Π½Ρ, ΠΎΡΠ³ΡΡΠΆΠ°ΡΡ Π΅Π³ΠΎ Π² Π°Π²ΡΠΎΠΌΠ°ΡΠΈΠ½Ρ Π΄Π»Ρ ΡΡΠ°Π½ΡΠΏΠΎΡΡΠΈΡΠΎΠ²ΠΊΠΈ Π±Π΅Π· ΡΠΎΠΏΡΠΈΠΊΠΎΡΠ½ΠΎΠ²Π΅Π½ΠΈΡ Ρ ΠΎΠΊΡΡΠΆΠ°ΡΡΠ΅ΠΉ ΡΡΠ΅Π΄ΠΎΠΉ. ΠΡΠΈ ΠΏΡΠΎΠΈΠ·Π²ΠΎΠ΄ΡΡΠ²Π΅ ΡΡΡΠΎΠΈΡΠ΅Π»ΡΠ½ΡΡ ΠΌΠ°ΡΠ΅ΡΠΈΠ°Π»ΠΎΠ² ΠΈΠ»ΠΈ Π±Π΅ΡΠΎΠ½Π° ΡΠΈΠ»ΠΎΡΡ ΠΈΡΠΏΠΎΠ»ΡΠ·ΡΡΡ Π² ΠΊΠ°ΡΠ΅ΡΡΠ²Π΅ Π΅ΠΌΠΊΠΎΡΡΠΈ, ΠΊΠΎΡΠΎΡΠ°Ρ ΠΏΠΎΠ·Π²ΠΎΠ»ΡΠ΅Ρ Π΄ΠΎΠ·ΠΈΡΠΎΠ²Π°ΡΡ ΠΎΠ±ΡΡΠΌ Π·Π°Π³ΡΡΠΆΠ°Π΅ΠΌΠΎΠΉ ΠΌΠ°ΡΡΡ Π±Π΅ΡΠΎΠ½Π° Π² ΡΠΎΡΠΌΡ ΠΈΠ»ΠΈ Π°Π²ΡΠΎΠΌΠ°ΡΠΈΠ½Ρ. ΠΠ»Π°Π³ΠΎΠ΄Π°ΡΡ ΡΠ²ΠΎΠ±ΠΎΠ΄Π½ΠΎΠΉ ΠΌΠ°ΡΡΡΠ°Π±ΠΈΡΡΠ΅ΠΌΠΎΡΡΠΈ ΡΠΈΠ»ΠΎΡΡ Π΄Π»Ρ ΡΠ΅ΠΌΠ΅Π½ΡΠ°, ΠΊΠ°ΠΊ ΠΈ Π΄ΡΡΠ³ΠΈΠ΅ ΡΠΈΠ»ΠΎΡΡ, ΠΏΠΎΠ·Π²ΠΎΠ»ΡΡΡ ΡΡΡΠΎΠΈΡΡ ΡΠ΅ΠΌΠ΅Π½ΡΠ½ΡΠ΅ Ρ ΡΠ°Π½ΠΈΠ»ΠΈΡΠ° Π½Π΅ΠΎΠ³ΡΠ°Π½ΠΈΡΠ΅Π½Π½ΠΎΠ³ΠΎ ΠΎΠ±ΡΡΠΌΠ° ΠΈ ΠΏΡΠΈ ΡΡΠΎΠΌ Π·Π°Π½ΠΈΠΌΠ°ΡΡ Π½Π΅Π±ΠΎΠ»ΡΡΡΡ ΠΏΠ»ΠΎΡΠ°Π΄Ρ.
Π‘ΠΈΠ»ΠΎΡΡ Π΄Π»Ρ Π·Π΅ΡΠ½Π° ΠΈ ΡΡΡΠΎΠΈΡΠ΅Π»ΡΡΡΠ²Π° ΡΠ»Π΅Π²Π°ΡΠΎΡΠΎΠ²
Π¨ΠΈΡΠΎΠΊΠΎΠ΅ ΠΏΡΠΈΠΌΠ΅Π½Π΅Π½ΠΈΠ΅ ΡΠΈΠ»ΠΎΡΡ ΠΏΠΎΠ»ΡΡΠΈΠ»ΠΈ Π΄Π»Ρ Ρ ΡΠ°Π½Π΅Π½ΠΈΡ Π·Π΅ΡΠ½Π°, Ρ ΠΈΡ ΠΏΠΎΠΌΠΎΡΡΡ ΠΏΡΠΎΠΈΠ·Π²ΠΎΠ΄ΠΈΡΡΡ ΠΏΠΎΡΡΡΠΎΠ΅Π½ΠΈΠ΅ Π·Π΅ΡΠ½ΠΎΡ ΡΠ°Π½ΠΈΠ»ΠΈΡ Π»ΡΠ±ΡΡ ΠΎΠ±ΡΡΠΌΠΎΠ². Π ΠΎΡΠ»ΠΈΡΠΈΠΈ ΠΎΡ Π΄ΡΡΠ³ΠΈΡ ΡΠΏΠΎΡΠΎΠ±ΠΎΠ² Ρ ΡΠ°Π½Π΅Π½ΠΈΡ Π·Π΅ΡΠ½Π°, Ρ ΡΠ°Π½Π΅Π½ΠΈΠ΅ Π·Π΅ΡΠ½Π° Π² ΡΠΈΠ»ΠΎΡΠ°Ρ ΠΏΠΎΠ·Π²ΠΎΠ»ΡΠ΅Ρ Π±Π΅Π· Π»ΠΈΡΠ½Π΅Π³ΠΎ ΠΎΠ±ΠΎΡΡΠ΄ΠΎΠ²Π°Π½ΠΈΡ ΠΎΡΠ³ΡΡΠΆΠ°ΡΡ Π·Π΅ΡΠ½ΠΎ Π½Π΅ΠΏΠΎΡΡΠ΅Π΄ΡΡΠ²Π΅Π½Π½ΠΎ Π² Π°Π²ΡΠΎΠΌΠ°ΡΠΈΠ½Ρ ΠΈ ΡΡΠ°Π½ΡΠΏΠΎΡΡΠΈΡΠΎΠ²Π°ΡΡ Π΅Π³ΠΎ Π΄ΠΎ ΠΌΠ΅ΡΡΠ° ΠΏΠ΅ΡΠ΅ΡΠ°Π±ΠΎΡΠΊΠΈ. ΠΡΠΈ ΡΡΠΎΠΌ Π·Π΅ΡΠ½ΠΎΠ²ΡΠ΅ ΡΠΈΠ»ΠΎΡΡ Π½Π°Π΄ΡΠΆΠ½ΠΎ Π·Π°ΡΠΈΡΠ°ΡΡ ΡΠΎΠ΄Π΅ΡΠΆΠΈΠΌΠΎΠ΅ ΠΎΡ Π²Π½Π΅ΡΠ½ΠΈΡ Π²ΠΎΠ·Π΄Π΅ΠΉΡΡΠ²ΠΈΠΉ.
Π‘ΠΈΠ»ΠΎΡΡ ΡΡΠ°Π»ΠΈ ΠΎΡΠ½ΠΎΠ²Π½ΡΠΌ Ρ ΡΠ°Π½ΠΈΠ»ΠΈΡΠ΅ΠΌ Π·Π΅ΡΠ½Π° Π½Π° ΡΠ»Π΅Π²Π°ΡΠΎΡΠ°Ρ , Ρ.ΠΊ. ΠΏΠΎΠ·Π²ΠΎΠ»ΡΡΡ Π±Π΅Π· Π»ΠΈΡΠ½ΠΈΡ Π·Π°ΡΡΠ°Ρ Π·Π°Π³ΡΡΠΆΠ°ΡΡ ΠΈ Π²ΡΠ³ΡΡΠΆΠ°ΡΡ Π·Π΅ΡΠ½ΠΎ Ρ ΠΏΠΎΠΌΠΎΡΡΡ ΠΏΠΎΠ³ΡΡΠ·ΠΎΡΠ½ΠΎΠ³ΠΎ ΡΡΠΊΠ°Π²Π°, Π·Π°ΡΠΈΡΠ°ΡΡ Π΅Π³ΠΎ ΠΎΡ Π²Π½Π΅ΡΠ½ΠΈΡ ΠΊΠ»ΠΈΠΌΠ°ΡΠΈΡΠ΅ΡΠΊΠΈΡ Π²ΠΎΠ·Π΄Π΅ΠΉΡΡΠ²ΠΈΠΉ. ΠΠ΅ΡΡΠΏΠΎΡΠ½ΡΠΌ ΠΏΡΠΈΠ΅ΠΌΡΡΠ΅ΡΡΠ²ΠΎΠΌ ΡΠ²Π»ΡΠ΅ΡΡΡ ΠΌΠ°ΡΡΡΠ°Π±ΠΈΡΡΠ΅ΠΌΠΎΡΡΡ Π·Π΅ΡΠ½ΠΎΡ ΡΠ°Π½ΠΈΠ»ΠΈΡ Ρ ΠΈΡΠΏΠΎΠ»ΡΠ·ΠΎΠ²Π°Π½ΠΈΠ΅ΠΌ ΡΠΈΠ»ΠΎΡΠΎΠ², Ρ.ΠΊ. ΠΏΡΠΈ Π½Π΅ΠΎΠ±Ρ ΠΎΠ΄ΠΈΠΌΠΎΡΡΠΈ ΠΌΠΎΠΆΠ½ΠΎ ΡΡΡΠ°Π½ΠΎΠ²ΠΈΡΡ Π»ΡΠ±ΠΎΠ΅ ΠΊΠΎΠ»ΠΈΡΠ΅ΡΡΠ²ΠΎ Π½ΠΎΠ²ΡΡ ΡΠΈΠ»ΠΎΡΠΎΠ². Π’Π°ΠΊΠΈΠΌ ΠΎΠ±ΡΠ°Π·ΠΎΠΌ ΠΏΡΠΈ Π½Π΅Π±ΠΎΠ»ΡΡΠΈΡ Π·Π°Π½ΠΈΠΌΠ°Π΅ΠΌΡΡ ΠΏΠ»ΠΎΡΠ°Π΄ΡΡ ΠΌΠΎΠΆΠ½ΠΎ ΡΠΎΠ·Π΄Π°Π²Π°ΡΡ Π±ΠΎΠ»ΡΡΠΈΠ΅ ΡΠ»Π΅Π²Π°ΡΠΎΡΠ½ΡΠ΅ Ρ ΡΠ°Π½ΠΈΠ»ΠΈΡΠ°, Ρ.ΠΊ. ΡΠΈΠ»ΠΎΡ ΡΡΠΎ Π²Π΅ΡΡΠΈΠΊΠ°Π»ΡΠ½ΡΠΉ ΡΠ΅Π·Π΅ΡΠ²ΡΠ°Ρ ΡΡΠ΅Π±ΡΡΡΠΈΠΉ Π½Π΅Π±ΠΎΠ»ΡΡΠΎΠΉ ΠΏΠ»ΠΎΡΠ°Π΄ΠΈ Π΄Π»Ρ ΡΡΡΠ°Π½ΠΎΠ²ΠΊΠΈ.
ΠΡΠΎΠΈΠ·Π²ΠΎΠ΄ΡΡΠ²ΠΎ ΡΠΈΠ»ΠΎΡΠΎΠ², ΡΡΠ΅Π±ΡΠ΅Ρ ΠΎΡ ΠΏΡΠΎΠΈΠ·Π²ΠΎΠ΄ΠΈΡΠ΅Π»Ρ Π½Π΅ΠΌΠ°Π»ΠΎΠ³ΠΎ ΠΎΠΏΡΡΠ°. Π ΡΠ²ΡΠ·ΠΈ Ρ ΡΡΠΈΠΌ ΠΏΡΠΎΠΈΠ·Π²ΠΎΠ΄ΡΡΠ²ΠΎ ΡΠΈΠ»ΠΎΡΠΎΠ², ΡΠ΅Π·Π΅ΡΠ²ΡΠ°ΡΠΎΠ², Π΅ΠΌΠΊΠΎΡΡΠ΅ΠΉ ΠΎΡΠ½ΠΎΡΡΡΡΡ ΠΊ Π½Π΅ΡΡΠ°Π½Π΄Π°ΡΡΠ½ΡΠΌ. Π§Π°ΡΠ΅ Π²ΡΠ΅Π³ΠΎ ΡΡΠ°Π»ΡΠ½ΡΠ΅ ΡΠΈΠ»ΠΎΡΡ ΠΏΡΠΈΡ ΠΎΠ΄ΠΈΡΡΡ ΠΈΠ·Π³ΠΎΡΠ°Π²Π»ΠΈΠ²Π°ΡΡ ΠΏΠΎ ΠΈΠ½Π΄ΠΈΠ²ΠΈΠ΄ΡΠ°Π»ΡΠ½ΠΎΠΌΡ Π·Π°ΠΊΠ°Π·Ρ ΠΈ ΠΈΡΡ ΠΎΠ΄Ρ ΠΈΠ· ΡΡΠ΅Π±ΠΎΠ²Π°Π½ΠΈΠΉ ΠΠ°ΠΊΠ°Π·ΡΠΈΠΊΠ°, Π²Π²ΠΈΠ΄Ρ ΡΠΎΠ³ΠΎ, ΡΡΠΎ ΡΠ°Π·ΠΌΠ΅ΡΡ Π΄ΠΎΠ»ΠΆΠ½Ρ ΡΡΠΈΡΡΠ²Π°ΡΡ ΠΎΠ±ΡΠ΅ΠΌ ΠΏΠΎΠΌΠ΅ΡΠ΅Π½ΠΈΡ Π½Π° ΠΏΡΠ΅Π΄ΠΏΡΠΈΡΡΠΈΠΈ, Π³Π΄Π΅ ΠΎΠ½ΠΈ Π±ΡΠ΄ΡΡ ΡΡΡΠ°Π½ΠΎΠ²Π»Π΅Π½Ρ. Π ΡΡΠΎΠΌ ΡΠ»ΡΡΠ°Π΅ Π½Π΅ΠΎΠ±Ρ ΠΎΠ΄ΠΈΠΌΠ° ΠΏΠΎΠΌΠΎΡΡ ΠΎΠΏΡΡΠ½ΡΡ ΡΠΏΠ΅ΡΠΈΠ°Π»ΠΈΡΡΠΎΠ², ΡΠΏΠΎΡΠΎΠ±Π½ΡΡ ΠΏΡΠΎΠΈΠ·Π²Π΅ΡΡΠΈ ΡΠΎΡΠ½ΡΠ΅ ΡΠ°ΡΡΠ΅ΡΡ ΠΏΠ°ΡΠ°ΠΌΠ΅ΡΡΠΎΠ² Π±ΡΠ΄ΡΡΠ΅ΠΉ ΡΡΡΠ°Π½ΠΎΠ²ΠΊΠΈ.
Π‘ΠΈΠ»ΠΎΡΡ Π΄Π»Ρ ΠΊΠΎΠΌΠ±ΠΈΠΊΠΎΡΠΌΠ°
ΠΡΠΎΠΈΠ·Π²ΠΎΠ΄ΡΡΠ²ΠΎ ΠΊΠΎΠΌΠ±ΠΈΠΊΠΎΡΠΌΠ° ΡΠ²ΡΠ·Π°Π½ΠΎ Ρ Ρ ΡΠ°Π½Π΅Π½ΠΈΠ΅ΠΌ ΡΡΠΏΡΡΠΈΡ ΠΊΠΎΠΌΠΏΠΎΠ½Π΅Π½ΡΠΎΠ² Π΄Π»Ρ ΠΈΠ·Π³ΠΎΡΠΎΠ²Π»Π΅Π½ΠΈΡ ΠΊΠΎΠΌΠ±ΠΈΠΊΠΎΡΠΌΠ°, Π° Π΄Π»Ρ Ρ ΡΠ°Π½Π΅Π½ΠΈΡ ΡΡΠΏΡΡΠΈΡ Π²Π΅ΡΠ΅ΡΡΠ² ΡΠ°ΠΌΠΎΠ΅ ΠΎΠΏΡΠΈΠΌΠ°Π»ΡΠ½ΠΎΠ΅ ΡΡΠ΅Π΄ΡΡΠ²ΠΎ — ΡΠΈΠ»ΠΎΡΡ. ΠΠΠ Β«ΠΠΠΒ» ΠΏΡΠΎΠΈΠ·Π²ΠΎΠ΄ΠΈΡ ΡΠΈΠ»ΠΎΡΡ Π΄Π»Ρ Ρ ΡΠ°Π½Π΅Π½ΠΈΡ ΠΊΠΎΠΌΠ±ΠΈΠΊΠΎΡΠΌΠ°.
Π₯ΡΠ°Π½Π΅Π½ΠΈΠ΅ Π±ΠΎΠ»ΡΡΠΈΡ ΠΎΠ±ΡΡΠΌΠΎΠ² ΠΊΠΎΠΌΠ±ΠΈΠΊΠΎΡΠΌΠ° Π½Π° ΠΆΠΈΠ²ΠΎΡΠ½ΠΎΠ²ΠΎΠ΄ΡΠ΅ΡΠΊΠΈΡ ΠΊΠΎΠΌΠΏΠ»Π΅ΠΊΡΠ°Ρ ΡΠΎΠΏΡΡΠΆΠ΅Π½ΠΎ Ρ ΠΎΠΏΡΠ΅Π΄Π΅Π»ΡΠ½Π½ΡΠΌΠΈ ΡΡΡΠ΄Π½ΠΎΡΡΡΠΌΠΈ. ΠΠ°ΠΏΡΠΈΠΌΠ΅Ρ, Π±ΠΎΠ»ΡΡΠΈΠ΅ ΠΎΠ±ΡΡΠΌΡ ΠΊΠΎΠΌΠ±ΠΈΠΊΠΎΡΠΌΠ° ΡΡΠ΅Π±ΡΡΡ Π·Π½Π°ΡΠΈΡΠ΅Π»ΡΠ½ΡΡ ΠΏΠ»ΠΎΡΠ°Π΄Π΅ΠΉ Π΄Π»Ρ Ρ ΡΠ°Π½Π΅Π½ΠΈΡ ΠΌΠ΅ΡΠΊΠΎΠ², Π° ΡΠ°ΠΊΠΆΠ΅ Π½Π΅ΠΎΠ±Ρ ΠΎΠ΄ΠΈΠΌΠΎ Π½Π΅ Π΄ΠΎΠΏΡΡΡΠΈΡΡ ΠΏΠΎΠΏΠ°Π΄Π°Π½ΠΈΡ Π²Π»Π°Π³ΠΈ. ΠΡΠΈ ΠΏΡΠΎΠ±Π»Π΅ΠΌΡ ΡΠΏΠΎΡΠΎΠ±Π΅Π½ ΡΠ΅ΡΠΈΡΡ ΡΡΠ°Π»ΡΠ½ΠΎΠΉ ΡΠΈΠ»ΠΎΡ. ΠΠ΅Π΄Ρ ΡΠΈΠ»ΠΎΡ ΡΡΠΎ ΠΏΡΠ΅ΠΆΠ΄Π΅ Π²ΡΠ΅Π³ΠΎ Π²Π΅ΡΡΠΈΠΊΠ°Π»ΡΠ½Π°Ρ Π΅ΠΌΠΊΠΎΡΡΡ, ΡΠΏΠΎΡΠΎΠ±Π½Π°Ρ Π²ΠΌΠ΅ΡΠ°ΡΡ Π½Π΅ΡΠΊΠΎΠ»ΡΠΊΠΎ Π΄Π΅ΡΡΡΠΊΠΎΠ² ΠΈ Π΄Π°ΠΆΠ΅ ΡΠΎΡΠ΅Π½ ΡΠΎΠ½Π½ ΠΊΠΎΠΌΠ±ΠΈΠΊΠΎΡΠΌΠ°, Π½ΠΎ ΠΏΡΠΈ ΡΡΠΎΠΌ Π·Π°Π½ΠΈΠΌΠ°Π΅Ρ Π½Π΅Π±ΠΎΠ»ΡΡΡΡ ΠΏΠ»ΠΎΡΠ°Π΄Ρ, ΠΈ ΡΠΏΠΎΡΠΎΠ±Π½Π° ΠΎΠ±Π΅ΡΠΏΠ΅ΡΠΈΡΡ Π·Π°ΡΠΈΡΡ. ΠΠ°Π³ΡΡΠ·ΠΊΠ° ΠΈ Π²ΡΠ³ΡΡΠ·ΠΊΠ° ΠΊΠΎΠΌΠ±ΠΈΠΊΠΎΡΠΌΠ° ΠΈΠ· ΡΠΈΠ»ΠΎΡΠ° ΠΏΡΠΎΠΈΠ·Π²ΠΎΠ΄ΠΈΡΡΡ Ρ ΠΏΠΎΠΌΠΎΡΡΡ ΡΠ½Π΅ΠΊΠ° ΠΈΠ»ΠΈ ΠΏΠ½Π΅Π²ΠΌΠΎΠ½Π°ΡΠΎΡΠ°.
Π‘ΠΈΠ»ΠΎΡΡ Π΄Π»Ρ Π°ΡΡΠ°Π»ΡΡΠ½ΠΎ-Π±Π΅ΡΠΎΠ½Π½ΡΡ Π·Π°Π²ΠΎΠ΄ΠΎΠ²
ΠΠΎΠ½ΡΡΡΡΠΊΡΠΈΠ²Π½ΠΎ ΡΠΈΠ»ΠΎΡΡ Π΄Π»Ρ Π°ΡΡΠ°Π»ΡΡΠΎ — Π±Π΅ΡΠΎΠ½Π½ΡΡ
Π·Π°Π²ΠΎΠ΄ΠΎΠ² ΠΏΡΠ΅Π΄ΡΡΠ°Π²Π»ΡΡΡ ΡΠΎΠ±ΠΎΠΉ ΠΈΠ·Π΄Π΅Π»ΠΈΠ΅ ΡΠΈΠ»ΠΈΠ½Π΄ΡΠΈΡΠ΅ΡΠΊΠΎΠΉ ΠΈΠ»ΠΈ ΠΏΡΡΠΌΠΎΡΠ³ΠΎΠ»ΡΠ½ΠΎΠΉ ΡΠΎΡΠΌΡ. ΠΠ° Π°ΡΡΠ°Π»ΡΡΠ½ΡΡ
Π·Π°Π²ΠΎΠ΄Π°Ρ
ΡΠΈΠ»ΠΎΡΡ ΠΈΡΠΏΠΎΠ»ΡΠ·ΡΡΡ Π² ΠΊΠ°ΡΠ΅ΡΡΠ²Π΅ Ρ
ΡΠ°Π½ΠΈΠ»ΠΈΡΠ° ΠΊΠΎΠΌΠΏΠΎΠ½Π΅Π½ΡΠΎΠ² Π°ΡΡΠ°Π»ΡΡΠ° ΠΈΠ»ΠΈ ΡΠ°ΡΡΡ ΡΠ΅Ρ
Π½ΠΎΠ»ΠΎΠ³ΠΈΡΠ΅ΡΠΊΠΎΠΉ ΡΠΈΡΡΠ΅ΠΌΡ ΠΏΠΎ ΠΏΡΠΎΠΈΠ·Π²ΠΎΠ΄ΡΡΠ²Ρ Π°ΡΡΠ°Π»ΡΡΠ°.
Π‘ΠΈΠ»ΠΎΡΡ Π΄Π»Ρ Ρ ΡΠ°Π½Π΅Π½ΠΈΡ ΡΠΎΠΏΠ»ΠΈΠ²Π½ΡΡ ΠΏΠ΅Π»Π»Π΅Ρ ΠΈ ΡΠΎΠΏΠ»ΠΈΠ²Π½ΡΡ Π³ΡΠ°Π½ΡΠ»
Π‘ ΡΠ°Π·Π²ΠΈΡΠΈΠ΅ΠΌ Π³Π°Π·ΠΎΡΠ½Π°Π±ΠΆΠ΅Π½ΠΈΡ ΠΎΡΠΎΠΏΠ»Π΅Π½ΠΈΠ΅ Ρ ΠΏΠΎΠΌΠΎΡΡΡ ΡΠ³Π»Ρ ΠΈ Π΄ΡΠΎΠ² ΡΡΠ»ΠΎ Π² ΠΏΡΠΎΡΠ»ΠΎΠ΅, Π½ΠΎ Π½Π° Π±ΠΎΠ»ΡΡΠ΅ΠΉ ΡΠ°ΡΡΠΈ Π·Π°Π³ΠΎΡΠΎΠ΄Π½ΡΡ ΡΠ΅ΡΡΠΈΡΠΎΡΠΈΠΉ ΠΈ Π² ΡΠ΅Π»ΡΡΠΊΠΎΠΉ ΠΌΠ΅ΡΡΠ½ΠΎΡΡΠΈ Π³Π°Π·ΠΎΡΠ½Π°Π±ΠΆΠ΅Π½ΠΈΠ΅ ΡΠ°Π·Π²ΠΈΡΠΎ ΠΊΡΠ°ΠΉΠ½Π΅ ΡΠ»Π°Π±ΠΎ. ΠΠ΄Π½ΠΈΠΌ ΠΈΠ· ΡΠΏΠΎΡΠΎΠ±ΠΎΠ² ΡΠΊΠΎΠ»ΠΎΠ³ΠΈΡΠ΅ΡΠΊΠΈ ΡΠΈΡΡΠΎΠ³ΠΎ ΡΠΏΠΎΡΠΎΠ±Π° ΠΎΡΠΎΠΏΠ»Π΅Π½ΠΈΡ Π΄ΠΎΠΌΠΎΠ² ΡΠ²Π»ΡΠ΅ΡΡΡ ΠΎΡΠΎΠΏΠ»Π΅Π½ΠΈΠ΅ Ρ ΠΏΠΎΠΌΠΎΡΡΡ ΠΏΠ΅Π»Π»Π΅Ρ ΠΈΠ»ΠΈ ΡΠΎΠΏΠ»ΠΈΠ²Π½ΡΡ Π³ΡΠ°Π½ΡΠ» ΠΈΠ·Π³ΠΎΡΠΎΠ²Π»Π΅Π½Π½ΡΡ ΠΈΠ· ΠΎΡΡ ΠΎΠ΄ΠΎΠ² Π΄Π΅ΡΠ΅Π²ΠΎ-ΠΏΠ΅ΡΠ΅ΡΠ°Π±Π°ΡΡΠ²Π°ΡΡΠ΅ΠΉ ΠΈ ΡΠ΅Π»ΡΡΠΊΠΎΡ ΠΎΠ·ΡΠΉΡΡΠ²Π΅Π½Π½ΠΎΠΉ ΠΏΡΠΎΠΌΡΡΠ»Π΅Π½Π½ΠΎΡΡΠΈ. Π’Π°ΠΊ ΡΠΎΠΏΠ»ΠΈΠ²Π½ΡΠ΅ ΠΏΠ΅Π»Π»Π΅ΡΡ ΠΎΠ±ΡΡΠ½ΠΎ ΠΈΠ·Π³ΠΎΡΠ°Π²Π»ΠΈΠ²Π°ΡΡ ΠΈΠ· Π΄ΡΠ΅Π²Π΅ΡΠ½ΡΡ ΠΎΠΏΠΈΠ»ΠΎΠΊ, ΡΡΡΡΠΆΠΊΠΈ, Π»ΠΈΡΡΡΠ΅Π², Π²Π΅ΡΠΎΠΊ, ΡΡΡΠΊΠΎΠ² ΠΈ Ρ.ΠΏ. ΠΠ²ΠΈΠ΄Ρ ΡΠΎΠ³ΠΎ, ΡΡΠΎ Π΄Π΅ΡΠ΅Π²ΠΎ ΡΠΏΠΎΡΠΎΠ±Π½ΠΎ Π²ΠΏΠΈΡΡΠ²Π°ΡΡ Π²Π»Π°Π³Ρ, ΡΠΎ ΠΈ ΠΏΠ΅Π»Π»Π΅ΡΡ Π½Π΅ΠΎΠ±Ρ ΠΎΠ΄ΠΈΠΌΠΎ Π·Π°ΡΠΈΡΠ°ΡΡ ΠΎΡ Π²ΠΎΠ·Π΄Π΅ΠΉΡΡΠ²ΠΈΡ Π²Π»Π°Π³ΠΈ ΠΈ Π΄Π»Ρ Π½ΠΈΡ ΡΡΠ΅Π±ΡΠ΅ΡΡΡ ΠΎΠ±Π΅ΡΠΏΠ΅ΡΠΈΡΡ ΡΡΡ ΠΎΠ΅ Ρ ΡΠ°Π½Π΅Π½ΠΈΠ΅. ΠΠ°ΡΠ΅ΠΉ ΡΠΈΡΠΌΠΎΠΉ ΠΈΠ·Π³ΠΎΡΠ°Π²Π»ΠΈΠ²Π°ΡΡΡΡ ΡΠΈΠ»ΠΎΡΡ Π΄Π»Ρ Ρ ΡΠ°Π½Π΅Π½ΠΈΡ ΠΏΠ΅Π»Π»Π΅Ρ ΠΎΠ±ΡΡΠΌΠΎΠΌ ΠΎΡ 3 ΠΊΡΠ±.ΠΌ., ΡΠΏΠΎΡΠΎΠ±Π½ΡΠ΅ Π½Π΅ ΡΠΎΠ»ΡΠΊΠΎ Ρ ΡΠ°Π½ΠΈΡΡ, Π½ΠΎ ΠΈ ΠΏΠΎΡΡΠ°Π²Π»ΡΡΡ ΠΊ ΠΊΠΎΡΠ»Ρ ΠΎΡΠΎΠΏΠ»Π΅Π½ΠΈΡ ΠΏΠ΅Π»Π»Π΅ΡΡ Ρ ΠΏΠΎΠΌΠΎΡΡΡ ΡΠ½Π΅ΠΊΠ°.
Π‘ΠΈΠ»ΠΎΡΡ Π΄Π»Ρ Ρ ΡΠ°Π½Π΅Π½ΠΈΡ Π½Π°ΠΏΠΎΠ»Π½ΠΈΡΠ΅Π»Π΅ΠΉ ΠΏΡΠ΅Π΄Π½Π°Π·Π½Π°ΡΠ΅Π½Π½ΡΡ ΡΡΠ°Π»Π΅ΡΠ° ΠΆΠΈΠ²ΠΎΡΠ½ΡΡ
Π‘ΠΈΠ»ΠΎΡΡ ΠΈΠ΄Π΅Π°Π»ΡΠ½ΠΎ ΠΏΠΎΠ΄Ρ ΠΎΠ΄ΡΡ Π΄Π»Ρ Ρ ΡΠ°Π½Π΅Π½ΠΈΡ ΡΡΠΏΡΡΠΈΡ ΠΌΠ°ΡΠ΅ΡΠΈΠ°Π»ΠΎΠ² ΠΈ Π²Π΅ΡΠ΅ΡΡΠ², ΡΠ°ΠΊ Π½Π° ΠΏΡΠΎΠΈΠ·Π²ΠΎΠ΄ΡΡΠ²Π΅ Π½Π°ΠΏΠΎΠ»Π½ΠΈΡΠ΅Π»Π΅ΠΉ Π΄Π»Ρ ΠΊΠΎΡΠ°ΡΡΠ΅Π³ΠΎ ΡΡΠ°Π»Π΅ΡΠ° ΠΈΡΠΏΠ»ΡΠ·ΠΎΠ²Π°Π½ΠΈΠ΅ ΡΠΈΠ»ΠΎΡΠΎΠ² ΠΏΠΎΠ·Π²ΠΎΠ»ΡΠ΅Ρ ΠΎΠ±Π΅ΡΠΏΠ΅ΡΠΈΡΡ ΡΠΎΡ ΡΠ°Π½Π½ΠΎΡΡΡ ΠΌΠ°ΡΠ΅ΡΠΈΠ°Π»ΠΎΠ².
ΠΠΎΠΌΠΏΠ»Π΅ΠΊΡΠ°ΡΠΈΡ ΡΠΈΠ»ΠΎΡΠΎΠ²
Π ΠΊΠΎΠΌΠΏΠ»Π΅ΠΊΡ ΠΊΠ°ΠΆΠ΄ΠΎΠ³ΠΎ ΡΠΈΠ»ΠΎΡΠ° Π²Ρ ΠΎΠ΄ΠΈΡ, ΡΠ°ΠΌ ΡΠΈΠ»ΠΎΡ, Π° ΡΠ°ΠΊΠΆΠ΅ ΠΎΠΏΠΎΡΠ½ΡΠ΅ ΠΊΠΎΠ½ΡΡΡΡΠΊΡΠΈΠΈ ΡΠΈΠ»ΠΎΡΠ°, ΠΏΠ»ΠΎΡΠ°Π΄ΠΊΠ° ΠΎΠ±ΡΠ»ΡΠΆΠΈΠ²Π°Π½ΠΈΡ, Π·Π°Π³ΡΡΠ·ΠΎΡΠ½Π°Ρ ΡΡΡΠ±Π°, ΠΎΠ³ΡΠ°ΠΆΠ΄Π΅Π½ΠΈΡ.
ΠΠΈΠ½ΠΈΠΌΠ°Π»ΡΠ½Π°Ρ ΠΊΠΎΠΌΠΏΠ»Π΅ΠΊΡΠ°ΡΠΈΡ ΡΡΠ°Π»ΡΠ½ΠΎΠ³ΠΎ ΡΠΈΠ»ΠΎΡΠ°:
- Π‘ΡΠ°Π»ΡΠ½Π°Ρ ΡΠΈΠ»ΠΎΡΠ½Π°Ρ Π΅ΠΌΠΊΠΎΡΡΡ;
- ΠΠΏΠΎΡΠ½ΡΠ΅ ΠΊΠΎΠ½ΡΡΡΡΠΊΡΠΈΠΈ ΡΠΈΠ»ΠΎΡΠ°;
- ΠΠ»ΠΎΡΠ°Π΄ΠΊΠ° ΠΎΠ±ΡΠ»ΡΠΆΠΈΠ²Π°Π½ΠΈΡ;
- ΠΠ΅ΡΡΠ½ΠΈΡΠ°;
- ΠΠ°Π³ΡΡΠ·ΠΎΡΠ½Π°Ρ ΡΡΡΠ±Π°;
- ΠΠ³ΡΠ°ΠΆΠ΄Π΅Π½ΠΈΡ;
- Π€Π»Π°Π½Π΅Ρ ΡΠ°Π·Π³ΡΡΠ·ΠΎΡΠ½ΠΎΠ³ΠΎ ΠΎΡΠ²Π΅ΡΡΡΠΈΡ Π½Π° ΠΊΠΎΠ½ΡΡΠ΅ ΡΠΈΠ»ΠΎΡΠ½ΠΎΠΉ Π΅ΠΌΠΊΠΎΡΡΠΈ;
- ΠΡΠΊ Ρ ΠΊΡΡΡΠΊΠΎΠΉ.
Β
ΠΡΠΈ Π½Π΅ΠΎΠ±Ρ ΠΎΠ΄ΠΈΠΌΠΎΡΡΠΈ ΠΊΠΎΠΌΠΏΠ»Π΅ΠΊΡΠ°ΡΠΈΡ ΡΠΈΠ»ΠΎΡΠ° ΠΌΠΎΠΆΠ΅Ρ Π±ΡΡΡ ΡΠ°ΡΡΠΈΡΠ΅Π½Π° ΠΈ Π΄ΠΎΠΏΠΎΠ»Π½Π΅Π½Π° ΡΡΡΡΠΎΠΉΡΡΠ²Π°ΠΌΠΈ (ΡΠΈΠ»ΡΡΡΡ, Π΄Π°ΡΡΠΈΠΊΠΈ, Π°ΡΡΠ°ΡΠΈΠΎΠ½Π½ΡΠ΅ ΡΡΡΡΠΎΠΉΡΡΠ²Π°, Π²ΠΈΠ±ΡΠ°ΡΠΈΠΎΠ½Π½ΡΠ΅ ΡΡΡΡΠΎΠΉΡΡΠ²Π° ΠΈ Ρ.ΠΏ.).
ΠΠ°ΡΠ΅ΡΠΈΠ°Π»Ρ ΠΏΡΠΈΠΌΠ΅Π½ΡΠ΅ΠΌΡΠ΅ ΠΏΡΠΈ ΠΈΠ·Π³ΠΎΡΠΎΠ²Π»Π΅Π½ΠΈΠΈ ΡΠΈΠ»ΠΎΡΠΎΠ² ΠΈΠ·Π³ΠΎΡΠ°Π²Π»ΠΈΠ²Π°ΡΡΡΡ ΠΈΠ· Π²ΡΡΠΎΠΊΠΎΠΊΠ°ΡΠ΅ΡΡΠ²Π΅Π½Π½ΠΎΠΉ ΡΡΠ°Π»ΠΈ ΠΈ ΠΏΠΎΠΊΡΡΡΡ Π°Π½ΡΠΈΠΊΠΎΡΡΠΎΠ·ΠΈΠΉΠ½ΡΠΌ ΡΠΎΡΡΠ°Π²ΠΎΠΌ, ΡΡΠΎ ΠΏΠΎΠ·Π²ΠΎΠ»ΡΠ΅Ρ ΡΡΠ°Π»ΡΠ½ΡΠΌ ΡΠΈΠ»ΠΎΡΠ°ΠΌ ΡΠ°Π±ΠΎΡΠ°ΡΡ Π² Π»ΡΠ±ΡΡ ΠΊΠ»ΠΈΠΌΠ°ΡΠΈΡΠ΅ΡΠΊΠΈΡ ΡΡΠ»ΠΎΠ²ΠΈΡΡ ΠΈ ΡΠ»ΡΠΆΠΈΡ Π³Π°ΡΠ°Π½ΡΠΈΠ΅ΠΉ ΠΈΡ Π΄ΠΎΠ»Π³ΠΎΠ²Π΅ΡΠ½ΠΎΡΡΠΈ. ΠΠ΅ΡΠ°Π»ΠΈ ΡΠΈΠ»ΠΎΡΠΎΠ² ΠΈΠ·Π³ΠΎΡΠ°Π²Π»ΠΈΠ²Π°ΡΡΡΡ ΠΈΠ· ΡΡΠ°Π»ΠΈ ΡΠΎΠ»ΡΠΈΠ½ΠΎΠΉ 6 — 12 ΠΌΠΌ. ΠΠ»Ρ ΠΏΡΠΎΠΈΠ·Π²ΠΎΠ΄ΡΡΠ²Π° ΡΠΈΠ»ΠΎΡΠΎΠ² ΠΠΠ Β«ΠΠΠΒ» ΠΎΡΠ½Π°ΡΠ΅Π½ ΡΠΎΠ²ΡΠ΅ΠΌΠ΅Π½Π½ΡΠΌ ΠΌΠ΅ΡΠ°Π»Π»ΠΎΠΎΠ±ΡΠ°Π±Π°ΡΡΠ²Π°ΡΡΠΈΠΌ ΠΎΠ±ΠΎΡΡΠ΄ΠΎΠ²Π°Π½ΠΈΠ΅ΠΌ, Π° ΠΏΠΎΡΠ»Π΅ ΡΠ²Π°ΡΠΊΠΈ ΠΌΠ΅ΡΠ°Π»Π»ΠΎΠΊΠΎΠ½ΡΡΡΡΠΊΡΠΈΠΉ Π²ΡΠ΅ ΡΠ²Π°ΡΠΎΡΠ½ΡΠ΅ ΡΠ²Ρ ΠΏΡΠΎΡ ΠΎΠ΄ΡΡ ΠΊΠΎΠ½ΡΡΠΎΠ»Ρ ΠΊΠ°ΡΠ΅ΡΡΠ²Π°. Π‘Π½Π°ΡΡΠΆΠΈ ΡΠΈΠ»ΠΎΡΡ ΠΏΠΎΠΊΡΡΠ²Π°ΡΡΡΡ ΡΠΏΠ΅ΡΠΈΠ°Π»ΡΠ½ΡΠΌΠΈ ΠΊΡΠ°ΡΠΊΠ°ΠΌΠΈ Π΄Π»Ρ Π·Π°ΡΠΈΡΡ ΠΎΡ ΠΊΠΎΡΡΠΎΠ·ΠΈΠΈ ΠΈ Π²Π½Π΅ΡΠ½Π΅Π³ΠΎ Π²ΠΎΠ·Π΄Π΅ΠΉΡΡΠ²ΠΈΡ. ΠΡΠΈ Π½Π΅ΠΎΠ±Ρ ΠΎΠ΄ΠΈΠΌΠΎΡΡΠΈ ΡΠΈΠ»ΠΎΡ ΠΌΠΎΠΆΠ΅Ρ Π±ΡΡΡ Π΄ΠΎΠΏΠΎΠ»Π½ΠΈΡΠ΅Π»ΡΠ½ΠΎ ΡΡΠ΅ΠΏΠ»ΡΠ½ ΡΠ½Π°ΡΡΠΆΠΈ.
ΠΠ΅ΡΠ°Π»Π»ΠΈΡΠ΅ΡΠΊΠΈΠ΅ ΡΠΈΠ»ΠΎΡΡ β ΠΏΡΠΎΡΠ½Ρ, Π½Π°Π΄Π΅ΠΆΠ½Ρ, Π΄ΠΎΠ»Π³ΠΎΠ²Π΅ΡΠ½Ρ. ΠΡΠ³ΡΡΠ·ΠΊΠ° ΠΌΠ°ΡΠ΅ΡΠΈΠ°Π»ΠΎΠ² ΠΈΠ· ΡΠΈΠ»ΠΎΡΠ° ΠΌΠΎΠΆΠ΅Ρ ΠΎΡΡΡΠ΅ΡΡΠ²Π»ΡΡΡΡΡ ΡΠ½Π΅ΠΊΠΎΠΌ ΠΈΠ»ΠΈ ΠΏΠ½Π΅Π²ΠΌΠΎΠ½Π°ΡΠΎΡΠΎΠΌ, Π° ΠΏΠΎΠ΄Π°ΡΠ° ΠΌΠ°ΡΠ΅ΡΠΈΠ°Π»ΠΎΠ² Π² ΡΠΈΠ»ΠΎΡ ΠΎΡΡΡΠ΅ΡΡΠ²Π»ΡΠ΅ΡΡΡ Π½Π΅ΠΏΠΎΡΡΠ΅Π΄ΡΡΠ²Π΅Π½Π½ΠΎ ΠΈΠ· ΡΡΠ°Π½ΡΠΏΠΎΡΡΠ½ΠΎΠ³ΠΎ ΡΡΠ΅Π΄ΡΡΠ²Π°, ΠΏΠΎ Π½Π°ΠΊΠ»ΠΎΠ½Π½ΠΎΠΌΡ Π»Π΅Π½ΡΠΎΡΠ½ΠΎΠΌΡ ΡΡΠ°Π½ΡΠΏΠΎΡΡΠ΅ΡΡ ΠΈΠ»ΠΈ ΠΏΠ½Π΅Π²ΠΌΠΎΠΏΠΎΠ΄Π°ΡΡΠΈΠΊΠΎΠΌ. Π Π·Π°Π²ΠΈΡΠΈΠΌΠΎΡΡΠΈ ΠΎΡ ΠΎΡΠΎΠ±Π΅Π½Π½ΠΎΡΡΠ΅ΠΉ ΡΠΊΡΠΏΠ»ΡΠ°ΡΠ°ΡΠΈΠΈ ΠΌΠΎΠΆΠ΅Ρ Π½Π΅Π·Π½Π°ΡΠΈΡΠ΅Π»ΡΠ½ΠΎ ΠΌΠ΅Π½ΡΡΡΡΡ ΠΊΠΎΠ½ΡΡΡΡΠΊΡΠΈΡ ΠΌΠ΅ΡΠ°Π»Π»ΠΈΡΠ΅ΡΠΊΠΎΠ³ΠΎ ΡΠΈΠ»ΠΎΡΠ°. ΠΠΠ Β«ΠΠΠΒ» ΠΏΡΠΎΠΈΠ·Π²ΠΎΠ΄ΠΈΡ ΠΈΠ·Π³ΠΎΡΠΎΠ²Π»Π΅Π½ΠΈΠ΅ ΡΠΈΠ»ΠΎΡΠΎΠ² ΡΠ°Π·Π»ΠΈΡΠ½ΠΎΠ³ΠΎ ΠΎΠ±ΡΡΠΌΠ° (ΠΎΡ 20 ΠΊΡΠ±.ΠΌ. Π΄ΠΎ 200 ΠΊΡΠ±.ΠΌ.). ΠΡΠΈ ΡΡΠΎΠΌ ΠΎΡΠ΅Π½Ρ Π²Π°ΠΆΠ½ΠΎ Π·Π°ΡΠ°Π½Π΅Π΅, ΠΏΡΠΈ Π·Π°ΠΊΠ°Π·Π΅ ΡΠΈΠ»ΠΎΡΠ°, ΠΎΠ±Π΄ΡΠΌΠ°ΡΡ Π²ΡΠ΅ ΡΡΠΈ ΠΌΠΎΠΌΠ΅Π½ΡΡ, ΡΡΠΎ Π±Ρ ΡΠΎΡΠ½ΠΎ ΠΎΠΏΡΠ΅Π΄Π΅Π»ΠΈΡΡΡΡ ΠΈ Ρ ΠΊΠΎΠ½ΡΡΡΡΠΊΡΠΈΠ΅ΠΉ Π°Π³ΡΠ΅Π³Π°ΡΠ°, ΠΈ Ρ Π½Π΅ΠΎΠ±Ρ ΠΎΠ΄ΠΈΠΌΡΠΌ ΡΠΏΠΈΡΠΊΠΎΠΌ Π΄ΠΎΠΏΠΎΠ»Π½ΠΈΡΠ΅Π»ΡΠ½ΠΎΠ³ΠΎ ΠΎΠ±ΠΎΡΡΠ΄ΠΎΠ²Π°Π½ΠΈΡ.
Π’Π°ΠΊΠΆΠ΅ ΡΠ»Π΅Π΄ΡΠ΅Ρ ΡΠ΄Π΅Π»ΠΈΡΡ Π²Π½ΠΈΠΌΠ°Π½ΠΈΠ΅ ΠΊΠ°ΡΠ΅ΡΡΠ²Ρ ΠΌΠ΅ΡΠ°Π»Π»Π° ΠΈΡΠΏΠΎΠ»ΡΠ·ΡΠ΅ΠΌΠΎΠ³ΠΎ ΠΏΡΠΈ ΠΏΡΠΎΠΈΠ·Π²ΠΎΠ΄ΡΡΠ²Π΅ ΡΠΈΠ»ΠΎΡΠΎΠ². ΠΡΠ΅ ΠΌΠ°ΡΠ΅ΡΠΈΠ°Π»Ρ ΠΏΡΠΈΠΌΠ΅Π½ΡΠ΅ΠΌΡΠ΅ ΠΏΡΠΈ ΠΏΡΠΎΠΈΠ·Π²ΠΎΠ΄ΡΡΠ²Π΅ ΡΠΈΠ»ΠΎΡΠΎΠ², ΠΎΠ±ΡΠ·Π°ΡΠ΅Π»ΡΠ½ΠΎ ΡΠ΅ΡΡΠΈΡΠΈΡΠΈΡΠΎΠ²Π°Π½Π½Ρ Π½Π° ΡΠΎΠΎΡΠ²Π΅ΡΡΡΠ²ΠΈΠ΅ ΡΡΠ΅Π±ΠΎΠ²Π°Π½ΠΈΡΠΌ ΠΠΠ‘Π’Π°. Π ΠΏΡΠΎΠΈΠ·Π²ΠΎΠ΄ΡΡΠ²Π΅ ΡΠΈΠ»ΠΎΡΠΎΠ², Π΅ΠΌΠΊΠΎΡΡΠ΅ΠΉ ΠΈ ΡΠ΅Π·Π΅ΡΠ²ΡΠ°ΡΠΎΠ² ΠΈΡΠΏΠΎΠ»ΡΠ·ΡΡΡΡΡ ΡΠ΅Ρ
Π½ΠΎΠ»ΠΎΠ³ΠΈΠΈ, ΠΏΠΎΠ·Π²ΠΎΠ»ΡΡΡΠΈΠ΅ ΠΏΡΠΎΠ²ΠΎΠ΄ΠΈΡΡ ΠΎΠ±ΡΠ°Π±ΠΎΡΠΊΡ ΠΌΠ΅ΡΠ°Π»Π»Π° Ρ ΠΎΡΠΎΠ±ΠΎΠΉ ΡΠΎΡΠ½ΠΎΡΡΡΡ, ΡΡΠΎ ΡΠΏΠΎΡΠΎΠ±ΡΡΠ²ΡΠ΅Ρ ΠΏΠΎΠ²ΡΡΠ΅Π½ΠΈΡ ΠΊΠ°ΡΠ΅ΡΡΠ²Π° ΠΏΡΠΎΠ΄ΡΠΊΡΠΈΠΈ, Π΅Π³ΠΎ Π΄ΠΎΠ»Π³ΠΎΠ²Π΅ΡΠ½ΠΎΡΡΠΈ ΠΈ Π½Π°Π΄ΡΠΆΠ½ΠΎΡΡΠΈ Π½Π΅Π·Π°Π²ΠΈΡΠΈΠΌΠΎ ΠΎΡ ΡΡΠ»ΠΎΠ²ΠΈΠΉ ΡΠΊΡΠΏΠ»ΡΠ°ΡΠ°ΡΠΈΠΈ ΠΈ ΡΡΠ°Π½ΡΠΏΠΎΡΡΠΈΡΠΎΠ²ΠΊΠΈ.
Π‘ΠΈΠ»ΠΎΡΡ ΡΠ΅ΠΌΠ΅Π½ΡΠ° ΠΌΠΎΠ³ΡΡ ΠΊΠΎΠΌΠΏΠ»Π΅ΠΊΡΠΎΠ²Π°ΡΡΡΡ ΠΏΡΠ»Π΅ΡΠ»ΠΎΠ²ΠΈΡΠ΅Π»Π΅ΠΌ, ΠΊΠΎΡΠΎΡΡΠΉ ΠΏΡΠ΅Π΄Π½Π°Π·Π½Π°ΡΠ΅Π½ Π΄Π»Ρ ΠΏΡΠ΅Π΄ΠΎΡΠ²ΡΠ°ΡΠ΅Π½ΠΈΡ ΠΏΠΎΠΏΠ°Π΄Π°Π½ΠΈΡ ΡΠ΅ΠΌΠ΅Π½ΡΠ½ΠΎΠΉ ΠΏΡΠ»ΠΈ Π² Π°ΡΠΌΠΎΡΡΠ΅ΡΡ, ΠΏΡΠ΅Π΄ΠΎΡΠ²ΡΠ°ΡΠ°Ρ Π²ΡΠ±ΡΠΎΡ ΡΠ΅ΠΌΠ΅Π½ΡΠ° Π½Π°ΡΡΠΆΡ. ΠΠΎΠ½ΡΡΡΡΠΊΡΠΈΠ²Π½ΠΎ ΠΏΡΠ»Π΅ΡΠ»ΠΎΠ²ΠΈΡΠ΅Π»Ρ ΡΠΈΠ»ΠΎΡΠ° ΡΡΡΠ°Π½Π°Π²Π»ΠΈΠ²Π°Π΅ΡΡΡ Π² Π²Π΅ΡΡ Π½Π΅ΠΉ ΡΠ°ΡΡΠΈ ΡΠΈΠ»ΠΎΡΠ°.
Π€ΠΎΡΠΎΠ³ΡΠ°ΡΠΈΠΈ ΡΠΈΠ»ΠΎΡΠΎΠ² Π΄Π»Ρ ΡΠ΅ΠΌΠ΅Π½ΡΠ°, Π·Π΅ΡΠ½Π°, ΠΏΠ΅ΡΠΊΠ°, ΠΌΡΠΊΠΈ ΠΈ Π΄ΡΡΠ³ΠΈΡ ΡΡΠΏΡΡΠΈΡ Π²Π΅ΡΠ΅ΡΡΠ² Π²Ρ ΠΌΠΎΠΆΠ΅ΡΠ΅ ΠΏΠΎΡΠΌΠΎΡΡΠ΅ΡΡ Π² Π½Π°ΡΠ΅ΠΉ ΡΠΎΡΠΎΠ³Π°Π»Π΅ΡΠ΅Π΅.
ΠΠΎΡΡΠΎΠΈΠ½ΡΡΠ²Π° ΡΠΈΠ»ΠΎΡΠΎΠ²
- ΠΏΡΠΎΡΠ½ΠΎΡΡΡ — Π·Π° ΡΡΡΡ ΠΏΡΠΈΠΌΠ΅Π½Π΅Π½ΠΈΡ Π²ΡΡΠΎΠΊΠΎΠΊΠ°ΡΠ΅ΡΡΠ²Π΅Π½Π½ΠΎΠΉ ΡΡΠ°Π»ΠΈ Ρ ΠΏΡΠΈΠΌΠ΅Π½Π΅Π½ΠΈΠ΅ΠΌ ΡΠ»Π΅ΠΌΠ΅Π½ΡΠΎΠ² ΠΆΡΡΡΠΊΠΎΡΡΠΈ ΡΠΈΠ»ΠΎΡ Π²ΡΠ΄Π΅ΡΠΆΠΈΠ²Π°Π΅Ρ Π·Π½Π°ΡΠΈΡΠ΅Π»ΡΠ½ΡΠ΅ ΠΌΠ΅Ρ Π°Π½ΠΈΡΠ΅ΡΠΊΠΈΠ΅ Π½Π°Π³ΡΡΠ·ΠΊΠΈ Π½Π΅ ΡΠ°Π·ΡΡΡΠ°ΡΡΡ ΠΈ ΡΠΎΡ ΡΠ°Π½ΡΡ ΡΠ²ΠΎΡ ΡΠΎΡΠΌΡ ΠΏΠΎΠ΄ Π²ΠΎΠ·Π΄Π΅ΠΉΡΡΠ²ΠΈΠ΅ΠΌ ΡΠΎΠ΄Π΅ΡΠΆΠΈΠΌΠΎΠ³ΠΎ ΠΈ Π²Π½Π΅ΡΠ½Π΅ΠΉ ΡΡΠ΅Π΄Ρ;
- Π½Π°Π΄ΡΠΆΠ½ΠΎΡΡΡ — Π²ΡΠ΅ ΡΠΈΠ»ΠΎΡΡ ΠΏΡΠΎΡ ΠΎΠ΄ΡΡ ΠΊΠΎΠ½ΡΡΠΎΠ»Ρ ΠΊΠ°ΡΠ΅ΡΡΠ²Π° ΠΈ ΠΈΡΠΏΡΡΠ°Π½ΠΈΡ, ΡΡΠΎ Π³Π°ΡΠ°Π½ΡΠΈΡΡΠ΅Ρ ΠΈΡ Π΄ΠΎΠ»Π³ΠΎΠ²Π΅ΡΠ½ΠΎΡΡΡ;
- ΡΠ΄ΠΎΠ±ΡΡΠ²ΠΎ Π·Π°Π³ΡΡΠ·ΠΊΠΈ/Π²ΡΠ³ΡΡΠ·ΠΊΠΈ ΡΠΎΠ΄Π΅ΡΠΆΠΈΠΌΠΎΠ³ΠΎ — Π±Π»Π°Π³ΠΎΠ΄Π°ΡΡ ΡΠ²ΠΎΠ΅ΠΉ ΡΠΈΠ»ΠΈΠ½Π΄ΡΠΈΡΠ΅ΡΠΊΠΎΠΉ ΡΠΎΡΠΌΠ΅ ΡΠΈΠ»ΠΎΡΡ ΠΏΠΎΠ·Π²ΠΎΠ»ΡΡΡ ΠΏΡΠΎΠΈΠ·Π²ΠΎΠ΄ΠΈΡΡ ΡΠ΄ΠΎΠ±Π½ΡΡ Π·Π°Π³ΡΡΠ·ΠΊΡ ΠΈ Π²ΡΠ³ΡΡΠ·ΠΊΡ ΡΠΎΠ΄Π΅ΡΠΆΠΈΠΌΠΎΠ³ΠΎ;
- ΠΌΠ°ΡΡΡΠ°Π±ΠΈΡΡΠ΅ΠΌΠΎΡΡΡ ΡΠΈΠ»ΠΎΡΠ½ΡΡ Ρ ΡΠ°Π½ΠΈΠ»ΠΈΡ — Π½Π΅Π±ΠΎΠ»ΡΡΠ°Ρ Π·Π°Π½ΠΈΠΌΠ°Π΅ΠΌΠ°Ρ ΠΏΠ»ΠΎΡΠ°Π΄Ρ ΡΠΈΠ»ΠΎΡΠΎΠΌ ΠΏΠΎΠ·Π²ΠΎΠ»ΡΠ΅Ρ ΡΠΎΠ·Π΄Π°ΡΡ Π½Π° Π½Π΅Π±ΠΎΠ»ΡΡΠΎΠΌ ΡΡΠ°ΡΡΠΊΠ΅ Π·Π΅ΠΌΠ»ΠΈ Ρ ΡΠ°Π½ΠΈΠ»ΠΈΡΠ° ΡΠ΅ΠΌΠ΅Π½ΡΠ°, Ρ ΡΠ°Π½ΠΈΠ»ΠΈΡΠ° ΠΏΠ΅ΡΠΊΠ°, Ρ ΡΠ°Π½ΠΈΠ»ΠΈΡΠ° ΠΌΡΠΊΠΈ ΠΈΠ»ΠΈ Π΄ΡΡΠ³ΠΈΡ ΡΡΠΏΡΡΠΈΡ Π²Π΅ΡΠ΅ΡΡΠ², Π»ΡΠ±ΠΎΠ³ΠΎ ΠΎΠ±ΡΡΠΌΠ°.
ΠΠΎΠΌΠΈΠ½Π°Π»ΡΠ½ΡΠ΅ ΠΎΠ±ΡΡΠΌΡ ΠΏΡΠΎΠΈΠ·Π²ΠΎΠ΄ΠΈΠΌΡΡ ΡΠΈΠ»ΠΎΡΠΎΠ²
ΠΠ΄Π½ΠΈΠΌΠΈ ΠΈΠ· ΡΠ°ΠΌΡΡ ΡΠ°ΡΠΏΡΠΎΡΡΡΠ°Π½ΡΠ½Π½ΡΡ ΠΎΠ±ΡΡΠΌΠΎΠ² ΡΠ²Π»ΡΡΡΡΡ ΡΠΈΠ»ΠΎΡΡ ΡΠ»Π΅Π΄ΡΡΡΠΈΡ ΠΎΠ±ΡΡΠΌΠΎΠ²:
ΠΠΎ ΠΏΡΠΈΠ²Π΅Π΄ΡΠ½Π½ΡΠ΅ ΠΎΠ±ΡΡΠΌΡ Π½Π΅ ΡΠ²Π»ΡΡΡΡΡ ΠΎΠΊΠΎΠ½ΡΠ°ΡΠ΅Π»ΡΠ½ΡΠΌΠΈ. ΠΡΠΈ Π½Π΅ΠΎΠ±Ρ ΠΎΠ΄ΠΈΠΌΠΎΡΡΠΈ ΠΌΡ Π³ΠΎΡΠΎΠ²Ρ ΠΈΠ·Π³ΠΎΡΠΎΠ²ΠΈΡΡ ΡΠΈΠ»ΠΎΡ Π»ΡΠ±ΠΎΠ³ΠΎ ΠΎΠ±ΡΠ΅ΠΌΠ° ΠΎΡ 3 ΠΊΡΠ±.ΠΌ Π΄ΠΎ 120 ΠΊΡΠ±.ΠΌ.. ΠΠΎΠ»ΠΈΡΠ΅ΡΡΠ²ΠΎ Π·Π°ΠΊΠ°Π·Π° — ΠΎΡ 1 ΡΡ.
ΠΠΎΠ½ΡΠ°ΠΆ ΠΈ ΡΡΡΠ°Π½ΠΎΠ²ΠΊΠ°
ΠΠΎΠ½ΡΡΡΡΠΊΡΠΈΠ²Π½ΠΎ ΡΠΈΠ»ΠΎΡΡ ΡΠ½Π°Π±ΠΆΠ΅Π½Ρ ΠΎΠΏΠΎΡΠ½ΠΎΠΉ ΡΠΈΡΡΠ΅ΠΌΠΎΠΉ Ρ ΠΏΠ»Π°ΡΡΠΈΠ½Π°ΠΌΠΈ, ΠΊΠΎΡΠΎΡΡΠΌΠΈ ΡΠΈΠ»ΠΎΡ ΠΊΡΠ΅ΠΏΠΈΡΡΡ ΠΊ Π·Π°ΠΊΠ»Π°Π΄Π½ΡΠΌ ΠΏΠ»Π°ΡΡΠΈΠ½Π°ΠΌ Ρ ΠΏΠΎΠΌΠΎΡΡΡ ΡΠ²Π°ΡΠΊΠΈ ΠΈΠ»ΠΈ Π²ΠΈΠ½ΡΠΎΠ²ΠΎΠ³ΠΎ ΡΠΎΠ΅Π΄ΠΈΠ½Π΅Π½ΠΈΡ. ΠΠ»Ρ ΡΡΡΠ°Π½ΠΎΠ²ΠΊΠΈ ΡΠΈΠ»ΠΎΡΠ°, ΠΊΠ°ΠΊ ΠΏΡΠ°Π²ΠΈΠ»ΠΎ ΡΡΠ΅Π±ΡΠ΅ΡΡΡ ΡΡΠ½Π΄Π°ΠΌΠ΅Π½Ρ Ρ Π·Π°ΠΊΠ»Π°Π΄Π½ΡΠΌΠΈ ΠΏΠ»Π°ΡΡΠΈΠ½Π°ΠΌΠΈ ΠΈΠ»ΠΈ ΠΊΡΠ΅ΠΏΡΠΆΠ½ΡΠΌΠΈ ΡΠΏΠΈΠ»ΡΠΊΠ°ΠΌΠΈ, ΠΊΠΎΡΠΎΡΡΠ΅ Π±Π΅ΡΠΎΠ½ΠΈΡΡΡΡΡΡ Π² ΡΠΎΠΎΡΠ²Π΅ΡΡΡΠ²ΠΈΠΈ Ρ ΡΠ°Π·ΠΌΠ΅ΡΠ°ΠΌΠΈ ΠΎΠΏΠΎΡΠ½ΠΎΠΉ ΡΠΈΡΡΠ΅ΠΌΡ ΡΠΈΠ»ΠΎΡΠ°.
Π‘ΠΏΠ΅ΡΠΈΠ°Π»ΠΈΡΡΡ Π½Π°ΡΠ΅Π³ΠΎ ΠΏΡΠ΅Π΄ΠΏΡΠΈΡΡΠΈΡ ΠΏΡΠΎΠΈΠ·Π²Π΅Π΄ΡΡ ΠΏΠΎΠ»Π½ΡΠΉ ΡΠ°ΡΡΡΡ Π½Π΅ΠΎΠ±Ρ ΠΎΠ΄ΠΈΠΌΠΎΠ³ΠΎ ΡΠ΅ΠΌΠ΅Π½ΡΠ½ΠΎΠ³ΠΎ Ρ ΡΠ°Π½ΠΈΠ»ΠΈΡΠ° Π΄Π»Ρ Π²Π°ΡΠ΅Π³ΠΎ ΠΏΡΠ΅Π΄ΠΏΡΠΈΡΡΠΈΡ.
ΠΡΠΎΠΌΠ΅ ΠΏΡΠΎΠΈΠ·Π²ΠΎΠ΄ΡΡΠ²Π° Π½ΠΎΠ²ΡΡ ΡΡΠ°Π»ΡΠ½ΡΡ ΡΠΈΠ»ΠΎΡΠΎΠ² Π΄Π»Ρ ΡΠ΅ΠΌΠ΅Π½ΡΠ°, ΠΌΡΠΊΠΈ, Π·Π΅ΡΠ½Π° ΠΈ ΠΏΠ΅ΡΠΊΠ° Π½Π°ΡΠ° ΡΠΈΡΠΌΠ° Π·Π°Π½ΠΈΠΌΠ°Π΅ΡΡΡ ΠΏΠΎΠΊΡΠΏΠΊΠΎΠΉ ΡΠΈΠ»ΠΎΡΠΎΠ² Π±ΡΠ²ΡΠΈΡ Π² ΡΠΏΠΎΡΡΠ΅Π±Π»Π΅Π½ΠΈΠΈ Π΄Π»Ρ ΠΏΠΎΡΠ»Π΅Π΄ΡΡΡΠ΅ΠΉ ΠΏΡΠΎΠ΄Π°ΠΆΠΈ, Π° ΡΠ°ΠΊΠΆΠ΅ Π·Π°Π½ΠΈΠΌΠ°Π΅ΡΡΡ ΠΏΡΠΎΠ΄Π°ΠΆΠ΅ΠΉ ΡΠΈΠ»ΠΎΡΠΎΠ² Π±ΡΠ²ΡΠΈΡ Π² ΡΠΏΠΎΡΡΠ΅Π±Π»Π΅Π½ΠΈΠΈ.
Π£Π·Π½Π°ΡΡ ΠΎ ΡΡΠ°Π»ΡΠ½ΡΡ ΡΠΈΠ»ΠΎΡΠΎΠ², ΡΠ΅Π½Π°Ρ ΠΈ ΡΡΠ»ΠΎΠ²ΠΈΡΡ Π΄ΠΎΡΡΠ°Π²ΠΊΠΈ ΠΈΠ»ΠΈ ΡΠ΄Π΅Π»Π°ΡΡ Π·Π°ΠΊΠ°Π· Π½Π° ΡΠΈΠ»ΠΎΡΡ, ΠΌΠΎΠΆΠ½ΠΎ ΠΏΠΎ ΡΠ΅Π»Π΅ΡΠΎΠ½Ρ 8 (495) 506-40-93. ΠΠ°ΡΠΈ ΠΌΠ΅Π½Π΅Π΄ΠΆΠ΅ΡΡ ΠΏΠΎΠΌΠΎΠ³ΡΡ Π² Π²ΡΠ±ΠΎΡΠ΅ Π½Π΅ΠΎΠ±Ρ ΠΎΠ΄ΠΈΠΌΠΎΠ³ΠΎ Π΅ΠΌΠΊΠΎΡΡΠ½ΠΎΠ³ΠΎ ΠΎΠ±ΠΎΡΡΠ΄ΠΎΠ²Π°Π½ΠΈΡ.
Π‘ΠΈΠ»ΠΎΡ (ΠΎΠ±ΡΠ΅ΠΌ 70 ΡΠΎΠ½Π½) |
Π‘ΠΈΠ»ΠΎΡΡ Π΄Π»Ρ ΠΌΡΠΊΠΈ (ΠΎΠ±ΡΠ΅ΠΌ 70 ΡΠΎΠ½Π½) |
Π‘ΠΈΠ»ΠΎΡΡ Π΄Π»Ρ ΡΠ΅ΠΌΠ΅Π½ΡΠ° |
Π‘ΠΈΠ»ΠΎΡΡ Π΄Π»Ρ ΠΌΡΠΊΠΈ (ΠΎΠ±ΡΠ΅ΠΌ 70 ΡΠΎΠ½Π½) |
Π‘ΠΈΠ»ΠΎΡ ΠΎΠ±ΡΡΠΌΠΎΠΌ 80 ΠΊΡΠ±.ΠΌ. |
Π‘ΠΈΠ»ΠΎΡ Π΄Π»Ρ ΡΠ΅ΠΌΠ΅Π½ΡΠ° |
Β | Β | Β |
ΠΠ»Ρ Π·Π°ΠΊΠ°Π·Π° ΡΡΠ°Π»ΡΠ½ΠΎΠ³ΠΎ ΡΠΈΠ»ΠΎΡΠ° Π·Π°ΠΏΠΎΠ»Π½ΠΈΡΠ΅ ΠΎΠΏΡΠΎΡΠ½ΡΠΉ Π»ΠΈΡΡ Π΄Π»Ρ ΡΡΠ°Π»ΡΠ½ΡΡ ΡΠΈΠ»ΠΎΡΠΎΠ²
www.dzm-k.ru
Π‘ΠΈΠ»ΠΎΡ Π² Π±ΠΎΡΠΊΠ΅ β ΠΡΠΌΡΡΠΊΠ°
ΠΡΡΡ Π½Π΅ΠΌΠ°Π»ΠΎ Π΄ΠΎΠΌΠ°ΡΠ½ΠΈΡ ΡΠ΅ΡΠΌ, Π³Π΄Π΅ Ρ ΠΎΠ·ΡΠ΅Π²Π° Π² Π΄ΠΎΡΡΠ°ΡΠΎΡΠ½ΠΎΠΌ ΠΊΠΎΠ»ΠΈΡΠ΅ΡΡΠ²Π΅ Π·Π°Π³ΠΎΡΠ°Π²Π»ΠΈΠ²Π°ΡΡ ΠΊΠΎΡΠΌ Π΄Π»Ρ ΡΠ²ΠΈΠ½Π΅ΠΉ ΠΏΡΡΡΠΌ ΡΠΈΠ»ΠΎΡΠΎΠ²Π°Π½ΠΈΡ Π² Π±ΠΎΡΠΊΠ°Ρ , ΠΈ ΠΆΠΈΠ²ΠΎΡΠ½ΡΠ΅ ΠΎΡ ΠΎΡΠ½ΠΎ Π΅Π³ΠΎ ΠΏΠΎΠ΅Π΄Π°ΡΡ. ΠΠ΅Π»Π°Π΅ΡΡΡ ΡΡΠΎ ΡΠ°ΠΊ.
ΠΠ΅ΡΡΡ, ΠΊ ΠΏΡΠΈΠΌΠ΅ΡΡ, 200-Π»ΠΈΡΡΠΎΠ²ΡΡ Π΄Π΅ΡΠ΅Π²ΡΠ½Π½ΡΡ Π±ΠΎΡΠΊΡ, Ρ ΠΎΡΠΎΡΠ΅Π½ΡΠΊΠΎ ΠΏΠΎΠ΄ΡΡΠ³ΠΈΠ²Π°ΡΡ Π½Π° Π½Π΅ΠΉ ΠΎΠ±ΡΡΡΠΈ, Π·Π°ΠΏΠΎΠ»Π½ΡΡΡ Π΅Ρ Π²ΠΎΠ΄ΠΎΠΉ ΠΈ Π·Π°ΠΌΠ°ΡΠΈΠ²Π°ΡΡ Π½Π΅ ΠΌΠ΅Π½Π΅Π΅ Π½Π΅Π΄Π΅Π»ΠΈ. ΠΠ°ΡΠ΅ΠΌ, Π²ΡΠ»ΠΈΠ² Π²ΠΎΠ΄Ρ, ΠΎΡΠΏΠ°ΡΠΈΠ²Π°ΡΡ ΡΠΌΠΊΠΎΡΡΡ ΠΊΠΈΠΏΡΡΠΊΠΎΠΌ. ΠΠΎΡΠ»Π΅ ΡΡΠΎΠ³ΠΎ ΠΌΠΎΠΆΠ½ΠΎ Π½Π°ΠΏΠΎΠ»Π½ΡΡΡ Π±ΠΎΡΠΊΡ ΠΆΠ΅Π»Π°ΡΠ΅Π»ΡΠ½ΠΎ ΠΌΠΎΠ»ΠΎΠ΄ΠΎΠΉ Π·Π΅Π»ΡΠ½ΠΎΠΉ ΠΌΠ°ΡΡΠΎΠΉ, ΠΊΠΎΡΠΎΡΡΡ, ΠΊΡΡΠ°ΡΠΈ, Π½ΡΠ½Π΅ΡΠ½Π΅ΠΉ Π΄ΠΎΠΆΠ΄Π»ΠΈΠ²ΠΎΠΉ Π²Π΅ΡΠ½ΠΎΠΉ Π»Π΅Π³ΠΊΠΎ Π·Π°Π³ΠΎΡΠΎΠ²ΠΈΡΡ: ΡΡΠ°Π²ΠΎΡΡΠΎΠΉ ΠΏΠΎΠ²ΡΡΠ΄Ρ ΠΎΡΠΌΠ΅Π½Π½ΡΠΉ.
Π£ΡΡΠ°ΠΌΠ±ΠΎΠ²Π°Π² Π·Π΅Π»Π΅Π½Ρ Π² ΡΠΌΠΊΠΎΡΡΠΈ, Π΄Π°Π»Π΅Π΅ ΠΏΠΎΡΡΡΠΏΠ°ΡΡ ΡΠ»Π΅Π΄ΡΡΡΠΈΠΌ ΠΎΠ±ΡΠ°Π·ΠΎΠΌ: Π»ΡΡΡ Π² Π½Π΅Ρ Π½Π΅ΠΌΠ½ΠΎΠ³ΠΎ Π²ΠΎΠ΄Ρ, Π° ΡΠ°ΠΊΠΆΠ΅ ΠΌΠΎΠ»ΠΎΡΠ½ΡΡ ΡΡΠ²ΠΎΡΠΎΡΠΊΡ (ΠΌΠΎΠΆΠ½ΠΎ Π΄Π°ΠΆΠ΅ ΡΠ΅Π»ΠΎΠ΅ Π²Π΅Π΄ΡΠΎ).
Π ΡΡΠΎ, ΠΊΠΎΠ½Π΅ΡΠ½ΠΎ, Π½Π΅ Π΅Π΄ΠΈΠ½ΡΡΠ²Π΅Π½Π½ΡΠΉ ΡΠ΅ΡΠ΅ΠΏΡ. ΠΠΎΠΏΠΎΠ·ΠΆΠ΅, ΠΊΠΎΠ³Π΄Π° ΠΏΠΎΡΠ²ΡΡΡΡ Π½Π° ΠΏΡΠΈΡΡΠ°Π΄Π΅Π±Π½ΠΎΠΌ ΡΡΠ°ΡΡΠΊΠ΅ ΡΠ²ΡΠΊΠ»Π°, ΠΌΠΎΡΠΊΠΎΠ²Ρ, ΠΊΠ°ΡΡΠΎΡΠ΅Π»Ρ, ΠΊΠ°Π±Π°ΡΠΊΠΈ, ΠΎΠ³ΡΡΡΡ, ΡΡΠΊΠ²Π°, ΠΏΠ°Π΄Π°Π»ΠΈΡΠ° ΡΠ±Π»ΠΎΠΊ ΠΈ Π³ΡΡΡ, Π²ΡΡ ΡΡΠΎ Π² ΡΠ΅Π·Π°Π½ΠΎΠΌ Π²ΠΈΠ΄Π΅ ΠΈ ΡΡΠ°Π²Ρ ΠΌΠΎΠΆΠ½ΠΎ ΠΏΠΎΠ»ΠΎΠΆΠΈΡΡ Π² Π±ΠΎΡΠΊΡ, ΠΏΠΎΡΠ»Π΅ ΡΠ΅Π³ΠΎ Π²Π»ΠΈΡΡ ΠΊΠΈΡΠ»ΠΎΠ΅ ΠΌΠΎΠ»ΠΎΠΊΠΎ (Π΄ΠΎΡΡΠ°ΡΠΎΡΠ½ΠΎ 1-2 Π»ΠΈΡΡΠΎΠ²).
Π Π² ΡΠΎΠΌ, ΠΈ Π΄ΡΡΠ³ΠΎΠΌ ΡΠ»ΡΡΠ°Π΅ ΡΠ»Π΅Π΄ΡΠ΅Ρ ΡΠΎΠ±Π»ΡΠ΄Π°ΡΡ ΠΏΡΠΎΡΡΡΠ΅ ΠΏΡΠ°Π²ΠΈΠ»Π°. ΠΡΠ»ΠΈ Π·Π°ΠΊΠ»Π°Π΄ΡΠ²Π°Π΅ΠΌΠ°Ρ Π² ΡΠΌΠΊΠΎΡΡΡ ΠΌΠ°ΡΡΠ° ΠΈΠ· ΡΡΠ°Π²Ρ ΠΈΠ»ΠΈ ΠΈΠ· ΡΡΠ°Π²Ρ ΠΈ ΠΊΠΎΡΠ½Π΅ΠΏΠ»ΠΎΠ΄ΠΎΠ² ΠΎΡΠ΅Π½Ρ ΡΠΎΡΠ½Π°Ρ, ΡΠΎ Π΅Ρ Π½Π΅ΠΎΠ±Ρ ΠΎΠ΄ΠΈΠΌΠΎ ΠΏΠΎΠ΄ΡΠ°Π»ΠΈΠ²Π°ΡΡ, ΡΠ΅ΠΌ ΡΠ°ΠΌΡΠΌ ΡΠ΄Π΅ΡΠΆΠΈΠ²Π°ΡΡ Π±ΡΠΎΠΆΠ΅Π½ΠΈΠ΅, Π½Π΅ Π΄ΠΎΠΏΡΡΠΊΠ°ΡΡ Π½Π°ΠΊΠΎΠΏΠ»Π΅Π½ΠΈΡ ΠΈΠ·Π»ΠΈΡΠ½Π΅Π³ΠΎ ΠΊΠΎΠ»ΠΈΡΠ΅ΡΡΠ²Π° ΠΌΠΎΠ»ΠΎΡΠ½ΠΎΠΉ ΠΊΠΈΡΠ»ΠΎΡΡ. Π ΡΠΎΠΌ ΠΆΠ΅ ΡΠ»ΡΡΠ°Π΅, ΠΊΠΎΠ³Π΄Π° ΠΌΠ°ΡΡΠ° ΡΡΡ ΠΎΠ²Π°ΡΠ°Ρ, ΠΏΡΠΎΠ²ΡΠ»Π΅Π½Π½Π°Ρ, ΡΠΎ ΠΏΠΎΠ΄ΡΠ°Π»ΠΈΠ²Π°ΡΡ Π΅Ρ Π½ΡΠΆΠ½ΠΎ ΡΠ»Π΅Π³ΠΊΠ°.
ΠΠΎΡΠΊΡ Ρ Π»ΡΠ±ΠΎΠΉ ΠΌΠ°ΡΡΠΎΠΉ Π·Π°ΠΊΡΠΏΠΎΡΠΈΠ²Π°ΡΡ. ΠΠ΅Π»Π°ΡΡ ΡΡΠΎ ΡΠ°ΠΊ: ΠΏΠΎΠ²Π΅ΡΡ ΠΌΠ°ΡΡΡ ΠΊΠ»Π°Π΄ΡΡ ΠΊΡΡΠΆΠΎΠΊ ΠΈΠ· ΠΏΠΎΠ»ΠΈΡΡΠΈΠ»Π΅Π½ΠΎΠ²ΠΎΠΉ ΠΏΠ»ΡΠ½ΠΊΠΈ, Π·Π°ΡΠ΅ΠΌ Π΄Π΅ΡΠ΅Π²ΡΠ½Π½ΡΠΉ ΠΊΡΡΠΆΠΎΠΊ ΠΈ ΠΏΡΠΈΠ΄Π°Π²Π»ΠΈΠ²Π°ΡΡ Π³Π½ΡΡΠΎΠΌ Π²Π΅ΡΠΎΠΌ 20-25 ΠΊΠ³.
ΠΠ΅ΠΎΠ±Ρ ΠΎΠ΄ΠΈΠΌΠΎ ΠΏΡΠΈ Π·Π°ΠΊΠ»Π°Π΄ΠΊΠ΅ ΡΠΎΠ±Π»ΡΠ΄Π°ΡΡ ΡΠ»Π΅Π΄ΡΡΡΠ΅Π΅ ΡΡΠ»ΠΎΠ²ΠΈΠ΅: Π΄Π΅Π»Π°ΡΡ ΡΡΠΎ Π½ΡΠΆΠ½ΠΎ Π±ΡΡΡΡΠΎ, ΠΈΠ½Π°ΡΠ΅ ΠΊΠΎΡΠΌ Π½Π΅ Π±ΡΠ΄Π΅Ρ ΡΠΎΡ ΡΠ°Π½ΡΡΡΡΡ Π² ΠΏΡΠΈΠ΅ΠΌΠ»Π΅ΠΌΠΎΠΌ ΡΠΎΡΡΠΎΡΠ½ΠΈΠΈ. ΠΠ°Π»Π΅Π΅ Π½Π°Π΄ΠΎ ΡΠ»Π΅Π΄ΠΈΡΡ Π·Π° ΠΏΡΠΎΡΠ΅ΡΡΠΎΠΌ Π² Π±ΠΎΡΠΊΠ΅. ΠΡΠ»ΠΈ ΡΠΎΠΊ Π±ΠΎΠ»ΡΡΠ΅ Π½Π΅ Π²ΡΠ΄Π΅Π»ΡΠ΅ΡΡΡ, ΡΠΎ ΡΠ΅Π»ΠΈ ΠΌΠ΅ΠΆΠ΄Ρ Π΄Π΅ΡΠ΅Π²ΡΠ½Π½ΡΠΌ ΠΊΡΡΠΆΠΊΠΎΠΌ ΠΈ ΡΡΠ΅Π½ΠΊΠ°ΠΌΠΈ ΡΠΌΠΊΠΎΡΡΠΈ Π½Π°Π΄ΠΎ Π·Π°ΠΌΠ°Π·Π°ΡΡ Π³Π»ΠΈΠ½ΡΠ½ΡΠΌ ΡΠ°ΡΡΠ²ΠΎΡΠΎΠΌ. ΠΠΎΡΠ»Π΅ ΡΡΠΎΠ³ΠΎ ΠΌΠΎΠΆΠ½ΠΎ ΡΡΠ°Π²ΠΈΡΡ Π±ΠΎΡΠΊΡ Π² ΠΏΡΠΎΡ Π»Π°Π΄Π½ΠΎΠ΅ ΠΌΠ΅ΡΡΠΎ Π½Π° Ρ ΡΠ°Π½Π΅Π½ΠΈΠ΅.
ΠΠΎΠ³Π΄Π° ΠΏΡΠΈΡ ΠΎΠ΄ΠΈΡΡΡ Π½Π°Π±ΠΈΡΠ°ΡΡ ΡΠΈΠ»ΠΎΡ, ΡΠΎ ΠΊΠ°ΠΆΠ΄ΡΠΉ ΡΠ°Π· ΠΎΡΡΠ°Π²ΡΠΈΠΉΡΡ ΠΊΠΎΡΠΌ Π½Π°Π΄ΠΎ ΡΡΠ°ΡΠ΅Π»ΡΠ½ΠΎ Π·Π°ΠΊΡΠΏΠΎΡΠΈΠ²Π°ΡΡ.
Π‘ΠΈΠ»ΠΎΡ ΠΏΠ΅ΡΠ΅Π΄ ΡΠΊΠ°ΡΠΌΠ»ΠΈΠ²Π°Π½ΠΈΠ΅ΠΌ ΡΠ²ΠΈΠ½ΡΡΠΌ ΠΆΠ΅Π»Π°ΡΠ΅Π»ΡΠ½ΠΎ ΡΠΌΠ΅ΡΠΈΠ²Π°ΡΡ Ρ ΠΊΠΎΠΌΠ±ΠΈΠΊΠΎΡΠΌΠΎΠΌ ΠΈΠ»ΠΈ Ρ ΡΡΡ ΠΈΠΌΠΈ ΡΠΎΠ»ΡΡΠ½ΡΠΌΠΈ Ρ Π»Π΅Π±Π½ΡΠΌΠΈ ΠΎΡΡ ΠΎΠ΄Π°ΠΌΠΈ.
ΠΡΡ ΠΌΠ°ΡΠ΅ΡΠΈΠ°Π»Ρ ΠΏΠΎ ΡΠ΅ΠΌΠ΅:
kumushka.com